Vidya Metal Manufacturing Company is looking forward to a promising 2025 with plans to increase its manufacturing capacity to 25,000 TPA from existing 18,000 TPA through the upcoming facility in Bandapur, Rajasthan. Mr. Abhinav Goyal, Director, Vidya Metal Manufacturing Company Private Limited, revealed during an exclusive interaction with Wire & Cable India that the company is aiming to become a global leader in the wire industry, while exploring new sectors such as renewable energy, automotive electrification and smart infrastructure for significant growth opportunities.
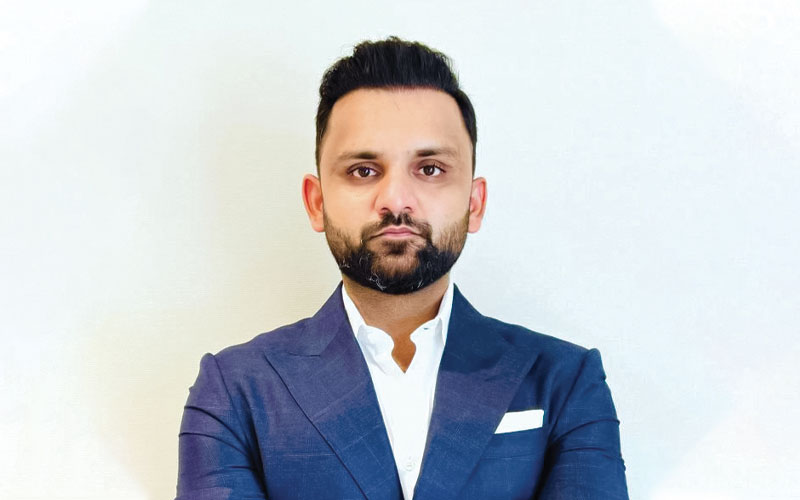
Wire & Cable India: Kindly share the business journey of VMI Group, outlining major milestones and crucial achievements.
Abhinav Goyal: Vidya Metal Manufacturing Company Private Limited (VMI Group) was founded in 1989 with a vision to support India’s rapidly growing electronic and automotive sectors. From the very beginning, we focused on producing high-quality copper bus bars, DPC wires & strips, and super enamelled aluminium winding wires & strips to meet the critical demands of these industries.
Our seven state-of-the-art facilities at Bhiwadi, Manesar, Bandapur, Chopanki, Daman, Jammu and Pathredi are equipped with certified facilities and globally recognized methodologies like 5S, Total Quality Management (TQM), Six Sigma and Production Part Approval Process (PPAP). These practices ensure that our products meet the highest quality standards, earning us the trust of our customers.
A significant milestone for Vidya Metal Manufacturing Company (VMMC) has been its ability to scale production of aluminium winding wires and strips to 18,000 TPA of total 80,000 TPA overall production capacity, with plans to increase this capacity to 25,000 tonnes this year to meet growing market demands. What truly defines our contribution is our role as a trusted supplier to several prestigious clients and leading OEMs in industries seeking quality performance in demanding conditions.
WCI: How much has your product portfolio diversified over the years? What are your best-performing products in the market? Where does the major demand come from?
AG: VMMC has evolved significantly since 1989. Our portfolio includes enamelled rectangular aluminum strips, aluminium bus bars, copper rods, copper bus bars and flats, bare copper wires, fibre glass, foils, bare wires, double paper-covered (DPC) copper, aluminum strips, DPC wire & strips, winding wires and polycoated strips. Over the years, we’ve diversified to include a wide range of products that cater to varied industrial needs.
These products cater to critical applications in industries such as transformers, motors, inverters, pumps, generators, submersible cable wires and compressors. Among our offerings, the copper and aluminium enamelled winding wires, DPC, foil, fibre glass, bus bars and flats are our best-performing products. These are widely preferred by industries for their versatility, quality and consistent performance in demanding conditions.
Watch: Top Cable Companies in India
WCI: Please tell us about your market footprint. How is your total sales volume split between the export and domestic markets?
