Ahead of competition in Rigid Stranding Machines
Main advantages of AEI Rigid Stranding Machines for end-user are high speed, latest technology, robust construction, minimal maintenance, and operator safety.
February 29, 2016
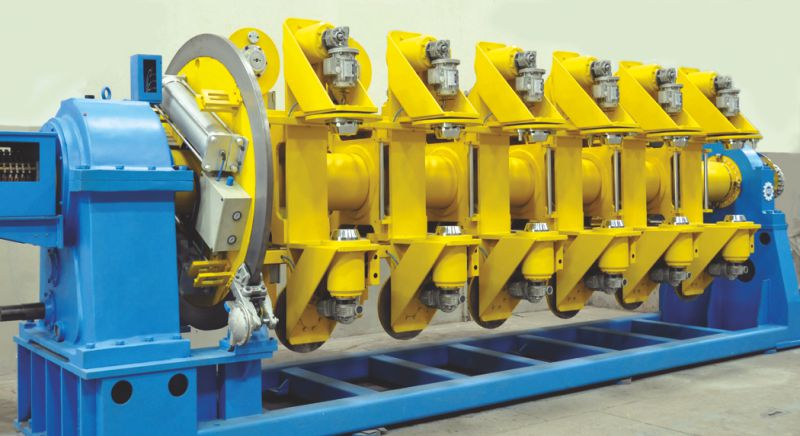
With 45 years of continuous presence in manufacturing and design of Rigid Stranding Machines, AEI Machines (Associated Engineers & Industrials Ltd.) has taken power conductor stranding to the next level.
The Rigid Strander Specialist known for superior quality and performance of its machines emphasizes on design innovation, materials, process, workmanship and after-sales support. One of the key factors for years of consistent operation of AEI Machines is the in-house parts manufacture, fabrication and assembly of the complete machine.
Main advantages of AEI Rigid Stranding Machines for end-user are high speed, latest technology, robust construction, minimal maintenance and operator safety. Moreover these highly automated machines offer higher energy efficiency and ease of operation with reduced workforce.
AEI shall showcase its Rigid Stranders which deliver accurate back tension, smooth strand deviation and precise lay control. These features are essentially required for superior quality compacted conductor in case of low, medium and EHV power cables and for high production speeds in case of overhead conductor manufacture. Enhanced cage speeds and use of fully automatic bobbin batch loading systems further ensure higher production efficiencies and uptime.
Also on display shall be the redesigned heavy duty compacting head suitable for high tolerance Milliken conductor and other heads including the recently developed TW head for manufacture of latest generation HTLS / Trapezoidal Wire overhead conductor.
At Wire 2016 Düsseldorf (Stand 11 D06), AEI shall be looking forward to welcoming visitors from all over the world and showcase the advantages of upgrading to AEI Stranders.
2015 has been Achievement Year for Ajex & Turner
VNT Nano Dies, Conform Metal Dies, Lubricants, Pressure Dies, PCD & TC Busbar Dies, Extrusion Tools, Ultrasonic Die Polishing Machine in 150, 200, 250, 300 watt, Die Polishing from 10 micron to 10 mm are among the biggest achievements of our company in the year 2015.
February 29, 2014
This year’s innovations have captured the Wire & cable industries attention and reminded us of the immense scope of new technologies accomplishment—as well as how far we have yet to go.
Ajex & Turner Wire Technologies has been an integral part of Wire & Cable show since past 30 years and this time at Dusseldorf fair 2016, we are looking forward to showcase our new developments as an ultimate opportunity to attract our target customers.
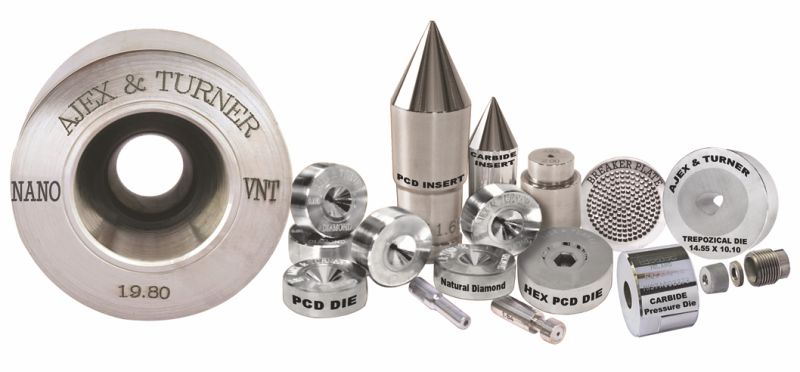
Ajex would be a one stop shop for major consumable requirements for any wire & Cable manufacturing plant.
Replacing the traditional ways of wire drawing and compacting, the company has developed revolutionary VNT Nano dies for copper, Aluminium, Aluminium alloy, stainless steel, MIG/ CO2 and high/low carbon wires.
Due to our domain expertise, we are able to provide these VNT Nano dies exactly as per the specifications detailed by the clients so that their production process can run efficiently. With an advanced diamond coating technology, our VNT Nano diesholds 0% tolerance throughout its working life and can achieve good wear resistance with accurate surface properties.
VNT Nano dies promise in terms of improving the performance, resiliency, and longevity of the die. In the simple words, VNT Nano dies is also seen as a boon since these can help with creating what is called New Generation Wire Dies.
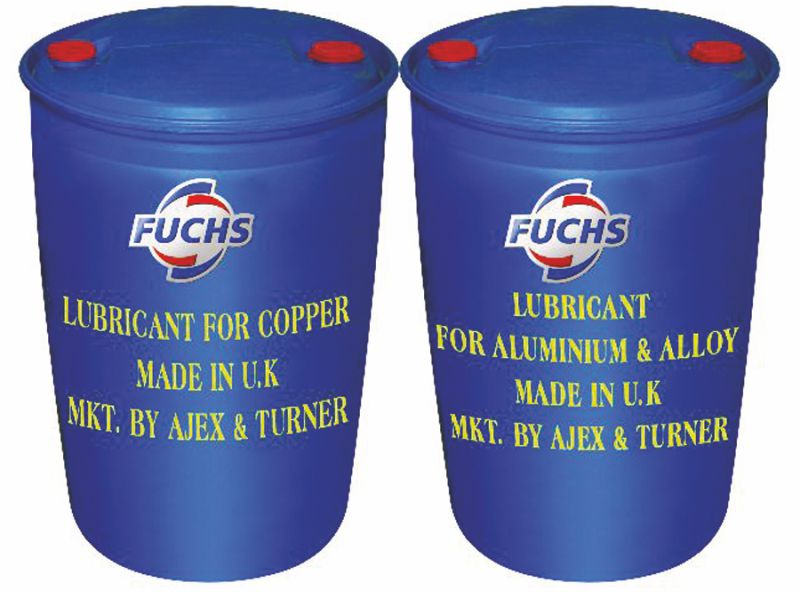
Ajex & Turner Wire technologies now represent Fuchs wire drawing lubricants, UK in India, Srilanka, Nepal, Bhutan, Malaysia, Bangladesh, Saudi Arabia & Middle East for Copper, Aluminum and Aluminum Alloys . These lubricants have the lowest consumption rate, can solve the problem of copper blackening, oxidation and have better lubricity & finish with low viscosity. It is excellent for drawing a wide cross section of pure copper & aluminium. Backed by the trust and excellent feedback by worldwide users, we hope to get the same response by overseas customers.
Due to our domain expertise, we are able to provide Extrusion Tools (Tips & Die) exactly as per the specifications detailed by our clients so that their extrusion process can run efficiently. With an advanced inserting and grinding technology, customers can achieve a more accurate as well as consistent insulation. We also ensure that our all precision extrusion tools have accuracy in concentric depending on the type and design of the tool.
One of the best innovative automatic high speed in-house carbide die polishing and grinding machine TCD-10 will surely be the attraction for the visitors as it grind and polish angles and bearing in one operation, which saves time, energy and also very cost effective. The machine operates at very high speed and can recondition dies in a very short time of period. It provides Accurate and Precise angles on re-cut dies.
For a cable industry from house wiring to HT conductor, our company has developed various type of extrusion tooling to meet customer demand and centricity specially maintain for longer life.
We intend to highlight our new developments at show by product demonstration by technical discussion and showing the product working video.
As our company believes in selling on value not price, we are open for free trials as well.
August Strecker to Present New Developments at WIRE 2016
STRECKER welders are well represented in many renowned national and international wire and cable factories
February 29, 2016
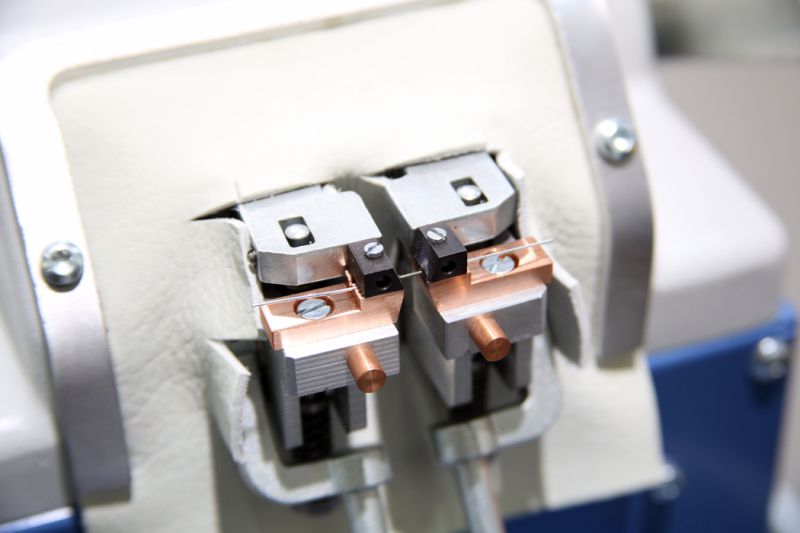
Facts and figures of WIRE 2016: 120 m² booth space, 22 machines on display, operator training, welds carried out live, welders for steel, copper, aluminium, brass, for solid and stranded conductors, coldwelders , welders with automatic deburring function
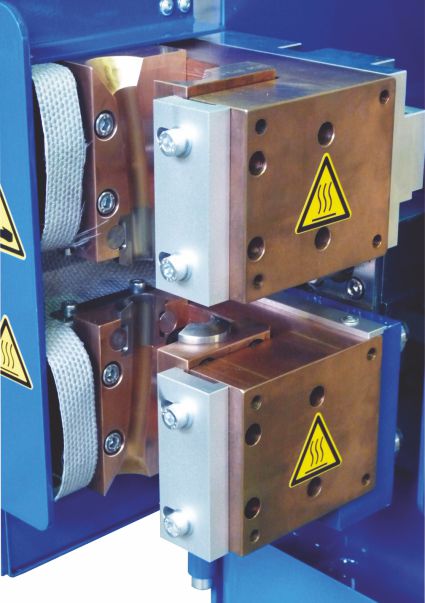
Messrs. AUGUST STRECKER GmbH & Co. KG was founded in 1933 and serves the wire and cable industry for more than 80 years now with today about 60 skilled employees at their Limburg/Germany headquarter.
STRECKER welders are well represented in many renowned national and international wire and cable factories and enjoy an excellent reputation for their reliability and performance. The majority of the company’s production is exported to more than 110 countries all over the world. Sales activities as well as customer-service are supported by 40 representative offices worldwide.
Through participation in European and many overseas exhibitions the trademark of STRECKER buttwelders has become a well-known symbol of quality.
AWCMA/VOEDKM to Participate in WIRE 2016 Duesseldorf
Achieving greater awareness of its market, leading high-tech products and Austrian engineering in the international wire and cable industry are central to the global aims of the AWCMA (AUSTRIAN WIRE & CABLE MACHINERY MANUFACTURERS ASSOCIATION).
February 29, 2016
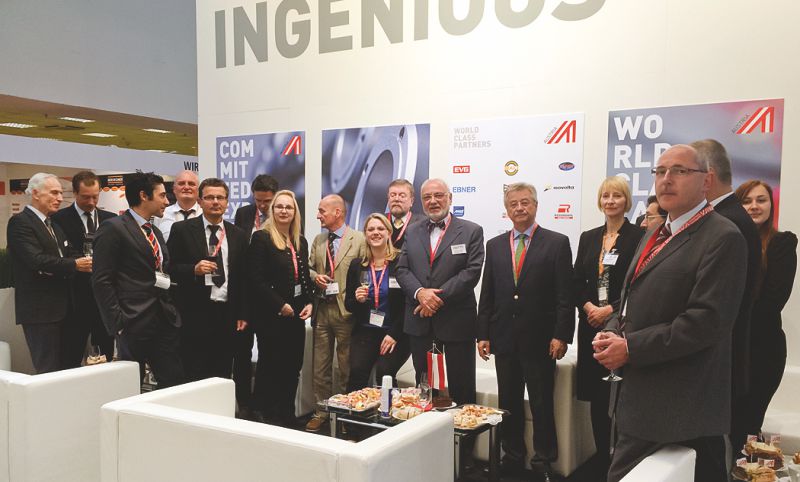
Fifteen (15) Austrian AWCMA specialist firms are available to apply state-of-the-art technology to the solution of any wire and cable production problems and will display their products at the subsequently mentioned stands within the Austrian Pavilion in Hall 10 and on individual stands in halls 9 and 16. The following AWCMA member companies will display their latest technologies, hard and software for the economic production of wires and cables in the Austrian Pavilion in Hall 10:
EBNER INDUSTRIEOFENBAU (10C42-06), MAG AG (10C52-09), EDER ENGINEERING (10C42-01), MALI (10C42-09), GEBAUER&GRILLER (10C42-02), MEDEK&SCHOERNER (10C52-01), KHU SONDERMASCHINEN (10C52-06), UNITEK (10C42-08), LENZING PLASTICS (10C42-03), VOEST ALPINE WIRE (10C42-07), LUMPI BERNDORF (10C42-05), VOEDKM/AWCMA (10C42-01).
Three (3) member companies will exhibit on individual stands:
ROSENDAHL-NEXTROM (9A60), E.V. G. (16A24), FORTUNA FEDERN (16E22).
As a tradition already, splendid Austrian hospitality of its best will be offered to all AWCMA members and their visiting guests and our friends in the special “Café Vienna”, located within the Austrian Pavilion (10C52-02), particularly during the “Austrian Evening” on Wednesday 6th April 2016 at 5pm.
All Austrian Specialist companies – be them exhibiting within the Austrian Pavilion or on individual Stands – will be at their full disposal to all visitors at WIRE 2016.
Cimteq to Showcase the Latest Cable Design Product CableBuilder at Wire 2016
Cimteq will be exhibiting three new innovations this year, as well as the latest release of their flagship cable design and quotation product, CableBuilder, featuring new productivity tools.
February 29, 2016
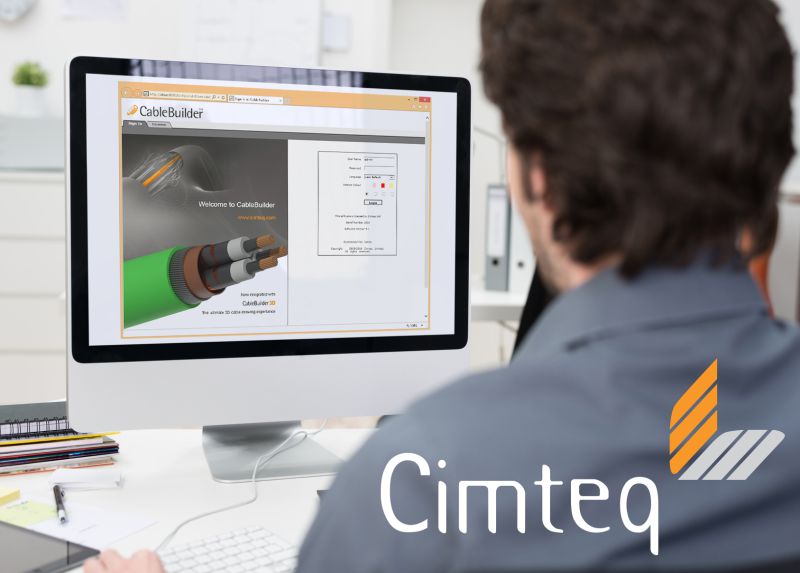
CableBuilder 3D – A complete 3D modelling CAD package that produces 3D models at the touch of a button and renders them to photo-realistic quality. With CableBuilder 3D there is no need for expensive product photographs when producing datasheets and catalogues.
CableMES – The most modern and flexible Manufacturing Execution System to date. It relays manufacturing instructions to the shopfloor, monitors machine running parameters and tracks order progress, quality and performance (OEE). With powerful analytical tools, it helps companies identify performance and quality problems quickly to minimise waste.
CableSuite – Is a joint venture between Cimteq and InnoVites. CableSuite is the most complete and fully integrated enterprise software that supports all business functions of cable manufacturers. CableSuite is designed to support the specific needs of the wire & cable industry in design, engineering, warehousing & logistics, sales, production, planning and finance.
