“In view of the increasing demand of E-beam cables in India, we have diversified into the manufacturing of electron beam cross-linked cables by establishing a state-of-the-art manufacturing facility with the latest technology.”
Excerpts of the interview with Mr. Ramesh Singh, President (Works), Vindhya Telelinks Ltd:
Product Portfolio and Technical Capabilities
Cross-linking is the interconnection of adjacent long molecules with networks of bonds induced by chemical treatment or electron-beam treatment. Electron-beam processing of thermoplastic material results in an array of enhancements, such as an increase in tensile strength and resistance to abrasions, stress cracking and solvents.
E-beam technology, that is an ionizing energy, as provided by an accelerated electron beam (EB), is an efficient means of cross-linking polymers used for wire and cable insulation and jacketing. In this process, the three-dimensional un-meltable network is created. This can be done without heat. E-beam processing is fast, good, controllable and in a lot of cases more economical than thermal and/or chemical cross-linking. The electron beam processing in wires and cables helps to improve thermal, chemical, barrier, impact wear and other mechanical properties. The electron beam cross-linked cable offers increased life, higher temperature withstand capability, higher current carrying capacity, improved physical properties with reduced thicknesses.
Our product range of E-beam cables are – locomotive cables for railways, solar PV cables, automotive wires and cables, cables for shipbuilding, windmill cables and EBXL flexible wires.
Manufacturing and Technical Setup
Vindhya Telelinks Ltd. (VTL) belongs to the prestigious MP Birla group which is a century old group enjoying excellent market reputation due to its superior product quality and support to its customers. The group has been pioneering in the field of power and telecommunication cable industry. Under the umbrella of M.P. Birla group, VTL has earned an enviable reputation and leadership position in the market and has a satisfied customer base in the domestic as well as overseas market.
In view of the increasing demand of E-beam cables in India, we have diversified into the manufacturing of electron beam cross-linked cables by establishing a state-of-the-art manufacturing facility with the latest technology. This E-beam facility has a 3.0 MeV/100KW electron beam accelerator along with suitably designed handling systems for irradiation of 0.5 sq mm to 500 sq mm and cable diameter up to 60 mm. Also, the irradiation of various types of electrical and automotive cables and wires, PE sheets, polymeric tubes/pipes, heat shrink products, gems and diamonds, medical product sterilization. The E-beam irradiation curing of elastomer and other polymeric cables has several advantages over conventional steam/dry curing methods. The Company possesses various system certifications including ISO 9001:2015, ISO 14001:2015, OHSAS 18001:2007, TL 9001 & ISO 27001:2013 and is one of the largest and most reputed manufacturers of copper telecom cables, optical fiber cables, railway signaling/quad cables catering to diverse industry segments.
“VTL has emerged as an obvious choice amongst its customers across various sectors and is further strengthening its market position by offering reliable products with the highest quality standards.”
Market Footprint
Electron Beam cross-linked wire and cables, being superior over conventional cables, are being adopted in all critical application areas such as – railways, defence, solar power, wind energy, nuclear power etc. VTL has emerged as an obvious choice amongst its customers across various sectors and is further strengthening its market position by offering reliable products with the highest quality standards. Our major thrust has been on adopting the most modern and advanced technologies and realizing the benefits derived in creating a strong product line to address the emerging market needs.
Raw Material and Quality
The materials like PVC/TPU/PVDF/EPDM/EVA/CPE/PE/ETFE etc. are suitable for E-beam cross linking. The Electron Beam technology can modify the physical, chemical, molecular and biological properties of materials and products, improving their usefulness and enhancing their value. Electron beam accelerator (E-beam Accelerator) is widely used for industrial applications such as – surface curing, cross-linking of wires and cables and sterilization/decontamination of pharmaceutical products.
Desired properties are obtained by the fine tuning of Electron Beam voltage/current and immediate observation of parameters including – hot set, tensile strength, elongation, etc. The Electron Beam cured product offers distinctive advantages over conventional insulation material.
