“Our Quality Assurance Plan (QAP) has been designed in a manner that covers all the parameters of quality and enables us to maintain almost zero rejection levels”
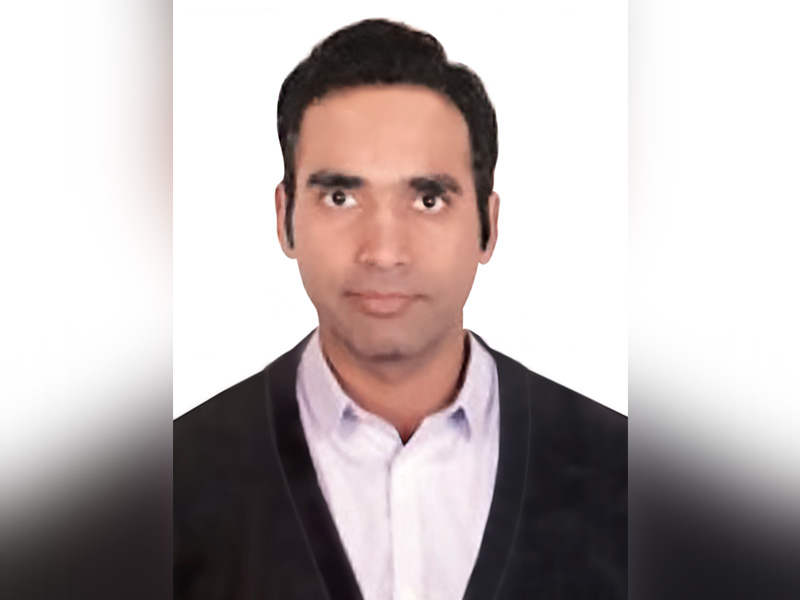
Varun Electrodes Pvt. Ltd. (VEPL) is one of the leading manufacturers of welding electrodes and MIG wires with global standards under the brand name ‘PRIMA’. Since its establishment in 1991, the company has been focusing on core engineering sectors around the world. Wire & Cable India recently interviewed Mr. Varun Kapoor, Director, Varun Electrodes Pvt. Ltd. wherein he dives into the product range of the company and sheds light on the infrastructure of the manufacturing facility.
Wire & Cable India: Kindly present an overview of Varun Electrodes and the key highlights in the business journey so far?
Varun Kapoor: Varun Electrodes Pvt. Ltd. (VEPL) is a family-owned professionally managed organization established in 1991, with a very small infrastructure catering to the domestic requirements of fabricators. With time, VEPL has grown up and catered to the complex requirements of various industries such as railways, coal mines, power plants, heavy fabrication, refineries, etc. We are not only catering to domestic industries but are exporting our products under our own registered brand name PRIMA.
WCI: What is the product portfolio offered by the Company for the welding wire segment? Please shed light on the unique features and key strengths of these wires?
VK: VEPL has its own registered brand name PRIMA and we offer a complete range of welding consumables such as mild steel, stainless steel, low hydrogen, hard facing, & cast iron welding electrodes, cutting & gouging electrodes, MIG/TIG welding wires and saw wires & fluxes.