Cimteq will have experts at hand on their stand to help you choose the best solution for your company and advise you how to use them to maximise their rewards.
Make More Wire than Dies with Die Quip
The goal of making more wire per die is easily reached with a Die Quip die finishing machine.
February 29, 2016
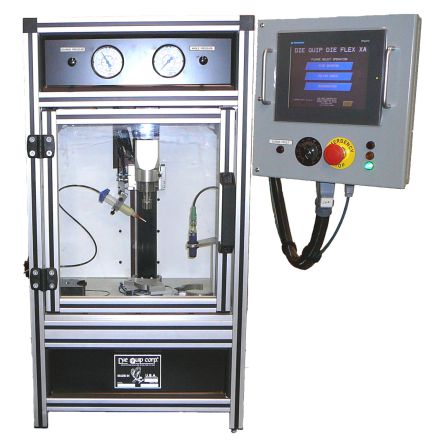
As a global manufacturing leader, Die Quip has established a line of machines to grind, polish and size dies in a quick, efficient, accurate process eliminating operator error and guesswork. Better dies pull more wire and cause less production problems so we have designed stand alone machines for finishing dies in all sizes, and for larger production runs we build work cells to keep maximum efficiency and eliminate downtime from size changeovers. Die Quip’s approach to a modern die shop brings huge benefits to the whole production process by implementing a workflow system that sets procedures and incorporates training to maximize each machine’s capabilities.
The company has designed many extensive training options and on site consultations that teach operators how to use our equipment, chooses diamond tooling for maximum results and different methods of making dies. Its technicians spend time in customers’ facility designing a program customized to meet their production needs and provide reference materials such as our exclusive Die Training Handbook.
Die Quip’s customer service doesn’t end with the purchase order. It supports customers through installation, training and troubleshooting for the life of the machine. Die Quip builds relationships with customers worldwide through a network of industry representatives that can support, translate and train in your facility.
As the die industry changes, Die Quip is still here as a leader providing quality solutions to all of the die making questions. It believes the key to fast, easy production lines is in the quality of the die; so come improve yours today with a visit to the stand at WIRE 2016, Dusseldorf #9/D06-01.
Solutions for Electrical Wire Drawing
CONDAT has used its 160 years’ expertise in lubricant technology to develop a comprehensive range of products dedicated to the electrical wire & cable market.
February 29, 2016
Leader in the mechanical wire drawing market, Condat has earned international reputation for supplying the steel wire industry with its famous brand name VICAFILTM.
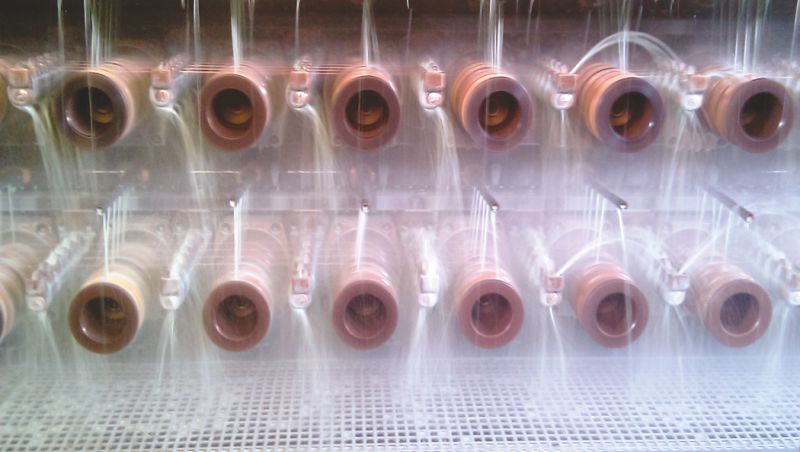
A wide range of high performance lubricants
- For Aluminum Wire drawing, VICAFILTM TFA neat oils range has been designed to offer both low residues and extended operating life. Its specifically formulated additives package minimizes thermal oxidation maintaining longer lubricant performance. The bath life is increased and thus reduces maintenance costs. Thanks to their low viscosity, VICAFIL TFA 1167 and VICAFIL TFA 1460 reduce lubricant consumption whilst offering high lubricity. These formulations are suitable from the rod breakdown to the final wire drawing operations.Condat also offers a range of stranding lubricants leaving very low residues and offering perfect compatibility with the subsequent plastic extrusion processes: perfect adhesion and no bubbling.
- For the drawing of Bare Copper Wires, VICAFILTM TCU concentrated soluble lubricants provide consistent and reliable performance. The high lubricity of the emulsions reduces wire breakage while the additives package has been formulated to keep the machine clean, reduce foaming and increase the emulsion stability. This range also offers specific products for high temperature wires (silver, tin or nickel plated copper wires): synthetic based formulations which reduce the buildup of particles that can cause wire breakage, and soluble emulsions which offer high lubricating power for the more demanding drawing of Nickel coated wires. Specific cooling synthetic solutions are also available. They provide cleaner wire surfaces, optimum metallurgical properties and good corrosion protection for the annealing cabinet.
- A full range of complementary products helps you in the management of the bath. Including products to clean your installations, bath maintenance additives as well as protection products for bare wires in order to avoid corrosion and extend shelf life.
Promoting an eco-responsible policy, Condat’s R&D department accommodates the latest regulations and focuses on developing safer products for both people and the environment, without compromising on performance. Several production sites, all ISO 9001 certified, enable Condat to deliver top quality products everywhere in the world through its distribution & service network.
Always willing to improve its customer relationship with tailored services, Condat is looking for additional local partnerships and distributors worldwide. In case of interest, please contact Condat’s team at wire@condat.fr.
Eder Engineering at Wire Dusseldorf 2016
EDER will offer a variety of latest technological developments in drawing die-tool working machines, allowing the users to benefit by longer life of the die and higher tonnage drawn
February 29, 2016
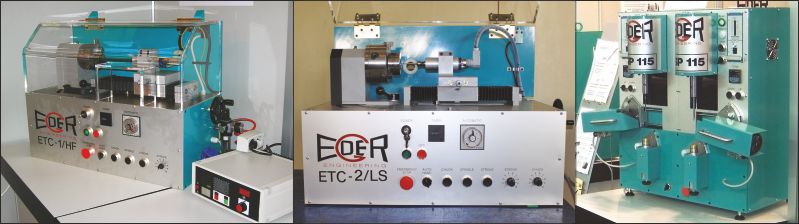
Offering innovative and high value added concepts with nearly 70 years of expertise in the field of reconditioning die working equipments, EDER-Austria is sustaining and developing its distinctive leading position across the globe and is presenting its various technologically leading equipments at Hall 10/C42- 01 at Wire Duesseldorf 2016.
Some examples of unmatched EDER machines at WIRE 2016 that will be presented life by EDER´s staff and on a video wall:
“ETC-1/HF” Efficient tungsten carbide die grinding and polishing equipment with a very large work range of between 0.10 up to 20 mm dia.
Particularly for refurbishing of the continuously growing quantity of PCD dies in use, a unique Ultrasonic machine, model “USP-TWIN”, with two workstations has been developed, which can efficiently work all die-sizes in a large range between 0.05 up to 8.0 mm dia. It can be operated by one only person, same time doubling output.
“ETC-2 LS” – for sizing and polishing tungsten carbide dies in the larger bore size range, of between 1.0 up to even 40 mm dia.
The company would be present at the booth 10/C42-01 to discuss industry’s new trends and concepts, particularly showing ultimate solutions for the efficient reconditioning of dies and would be pleased to visualize the many benefits, outstanding potentials and capabilities of EDER machines.
.
EJP Defines New Benchmark in Drawing Technology
At Wire 2016, EJP will present its new generation of drawing machines, which make drawing operations simpler and more reliable
February 29, 2016
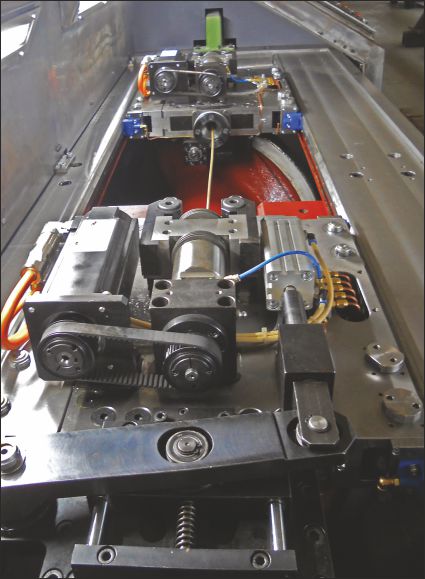
At Wire 2016, EJP will present its CDS-TQ 50/100 drawing machine, a new generation of its CDS-TQ series with numerous innovative design features: the servo-electric actuation system for the drawing jaws operates without any hydraulics and the employed torque motor without any gears. The new machine offered by EJP provides more flexibility in bar and tube drawing, cuts set-up times and reduces the maintenance effort.
At the trade fair, EJP will present its new generation of drawing machines, which make drawing operations simpler and more reliable: electrics have replaced hydraulics, a torque motor makes gear units superfluous. All this has made the machine design less complex and more compact.
The main shaft of the drawing unit is directly driven by a torque motor capable of generating a high torque at the low speed required for the drawing operation. As the new machine has no conventional main motor or a gear unit, there is no power loss that would otherwise result from the existence of a gear. EJP has also reduced the required maintenance effort as the drive components of the new machines have been designed without any ball bearings, gear wheels or oil lubrication.
An entirely new feature is the electric control and actuation system for the drawing jaws. With this technology, which is unique in the world, EJP has set a new benchmark in drawing equipment design, as the jaws can be closed and opened much more easily now. So far the state of the art had been to use hydraulic cylinders that would close and open the jaws. That, however, required sophisticated synchronization between the actual drawing speed and the positions of the two slides.
In the new, combined EJP drawing machines, servo-motors actuate the drawing jaws. The motors directly control the actuation of the jaws based on the contour of the drawing curve “in real time”. The advantage is that the jaws can now be closed or released without the previously necessary detour via the hydraulic system and without the associated control of the hydraulics, which had to take into account the current drawing speed. Moreover, the risk of leaking hydraulic fluids has now been eliminated and with it any contamination that may result from such fluids.
The servo-electric actuation of the drawing jaws also provides the advantage that they can handle solid material of different diameters. The V-shaped jaws may handle diameters from 11 to 15 millimeters. Size changes within that diameter range can be conveniently implemented at the control desk, without any manual intervention.
Such a system of electrically actuated drawing jaws has been in operation at a non-ferrous metals producer for almost a year, and has proved highly reliable. A second system is currently being installed at a producer of aluminium bars.
Jacques Paraskevas, Managing Director of EJP, sees the new machine as an innovation platform. “The machine which we will show at Wire 2016 combines all functions and features that we consider as useful and feasible for the future requirements placed on drawing equipment. The new machine underpins our technology leadership in the design of drawing machinery. Our designers’ approach had been to “design simpler and make it better”. Servo-motors make complex hydraulic equipment superfluous and the torque motor ensures that the required high torque will directly act where it is needed, namely on the main shaft.“
Further exhibits:
Two-roll straighteners
EJP will also show two-roll straighteners of the SP series. EJP is the only manufacturer who optimizes the contours of the rolls in every straightener supplied by means of computer simulations to meet the specifics of the straightener’s future application. In coil-to-bar production, the straighteners operating in line with the combined drawing machines achieve perfectly straight round bars.
The portfolio of machines ranges from straighteners featuring a straightening force of 1 t and designed for the straightening of short bars through to machines generating straightening forces of up 600 t for round stock, hot rolled or surface treated with up to 200 mm in diameter.
Butt welding machines
As a premiere, the subsidiary EJP Italia will present the new butt welding machines of the TX and hTX series. These machines feature an electronic system that allows them to weld material with a maximum diameter of 25 mm at significantly lower electric power levels. Also customized solutions can be provided at any time.
Enkotec to Display Most of its Products at Wire Dusseldorf
ENKOTEC A/S continues to make headlines with its high-performance machinery for nail production.
February 29, 2016
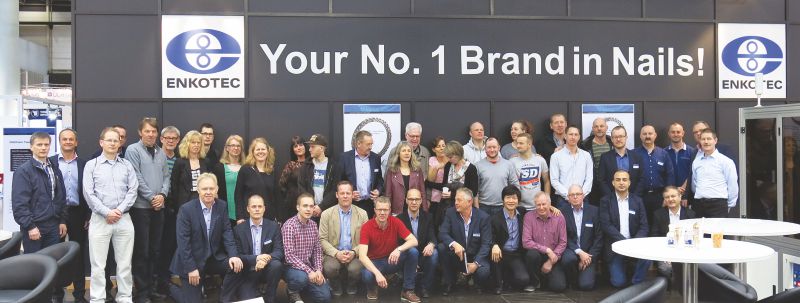
At this year’s Wire Düsseldorf show, ENKOTEC will display most of its product programme, featuring great news as usual.
ENKOserv for best performance: ENKOTEC will have areserved area in its booth, where staff will show customers how ENKOTEC can offer help with improving production efficiency on existing machines.
ENKOline, 2,500 npm, wire: ENKOTEC A/S and BAUSSMANN Collated Fasteners GmbH will jointly exhibit a high-speed in-line nail manufacturing line including an ENKOllator wire coil collator, an ENKOnail+ machine and an ENKOroll thread-rolling machine.
ENKOline, 1,500 npm, plastic: A second machine line jointly exhibited by ENKOTEC and BAUSSMANN features abrand-new high-efficient plastic stick collator paired with a high-speed ENKOnail+ machine.
ENKOllator paper stick: ENKOTEC will also show its new paper stick collator, which has been designed for making collated sticks of nails with many new features for reliable and cost-efficient production.
ENKOfeed &ENKOveyor: The three machine set-ups will all include the brand-new high-speed ENKOfeed nail feeder, which comes in a clockwise or counter-clockwise version, as well as the new magnetic ENKOveyor for the transportation of nails, available in different sizes and with different size hoppers.
ENKOnail with ENKOpack: Finally, ENKOTEC will demonstrate an ENKOnail machine, intended for small and midsize capacity needs, which will be running together with ENKOTEC’s movable ENKOpack nail-counter packaging machine.
Managing Director, Bent Just Petersen: “We hope that many of you will visit the Wire 2016 show in Düsseldorf, where ENKOTEC will be pleased to welcome you at our biggest booth ever. Apart from high-efficient nail machinery on display, you will be introduced to many new ENKOTEC service products, as we wish to improve our service and customer support even further in 2016”.
Flymca & Flyro to Showacse Its Latest Developments at Wire 2016
The stand will be showing some interesting pictures regarding projects made during last two years
February 29, 2016
Once again, FLYMCA will be present at the most well known, important and attractive exhibition with many interesting news about their equipment last developments and up-dates. The stand will be showing some interesting pictures regarding projects made during last two years so that all visitors will have the opportunity to know about them. As for instance:
- For power cable market: some new rigid strander developments improving the features of the previous models. Either for bobbins Dia. 630 or 800 mm DIN or even for both bobbins on the same machine, allowing factories to use advantages of both; automatic bobbins loading process either by side carriages at 90º or at 45º; higher rotating speeds to get production improvements; smooth, precise and constant wire tension control to achieve high quality conductor standards, etc….
- For steel wire ropes: larger capacity of machinery for bigger ropes. Tubular and planetary closers able to manufacture bigger ropes in lower production time thus increasing the machine productivity. The use of special new material let us achieve better results allowing improvements mainly in reliability, low maintenance and therefore longer life time expectancy.
- Control and special cables made on planetary stranders using advanced solutions for really smooth and fine tension values on elements, including double control systems either in the cradles and in the formation with wifi communications to achieve final special cable features.
- For greenhouse: special customized machinery to improve the production of steel strands composed of 2 and 3 wires, reaching as well higher outputs.
- For CTC (Continuous transposed conductors) a long experience on this traditional market let us offer state of the art combined solutions to achieve high quality cables with larger production.
Sister company FLYRO will be proposing its large inventory of available second hand machinery. As known by its customers, FLYRO proposes used machinery mainly still installed and in working condition but also offers services of dismantling, refurbishing as well as production of new electrical cabinets.
FENN to Display New Machine and New Design at Wire 2016
FENN, with over 115 years of experience, is a global supplier of state-of-the-art metal forming machinery including: Wire Flattening and Shaping lines, Rolling Mills, Turks Heads and Drawbenches.
March 3, 2016
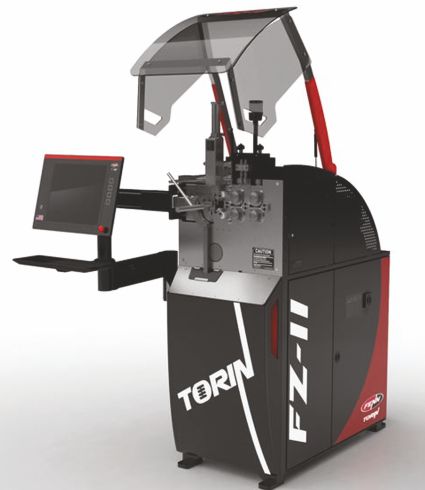
At Wire Dusseldorf 2016, FENN will display the enhanced 2016 Torin FZ series spring coiler as well as the design for the new FENN FSL Series Wire Flattening and Shaping line.
