Zumbach launches new 3-axis lump detector family KW TRIO for extrusion lines, optical fibre draw towers, rewinding processes and others. The first technology with a pulsing light source and automatic ambient light rejection after the cycle makes these detectors impervious to stray light and the pioneers in their class. Line speed or iridescent light have no influence on measurement results – even the smallest surface faults are detected reliably on a micrometre scale.
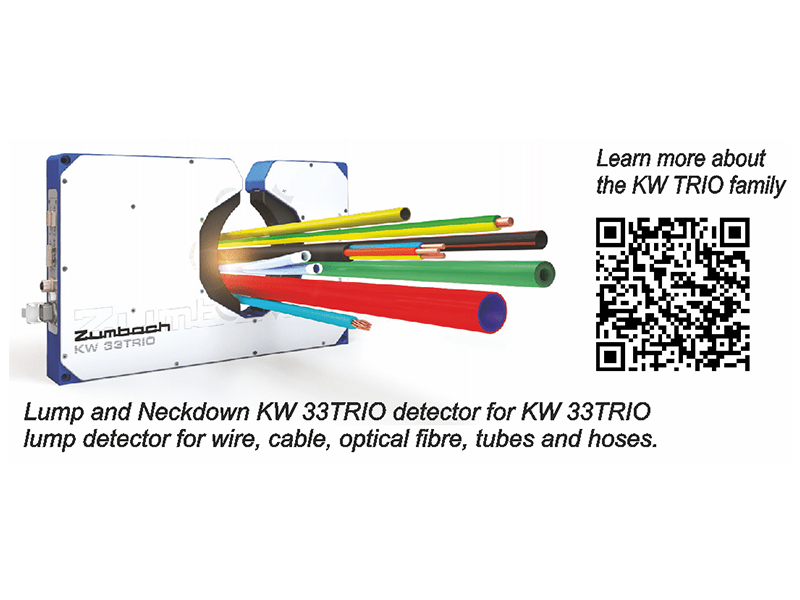
In insulating, sheathing, enamelling, wire drawing and other processes, surface faults such as lumps and neckdowns must immediately be detected. Zumbach has developed a new concept eliminating stray light as a factor in fault detection in order to enable production processes with the highest quality possible at extrusion lines, optical fibre draw towers, etc. The one-of-a-kind combination of an electronic measuring principle and a complex optics solution sets a new standard in fault detection reliability and performance.
Advantages for the quality control
• measurement results are unaffected by stray light, velocity and vibration
• complex optics solution enables minimal fault detection height of only 0.01mm and a minimal fault detection length of only 0.2…0.3mm
• Fully digitalized signal processing DSP
• Micro-processor for intelligent fault analysis and classification
• Illuminated, mobile operating and display unit
• detailed error log
• interface for host connection
• compact design, flexible mounting concept
• theoretically unlimited lifespan
Since faults often only cover a limited angle on the product circumference, e.g. lumps, neckdowns, blisters, etc., 2-axis detectors (X/Y) are usually used. However, reliability can be three times as high by using the 3-axial measurement of the KW TRIO models. This is due to the significant reduction in blind spots that only the KW TRIO models enable.