AG: Currently, our major sales volume comes from the domestic market, which has been our primary focus. India’s rapidly growing sectors, such as energy, transportation and electronics have created a consistent demand for our products. We are proud to be a key supplier to prestigious companies like Bharat Heavy Electricals Limited (BHEL), Tata Power Company Limited, Havells India Limited, HPL Electric & Power Limited, Toshiba Corporation, Livguard Energy Technologies Private Limited, Su-Kam Power Systems Limited and Bajaj Group, along with other major clients and leading original equipment manufacturers (OEMs) in the inverter, electronic appliances, switch gears, fans, battery segments and transformer manufacturing industries. Our products have become critical components in powering infrastructure and energy solutions across India.
Our success in the market is attributed to the consistent quality of our products. Each item undergoes rigorous testing and quality checks to ensure it meets the performance requirements of the most demanding applications. This commitment to quality has earned us a reputation for reliability, which is a key factor driving customer preference. In the domestic market, our ability to quickly adapt to the evolving needs of sectors like OEM, transformer and electronics have been instrumental in maintaining our leadership. For the domestic market, we’ve been focusing on expanding our footprint by targeting regions with high growth potential and fostering long-term partnerships with our clients.
WCI: Please shed light on the manufacturing and technological capabilities of the production facility. Are there any plans for undertaking capacity expansion?
AG: Our manufacturing facilities form the backbone of VMI Group’s success. Located in Bhiwadi, Manesar, Bandapur, Chopanki, Daman, Jammu and Pathredi, these facilities are designed to meet the highest standards of quality and efficiency. All plants feature state-of-the-art machinery and automated processes that ensure precision and consistency in production. Our facilities are also equipped with globally recognized and certified methodologies like 5S, Total Quality Management (TQM), Six Sigma and Production Part Approval Process (PPAP). These practices ensure that our products meet the highest quality standards, earning us the trust of our customers.
VMI Group takes pride in integrating advanced technologies into its operations. For instance, the computerization of manufacturing processes and management systems has enhanced operational efficiency and allowed us to maintain real-time monitoring of production. This not only ensures better quality control but also minimizes downtime and waste. Our facilities also house new advanced mechanics for faster production cycles, which help us to meet the growing demands of our customers. These include high-speed winding and enamelling machines, automated testing systems and precision cutting tools. By adopting such advanced technologies, we’ve been able to maintain a competitive edge in the market.
Looking ahead, we have ambitious plans for capacity expansion. One of the most exciting developments is the upcoming production facility in Bandapur, Rajasthan. This new plant will focus on increasing our production capacity while incorporating the latest advancements in manufacturing technology. It will be equipped with highly automated systems and smart machinery to ensure both speed and quality in production. The Bandapur facility is expected to play a crucial role in meeting the increasing demand for our products, both domestically and internationally.
Currently, our facilities have a combined production capacity of 18,000 tons per annum, which we plan to expand to 25,000 tons per annum with the addition of the Bandapur plant. This expansion will allow us to cater to the growing requirements of sectors like OEM, automobile, and electronics.
WCI: What have been the recent developments at VMI and what are your future growth plans?
AG: At VMI, we are continuously evolving to stay ahead of industry demands while contributing to a sustainable future. Some of our recent developments reflect this commitment. On the operations front, we’ve enhanced our focus on domestic markets. As the major contributor to our sales, we’ve been expanding our presence by building strong relationships with major, distinguished clients. This growth has been fueled by our reputation for delivering high-quality products.
Another notable development is the solarization of our manufacturing facilities, enabling a portion of our plants to run on renewable energy. This initiative not only reduces our dependence on conventional energy sources but also lowers our carbon footprint, aligning with our vision for a greener future. In terms of environmental responsibility, we’ve implemented several eco-friendly practices. For example, our facilities now feature sewage water treatment plants to ensure proper recycling and disposal of water. We’ve also launched extensive plantation drives in and around our manufacturing units, contributing to local biodiversity and improving air quality.