Show attendees will have the opportunity to see the updated FZ series spring coiler in action. This enhanced machine offers higher output speeds, and part reliability with added features for increased operator efficiency. The FZ series caters to spring and wire form makers around the world by offering multiple languages on its touch screen HMI. The versatile FZ Series machine is capable of making seven different types of springs including Compression, Extension, Torsion, Gun Magazine, Wire Forms, Belting, and Rings, all on a single machine. Constant Force capability is also available.
Fenn’sTorin FZ Series is available in a variety of models to accommodate wire sizes ranging from .076 mm to 19.05 mm with a multitude of exciting new features including:
- Integrated tool tray for added convenience
- New ergonomic guardpromotes operator safety
- Your length gauge is easy to view atop Torin’s new built-in mount
- Easier-to-access grease points to keep your machine in top shape
- Left hand configuration available for special applications
- Intuitive state-of-the-art controls
- Fast and simple program creation
- Sleek, updated styling from FENN, an industry work horse
FENN will also be unveiling the concept for its highly anticipated FSL Series Wire Flattening and Shaping Line. Fenn wire lines have set the standard for precision, high speed production and versatility with installations worldwide. FENN’s wire shaping lines have been utilized in a variety of industries including the production of photovoltaic wire for the renewable energy industry and wedge wire for the oil and well screen industry.
Gauder Group at WIRE 2016
New machines, second-hand machines, services and bows
February 29, 2016
BOW TECHNOLOGY
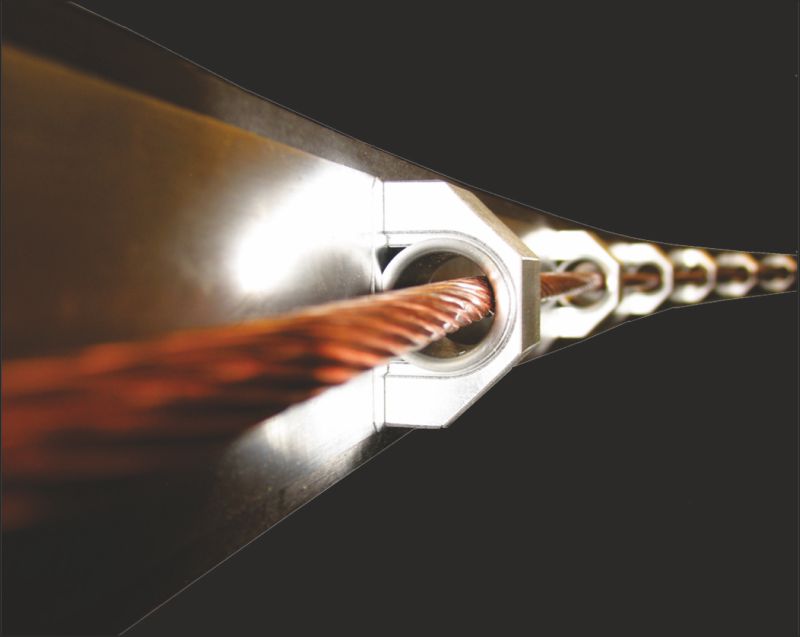
Why BOW TECHNOLOGY? Based on 60+ years of experience in double twist, the BOW TECHNOLOGY member of the Gauder Group designs and manufactures high-technology bows in a real technical partnership with the most renowned cable makers. The dedicated team carries out comparative analysis and trials to customize and upgrade obsolete designs as well as technical studies of bow parks.
The result? A wide range of 500+ customized bow designs – as well as the exclusive and patented GreenBow2 enabling energy savings – are available for 25+ well-known brands of double twist machines (560 – 2500 mm) such as Cortinovis, Lesmo, Niehoff, … BOW TECHNOLOGY is the right partner for everyone concerned by a higher level of performances and an extended lifetime of the equipment.
Cable Services & Systems
The C2S division of the Gauder Group takes care of all wire & cable production lines, whatever the brand of the rotating equipment. C2S recently reinforced its Engineering & Commissioning team with ex-Lesmo and ex-Cortinovis Engineers.
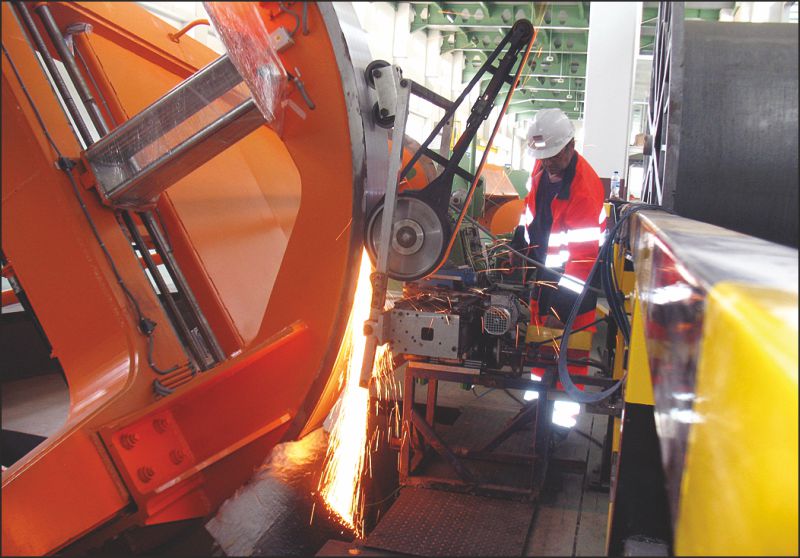
70,000 identified spare parts references are distributed worldwide through 4 logistic platforms, including high technology bows. A team of 55+ technicians is continuously trained to handle troubleshooting and urgent repairs and the division also offers dedicated services such as periodical visit contracts, transfer and restart operations of complete lines, training and consulting possibilities. C2S is being assigned upgrading projects for all brands as well, either mechanical / electrical interventions or process improvements with transfer of know-how.
DALOO
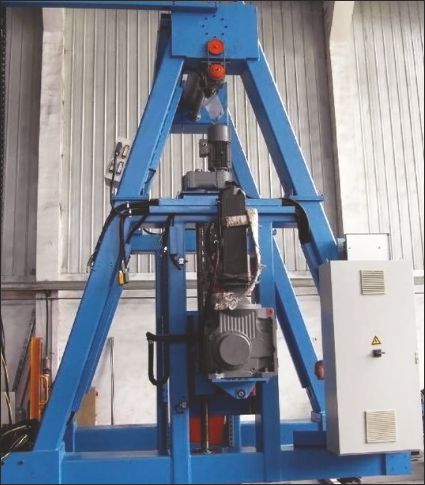
DALOO, a member of the Gauder Group, is the logical extension of the group global offer for cable producers wanting an attractive alternative between new machines made in Europe – with higher cost – and second-hand machines – without guaranteed performances.
Its complete stranding lines and accessories for the production of power and communication cables are delivered worldwide : rigid cage stranders, taping lines, rewinding lines, take-ups and pay-offs, pulling caterpillars … and now tubular stranders.
The designs as well as the manufacturing (in Changzhou) are based on European experience (proven Gauder Group methods) following strict quality criteria.
GAUDER
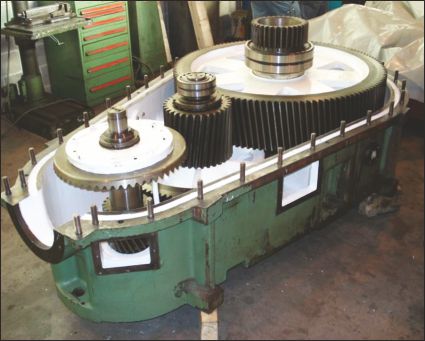
GAUDER s.a., on which the Gauder Group was found, is at the head of the largest stock of machines for the wire and cable industry in Europe. “Creating solutions together”, the company is the ideal partner to set up “ready to manufacture processes” from its 1000+ machinery warehouse (drawing, stranding / cabling, screening / taping / armouring, wire coating, extruding, coiling / rewinding, …) for the production of wires, conductors, cables, ropes or steel products.
The Belgian based supplier has today become a key player in reconditioning second-hand machines. GAUDER is N°1 in complete plant reselling and gained – among other skills – a specific know-how in lead extruders revamping. Last but not least, the company markets new MAPRÉ extruders ranging 38 – 150 mm available with accessories.
A free shuttle service is organized daily from the booth to discover the stock of equipment displayed in 20,000 sqm warehouses as well as see a reconditioned Drum Twister for power cable. Visitors may browse the on-line stock at www.gauderonline.com to prepare their visit.
POURTIER

POURTIER, France, develops and produces high quality stranders, cablers and armouring lines for ferrous and non-ferrous cables. These machines are made in Europe with the highest standards in design and manufacturing for the production of all types of power cables, from Low and Medium voltage up to High and Extra-high Voltage : overhead cable (including new development with various shaped wires) and insulated cable, AC type (using high quality Milliken conductor) or DC type (using large round compacted cross sections).
POURTIER has made recently impressive achievement in the field of submarine and umbilical cables with the supply of large armouring lines and laying-up lines. The Company is continuously extending his range of machinery to meet the Customers’ needs.
Worldwide leaders in rotating machines, POURTIER and SETIC (a member of the Gauder Group as well), are offering the widest range of twisting/stranding solutions to cable makers and steel rope producers.
.
SETIC
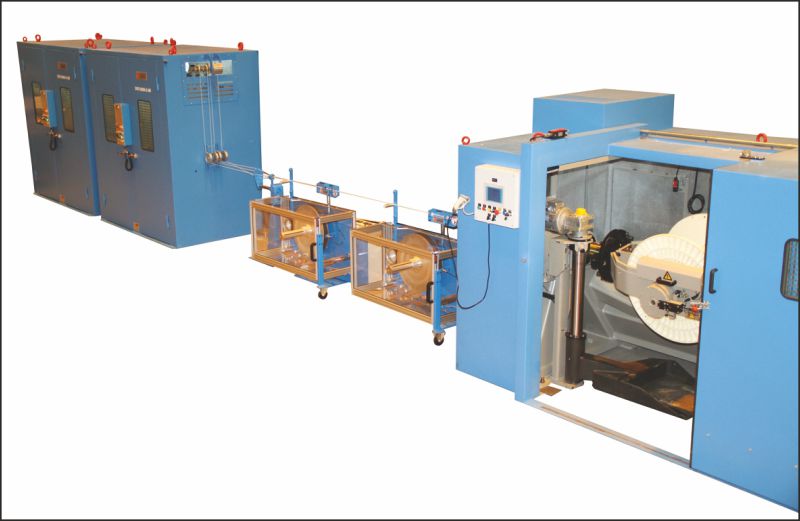
The Company is continuously developing new lines and new concepts for non-ferrous cables in order to meet the Customers’ needs such as tandem “mica taping/bunching”, special high speed lines for battery cable, new high speed lines for special and instrumentation cables, …
SETIC combined with POURTIER (also a member of the Gauder Group), are worldwide leaders in rotating machines offering the widest range of twisting/stranding solutions to cable makers.
Specialists for Wire and Tube Cleaning
The company is a leading producer of cleaning systems for the treatment of wires, cables and strips
February 29, 2016
For the eleventh time, GEO-Cleaning Technology GmbH (GEO) is presenting its comprehensive portfolio of cleaning systems and components for the surface treatment of wires, cables and strips at the Wire Exposition in Dusseldorf.
GEO offers a wide range of solutions for the wire and cable industry, either as a comprehensive, “turnkey” system, as an upgrade or as a complement to existing processes.
Both in single lines for wire, cable and pipe as well as in multi-wire cleaning applications, ultrasonic modules, high-pressure nozzles and steam jets, integrated in space-saving in-line systems with fluid management, guarantee outstanding results in the non-contact and “pore deep” aqueous cleaning.
Mechanical systems with textile materials, such as the cost-effective and flexible wiper “Primary Wire Wipe” (PWW) are suitable for the reduction of drawing residues and loosely adhering particles and as well as for the application of liquids.
Systems equipped with rotary brushes (DRB-WCS), both for dry as well as fluid assisted cleaning, compliment the options for optimizing the surface quality of wires, cables andpipes.
Welding wire manufacturers will find, besides the in-line cleaning after the drawing process, systems for coating with welding wire finish and test systems for final quality inspection of welding characteristics.
The KFP-V system for the removal of misprints on any, flat or round cable insulation in continuous operation at line speeds of about 50 m/min will be of interest for cable manufacturers.
Furthermore, producers of tubes will find a visit to the Wire Exposition worthwhile. Manufacturers of tubes- or tube products for the aerospace industry, energy and automotive industry, OCTG, building and construction or medical applications achieve outstanding cleaning results of the outer and, depending on the form, diameter and length, inner surfaces with custom-tailored solutions in both the continuous in-line operations as well as for finished products.
A wide assortment of accessories supplements the product range. In particular, these include powerful and economical Air Wipes for the drying of wire, cable, strip, flats and other profiles even at high line speeds.
For a variety of cleaning operations inverted spiral brushes are recommended. The brushes are available in a broad range of sizes with a variety of synthetic and metal filaments.
Hangzhou Sanli to Exhibit its Cutting-edge Continuous Hot-wind Tempering Furnace
The company exports is heat treatment production lines and various furnaces to a host of countries
February 29, 2016
Hangzhou Sanli Furnace Co.,LTD is a Chinese company specializing in the design, manufacturing of the complete production line for the heat treatment of various fasteners, continuous hot-wind tempering furnaces, continuous protective atmosphere quenching furnaces.
With ISO9001:2008 and C.E certificate, its products are sold to the United States, Canada, Turkey, Europe, Argentina, South Korea, India, etc. and gain the deep confidence from our long-run customers in the sectors as bolts, clips, spring cushion, screws, bearings, standard parts, hardware, chains, stamping parts, cast products of high chrome and high manganese, rollers.
In 2016 Dusseldorf Wire and Cable Exhibition, Hangzhou Sanli is going to show one of its continuous hot-wind tempering furnace, 8Kw, with an air-cleaner on top. It exports regularly to the Indian market since 6 years ago and will continue to concentrate to better serve our customers.
Feel free to visit the new website: www.sanlifurnace.com
Stay Efficient with Spare Parts from Heinze & Streng
A comprehensive product range on display such as Nickel Band, Coils and Rings, Nickel Tubes coated brass and copper, Carbon Fiber Bows for all types of drawing machines, special materials, etc.
February 29, 2015
Heinze & Streng GmbH based in Germany is an international operating trading company with long terms experience and well known in the wire and cable industry.
Our wide ranged product line includes various spare and wears parts, equipment and complete solutions based on customer’s request.
H&S top products are:
- Nickel Band, Coils and Rings (99,5% pure Nickel in all dimensions )
- Nickel Tubes coated (from 0,05mm up to 0,5mm) , brass and copper
- Carbon Fiber Bows for all types of drawing machines: (Niehoff, Samp, Lesmo, Henrich, Caballe, Maillefer, Northhampton, Setic …
- The special material – braided carbon fiber- makes the bows absolutely energy efficient and long-lasting.
- The new innovation of mounts and the eliminated wear plates guarantees easy handling for maintenance and saving costs
- Carbon brushes and holders as per customers’ instructions
- All kind of high tech ceramic special seals (acid-resistant)
- AirWipes ( most efficient method to clean wire) – robust system, long lasting material, low noise, easy handling , low energy consumption for bare and insulating wire
Heinze & Streng is going to roll-out their business to the Indian Market and concerning to the long time experience including all aspects of quality assurance, plant maintenance, materials management logistic and sales and supporting of our reliable partners we are on the right way.
KEI to Showcase Its Wide Range of Stainless Steel Wires in the Exhibition
KEI is one of the pioneer producers and exporter of Stainless Steel Wires since 1994, having certifications of ISO 9001 : 2008, ISO 14001 : 2004, OHSAS 18001 : 2007 and PED Certificate
February 29, 2016
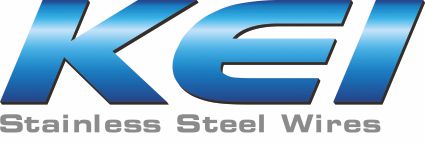
KEI Industries Ltd is India’s leading producers of Stainless Steel Wires and Electric Cables. In Wire 2016 Exhibition in Dusseldorf City of Germany, KEI will be showcasing its wide range of Stainless Steel Wires in the exhibition.
Wire 2016 – Dusseldorf exhibition will give chance to KEI Customers and suppliers to meet and experience KEI products and will give common ground for enhancement of business in coming market scenarios.
