Improvement of the product quality through less material faults as well as a homogeneous structure, increasing the resilience while reducing the weight without any constraint as regards the resistivity – all these requirements to components are mainly achieved by a high quality wire. The meaning of wire for the automotive industry, the medical technology, the cable and electro technology as well as many other applications in our everyday life can never be appraised highly enough.
Introduction
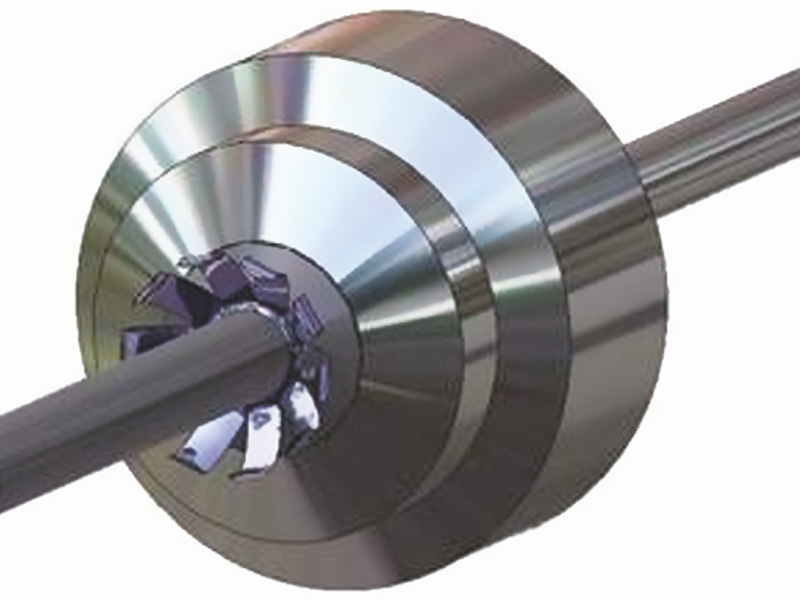
Draw-peeling – also known as shaving – has been known in the wire industry for many years. Terms like shaving or scalping or also back-die shaving have been created. Developments, especially in the field of combustion engines led to the fact that this operation is now an essential step in the manufacturing of valve spring wire. The company KIESELSTEIN International GmbH/Germany has, in extensive tests in its technology centre which was created especially for this purpose, enhanced the operation, classified it, solved open questions and built the technological platform.
Basics of draw-peeling
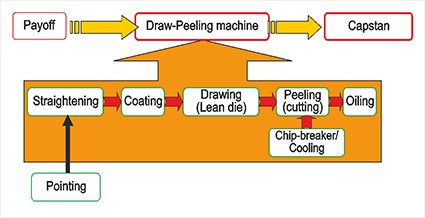
[source KIESELSTEIN]
Draw-peeling is a cutting procedure. The cutting tool in this case is a draw-peeling die / shaving die. This is a static tool with a circular blade. The geometry is similar to a regular drawing die. The main difference is that in contrary to the transformative geometry of the drawing die, there is a cutting edge. Picture 2 shows the technological composition of a draw-peeling plant.
A descaling (i.e. pickling) and a coating which is usually required for steel wire is not necessary in front of this cutting operation. The occurring chips are broken by a rotating chip breaker so they can be disposed of more easily. The necessary feeding force to pull the material through the straightener, the lean die and the draw-peeling die – altogether in the draw-peeling unit (shaving head) – comes from the drawing capstan. The chip cutting during the draw-peeling operation is cooled by means of a coolant to ensure higher tool life.
Initial state
As mentioned above, draw-peeling is used to improve the surface quality of wire. It is used when there is a special need for an immaculate surface quality, a homogeneous material structure and material purity. Different kinds of defects can be removed by draw-peeling. In the field of iron and steel materials there are surface cracks, rolling scores, scale scars, double skins, overlaps, light blowholes and decarburized margin layers (picture 3). In the area of non-ferrous metals the defects can occur as a consequence of the rolling process or the production of the raw material which have negative influence on the smoothness of the material to be processed. To remove these defects verifiably a material exposure is inevitable.
Comparison to other cutting operations in the wire industry
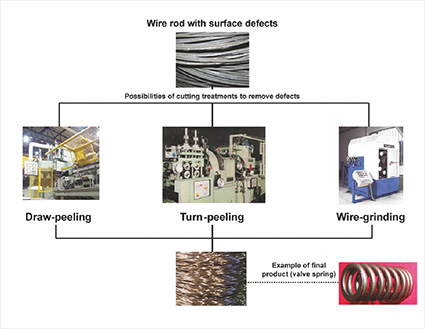
wire [source KIESELSTEIN]
Besides the draw-peeling of wire there are different procedures for the improvement of the surface quality. At this point we would like to highlight that it is not primarily an operation for the removal of scale. It is a procedure with which much more material is removed. During draw-peeling between 0.01 and 0.25 mm of the surface of the wire or 0.02 to 0.50 mm in relation to the wire diameter can be removed in one step. Besides this operation there are two more procedures known in the wire industry (picture).