As part of our diversification strategy, we are exploring new sectors such as renewable energy, automotive electrification, and smart infrastructure. These emerging areas represent significant growth opportunities, and we are developing products tailored to their unique requirements. Additionally, we aim to expand our research and development efforts to create innovative solutions for industries like energy storage, electric vehicles and green energy solutions. These efforts will help us in addressing the evolving needs of our clients, while staying true to our commitment to sustainability.
Also Read: Borouge Supporting Mumbai’s Digital & Industrial Transformation with Asian Cables
WCI: How do you perceive the current state of the wire industry? What are the major ongoing challenges in the Indian wire industry and how can these be overcome? What, according to you, are the primary growth drivers for the industry?
AG: The wire industry is currently at a pivotal stage, driven by rapid expansion of sectors like energy, infrastructure, transportation and electronics. The demand for high-quality wires and related products is growing steadily, particularly in areas like renewable energy (RE), electric vehicles (EVs) and smart infrastructure development.
However, the industry is also facing certain challenges that need to be addressed to unlock its full potential. One of the key challenges is the volatility in raw material prices, especially copper and aluminum, which are vital for wire manufacturing. This price fluctuation not only increases production costs but also makes it difficult for manufacturers to offer consistent pricing to customers. It also impacts pricing in a competitive market. To address this, the industry needs to adopt strategies like long-term contracts with suppliers, hedging against market fluctuations and exploring alternative materials that can reduce dependency on traditional metals.
Another concern is the need for technological adaptation in small and medium enterprises (SMEs) across the sector. Many units still rely on outdated equipment, leading to inefficiencies and inconsistent product quality. The solution lies in upgrading the infrastructure with advanced manufacturing technologies like automation, digitalization and Industry 4.0. Government initiatives like the Production Linked Incentive (PLI) scheme can also help the manufacturers to overcome current challenges and seize future opportunities. As industries become more demanding, the wire sector must keep up with advancements in materials, manufacturing processes and product specifications to meet higher efficiency and sustainability standards, as well as reduce costs. Additionally, fostering innovation through research and development will enable the production of specialized products tailored to emerging sectors.
The industry also faces issues related to global competition. With the influx of cheaper imports, particularly from countries like China, domestic manufacturers are under pressure to maintain their competitiveness. To address this, Indian manufacturers must focus on quality, innovation and customization to differentiate their products.
Additionally, government policies on import duties and promoting Make in India initiatives can provide the much-needed support to domestic players.
Another challenge is global supply chain disruptions, especially in the wake of global events like the Covid-19 pandemic. Delays in raw material procurement and increased logistical costs pose hurdles for manufacturers in meeting delivery timelines and maintaining margins. The industry can mitigate these issues by diversifying its supplier base, optimizing inventory management and exploring local sourcing options to reduce dependency on imports.
Lastly, environmental sustainability is becoming increasingly important. The wire industry is often associated with high energy consumption and waste generation. To overcome this, companies must adopt eco-friendly practices, such as using RE for production, implementing waste management systems and developing recyclable materials.
WCI: What is your vision and plan for VMI’s future?
AG: Our vision for VMI is to become a global leader in the wire industry by delivering innovative, sustainable and high-quality solutions that drive progress across industries. As we grow, our goal is not just to expand our business but also to create a meaningful impact on society and enhance the lives of our workforce.
One of our primary focus areas for the future is capacity expansion and innovation. With the upcoming production facility in Bandapur, Rajasthan, we aim to increase our manufacturing capacity to 25,000 TPA. This facility will integrate advanced technologies and sustainable practices, ensuring that we meet the evolving demands of sectors like RE, electric vehicles and smart infrastructure. We are also investing in research and development to develop next-generation products that align with global trends in energy efficiency and sustainability.
The welfare of our labor force is at the heart of our vision. At VMI, we believe that our people are our greatest assets. We have implemented programs to enhance the well-being of our workers, including healthcare initiatives, skill development workshops and financial literacy programs. By providing a safe and inclusive work environment, we aim to empower our workforce and enable them to grow alongside the company.