KEI is one of the pioneer producers and exporter of Stainless Steel Wires since 1994, having certifications of ISO 9001 : 2008, ISO 14001 : 2004, OHSAS 18001 : 2007 and PED Certificate covered by Directive 97/23/EC for its stainless steel wires. Exporting to over 50 Countries worldwide.
KEI Stainless Steel Wires includes Industrial use Wires, Spring Wires, Braiding Wires, Weaving Wires, Knitting Wires, Cold Heading Wires, MIG Wires, TIG Wires, Welding Wires and Wires for Kitchen Applications and general use.
KEI’s have modern production facility equipped with state of the art machinery and in house die maintenance and polishing room. KEI’s well experienced quality persons ensure one the best quality wires which tested and assured of proper quality at its in house laboratory equipped with modern equipments like Spectro meter, radiation check meter, Ultimate Tensile Testing machines imported from Europe, Hardness, surface checking machines, etc.
KEI Produces wires from diameter of 0.07 mm to diameter of 7.00 mm in various grades and tensile strengths.
KEI offers wires in packing of DIN standard plastic spools, Continuous coils, Wooden Drums, Mild Steel Carriers, Cardboard Barrels, Tubes and MIG spools. Customized packing as per requirements of customer is also available.
KEIR to Highlight its Alumina Ceramic Guides, Air Wipes and Flyer Bows at Wire 2016
KEIR’s patented SureShot and SplitShotAir Wipes provide a far more effective drying method that does not depend on high-volume air consumption
February 29, 2016
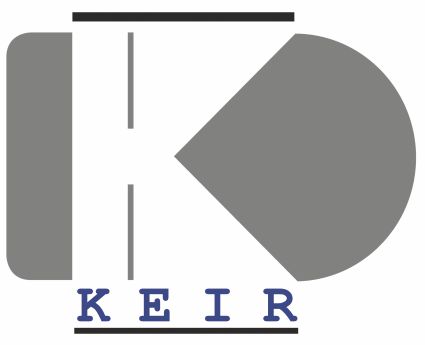
KEIR Manufacturing, Inc is an American based manufacturer of high-purity 99.8% Alumina Ceramic Guides, the Frontiersman™ line of Air Wipes, and Composite Flyer Bows serving the global wire & cable industry. These items will be displayed and highlighted at Wire 2016 in Dusseldorf. It is dedicated to making products that enable manufacturing processes to run more efficiently and productively through the application of leading edge materials. KEIR’s solutions are focused on continuous process improvement, energy savings, and longer operating life.
KEIR’s patented SureShot and SplitShotAir Wipes provide a far more effective drying method that does not depend on high-volume air consumption. Its efficient design yields effective drying using a very low volume of compressed air and lasts much longer than other brands due to the rugged ceramic insert lining the wire path. This equates to over 25% reduction in compressed air usage and an operating life of years versus months.
KEIR’s triaxially braided composite Standard and BackBone™ flyer bow constructions have greater durability than layered/laminated designs allowing them to take more hits and endure higher stress yielding increased operating life and less machine downtime. The more aerodynamic BackBone™ design functions at lower power consumption and higher TPM with improved wire quality and a further reduction in bow breakage. Up to 40% less energy (AMPS) is used along with a decrease in wire scrapped.
KRENN Presents KAMAX Product Range at the Wire2016 for the First Time
KAMAXHydraulic presses for the compression testing of wire samples with a maximum diameter up to 45 mm and a piston pressure of 500 to 5,000 kN will be introduced
February 29, 2016
KRENN is the specialist in steel cutting! Founded in 1947 for the production of technical springs, Krenn has established its position on the international market as the most versatile provider of steel cutting devices and tools.
In the Krenn product range you will find manual bolt cutter, pneumatic and electro-hydraulic cutting devices, partially battery-operated; furthermore hydraulic cutting heads and straighteners. The product range also features specialized devices for the cutting of chains, wire ropes and steel armored cables.
With the acquisition of the steel cutter and testing press division from KAMAX in 2015 the product range of Krenn has significantly expanded.
For the first time themedium-sized German company with a tradition of almost 70 years presents the high-quality hydraulic KAMAX steel cutters at the Wire 2016. KAMAX Hydraulic presses for the compression testing of wire samples with a maximum diameter up to 45 mm and a piston pressure of 500 to 5,000 kN will be introduced. Also available as double press with integrated cutting device as well as special designs.
Exceptional Offering from the Wire and Cable Manufacturing Competence Leader
With an astonishing 4000 line deliveries and several new products, Maillefer offers a unique competence for the wire and cable industry
February 29, 2016
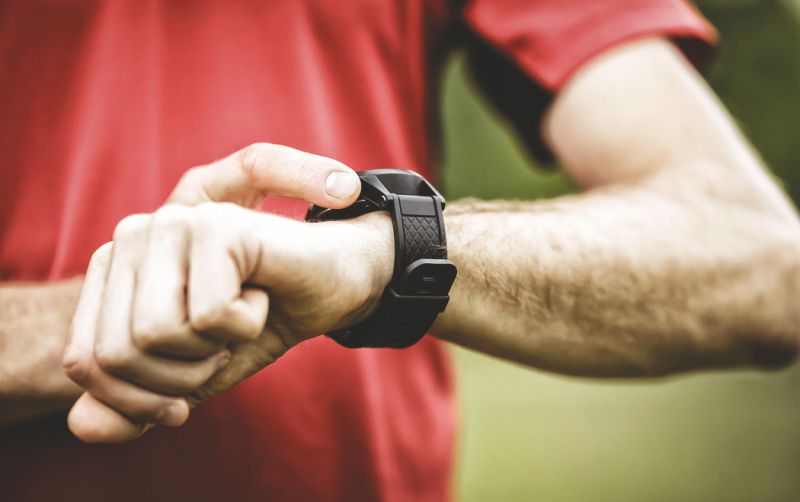
Maillefer is the only W&C technology supplier in the market with roots in cable manufacturing. This combined with the widest application coverage and over 4000 line deliveries has created unique competences available now for our customers via several new products. The company is known for introducing many novelties which enhance the competitiveness and responsiveness of wire and cable manufacturers. Competence counts!
Maillefer Factory System is a qualified concept to plan and realize a greenfield factory with the lowest possible risk and cost. Maillefer is the only supplier in the global market having experience of the full delivery. Maillefer Factory System is a unique way to outsource a factory project right after you have defined the end product, and it is suitable also for expansion of current production facilities.
Maillefer Consultation is a new service entity that is built around the wire and cable production process. It exploits our core knowledge into individual advice and process skill improvements of wire and cable manufacturers.
Maillefer will launch two new Value Packages. Maillefer Plus Value Package is a whole new way to quickly match increased demand with no pre-investments in production line(s). It is a plug-and-play solution for manufacturers, who want to react fast to the emerging demand and set-up their production only after an order is in place. Cable quality gets a totally new meaning with the new Cable Roundness Value Package with which production is controlled under very precise tolerances. This brand new curing concept guarantees utmost roundness in high voltage cable production.
The Three Layer Co-extrusion Crosshead ECH 200/240 TL redefines the production of big power cables. It applies all three layers on the cable core simultaneously, and allows the placing of all three extruders on one side of the line. This makes the crosshead extremely user and space friendly.
A new application − Aviation gets its own production line, the Aviation Line TEL 25XF. Maillefer has also reached the ultra-high speed of 1000 m/min with its new Fiber Optic Cable Secondary Coating Line OEL 40 ///Explore which is designed for future production efficiency.
Further component novelties include the Air Cooled Extruder MXC 120-24D for preventing material over use, Quick Conductor Splicing QCS for greater productivity, Nitrogen Circulation System NCS for upgrade opportunities, and Micro ducts for pipes.
Maillefer’s unique R&D Center with the Vertical Pilot Line for cables up to 750 kV as well as simulations for polymer flows will be displayed on the booth.
The material know-how will be proven by demonstrations of how a rheometer for testing rubber curing parameters and our Curing Calculation Program NSS play together to give the best possible production run recipe. The new aviation cable line is proof of our expertise on fluoropolymer extrusion.
Mathiasen Machinery with its Inventory of Used Machinery at Wire 2016
The company also offers services such consignments, warehousing, appraisals and liquidation
February 29, 2016
Mathiasen Machinery buys and sells used wire and cable machinery internationally. Machinery is purchased for inventory or it can be sold on an exclusive basis. MMI has interest in locating individual machines, complete lines or entire plants. Consignments, warehousing, appraisals and liquidation services are also offered. MMI has buyers seeking all types of good quality used wire and cable machinery. It is serving the domestic and international Ferrous and Non-ferrous wire machinery markets. Their booth will display photos of a wide variety of second hand machinery. Customers are encouraged to bring their surplus machinery list and photos for evaluation. Mathiasen Machinery has been buying and selling used machinery in India since 1995.
Medek & Schörner’s Machines for Marking of Cables and Coating of Optical Fibres
The company covers virtually the entire spectrum of machines for marking cables and coding optical fibres; in particular for power, telecom, and data cables
February 29, 2016
Medek & Schörner will be presenting and demonstrating the following high-performance cable marking machines at the WIRE 2016 Düsseldorf fair:
Cable Marking Machines
- High quality gravure printers (LAN cables, control cables, etc.) for speeds up to 1200 m/min,
- Water Misting unit for the application of fine water dust for pre-cooling of the hot wire immediately after the extruder.
- Embossing meter markers / hot foil sequential meter markers for highest accuracy of length measurement (power cables, telecommunication cables, optical fibre cables, etc.)
- High performance ring markers for marking telephone wires, switchboard wires, automotive cables, LAN cables.
- Video system for monitoring the print quality of fast-running cable printing machines, e.g. allowing real-time inspection for bad quality and/or missing prints
- Laser Marking System for Cables
Optical Fibre Coating Systems
Top speed optical fibre processing systems:
- Optical fibre colour coding up to 3000 m/min;
- Ring marking of optical fibres;
- Tight buffering up to 1300 m/min;
- Fibre ribbon production with excellent ribbon planarity and for speeds up to 1000 m/min.
- CFU Production of compact fibre units
Thanks to the modularity and flexibility of its systems, Medek&Schoerner as one market leader in coating machines for optical fibres was able to implement other applications, including some outside the field of optical fibres:
- Copper wire insulation with UV varnishes (enamelled wire)
- Manufacture of dimension-sensitive precision micro flexible flat cables (FFC) using UV resins
For decades now, Medek & Schörner has been a world market leader in cable marking machines and optical fibre processing lines.
As the only company operating in this market segment, Medek & Schörner covers virtually the entire spectrum of machines for marking cables and coding optical fibres; in particular for power, telecom, datacables.
In the last decade India has become the most important and successful market for Medek&Schoerner, in particular in the field of optical fiber coloring and coating.
All big players in Indian Cable Industry are regular customers of Medek&Schörner: Sterlite Technologies Ltd., Birla Furukawa, Birla Ericsson, Vindhya Telelinks, AkshOptifibre, Finolex, HFCL, Polycab, Motherson Sumi, KEC, UM Cables, Lapp India, and many more.
The Meltech Company Presents at Wire 2016 with a Fresh Focus on Innovation and Design Engineering
The company is a UK based business specializing in engineered design solutions primarily for the processing and management of non-ferrous metals. Its capabilities include Continuous Rotary Extrusion (CRE) technologies, wire and cable handling machinery as well as strand annealing furnaces and ovens.
February 29, 2016
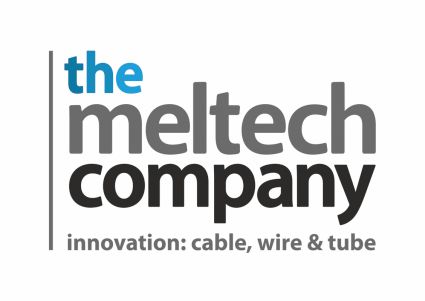
The Meltech Company will be showcasing its design engineering capabilities at Wire 2016, with its Strongform™ Continuous Rotary Extrusion (CRE) innovation taking centre stage.
For visitors involved in processing of Aluminium or Copper for applications such as refrigeration and air conditioning tubes or for electrical bus bars, power cables and trolley wire, the Meltech stand will be an important stop-off point at the show.
Strongform™ re-thinks the conventional CRE machine with a unique, fully visible cantilevered extrusion wheel and a substantially more robust machine configuration.
For non-ferrous metal processors, Meltech’s technology offers transformational productivity improvements with its exceptional process control, output efficiency and minimal wastage.
Meltech’s General Manager, John Stamp said: “Strongform™ is a real game-changer in CRE processing. Machine set-up times have gone from hours down to just minutes and downtime for maintenance and tool changes is reduced by as much as 90%. The incorporation of a new heat recovery process that allows waste energy to be recovered is also yielding energy savings of around 30%.”
Visitors to the Meltech stand (Hall 16/Stand F49) will also learn more about the company’s ongoing innovation in CRE capabilities, including its advancement of process applications for alloys such as Brass and Bronze and high value metals such as Sliver, Gold, Titanium and Zinc.
Other CRE developments on the show will include the technology’s versatility to convert non-ferrous metal powder, granulate and even scrap metal into new profile or rod materials.
Supporting its CRE innovation, Meltech will also be welcoming Wire and Cable industry visitors to learn more about their precision coiling and high performance cable handling machinery. With capabilities ranging from equipment for winding of 0.1 mm diameter medical wire to cable handling of 400mm sub-sea umbilicals, Meltech will be on-hand to discuss its full portfolio of engineered solutions in this field.
For the Wire Drawing industry, Meltech’s world-‐renowned range of strand annealing furnaces and de-gassing ovens will also be featured for visitors involved in supplying wire and strip for aerospace, automotive, spring making and surgical applications.
MIXER to Present its innovative Rubber & Thermoplastic Compounds at Wire 2016
Mixer is a manufacturer of rubber compounds and thermoplastic compounds for the insulation, sheathing and filling of flexible cables, rubber cables, power cables and flame-retardant cables.
The company produces cable insulation, cable sheathing, cable filling and masterbatch cable compounds, using both rubber and thermoplastics.
Our trademarked EKOPREN® products are based on halogen- free polymers and additives with low toxicity and light smoke emission. Customers can choose from heavy metal-free, high LOI and fire/oil/ozone-resistant compounds.
Nevatia to Dispaly its Metal Products in Wire 2016
Subtitle: The manufacturer of stainless steel wire and bright bars has introduced a new product line of stainless steel welding wire with brand name Nevinox.
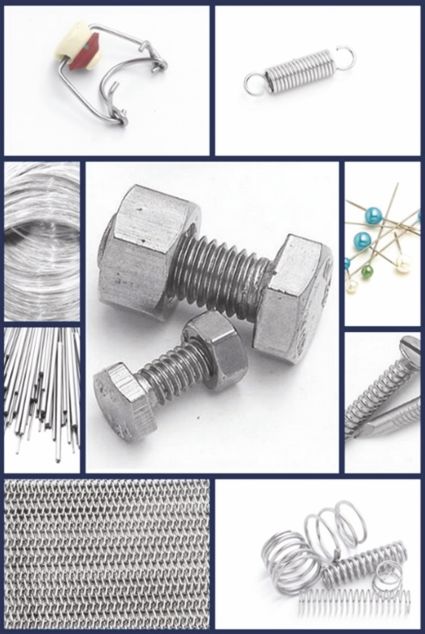
Nevatia Steel & alloys Pvt Ltd, was incorporated in 1988, with head office in Mumbai. The company has two manufacturing units at Tarapur (near Mumbai) with total manufacturing capacity of 9000 MT per annum.
Nevatia Steel products are used in manufacturing of springs, screws, rivets, nails, sieves, wire mesh, fasteners, wall ties, kitchenware, EPQ for baskets and trolleys, filler wire, electrodes, etc. They are also used in Automotive, Marine, Petrochemical, Food and Paper industries.
Our Products are exported across the Globe, including Argentina, Australia, Canada, Chile, France, Germany, Italy, Korea, Poland, Spain, The Netherlands, Turkey, U.K., USA, Russia, Malaysia and Vietnam.
Nevatia Steel is proud to announce that Nevinox® brand MIG (GMAW) and TIG (GTAW) stainless steel filler welding wire have recently been accredited with Deutsche Bahn (DB) approval in addition to prestigious approvals from Bureau Veritas for marine applications, TUV for pressure vessels & equipment and CE Mark.
Nevatia Steel is one of the leading manufacturers & exporters of Stainless Steel wire, Bright bars and is the first Indian stainless steel wire company to have triple certification of ISO 9001, ISO 14001 & OHSAS 18001. And now another…Nevatia Steel obtains TS 16949 accreditation.
A Recent Move…
As a part of sustained growth, the company has introduced a new product line of stainless steel welding wire with brand name “Nevinox”.
“Nevinox” brand includes Stainless Steel MIG, TIG, SAW and core wires for welding electrodes.
