One of the most reputed and largest cable manufacturing companies in India, Universal Cables Limited (UCL) manufactures electrical products like extra high voltage, medium voltage, control and instrumentation cables, power capacitors, automatic power factor control and relay panels, etc.
In an absorbing interview given to Wire & Cable India, Amitava Bose, Chief Operating Officer, Universal Cables Limited, talks about the recent performance of his company, the new developments that have taken place in the company, the challenges that the wire and cable industry will face in times to come and his future targets.
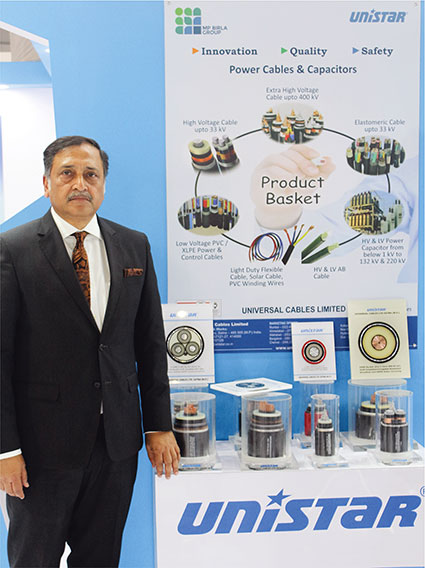
Excerpts.
Wire & Cable India: Could you tell us about UCL’s recent performance?
Amitava Bose: Our performance during 2018 to 2019 was one of the best performances in the last 20 years. We are doing very well this year as well. We have a strong order booking with a good product-mix to carry us forward. Despite the economic slowdown, we have cruised quite smoothly this year and I hope that the ending of the year 2020 would be as good as that of the previous year.
WCI: What new developments have recently taken place in your company?
AB: One of the new developments is in the coveted market segment of 400kV cable; and in the next fiscal year, we expect to supply a very large quantity of 400kV cable to a power utility in India and install the same. Initially, we had a technical tie-up with Furukawa Electric Co., Ltd., Japan, for technology transfer for Extra High Voltage (EHV) cables manufacturing using VCV manufacturing technology and the know-how for the complete system for underground power transmission system. The VCV technology is available to technically advanced global cable manufacturers. The EHV segment is to be seen as a complete system including cable jointing technology along with other associated components. The technology transfer from Furukawa Electric Co., Ltd. has been completed. Our association with Furukawa Electric Co., Ltd. has given us the fillip to execute a large number of projects up to 220kV, thereby making ourselves independent and more secure in terms of technology. As the next step, we have entered into a technical tie-up with NKT GmbH & Co. KG, Germany, in our endeavor to commercialize 400kV-500kV EHV cables which is the highest voltage class in the world. In some countries, it is 400kV; and in some countries, it is 500kV – according to the system they have adopted.
WCI: Could you tell us about the machinery or equipment you have installed for 400kV at your facility?
AB: We have the Vertical Continuous Vulcanizing technology, which is popularly known as the VCV process. This has been adopted in many advanced countries – Japan and a few European countries. We have adopted the same technology in India. The VCV process has many advantages over the conventional CCV process. Of course, VCV technology is much superior to CCV technology and that is the reason for our choosing the VCV technology. Worldwide, in many of the customer’s specifications, it is mentioned that the product has to be manufactured using the VCV process. We have two VCV lines, one from Troester, Germany, and the other from Maillefer, Finland. We are also planning to install the third VCV line to further increase our capacity. So, right now, we have the largest capacity of Extra High Voltage cable manufacturing in the country. The two lines provide redundancy to maintain continuous production in the event of stoppage of one line so the customer is sure of the security of supplies. And, of course, the third line would level our capacity to that of any of the largest manufacturers in the Asian region.