Turn peeling is also a cutting process with a geometrically determined cutting edge with which material is removed alongside the wire. It is similar to turning, whereas in contrary to turning the tool is rotating and not the wire. In contrary to draw-peeling, turn-peeling has some disadvantages when working with small wire diameters. These are e. g. the lower production speed, the hazard of waviness due to vibrations and spiral structures due to uneven tool wear which occurs during turn-peeling. The operating range of draw-peeling plants in the area of <25 mm differentiates the two procedures from each other. For the processing of wire > 25 mm turn-peeling is more suitable as the processing of bars is possible.
Besides the possibility of turn-peeling there is the option of wire grinding. This is a cutting operation with a geometrically undetermined cutting edge. Recently wire grinding has been used more often in the area of descaling of wire rod in straight line with a succeeding wire drawing machine. It should be mentioned that with these operations the main focus is on the cleaning or the removal of scale.
Finally it can be stated that draw-peeling offers the following advantages in comparison to the other operations:
1. Cutting direction = feeding direction – an optimum surface topography (longitudinal structure) of the material is realized.
2. Processing of wire < 25 mm which results in a higher flexibility of the plant, because it can be adjusted to any diameter through the tool
3. Higher clarity and avoidance of abrasion and rests on the draw-peeled surface
4. Higher flexibility in the process speed which enables a stand-alone solution as well as an integration of the draw-peeling in existing plants
5. Operation speed with steel wire of up to 3 m/s, of non-ferrous metals up to 40 m/s, depending on the application
6. Comparatively high durability of a draw-peeling tool depending on the material
7. Low investment costs compared to turn-peeling plants
8. Exact adjustment of the chip removal due to the relation of the lean die to the draw-peeling die
Conclusion and result of the draw-peeling process
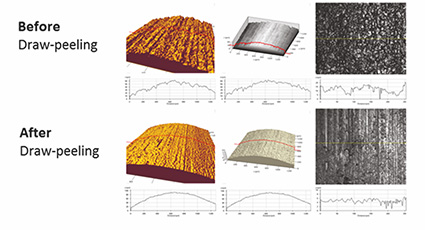
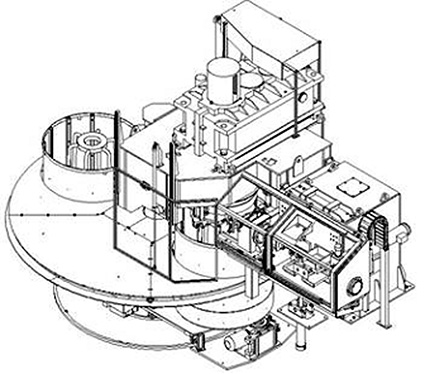
Drawing machine with integrated draw-peeling unit
[source KIESELSTEIN]
As mentioned above the draw-peeling process’ main purpose is the removal of defects. A homogeneous material with very low roughness of 0.1 µm (picture 5) is achieved. By varying the tool and the cutting geometry the surface roughness can be influenced or changed. This may become necessary for an easier processing of the wire after the draw-peeling operation. A defined roughness improves the lubricant absorption if required.
As mentioned above the draw-peeling process’ main purpose is the removal of defects. A homogeneous material with very low roughness of 0.1 µm (picture 5) is achieved. By varying the tool and the cutting geometry the surface roughness can be influenced or changed. This may become necessary for an easier processing of the wire after the draw-peeling operation. A defined roughness improves the lubricant absorption if required.
Machinery for draw-peeling
Besides the choice of suitable operating materials there is the question regarding the machine design. At first, two basic principles have to be differentiated (picture). On the one hand the single plant as a stand-alone-machine, which allows only for draw-peeling the wire, and on the other hand the principle of an integrated plant, where a draw-peeling unit is integrated into an existing plant. Several aspects should be taken into consideration. One is the general production process. Moreover, a high level of process integration causes additional disturbing sources that are influenced by the preceding or succeeding process. On the other hand, for the treatment of copper and aluminium material there are ways to combine the drawing with the process of draw-peeling. Both technological concepts have already been realized by KIESELSTEIN. In the following the main differences and characteristics are explained further.