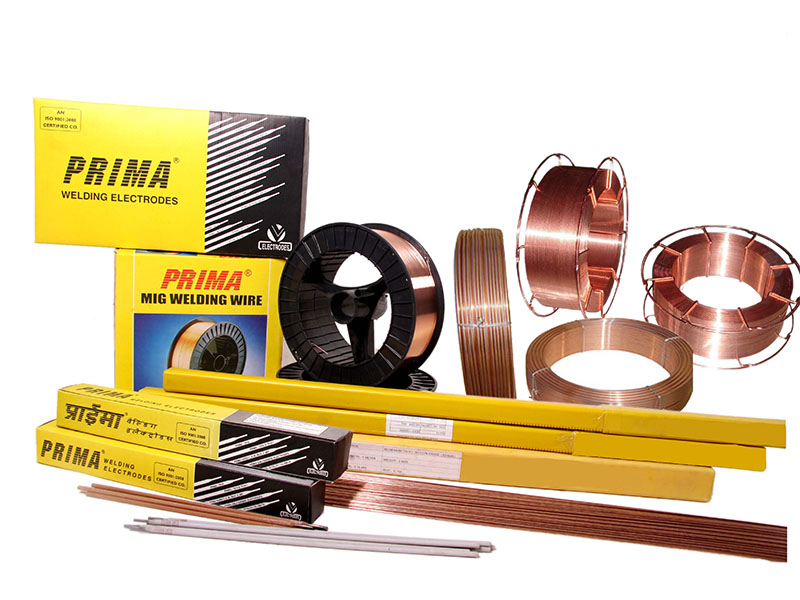
“VEPL is catering to all major OEMs in India such as BHEL, NTPC, ICF, RCF, MCF, Coal India, ONGC, SAIL, Tata, and automobile giants, among others.”
All the batches produced in VEPL are being completely tested in our fully developed and modernized laboratory comprising of the spectrometer, UTM, impact tester, metallurgical microscope, hardness tester, etc. Random samples are also sent to NABL approved laboratories for further quality confirmation. This vigorous testing helps us to maintain our quality and consistency in all batches.
WCI: Could you please talk about the market presence of Varun Electrodes? Are there any plans of expanding the market reach in the near future?
VK: Currently, VEPL is catering to all major OEMs in India such as BHEL, NTPC, ICF, RCF, MCF, Coal India, ONGC, SAIL, Tata, and automobile giants, among others. Apart from domestic supplies, we are also exporting our goods to a few of the countries in Asia, Africa, and the Middle East. We are looking to enhance our retail market in domestic as well as export market.
WCI: Tell us about the quality management system which enables the company in to ensure consistency in the product quality. Also, elaborate on the certifications the company has attained for its product range and manufacturing operations?
VK: VEPL is ISO 9001:2015 certified company. Our quality assurance plan (QAP) has been designed in such a manner that it covers all the parameters of quality and enables us to maintain almost zero rejection levels. Our products are accredited by authorities such as BIS, IBR, IRS, RDSO, EIL, TPL, and many others.
WCI: As a manufacturer of GMAW wires, what is your outlook on the growth potential and prospects of this wire segment? Tell us about the various applications of these wires and the industries which are the users of these wires?
VK: With each passing day, industries are evolving in automatization. GMAW wires play a vital role in the same; hence, the industry is in a major technology shift from MMAW to GMAW specifically, in the areas where continuous production is required. Also, with the development of casting units, the availability of various alloys in wire rods is becoming easy which helps the welding industries to shift from MMAW to GMAW. Hence, we can feel the industry shift at a high rate.
WCI: Please touch upon the capabilities of the company – with regard to manufacturing capacity and also outline the infrastructure of the manufacturing facility?
VK: VEPL has two manufacturing plants – both are located in Panipat, Haryana, and equipped to produce 8000 metric tonnes of welding consumables annually. With time, we have developed our pattern of manufacturing GMAW wires. Gradually, we are also enhancing the production with each passing year. From cleaning of wire rod surfaces to the winding and packing of wire, all the processes are done in-house.
WCI: Has there been any recent development at the Company with respect to expansion in the product range or any up-gradation at your manufacturing facility that you wish to talk about?
VK: Currently, the company is focusing on developing methods to reduce manpower involvement in the production cycle.
WCI: What are the future plans of Varun Electrodes going forward? Also, what are your growth strategies for the coming years?
VK: Soon, VEPL will be coming up with flux-cored wire production and promoting the same under its registered brand name PRIMA. The only strategy VEPL has been focusing upon for years is to deliver quality.
“VEPL will be coming up with flux-cored wire production and promoting the same under its registered brand name PRIMA.”