Plasmait’s Plasma Technology Based Heat and Surface Treatment Solutions at the Exhibition
The company will display its Plasma ANNEALERs for ferrous and non-ferrous wire, tube, strip, strand and ropes at Wire 2016, Dusseldorf
February 29, 2016
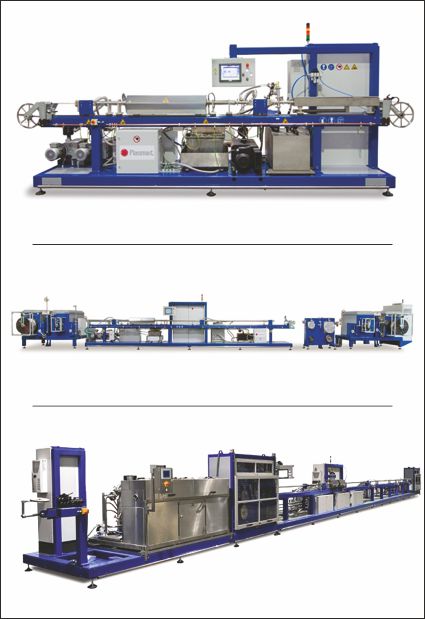
Plasmait is a supplier of heat and surface treatment solutions based on plasma technology for continuous and batch applications in the ferrous and non-ferrous metals industry. In Düsseldorf Plasmait will present the following machinery:
PlasmaANNEALER– HPA40 is a high output annealer for stainless steel, nickel and copper alloys. The machine is typically used for wire/tube sizes of 1-10mm OD. The annealer has an output of up to 170kg/h on austenitic stainless steels, 220kg/h on martensitic stainless steel and 300kg/h on copper materials.
PlasmaANNEALER– HPA10 is typically used for annealing of fine stainless steel wires (0,05-1mm) at speeds of up to 25m/s or in-line with rolling or drawing. Plasmait will present an integrated drawing/annealing solution for fine stainless steel wires together Schmidt MaschinenbauGmbH
PV Ribbon Line for high-speed rolling, annealingand chemical-free and flux-free tinning of super-soft PV ribbon.
Tinning Line for chemical-free and flux-free tin coating of copper or aluminium wire, tube or narrow strip.
PlasmaACT is used for lubricant adhesion on stainless steel and titanium alloy rods.
PlasmaPREPLATE is heat and surface treatment machine for heating, cleaning, deoxidation and surface activation for coating, hot dip and electroplating applications.
PlasmaCLEANER is a plasma surface treatment machine designed for pre-heating, surface cleaning, degreasing or deoxidation on ferrous and non-ferrous wires, tubes or strip.
Applications/Materials:
- Stainless steel nickel alloys
- Resistance/heating alloys
- Medical wires, tubes, strips, stranded wires and ropes
- Fine wire for filters, mesh, knitting
- Aerospace, electronics, oil and gas applications
- Copper and copper alloys, superconductor
- Plating, coating, enamelling and taping
- Precious metals and jewellery and decorative
- Titanium, tungsten, tantalum, molybdenum
- Welding wires
Plasma ANNEALERs for ferrous and non-ferrous wire, tube, strip, strand and ropes
Polyone to Exhibit Its New Polymer Solution ECCOH™5702 for Optical Fiber Cable Manufacturers
New solution eases installation of optical fiber cable and is highly flame retardant, non-halogenated sheathing formulations designed to facilitate the installation of optical fiber cable in existing conduit
February 29, 2016
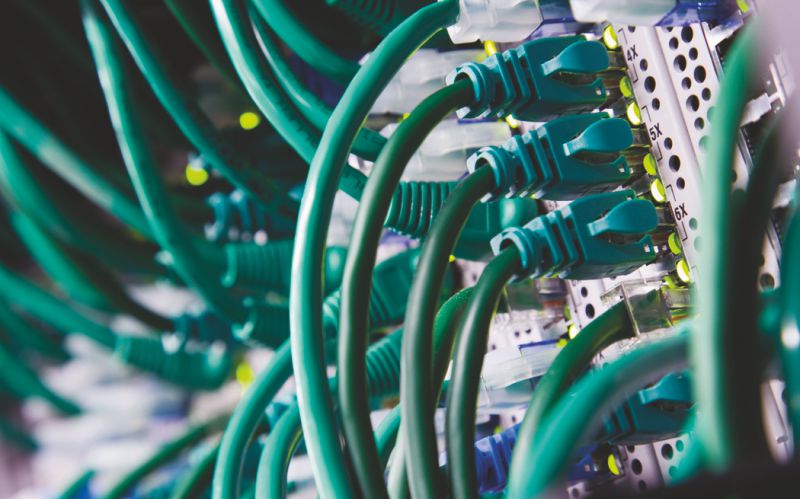
is easier to install in complex conduit and over long distances.
A new advanced polymer solution from PolyOne (Stall 9/B50) benefits manufacturers of optical fiber cable and their customers by significantly easing cable installation. The ECCOH™5702 solutions are highly flame retardant, non-halogenated sheathing formulations designed to facilitate the installation of optical fiber cable in existing conduit. Cable manufactured from these solutions has a low coefficient of friction (CoF) on its surface, easing installation even when conduit is complex or a cable must be installed over a long distance.
The demand for optical fiber cable remains strong, but much of the new cable installation must be done in urban areas, with cable running from larger networks to residential or commercial buildings and offices, so the cable often must be pushed through existing conduit. With ECCOH 5702 formulations, workers can more easily guide cable even through conduit with very complex designs and shapes, reducing installation costs.
Tests conducted by PolyOne on cable extruded from ECCOH 5702 specialty polymers reveal these have aCoF up to 75% lower than standard LSFOH (Low Smoke and Fume, Non-Halogen) formulations. In addition to the low CoF, these new formulations have a low melt viscosity, making them easy to process. Cable made with these materials exhibits excellent mechanical strength, low shrinkage and a smooth surface finish. For outdoor applications, ECCOH™ 5702 solutions can be UV stabilized, including formulations that pass the SEPAP accelerated aging test.
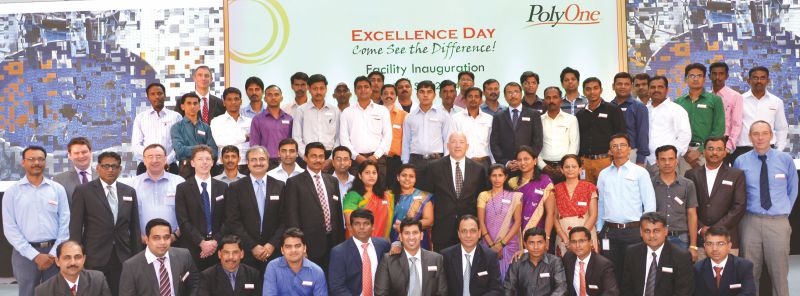
PolyOne offer a full range of specialty polymer solutions for manufacturing optical fiber cable, including for tight buffer, loose tube, fiber bundle, and sheathing applications, as well as almost every other type of cable. The global company has been active in India for many years, and in 2014 officially opened its new plant in Pune, from where it supports Indian wire and cable manufacturers with color and additive masterbatches and other polymer-based solutions.
.
PWM to Launch Its New Cold Welding Machines at Wire 2016
The ST40 air/hydraulic strip welder is designed for joining non-ferrous strip and tape used on armouring lines
February 29, 2016
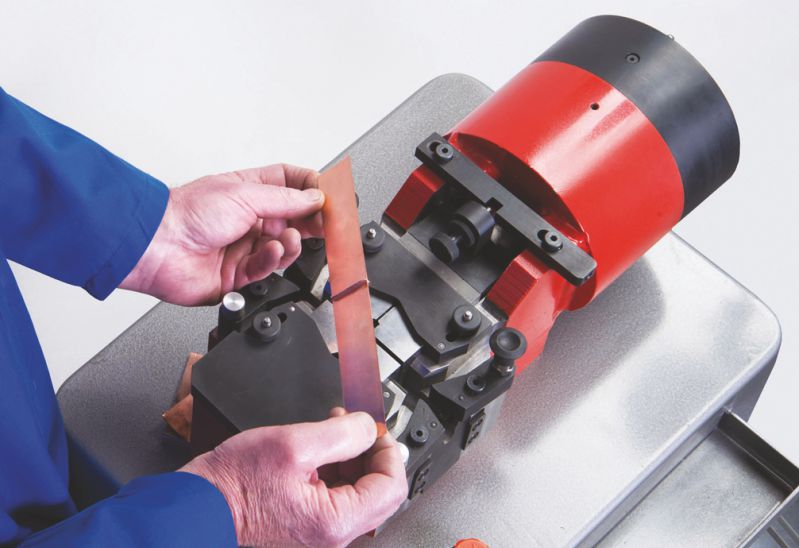
British company PWM, leading manufacturer of cold pressure welding equipment for over 30 years, will introduce two new cold welding machines at wire 2016 (stand 9B41).
The ST40 air/hydraulic strip welder is designed for joining non-ferrous strip and tape used on armouring lines. The machine, for strip and tape up to a maximum width of 45mm (1.772) and a maximum cross sectional area of 33mm² (0.0514²), produces strong, reliable bonds stronger than the parent material without loss of electrical integrity. No set up time is required, and, like all PWM welders, the ST40 is low maintenance, simple and cost effective to operate. Mounted on a trolley, the ST40 can be wheeled easily to the work area, saving effort and reducing downtime.
The new HP180T air/hydraulic cold welder is a versatile machine for wire sizes 0.30mm to 1.80mm (.0118” to .071”). Supplied on a trolley, it can be hand-held (within the limit of the air supply pipe) if required. Quick and easy to use, the HP180T enables the operator to produce strong consistent welds without effort. An alternative version of the machine (the HP180CP) can be supplied with a carry pack.
Also on show will be PWM’s powerful energy-efficient electro/pneumatic and electro/hydraulic rod welders for joining large rod sections from 5mm to 30mm (.197” to 1.181”), and its comprehensive range of manual cold welders, for wire sizes 0.10mm to 5.00mm (.0039” to .197”). This includes lightweight hand-held machines, as well as larger portable models which can be used on a workbench or with a trolley.
PWM cold welding equipment is made to high quality standards by skilled technicians in PWM’s own UK workshops. Dies are individually hand-made in matched sets, in standard or custom sizes, to suit round or profile wire.
QUEINS to Present Its Newly Manufactured, Heavy Duty, Chain-Type Caterpillar Capstan for Subsea Cable
The company is well-known for its main products such as all kind of high-speed stranding machines, machines for CTC conductors, pay-offs/take-ups, taping heads, disc-and belt-type caterpillars/capstans
February 29, 206
QUEINS Machines GmbH together with STOLBERGER-KMB, both Germany based companies, are successful in business since many years as manufacturer of first-class machinery. Interested customers can see at stand 9B 06 a newly manufactured, heavy duty, chain-type caterpillar capstan for subsea cable as well as a belt-type capstan with extra-large pulling belts.
Furthermore QUEINS Machines GmbH/STOLBERGER-KMB will show at the WIRE 2016 a number of larged sized pictures and videos of delivered machines to the rope and cable industry.
The main products are all kind of high-speed stranding machines, machines for CTC conductors, pay-offs / take-ups, taping heads, disc- and belt-type caterpillars / capstans.
Further information to the range of different manufactured lines for special applications such as power transmission, steel rope applications, subsea cables and other fields can be given during the exhibition.
The second-hand department offers a full choice of machines and equipment for the wire and cable industry.
Introducing NEW Sealed Furnace, Copper Alloy Continuous Casting Technology
The new design of alloy rod caster enables the production of complex alloys which are not possible to cast using conventional continuous casting technology
February 29, 2016
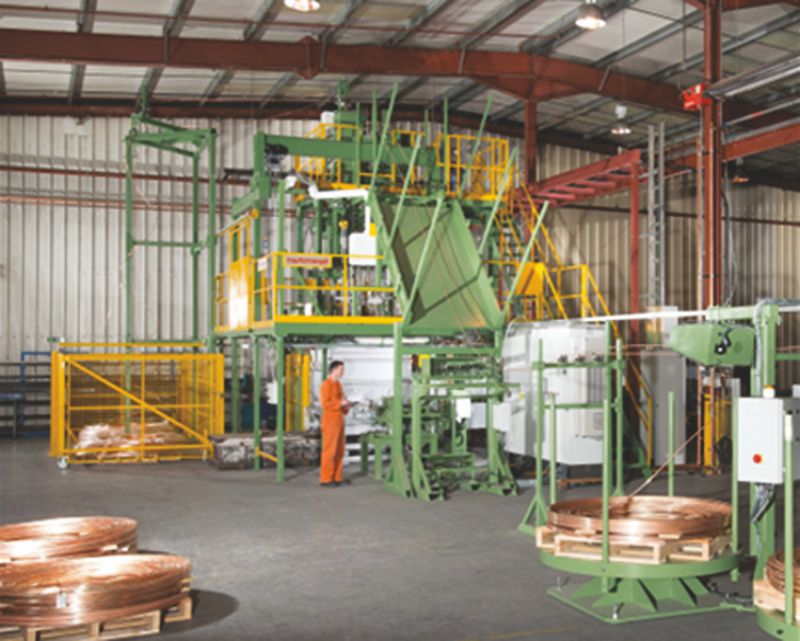
Rautomead Limited, specialist suppliers of Continuous Casting Systems, will be promoting its new copper alloy rod casting technology which has been developed at the Rautomead R&D Centre in Dundee.
The Patented Technology includes new designs of coolers, a sealed furnace lid with controlled delivery of alloying elements using an automated grain feeder and the Affival cored wire feed unit.
This new design of alloy rod caster enables the production of complex alloys which are not possible to cast using conventional continuous casting technology. The sealed lid with enclosed atmosphere allows accurate and consistent composition control of alloys containing reactive and volatile elements e.g. Cr, Zr, Ti, Mg and eliminates the requirement for graphite flake melt cover.
Rautomead also continue to offer continuous casting technology for oxygen-free copper wire rod, copper magnesium alloy rod, binary brasses and bronzes from 2,500 to 25,000 tonnes per year, rods from 8mm to 30mm diameter.
Richardapex to Present Its Unique Range of Wet Lubricants at the Fair
RichardsApex is a leading global manufacturer of wet lubricants for wiredrawing and hot-rolling applications
February 29, 2016
The company also provides semi-synthetic and synthetic compounds for wet drawing of nonferrous and ferrous wire as well as protective coatings, cleaners, corrosion inhibitors and oil-form lubricants for all nonferrous and ferrous alloys for both wire and tube applications.
Its core products can be made at all of the company’s manufacturing locations in the U.S., Europe, Australia and Mexico. With over 114 years of history, RichardsApex has an established global sales network to service customers throughout the world, including on-site support and technical sales assistance.
The company has subsidiaries located in both the U.K. (RichardsApex Europe) and in Australia (RichardsApex AustralAsia), and representatives in Canada, China, Greece, India, Italy, Japan, Korea, Malaysia, Mexico, Peru, Poland, Russia, Taiwan, Thailand, Turkey, Venezuela and Vietnam, with many other countries serviced by the subsidiaries and representatives.
Please stop by and see how partnering with RichardsApex can help your company achieve your goals for production and cost savings. www.richardsapex.com.
The Best Service and Support is of Utmost Importance
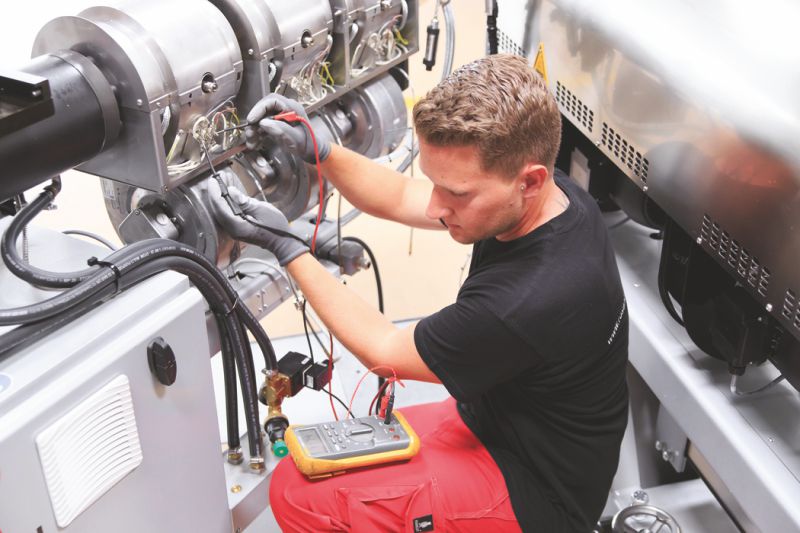
Imagine this… You are a cable manufacturer and your production line has been in continuous service for several years now. You are fully satisfied, since your line has always performed quite well. However, over the past few weeks something has being going on and its production speed has fallen. Just slightly and for no particular reason. Suddenly, a wire break necessitates taking the line out of operation. Your gut feeling had been telling you that it was about time to have it checked. It is Friday afternoon and the line cannot be restarted. An error has occurred and your staff are not able to get it remedied. What do you do?