The other important aspect is the metallic sheathing technology, which is for water protection, impact resistance and path for the system fault current. We have all varieties: sheathing with lead, corrugated aluminum, smooth aluminum and aluminum tape. It is worth mentioning that we have a unique facility of providing seamless corrugated or smooth aluminum sheath by the extrusion process without welding as provided by most manufacturers. By providing seamless aluminum sheath, no weak spots or pin holes exist in the whole aluminum sheath. Most of today’s companies across the world use the welded process, but we can provide a superior seamless extrusion process. In India, we are the only company that has this extrusion process for providing seamless sheathing with aluminum. The other process we do is the lead sheathing process. We have two lead sheathing lines which here again provide similar redundancy to maintain continuity of production even in a situation where one line is under breakdown or maintenance.
To summarize, we have two vertical lines for extrusion, two lines for corrugated aluminum sheathing and two lines for lead sheathing providing complete process redundancy. We also have two independent EHV testing laboratories, apart from other testing laboratories for medium and low voltages cables. So, if you see the total chain, you will find that we have built in redundancy right from start to finish for the EHV manufacturing process.
WCI: What are your future targets?
AB: In 2020, we expect the company to grow by 20 percent. The area where growth is expected to take place is the extra high voltage segment. As you know, the extra high voltage cable segment is a project-based business; therefore, there are a lot of issues to be tackled, such as obtaining right of way and fund availability to the utility. As you know, today, underground power transmission is the only alternative in urban areas without which further urban development is not possible.
WCI: What challenges will the wire and cable industry face in times to come?
AB: A change is taking place in the ecosystem of the power sector: Conventional energy is gradually becoming renewable energy. So, conventional cables need to be gradually replaced with renewable cables. The industry must be prepared to face this challenge. The cable companies in M. P. Birla Group comprise of Universal Cables Ltd., which specializes in making power cables; Vindhya Telelinks Ltd., which specializes in optic fiber cables, special cables for communication, LV cables, DC Solar cables and EPC business; and Birla Cable Ltd., which specializes in optic fiber cables. Universal Cables Ltd. has a factory in Goa as well which manufactures light duty cables. We also have a joint venture company with Furukawa Electric Co. Ltd., Japan, which manufactures high performance optic fibers. We are trying to establish a synergy amongst these companies. For example, we have an EPC division at Vindhya Telelinks Ltd. We can always exchange the strengths of each of these companies to bring in a synergy. We are prepared for it, and I can tell you that many of the Universal Cables orders cater to the EPC division of Vindhya Telelinks Ltd. and, likewise, vice versa. So, we are building up our strengths continuously to face the market challenges and opportunities in India. We have to turn India into a developed nation. Our Prime Minister’s vision of a USD 5 trillion economy is going to bring a total change in the business landscape for engineering and infrastructural products. The only problem is that there is a liquidity crunch in the market, which has been because of due diligence in the banking system where banks and financial institutions have become more careful and risk-aversive. We, therefore, do not see the flow of money in the downstream infrastructural projects to the extent at which the reforms have been made. So, there is some sort of mismatch between the aspirations of the Government to build up a seamless infrastructure and the flow of liquidity on the market. This will take some time to settle down. We may have to go through this situation for another year. We have to view business from a long-term perspective, and so I think, we have to tackle the current challenges and wait for better days.
WCI: Could you tell us about your solar cable segment?
AB: To cater to this segment, we have put up two of the most modern lines from Rosendahl, Austria. It is a totally automated plant with state-of-the-art features. This is backed-up by an Electron Beam Accelerator for Electron Beam Cross-linking. It is known as the physical cross-linking process – the cross-linking of the polymer to give it higher temperature resistance and better physical strength and provides higher current rating. We have already manufactured samples, which will be sent for approval. So, solar cable is a big market for us. The setup has been done at Vindhya Telelinks Ltd., Rewa, M.P.
WCI: Is there anything else you would like to add?
AB: Universal Cables Ltd. has always believed in quality, and quality pays in the long run. There have been ups and downs in terms of competition, and we had to retreat from many of the market segments. Now we are getting back these markets because of our emphasis on product quality. We are gradually penetrating the global market. Our first interest is to cater to the home turf where the market is large. We are simultaneously growing in the export market, though the growth has been rather low: It would be around 5 percent of our total turnover. However, in future, we expect a wider and deeper footprint in the neighboring countries and beyond.