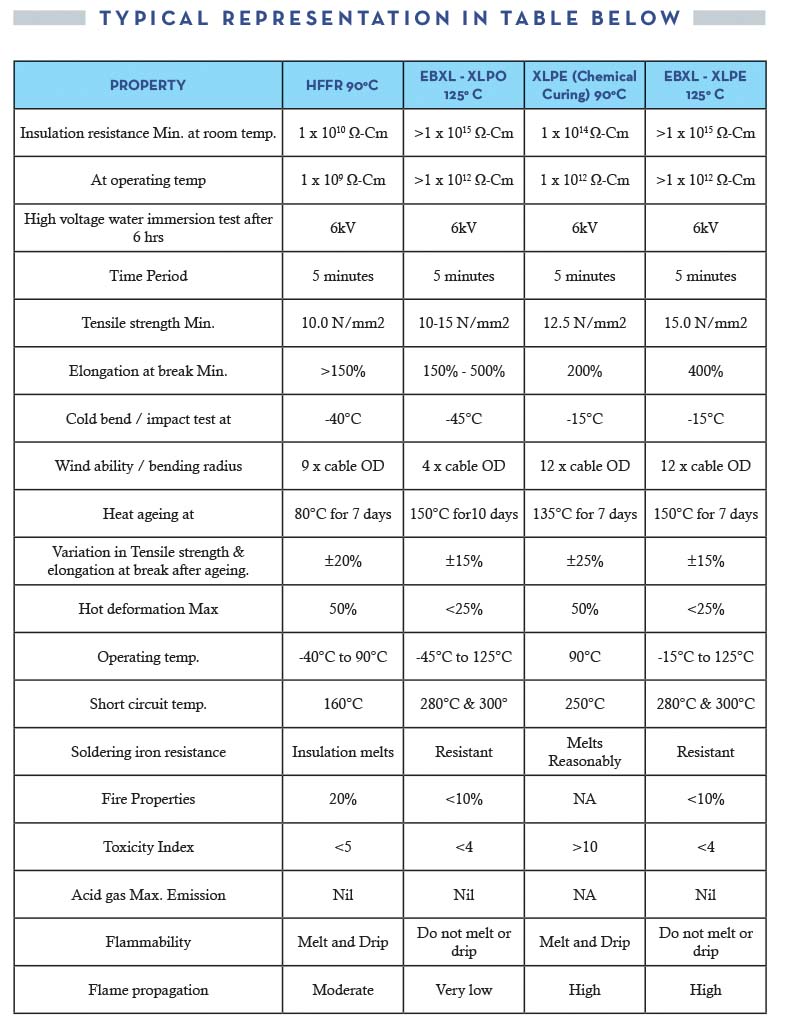
Market Potential and Demand Shift
By virtue of its offerings, the E-beam cables are being favored in sectors such as – solar, railways and shipping, where cables are required with cross-linked polymeric insulation with lower insulation thickness for high temperature applications.
The market for these cables is gradually increasing as new sectors are opening up for this technically advanced product. However, the larger consumer markets are yet to open up for E-beam cables, but due to its superior properties E-beam cables will soon start penetrating these markets in a big way. VTL is fully geared up to deliver cables as per market needs.
Advantages Over Conventional Curing Process
Some of the major advantages of E-beam over chemical cured cable are – higher degree of cross-linking up to 75-80% in E -beam cables as compared to the 50-55% in chemically cross-linked and there is no polymer degradation due to the exposure to high temperature as EB cross-linking occurs at room temperature. In addition, there is no oxidative degradation in polymer due to leftover chemicals, oxygen in air and operating temperature of cable, as observed in chemical cross-linking. The curing time is less as compared to chemical curing and the 125°C temperature rating implies – long life, higher ampacity, protection from thermal overloads.
Improved abrasion-resistance results in reduced wall thicknesses to save raw materials, space, energy and weight. Also, lower weight gives an extra premium in terms of lower energy consumption in trains, ships, planes and other transportation systems. As a matter of fact, there is no dripping in case of fire, less flame spreading, less smoke, and less pollution in case of fire. Moreover, no immediate melting means no immediate short circuits in areas like elevators, large public buildings like schools, theaters, airports, stadiums, ferries and so on. There is a reduced risk of damage by mechanical pressure and cut through, no short circuits and electrical sparking and also, improved oil and fluid resistance makes the cables function longer during immersion.