You immediately call Rosendahl. They ask you a few pertinent questions and offer you the best service options available. If it is a minor issue, proper support can be provided over the phone. Whether by means of online service or remote support, they can assist you with any and all of Rosendahl’s lines. And if you have a service contract, someone is dispatched from one of the nearby service offices to quickly alleviate your problem.
Get service support on site
Technological solutions required to operate continuously and effectively are a basic need of cable manufacturers worldwide. The team at Rosendahl and Nextrom knows all too well why this requirement is on their list of priorities. They support their global partners with the best service possible. Therefore, being on site and providing local support is of utmost importance. Sales and service units are located globally, an added benefit that serves both customers and the company itself when it comes to on-site assistance – wherever it may be needed.
As a first-class solution provider, Rosendahl and Nextrom are able to cover your specific needs. Their vision, “Your success is our passion – here for you. “, means they never leave their customers alone – no matter what the problem may be. The service portfolio is comprised in such a way as to continuously improve and maintain the equipment delivered. Excellent support and rapid deliveries of premium spare parts allow a significant reduction of equipment downtime. Do you need a partner for your complete equipment lifecycle? Rosendahl and Nextrom will offer a tailor-made service package to help you achieve your targets. And the outlook for future developments reveals that Industry 4.0 will open new doors and opportunities to the best service possible.
Meet Rosendahl and Nextrom at the Service Lounge at Wire Düsseldorf at Booth 9A60, where you will discover what they have to offer and boost your own business thanks to the utmost in high-quality performance equipment.
Sampsistemi to Toast its 80th Anniversary at the Wire 2016 Show
A number of innovative solutions for the manufacturing of wire and cable will be on display to highlight the importance of this anniversary
February 29, 2016
The upcoming Wire show in Düsseldorf (April 4-8, 2016) will mark the 80th Anniversary of Sampsistemi. The Italian company looks forward to meeting customers, partners and friends at Hall 9, Booth 9C60 to celebrate together and share the latest news concerning new developments, investments and more!
Let’s have a look at some of the most interesting solutions on display:
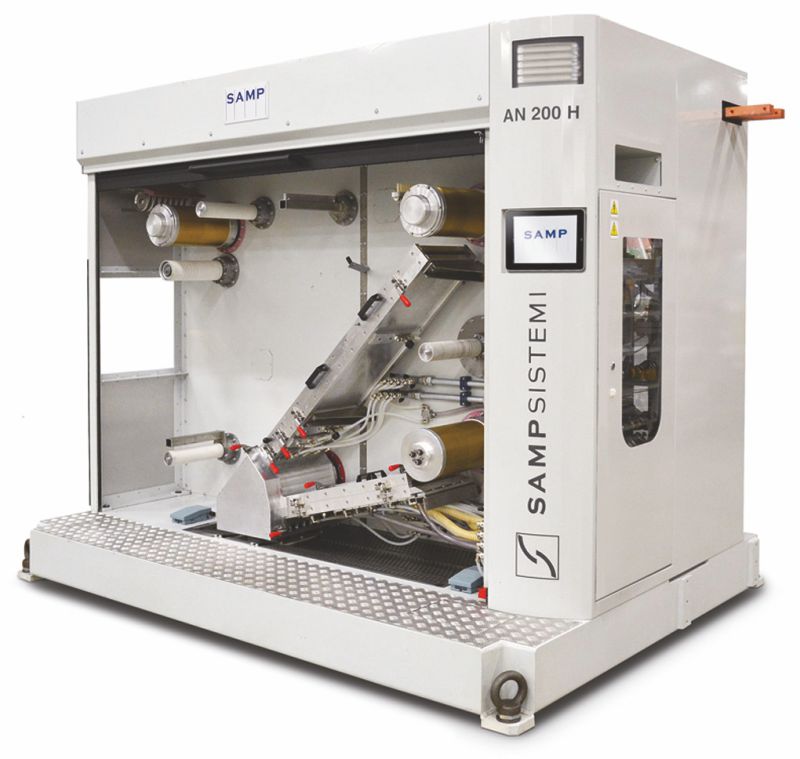
Aluminium and its alloys are playing an important role in the development of wire and cable solutions for automotive applications, as a consequence of new environmental regulations, price pressure and more on-board applications. For these reasons, Sampsistemi has developed a whole range of products specifically designed for the multi-wire drawing, in-line annealing, spooling and successive bunching of aluminium wire, which will be displayed at the upcoming Wire show.
The Sampsistemi Multiwire Drawing Platform (DM Platform) is based on the splitting of gear transmission into two or more independent sections, with separate AC servomotors. This allows slip recovery between each section and at the inlet side. All motors are synchronised by means of a control motion system. Slipping reduction and the improvement in the quality of gear transmission, bearings and seals result in a reduction of energy consumption by 10-15% and in a consequent improvement of production costs. Die holders have been specifically designed to improve wire lubrication within the die, to reduce friction and to facilitate the wire cleaning, thereby enhancing the product quality and prolonging the die life. Zirconium oxide pulling rings are used to reach the best possible quality surface of the wire.
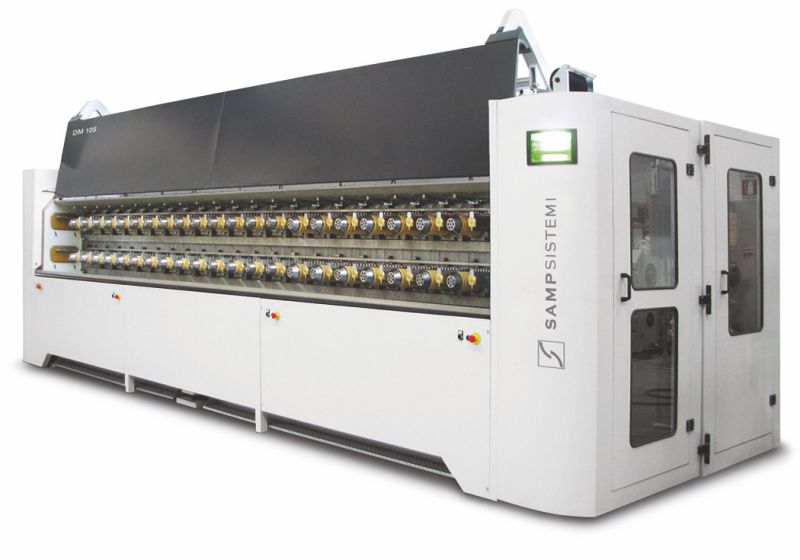
The Sampsistemi Annealing Platform includes a number of technical features, such as multimotor technology, adjustable pre-heating length and a wire-walker before contact rings. In addition, the cleaning device on contact rings ensures the integrity of the wire surface, the requested physical properties (mechanical strength, elongation, conductivity and resistance) and maintains the diameter and roundness of the wire. The control system is able to set up production parameters, in particular the kinematic ratio between each axis, in order to form a production recipe stored in the HMI panel. The Annealer Platform is completed with the latest development in annealing technology, in particular the development of the electronic equipment that reduces current distortion (THD-I) and energy waste (PF > 0.90).
Also on display, a Sampsistemi Extrusion Group for the Sheathing of HV Cables with a diameter of up to 180 mm, with both smooth and corrugated tape. Thanks to its highly innovative structure, this extrusion group allows an important reduction of production costs if compared to traditional methods. This new solution has been developed together with CJ TEK, our Swiss Technology Partner for Extrusion Crossheads, who will be a co-exhibitor at the Wire show together with Sampsistemi, displaying a number of high-technology, innovative crossheads for many different applications.
SIKORA at the Wire 2016
SIKORA continues its claim for Technology To Perfection: At the leading show for the wire and cable industry, ‘Wire’ 2016, the Bremen based company is presenting a full program of well proven and innovative non-contact measuring, control, inspection and sorting devices for quality assurance and cost reduction in the wire, cable, optical fiber and plastics industries.
Harry Prunk, Member of the Board at SIKORA:
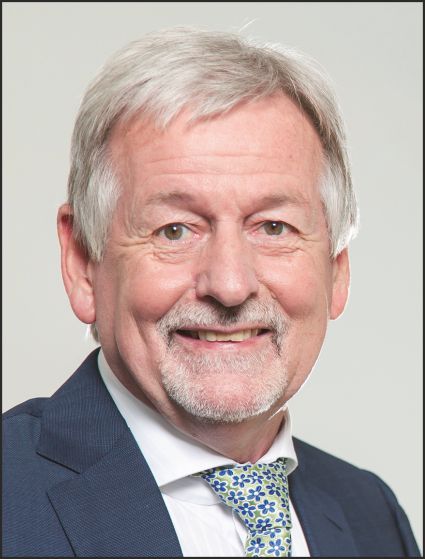
“I am looking forward to meeting and talking with customers, friends and interested show visitors while introducing our innovative technology. This is among others the PREHEATER 6000 TC, a temperature controlled conductor preheating device that assures an optimum adhesion of the PE or other plastics on the conductor. In this context we will also present the WIRE-TEMP 6000, a non-contact conductor temperature measurement system that is now also available for diameters up to 50mm and thus suitable for installation in CV-lines.
“Another highlight will be the PURITY SCANNER for online inspection and sorting of plastic material that is used, for example, for the insulation of power cables. The system assures that only pure material is entering the extrusion process and the final product. Furthermore, the PURITY CONCEPT Systems celebrate their premiere at the ‘Wire’. With this technological innovation there are modular designed devices available for on- or offline inspection and analysis of pellets, flakes and tapes/films. The systems are based on X-ray, infrared or optical technologies depending on application.
“In addition, visitors will get to know our sophisticated systems for quality assurance of optical fibers in the drawing tower. The product series is now complemented by a gauge head for measuring the fiber temperature as well as innovative equipment that gives information on the coating concentricity. Experience these and many other innovations from SIKORA. Come up to our booth for conversations, technical discussions and enjoy freshly prepared food and refreshments from our cocktail bar in the second floor.”
Selected technological highlights at the SIKORA booth:
PREHEATER 6000 TC
- Temperature controlled conductor preheater for optimal adhesion of the insulation
WIRE-TEMP 6000
- Non-contact temperature measurement of the conductor
- New device WIRE-TEMP 6050: for conductor diameters up to 50mm
PURITY SCANNER
- Inspection and sorting system for XLPE pellets
- Dual inspection: X-ray and optical technologies for detection of metallic and organic contamination from 50 µm on the pellet surface and inside the pellet for highest material quality
New: PURITY CONCEPT Systems
- Modular designed systems for on- or offline inspection and analysis of pellets, flakes and films/tapes
- Based on X-ray, infrared or optical technologies
- Detection of contamination from 50 µm
FIBER Series 6000
- Diameter measurement before and after coating
- Determination of the fiber position, vibration frequency, tension and spinning
- Airline detection
- 100% lump detection
- Highlight: Temperature measurement of the optical fiber and concentricity evaluation of the coating
TKT Group at “Wire 2016” in Düsseldorf
The company will be showcasing, for the first time, its recent innovation TECNOLUBRE FM/241, a special calcium lubricant
February 29, 2016
TECNOVO and KONER, leading companies of TKT Group, are going to meet their customers at TKT’s booth (HALL 11, BOOTH: A56) for the “Wire 2016” trade show, that is going to take place in Germany, Düsseldorf, from April 4th to April 8th 2016.
On the occasion of this event, very important newness will be showcased, as result of TKT Group will to provide customers with more and more innovative solutions, reaping the profits of the recent big efforts in terms of investments, products research and development, technological innovation and continuous improvement.
One of the main innovations of recent development is TECNOLUBRE FM/241, a special calcium lubricant, specific for high carbon galvanized wire added with special tackifier additives, to be used in the first steps. The main characteristics of this innovative calcium soap:
- Universal soap used for HC, LC and alloy steel
- Medium content of fatty acids
- Very low content of TiO2
- 100% boron and sulfurized additives free
- Sticky additives improving the lubricant adhesion to the wire
- Better lubrication in the redrawing process, especially in wet operations
Furthermore, a very new product is going to be launched: TECNOLUBRE FM/413, the first calcium/sodium beaded lubricant in the worldwide market. Below the main features:
- Beaded product
- 100% dust and borax free
- Perfect sliding of the soap on the wire, minimizing the friction
- Very low final residual
- Partially soluble in water
- Excellent results for high carbon Zn/Al coated wire
Both the innovative products will be presented at “Wire Show 2016” for the very first time.
The TROESTER Group at WIRE 2016
TROESTER will present its state-of-the-art extrusion equipment for the production of LV, MV, HV and EHV cables
February 29, 2016
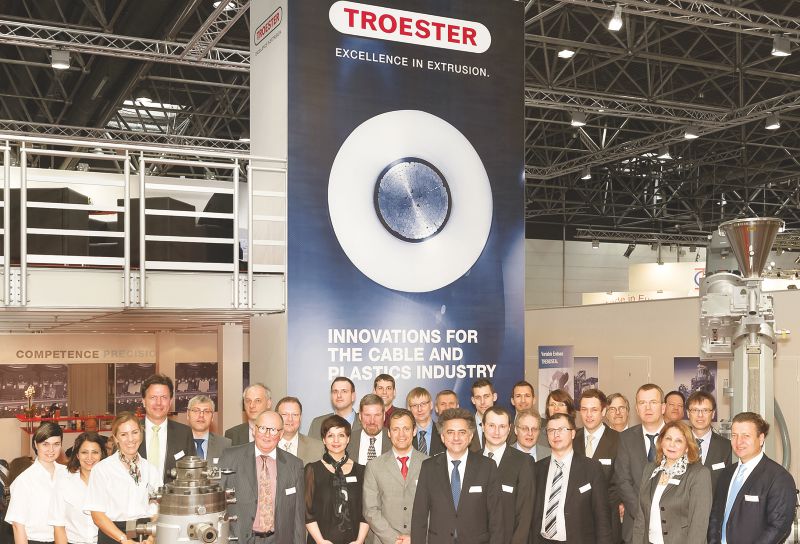
The TROESTER Group is a worldwide leading manufacturer of complete extrusion systems for the cable industry. The excellent results produced by its extrusion technology makes TROESTER a competent and reliable partner in the cable industry.
TROESTER will present its state-of-the-art extrusion equipment for the production of LV, MV, HV and EHV cables; this comprises CCV and VCV Lines, Insulation and Sheathing Lines as well as single machines and components for efficient cable production. TROESTER will introduce the latest generation of extruders type PXS, a high performance extruder to be used in Insulation and Sheathing Lines. In addition TROESTER will present solutions for upgrading existing CV-lines, like TRENDSEAL, a flexible end seal able to increase the efficiency of every kind of CV-Line, a new edition of the sag measuring unit TRISAG 3.0 and also heating tubes with improved energy efficiency, splice boxes and other CV-tube components.
X-Compound, member of the TROESTER Group will join the booth and present their kneader technology for the continuous compounding of HFFR (LSOH), PVC, XLPE, Semiconductive Materials and EPR/EPDM. X-Compound is specialized in the planning and construction of complete systems for the compounding of plastics with the process steps conveying, melting, dispersing, mixing and degassing.
The team of specialists from TROESTER and X-Compound looks forward to meeting you at booth 10/F60 and will be happy to discuss your specific requirements with you.
Venus Celebrates 25 Years of Excellence!
The manufacturer of stainless steel wires and bars is participating in Wire 2016 at Dusseldorf with its wide array of products and would be renewing its relationship with many of its clients who trusted the company in its 25 years journey.
February 29, 2016
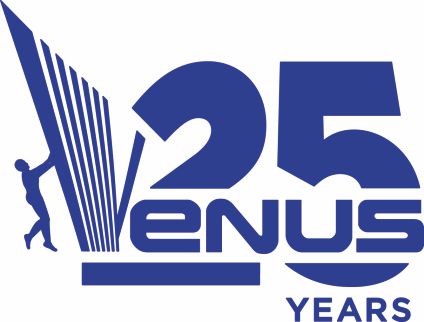
Venus, a leading manufacturer of stainless steel wires & bars, has established a wide market presence with its superior quality and impeccable service levels. It has manufacturing facility in Khopoli, Maharashtra, India and the company has been exporting its products for 25 years.
Venus provides a fully integrated service for stainless steel wires and bars with all the production activities, right from Melting, casting, Hot Rolling and cold processing carried out under its direct supervision.
