Walson Woodburn Wire Die has strengthened its position as the key manufacturer and supplier of a diverse range of wire drawing dies. Based in Surat, it serves the Asian market, Middle Eastern countries and African market.
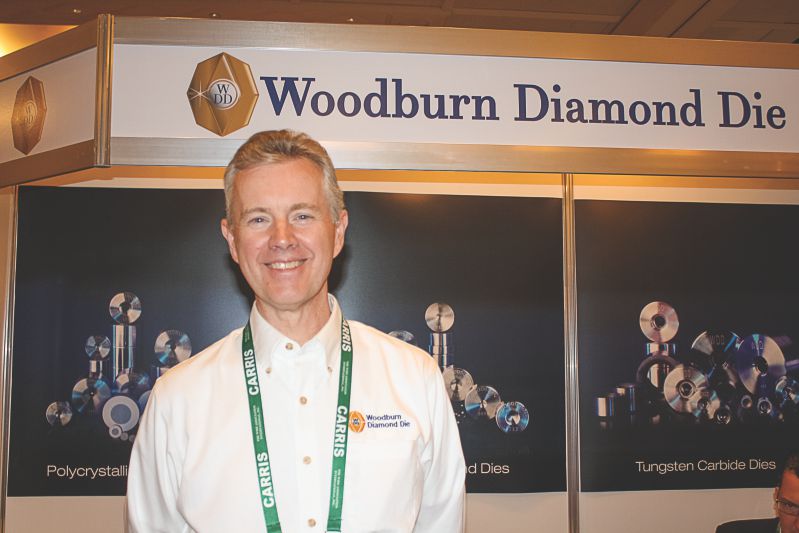
In an exclusive interaction with Wire & Cable India, Mr. Bill Schwehn, Senior Executive (Global), Walson Woodburn Wire Die talks about the journey of the company, the product range, their plans with regard to expansion, the kind of capabilities they have developed for diamond dies, and the future plans they wish to accomplish.
Wire & Cable India: Could you please highlight the key technological innovations that you have introduced in your products and operations in recent times?
Bill Schwehn: From humble beginnings in the wire die industry, Walson Woodburn Wire Die has grown from making singular dies by hand in the initial days of its business to now producing thousands in a controlled setting that focuses on the repeatability of very tight specifications required by today’s machine manufacturers and the wire producers utilizing them.
Particularly, advanced laser technology has been immensely beneficial in creating initial holes and then, through the profile characteristics, the subsequent shaping, polishing, and final sizing processes are carried out.
“ Being located in the diamond processing capital of the world allows us to have access to stones most appropriate for use in the wire industry. ”
WCI: What are the product offerings of your company?
BS: Our range of products and services includes — natural & synthetic single-crystal (S-C) diamond dies, polycrystalline diamond (PCD) dies, bunching, stranding & cabling dies-in both diamond, PCD, and carbide; recutting services/die repair for each material, diamond powders to support in-house repair, inventory management services and die shop equipment and training program.
WCI: Are there any plans to diversify your product range in the near future?
BS: We are presently looking at a critical area of wire industry that is underserved, and which is desired by our present customer base, but we have more work to do before discussions can go further.
WCI: Kindly describe the manufacturing capabilities of the company. What are the different steps you undertake which enable you to achieve quality improvement and enhance efficiency in your production operations?
BS: At the outset, producing world-class diamond dies starts with the selection of high-quality stones — whether it is natural or synthetic. Being located in the diamond processing capital of the world allows us to have access to stones most appropriate for use in the wire industry. Moreover, we source quality grade synthetic stones only from the recognized leaders in this field.
With regard to our capabilities, I’d like to mention that while in ‘S-C’, the capabilities on diamond drawing dies range from 0.015mm to 2.00mm, however, in ‘PCD’, our capabilities range from 40 micron to 32 mm and for carbide from 0.200mm to 75.00mm, which implies that we support the diverse requirements of the whole cabling industry – by offering dies suitable for different kinds of cables.
During the forming and finishing process, each product line is carefully monitored to obtain the required profile features. Moreover, vigilant use of new processing technology and measuring equipment can not only improve production efficiency but also meet or exceed customer expectations for the final product.
“ We are presently looking at a critical area of wire industry that is underserved, and which is desired by our present customer base. ”
WCI: Since the proper choice of drawing dies is of great significance in the wire drawing process, what are the key aspects which ensure that the die equipment is suitable for a particular wire drawing machine and process?
BS: The initial steps in developing the proper die train and profiles for a particular application include understanding how the machine is designed in terms of the drafting or reduction of the drawn wire, and, most importantly, in understanding the type of wire that will be processed. Once we figure out these two factors, we can make reasonable recommendations for the die sequence, the best die materials, and the profile features that support these combined properties.
WCI: Please describe the key strategic priorities of Walson Woodburn Wire Die. Also, how do you keep evolving your strategies of marketing in order to sustain your leading position in the global wire dies market?
BS: As what is generally true for most companies, we know exactly where we are the most proficient in and subsequently, we work hard to foster growth with companies that offer the potential to utilize these strengths. Having said that, we are also aware of the areas where we have some limitations and we continually look for ways to improve in those areas and search for outlets on product lines, which are presently limited.
In addition, we have an excellent group of representatives worldwide, who offer access to a number of regions in the global marketplace. These representatives are in constant communication with the wire mills which enables us to have immediate conversations on how to sustain business and help develop new product lines within the various sections based on knowing their individual needs.
“ Vigilant use of new processing technology and measuring equipment can not only improve production efficiency, but also meet or exceed customer expectations for the final product. ”
WCI: What is the future roadmap of the company for the future years?
BS: Our future goals are fundamentally going to be the same as they have been for the past 60 years, i.e. we plan to keep working efficiently, identify areas in the business that can be improved, and most importantly, we strive to support our customers and help them be successful in their respective markets.