Single draw-peeling plant
Single or stand-alone draw-peeling plants are further separated into processing from coil to coil and from coil to spool. This has no influence on the process of draw-peeling itself, i.e. the cutting operation. However, the plant design influences several boundary conditions of the plant technology. Currently, the coil-to-coil-concept is considered as the most mature one. Here the wire is shortly pointed and then inserted into the draw-peeling unit through an automatic pull-in dog. After clamping the wire end by the pull-in dog incorporated in the drawing capstan of the draw-peeling plant the cutting commences immediately.
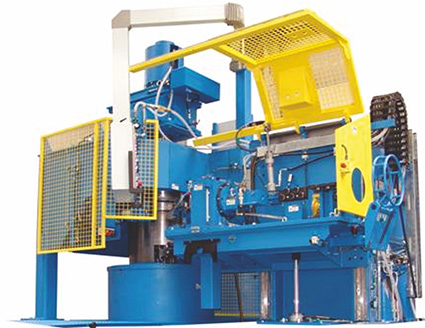
The draw-peeled wire falls off the hanging haul-off capstan onto the stem underneath. Due to short downtime for exchange of the tool, if necessary at all, a high rate of availability can be achieved with this plant concept, as the primary processing time, i.e. operation time of the plant can be used for loading and unloading. Required are a double wire take-up and a double pay-off system. Depending on the wire diameter the size of the capstan and the complete concept of the plant are defined.
With the concept of working from coil to spool the process of the pure draw-peeling depending on the material is the same as with the concept explained before. However, a larger pointing section could be necessary. If the restriction of the stopping with blade engaged does not exist, this concept allows for a more smooth wire take-up. It is especially suitable for copper and copper alloys and for the processing of aluminium.
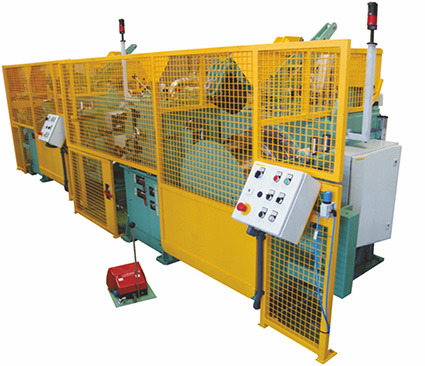
Trials on the KIESELSTEIN testing plant help to figure out which of the concepts is more suitable for the customer. Possibly the procedure of stopping can be tested and examined which helps to make a choice on the concept at an early stage.
Integrated draw-peeling technology
The integration of draw-peeling into an existing drawing plant is very common in the area of copper and aluminium processing. In the area of copper processing, depending on the tensile strength of the wire, there is the possibility to integrate the draw-peeling operation at the beginning, i.e. at the inlet of a multiple draft plant. The best position can be evaluated by using special computational models.
In addition, it could be necessary to carry out the draw-peeling operation several times, e. g. with very tough material. At first, during trials carried out on the testing plant fundamental draw-peeling processes have been developed in order to find the optimum technological graduation of drawing – draw-peeling – and one more draw-peeling step. Based on that, a plant with three steps has been developed, with a drawing operation at the first block in order to strengthen the wire material. The increased tensile strength improves the chip breaking which is realized in the second block. In the third step the surface quality is finalized by a planishing process. This plant concept, which is highly flexible due to the combination, allows for the following processing steps:
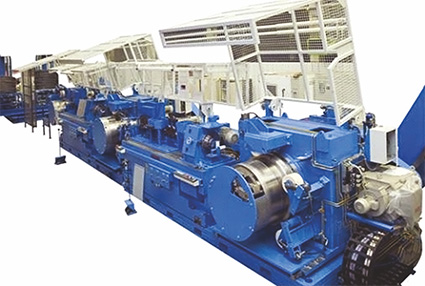
Drawing – Drawing – Drawing
Drawing – Draw-Peeling – Drawing
Drawing – Drawing – Draw-Peeling
Drawing – Draw-Peeling – Draw-Peeling
This creates an integrated plant, which allows besides the draw-peeling, a pre-drawing in one plant. By combining or integrating this processing step, the productivity of the plant can be increased.
Conclusion
Potential future developments are the improvement of the process in order to descale wire mechanically at low cost, the integration of further process steps such as drawing or pre- or post-treatment like coating or heat treatment, the processing of material that is difficult to cut like titanium / titanium alloys or magnesium / magnesium alloys as well as the improvement of the current state of technology by developing new tool geometries and the improvement of the choice of the tool material and coating. At the same time, in close cooperation with academic and non-academic institutes theoretic basics are created and broadened, with the target to reduce trial efforts and start-up time. KIESELSTEIN contributes to an improvement of quality in the wire industry and creates future fields of application for high-purity, high-resistivity and high-quality wire. n
By: Mr. J. Kieselstein,
KIESELSTEIN®International GmbH