Venus Product Range Includes:
Stainless Steel Fine Wire in size range 0.10mm to 0.80mm and having applications such as Braiding, Knitting, Weaving;
Stainless Steel Thick Wire in size 0.90mm to 22mm and application such as Wine yards, Wool for automatic exhauster, Shot wire, Rope wire, Roofing hook, Balls, Nails, Brush Wire, Conveyor Belts, Pot Handles, Wire for profiles, Filter bag cages, Wall ties, Roofing Hooks, Fasteners etc;
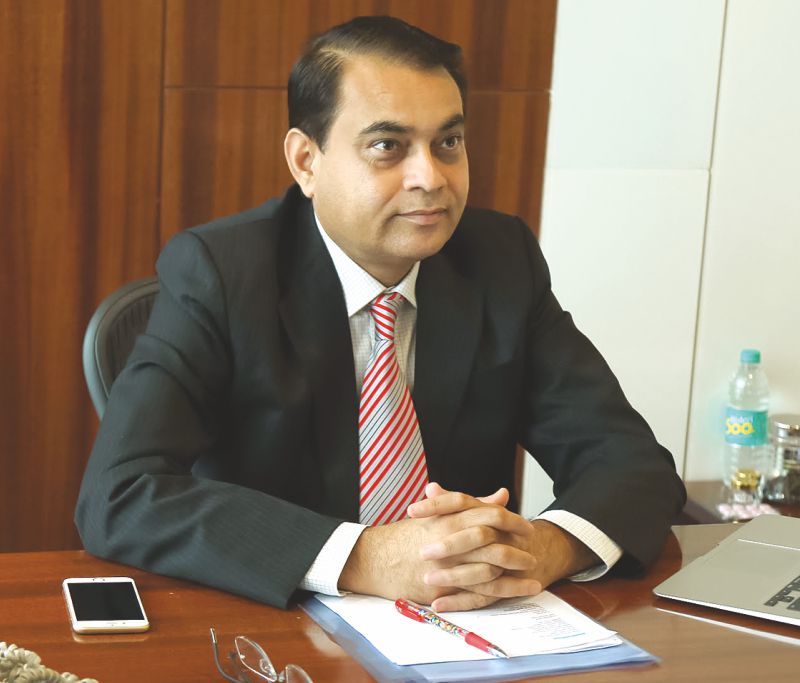
Stainless Welding Wires which includes MIG Wire, TIG Wire, Sub Arc Wire & Core Wire for electrodes having applications in Welding for Automotive, Railways, Nuclear power plants, Boilers etc.;
Stainless Steel Bars in size range of 3mm to 155mm (Brands – Tru-Tuf, Vsq Bars, FitMach, Solenoid quality bars); Applications – Propeller Shaft, Centrifugal pumps, Pneumatic and Hyradulics, Valve stem, Fuel injectors, and various other components for Automotive, Oil and gas, Nuclear, Food industries.
Venus also offers almost all stainless steel grades possible in Austenitic, Martensitic, Ferritic, Also Duplex & Super Duplex & Nickel Alloy.
The company has got all the necessary approvals such as ISO 9001:B5:B9 2008, PED AD 2000 Merkblatt W0,PED AD 2000-Merkblatt WO VdTUV Merkblatt 1153, ISO 14001:2004 +Cor.1:2009, BS OHSAS 18001:2007, ISO/TS 16949: 2009, ISO/IEC 17025 : 2005, AS 9100C: 2009, DB, CWB, CE MARKING(CPD), ASME Section III, NCA 3800, IBR, NPC, RDSO, NABL.
It has good presence in India. Since the economic slowdown of 2008, Venus has focused more on the Indian market as the Indian economy stayed strong. Also demand for quality products has been increasing drastically in India lately. The company has increased its market share from 5 percent to 20 percent in the Indian market.
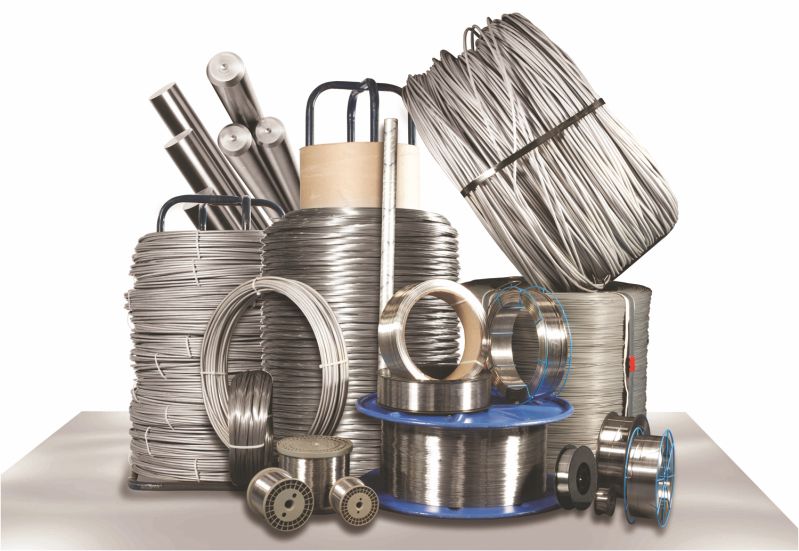
A Seamless Operation: Getting Micro Printing Right First Time
Videojet is a world-leader in the product identification market, providing in-lineprinting, coding, and marking products, application specific fluids and product life cycle services. With its customer application experts and technology leadership in continuous inkjet (CIJ), thermal inkjet (TIJ), laser marking, thermal transferover printing (TTO), case coding and labeling, and wide array printing, Videojet has more than325,000 printers installed worldwide.
Wire and cable is vital to global industry, as without it very little could function effectively. Manufacturers of wire and cable are under pressure to produce vast quantities of product, often to rigorous standards and specifications.
Given that wire and cable often has limited or no packaging, in-line printed codes are essential to the finished product, and the applications are many and varied. Regulatory compliance may dictate the need for certain information to be printed, such as the composition of the material or its electrical insulation rating, whilst others may relate to a specific part number, manufacturer or even a brand name.
Printing is often required to be placed on extremely limited surface areas to a standard that allows it to be highly legible, visible and able to withstand the rigorous process of winding, storage and installation, without becoming smudged or blurred.
Operating challenges
Operating conditions in wire and cable manufacturing can be harsh and often fluctuate due to exposure to heating elements or external weather conditions.. In addition, high production speeds can increase printing difficulty, with some line speeds exceeding one thousand feet per minute. At these speeds, electrical static can be a concern, in addition to operating in close proximity to very hot extruder output.
Another consideration is that the wire and cable industry often print on dark substrates, which requires the coding solution to carry opaque (or pigmented) inks. These inks require constant agitation to maintain consistent performance, which cannot be achieved by older printers. Technology is now available that incorporates a specially designed core with this challenge in mind that is capable of applying up to five lines of high-resolution print at speeds up to 888 feet per minute (271m/min).
Maximizing uptime on the line
While all production environments value uptime, it is paramount with extruded products given the continuous production process. Extrusion lines operate at high speeds and, as the outer casing must be heated to a high temperature to facilitate the wire or cable placement within, are difficult or impossible to stop once a run has commenced. Therefore, if the coder fails, it will invariably lead to rework or waste costs to the manufacturer.
Advanced solutions available on the market have largely been developed through listening to the challenges manufacturers are facing every day and addressing the problems that have historically led to unscheduled downtime. Outmoded methods, such as hot stamping or contact rolling, can damage the product and require more frequent user intervention.
In addition to being a non-contact printing method, the newest CIJ printers can provide substantial productivity benefits to the wire and cable industry. Solutions like CleanFlowTM and Dynamic CalibrationTM are useful examples of how production uptime can be increased. CleanFlow employs a positive flow of filtered air to the printhead, which reduces ink build up that can cause ordinary inkjet printers to shut down. Dynamic Calibration automatically adjusts printer settings according to the ambient temperature in order to help ensure consistent print quality. In addition, new generation printer cores have a life span of up to 14,000 hours, helping to minimize necessary maintenance intervals.
Protecting your brand
Wire and cable products are typically distributed with limited or no secondary packaging or other identification, often making codes the only opportunity a manufacturer has of conveying its brand and product information to the customer.
Historically, codes produced by outdated printing methods have been difficult to read which, if allowed to reach a customer, could potentially lead to an unfairly negative perception in relation to a product’s quality. Ensuring codes are clear and highly legible is therefore of paramount importance, as a high quality code drives perception of a high quality product.
Micro printing via a CIJ printer is the perfect solution for the wire and cable industry, due to its ability to print highly legible codes onto substrates with very limited space. Importantly, by utilizing specialist inks in conjunction with this printing technology, this method ensures codes remain clear if the product is rubbed, or as it is spooled as it exits the line, safeguarding brand integrity.
Built in productivity
The latest Continuous Inkjet (CIJ) micro printing technology has been designed with productivity in mind.
Advanced CIJ printers maximize productivity through smart solutions embedded within the printer itself. As an example, CIJ printers from Videojet are able to monitor Overall Equipment Effectiveness (OEE), providing accurate data pertaining to the availability of the printer, any issues that may have occurred, either through operator or rare technical errors, and importantly, actionable information that can be used to identify causes and fix them quickly. This is a valuable tool to help minimize unscheduled linestoppages.
This technology can be used in conjunction withadvanced software solutions, designed to help ensure the right codes are printed on the corresponding products consistently. A simple wizard tool enables rapid set-up speeds via bright colored touchscreens, whilst on-board diagnostics assist in monitoring and achieving OEE targets.
Benefits of the latest CIJ technology
The benefits of the latest CIJ printers are many and varied when compared to older, outdated units.
Historically, ink was stored in bottles, which were prone to spills and made it possible to place the wrong ink or makeup in the printer. Current CIJ technology avoids this through the use of smart cartridges, which feature a needle and septum design that makes it virtually impossible to leak when refilled. The latest cartridges also feature smart-chip technology, which prevents incorrect fluids from being inserted, at the same time as monitoring fluid levels.
Smaller nozzle sizes and higher nozzle frequencies on CIJ printers also enable micro text to be printed to the highest quality without compromising on line speeds – allowing operators to maximize productivity.
Conclusion
Whilst it can be tempting to adopt a ‘stick with what you know’ outlook when it comes to micro printing there are bottom line benefits to a modern CIJ solution. New technology can be integrated quickly and efficiently into your existing manufacturing operation, driving productivity increases to offset the capital investment.
Videx’s Fully Automatic Bent Bolt Machine & Planetary Thread Roller at Wire 2016
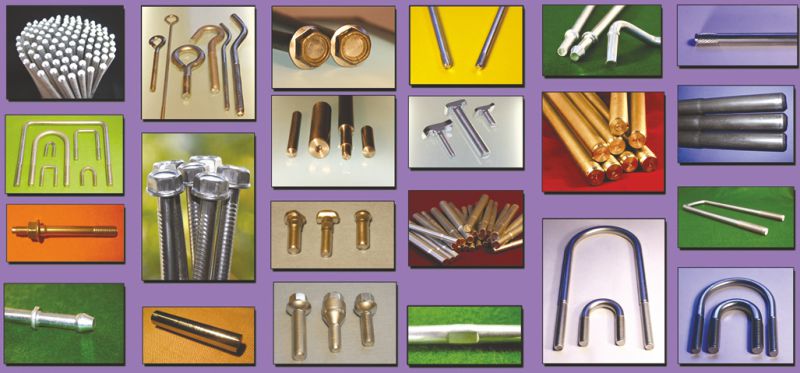
Videx is manufacturing the following lines of equipment:
- Planetary Thread Rollers for Headed Fasteners.
- Dual-Spindle Thread Rollers for Straightening and Thread Rolling long hardened fasteners, thread and knurl Wheel Bolts and thread roll dual side fasteners.
- Straighten & Cut machines from coil with optional Chamfering up to Ø45mm.
- U-bolts, Straight-Studs & Eye-Bolt machines from coil.
- Extrusion machines for bars up to Ø100mm
- Rod Headers from coil or bars; Open/Closed die.
- Forging lines for Hex Bolts up to M-76.
- Threaded Rods lines and Bundling machines.
- Planetary/Rotary Thread Rolling dies.
In WIRE 2016, the company will be exhibiting the following machines:
- Fully Automatic Bent Bolt machine from coil, model VAS-20-DBH, for production of U-Bolts and Eye-Bolts. The machine pulls the wire from coil, straightens it, cuts to length, thread rolls on both sides and bends to shape. Thread range: M-6 to M-12.
- Planetary Thread Roller with Closed Structure, model VA 20-ES for thread rolling of pre-hardened fasteners.
The machine controls the feed position and indexes the feed cam to a fresh start point thus considerably increasing die life. It is also equipped with Videx’s “Controlled Feed” system, for threading Lap-Free threads on any material.
Other features include Hydraulic Clamp of the thread rolling dies & Quick Set-Up features. Thread range M-6 to M-16. Production speed up to 640 PPM.
Under Stress, in Rotation, at High Speed – Blast Technology for Wire, Rod and Springs at WIRE 2016
Blast technology expert Wheelabrator will present latest machine concepts and developments for the wheelblasting of wire, rod and springs at WIRE 2016 in Düsseldorf, Germany.
The line-up includes the tried and tested FL machine series for the mechanical descaling of wire and rod, ranging from stand-alone machines to fully integrated high-performance equipment for high-speed drawing lines.
At WIRE, the Wheelabrator team will also be at hand to discuss specialist shot peening equipment for leaf and coil springs, particularly for automotive applications.
Blast machines from Wheelabrator can be automated variably, have a flexible design and integrate seamlessly into sophisticated production processes – be it as a self-contained, autonomous solution or as a fully integrated through-feed machine.
FL: Efficient Descaling of Wire and Rod
Wheelabrator’s FL range is very popular, with over 200 FL machines in operation across wire and rod production worldwide. Over the last decades, FL machines have almost completely replaced chemical descaling methods in wire and rod production.
Common feature of all FL machines is the focussing of the abrasive via guide plates, which can be adapted to suit different workpiece diameters. With Wheelabrator’s latest model, FL-4-37/55, the guide plates are adjusted automatically, resulting in a more efficient operation of the drawing line.
New Concepts for Demanding Applications
Special machines for shot peening of springs play a key role in the manufacturing process of, for example, coil springs in automotive, where shot peening allows the reduction of weight while improving the fatigue strength of a part.
Peripheral equipment around these special machines can be adapted to suit individual production requirements, including various methods for loading and unloading (via robot, manipulator or other handling equipment). This ensures process security, reliability and efficiency of production.
Another new machine concept is the rotary through-feed shot peening machine (RDS), in which coil springs are peened from all sides, under constant rotation, while swiftly and steadily passing through the machine.
Stress peening (SRS) machines shot-peen chassis springs while a load is applied. The spring preload follows the direction of load of the part when in operation, replicating tensile stresses occurring in the part under operating conditions.
Dosing for the Extrusion of Cross-linked and Foamed Insulations
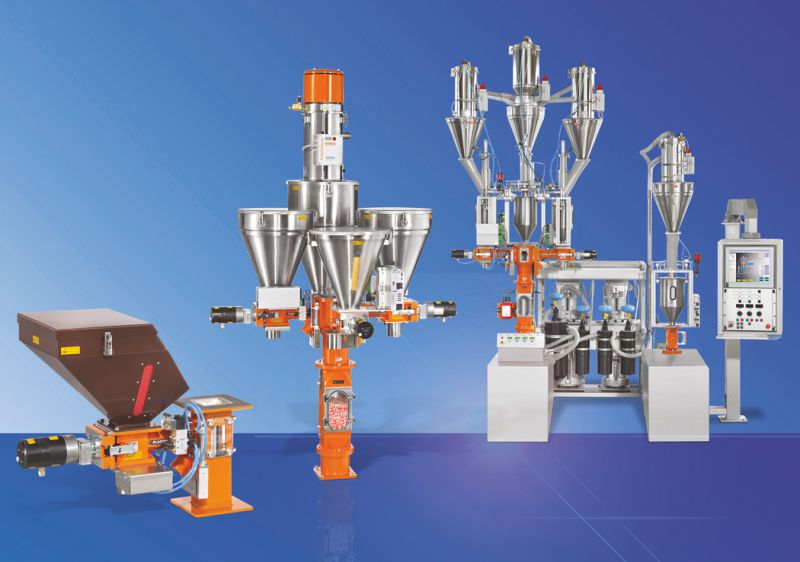
Until today that are still cable manufacturers preparing material mixtures by hand. Here the risk of wrong mixtures or separation of material is very high. Reproducibility cannot be guaranteed.
The first real automatisation for the dosing of materials in the cable manufacturing industry was the implementation of the “Wilson Color-O-Meters” (disc dosing units), which we mounted on the main material hoppers. Thus the human factor was minimized. The disadvantages of such systems were the high maintenance, the comparatively difficult handling, the risk of material separation when having different material densities (stirring devices had to be used) and the associated must of overdosing, as well as material spreading around the equipment.
With the introduction of the screw feeding dosing units, the above systems were replaced step by step. Screw feeding dosing equipment was being installed between the main material hopper and the material inlet of the extruder. The separation of material was eliminated. Changeover period have been reduced drastically. Handling was improved and the spreading of material around the equipment was stopped.
Up till today these systems are being used. In comparatively basic productions methods when the speed of the extruder is not or very rarely changed (ramping) and when the requirements to the quality of the mixture are minimal, this way of having a dosing unit synchronized to the speed of the extruder is still common. The speed (RPM) of the dosing unit is synchronized with the speed of the extruder (capacities are not synchronized).
But the requirements to the product properties have increased over the passed 30 years and new products need highly precise dosing solutions.
As an example cross-linked and foamed (chemical foaming) products are to be mentioned. Here it is extremely important that a uniform cross-linking over the entire production run is being achieved or respectively that the product is having a uniform cell structure and a regular result of foaming.
Mixing Station Systems are required when precise dosing is necessary over the complete speed range of the extruder, if very small amounts/percentages of additives are to be dosed or if non-visible additives are to be handled.
Depending on the requirements there are various systems/solutions available. As each manufacturing requires individual solutions, it is recommended that specific solutions are being worked out, in order to get the best results.
In the cable manufacturing nowadays it is common to make use of Mixing Station Systems.
In this type of systems all materials are being dosed and thus also controlled. Mixing Stations are working fully independent of the extruder speed and material consumption.
Since the end of 1970 the company of Woywod Kunststoffmaschinen has continously developed this technology and thus having supplied reliable and high quality PLASTICOLOR equipment to the market, which meets the requirements of the various customers.
Woywod Kunststoffmaschinen GmbH & Co. Vertriebs-KG are offering two main versions of the mixing stations:
- PLASTICOLOR volumetric mixing stations and
- PLASTICOLOR gravimetric mixing stations (loss-in-weight principle).
PLASTICOLOR Volumetric and gravimetric mixing stations are having the following advantages:
- Very good handling of all plastic materials, ranging from free-flowing powder, to micro-granules
- and going to coarse regrind.
- Extreme precise dosing of each individual component at any time of the production.
- Experience has shown that this precision is at +/- 0,5% or better. Here it is to be noted that this precision is not taken from the average of many batches.
- Very good handling, quick cleaning and short changeover times.
- Sticking to the preset recipe over the full RPM range of the extrusion line.
- Very homogenous and good quality of the mixture, also when having different material densities and varying material properties.
- Low volume of pre-mixed material.
Specific Advantages/Disadvantages of PLASTICOLOR volumetric mixing stations:
- Material calibration tests are necessary
- Comparatively low investment
Specific Advantages/Disadvantages of PLASTICOLOR Gravimetric “Loss-in-Weight” Mixing Stations
- No material calibration tests are necessary
- Slightly higher cost of Investment
For special applications and for the extrusion of special materials also synchronized PLASTICOLOR Mixing Stations can be offered. These systems are providing a constant material level in the neckpiece and thus make sure that the amount of material is not varying.
For detailed information please visit Woywod Kunststoffmaschinen GmbH & Co. KG in Hall 9 on Booth A 42
WTM Will Display a New Horizontal Line Suitable for Coaxial Cables Wrapping with COPPER SILVER-PLATED TAPES/WIRE
The company is a leading manufacturer of high performance machines such as concentric taping lines, spinning machines, single twisting equipment, and rewinding lines
February 29, 2016
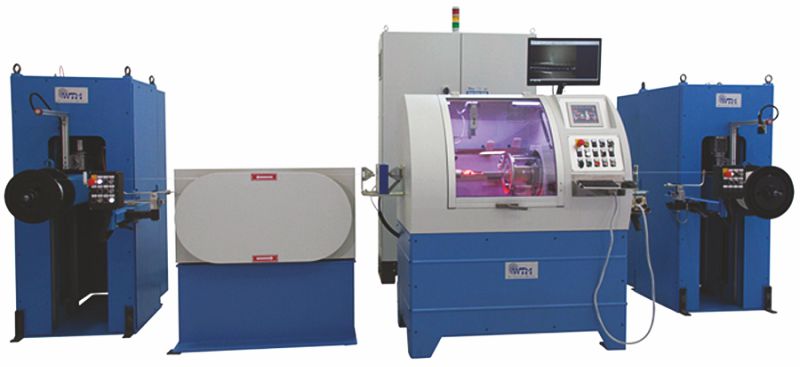
WTM S.r.l. is on the wire and cable market since the end of the 80’s, and it has gained a reputation as specialist in designing, developing and manufacturing high performance machines such as: concentric taping lines, spinning machines, single twisting equipment, rewinding lines and any special equipment for specific applications.
Its devotion to research and design, material selection, accurate manufacturing, assembly and testing, allows WTM machines to meet fully the requirements of the most demanding cable producers all over the world.
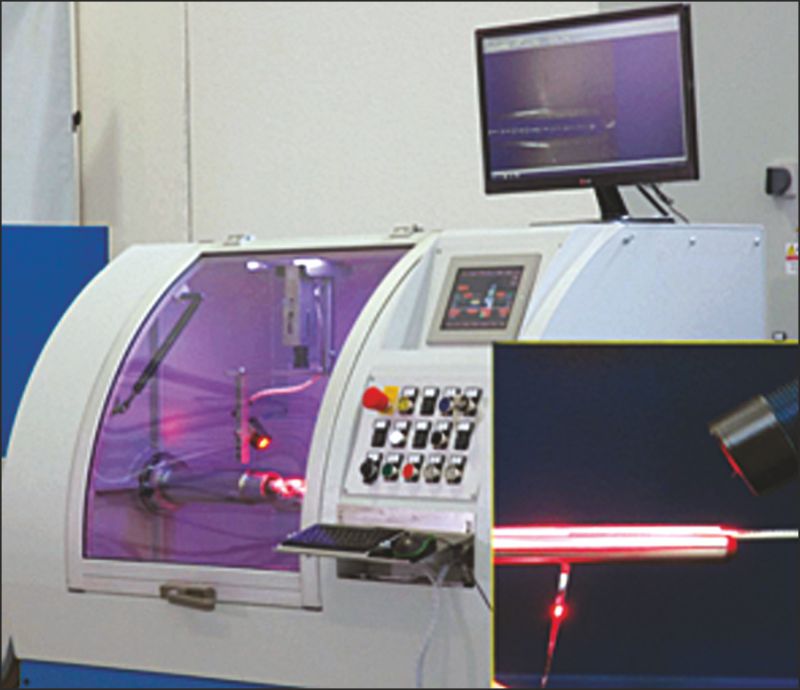
The cables produced with WTM’s equipment comply with the strictest rules thanks to the high precision and flexibility of his machines achieved with the big experience gained through the development of hundreds of different applications.
WTM S.r.l., at the stand no.11D78, will display a new horizontal line suitable for coaxial cables wrapping with COPPER SILVER-PLATED TAPES/WIRE. It will be a complete line, working all day long, equipped with the latest generation taping head for CuAg-coated tape/wire. This triple motorized head is particularly suitable for such cables, thanks to its high sensitivity DYNAMIC DANCER that grants a wrapping of the highest precision available.
This active control system, DYNAMIC DANCER, adjusts the tension in real time, directly on the materials being wrapped, applying the pre-set pulling tension on the tape/wireand keeping it constant in any situation, including when the tape is traversing from edge to edge on the spool.
A further advantage of this line is to be equipped with new designed single-shaft pay-off and take-up units: they are traversing, self-aligning and self-levelling in two axis. The technologically advanced torque control, in combination with diameter laser control and torque sensors, allows obtaining a cable tension directly monitored and adjusted in real time. With this advanced adjustment system, also for very low cable tensions, no dancers are used avoiding extra detrimental bending on the cable.
WTM’s VISIO System will be installed in the line. The well-known WTM’s electro-optical control system, available in several configurations and with a variety of options, magnifies the cable surface image during the production process.
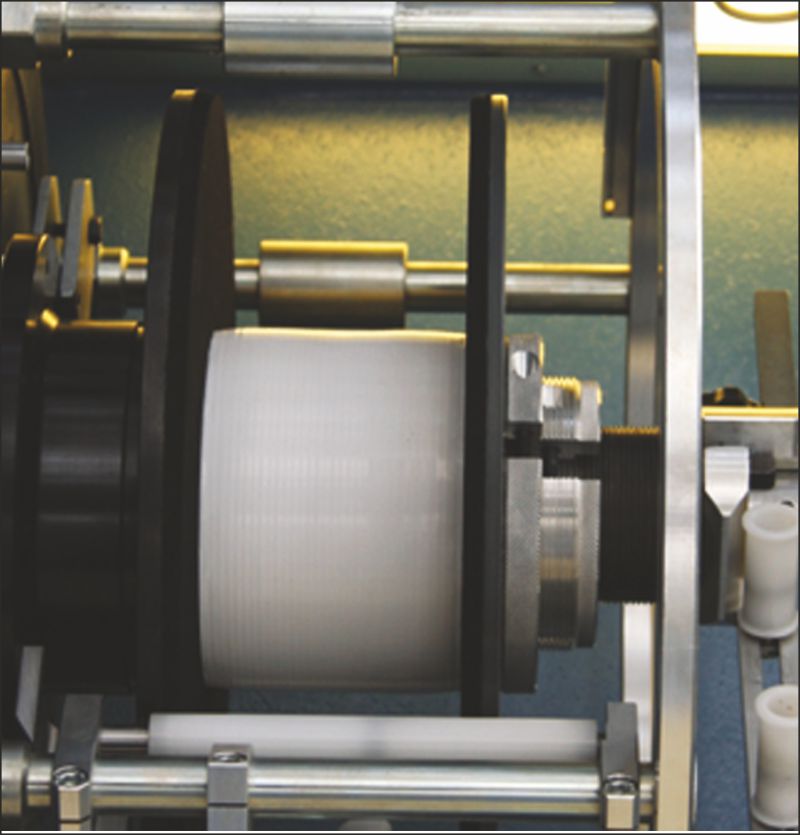
Measurements, direct feedback and real time checking on the cable surface are now possible. Data obtained can be stored or sent by LAN connection to any department for being analyzed, for generating statistics, trends and production diagrams and any other application requested.
A second module will be displayed, equipped also with the triple motorized taping head, in this case, suitable for PTFE. This taping head is a variant of the previous one and it is suitable to control directly and immediately before wrapping point, the tape tension with the tight deviation of ± 50 grams.
In this case, the high sensitivity of our DYNAMIC DANCER gives the possibility to process the softest and most critical materials.
Any part of our lines is designed for processing every kind of cables at the best, including those used for the most sophisticated applications: aeronautical, aerospace, IT communication and military uses.
A third machine will be presented at out stand. It is a new single twisting unit designed for very sophisticated LAN cables Cat. 5/6/7/7a/8. Thanks to the new developed technical solutions, this highly efficient unit, can produce also other kinds of precise cables such as: high flexibility cables, signal cables (encoder), cables for robotic and suitable for overhead laying ones.
The impressive quality of the cables produced is granted also from an accurate control of the tension on the cable itself, in fact the machine can work both with dancer or torque control thus enabling the best tension regulator according the cables’ specific characteristics, assuring the widest range of product processing capability. In addition the pulling capstan, that is rotating to grant a constant lay length, can be excluded widening again the flexibility of the machine.
This machine is suitable be coupled with WTM’s concentric back twist feeders that we first have produced and introduced on the market or to be placed in line with existing payoffs. The line can be completed with several other equipment and accessories including various type of tape wrapping machines for different tapes.
WTM realizes completely its machines: the design, the construction, the assembly and even the software. In this way, every WTM machine can be integrated or completed with any other existing machine or equipment without problems, even from other suppliers. These include also laser gauges, spark testers and any other instrument useful for the production process, which can be connected and set directly from the machine operator panel.
WTM is continuously expanding his presence all over the world and it is starting to promote its products in India too, where the demand of high technology is growing day by day.
Zumbach to Exhibit its of Dimensional Measure-ment and Inspection Systems at Wire 2016
All Components in View -Measure Any Offshore Flexible with Instruments from Zumbach
February 29, 2016
Zumbach will showcase its extensive portfolio of Dimensional Measurement and Inspection Systems for Wire Drawing, Wire Insulating and Cable Jacketing processes as well as for Rod and Bar Mills. In order to achieve the highest precision and best price-performance ratio, different technologies such as laser scanning, X-ray, ultrasound, light-section technique and linear sensor technology are used.
The production of off shore Flexibles involves complex process’s requiring varying individual performances for quality control. Any deviations from the required standardscan risk horrific consequences if failure occurs depending the applications scenarios. In order that the risks for future product failure are eliminated during the manufacturing processes, such as wire drawing, profile rolling / extruding, stranding and sheathing, ZUMBACH provides reliable solutions for the measurement of all critical parameters.
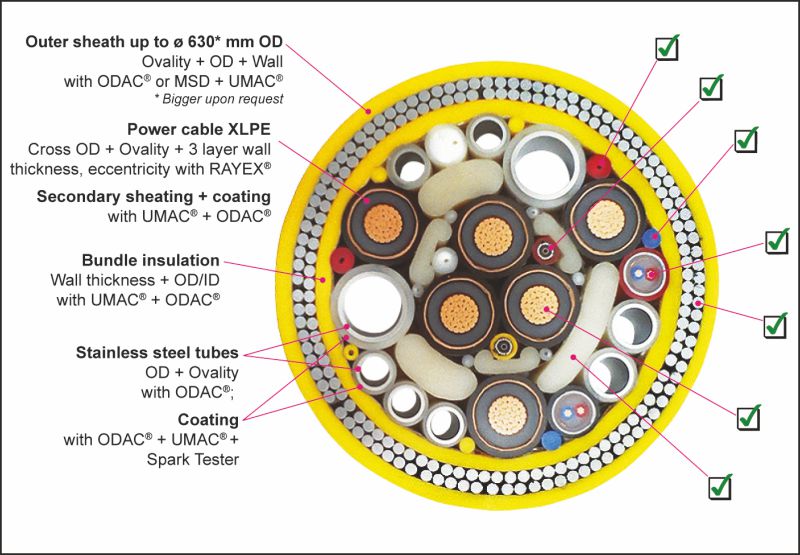
gauges from ZUMBACH
Zumbach has measurement solutions for nearly all wires, cables, tubes and profiles:
Extruded Cables, Tube and Hoses under Tight Control with Precise In-Line Measurement and Control of Eccentricity and Wall Thickness
Material savings thanks to measurement and control of eccentricity and wall thickness. The versatile high-tech ultrasonic system WALLMASTER offers application-specific solutions for measuring and monitoring wall thickness. The measuring data processor with touch-screen display gathers data and QC fully automatically.
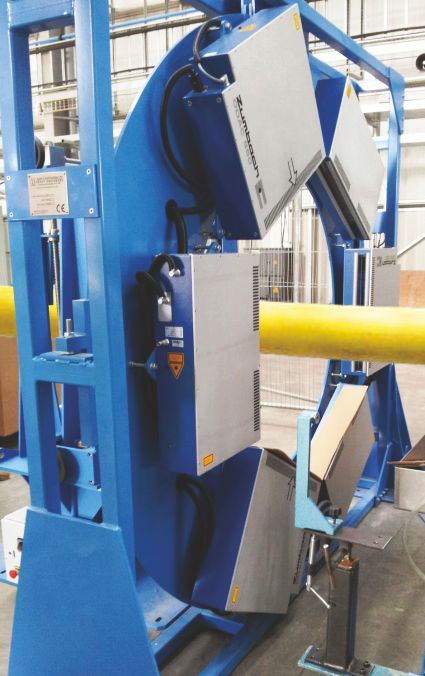
measuring an Offshore cable
of 500 mm OD
In combination with ultrasonic UMAC® scanners and various ODAC® diameter measuring gauges as well as with error detectors, the measuring and monitoring scale can be expanded to outside and inside diameter, statistics, SPC and processor communication.
Using Zumbach’s WALLMASTER measurement and control systems, manufacturers can economise their expenditure of raw materials. The ROI is achieved within a few months. The use of these systems also allows reducing considerably the start-up time.
New ultrasonic scanners for flexible diameter adjustment. This novel construction (pat. pend.) is going to be one of the exhibition’s highlights: the traducers can be either individually or simultaneously adjusted to the best possible measuring position within seconds. The scanners represent a smart and simple solution for full non-contact, in-line eccentricity and wall thickness measurement of cable jackets, tubes and hoses.
Complete line of Measurement and Control Equipment for Any On-line and Manufacturing Process
- New 1, 2 and 3 axis diameter gauges of the high precision, well known ODAC® series for any wire and cable. New models with special beam geometry, fault detection function and high scan rate.
- The advanced ODEX® concentricity and diameter gauge for wire extrusion. Fully non-contact, based on magnetic and laser technology.
- New LSV length & speed gauges for down to zero speed measurement
- New and state-of-the-Art Spark Tester AC and DST systems
- Advanced KW fault detectors with new local BAE control and display unit
- New economic, modular high performance USYS IPC data acquisition, processing and display units.
- RAYEX® D series: ZUMBACH’s X-Ray measuring & control system for CV lines, for wall thickness (3 layers), eccentricity and diameter/ovality for CV lines.
- PROFILEMASTER® series: High-end Non-contact Profile and Shape Measurement, Combining Laser and CCD Technology for shaped wire and any other profile.