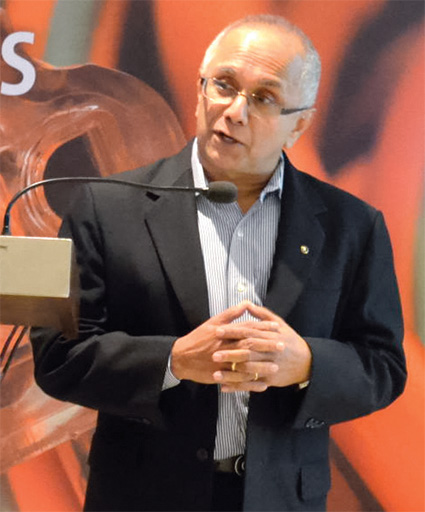
UL (Underwriters Laboratories), a premier safety science company, organised a seminar on the importance and challenges in the adoption of TR XLPE Technology in the Indian cable industry. The seminar was followed by a brainstorming session chaired by Mr. R. A. Venkitachalam, Vice President, Public Safety Mission, Underwriters Laboratories Inc., on developing a roadmap to ensure consumer safety from electrical hazards.
The forum saw the convergence of various stakeholders, industry representatives and senior officials who brought to the fore key challenges in the adoption of TR XLPE in India and their recommendations and expectations from the governing authorities.
.
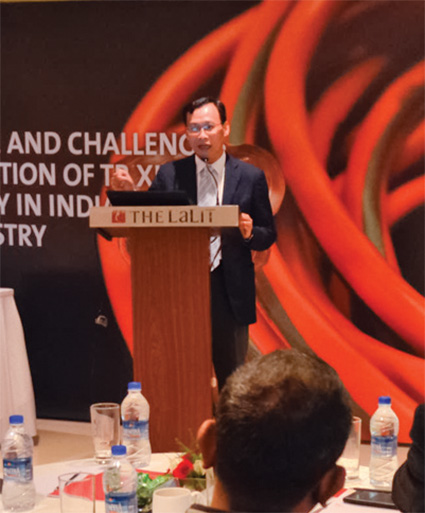
In his introductory speech, Mr. L. F. Lai, Vice President, UL’s Wire & Cable Division, said that UL is synonymous with safety and wire and cable is one of the earliest product categories certified by UL around 100 years ago. Among the various challenges, the manufacturing variations in underground cables are a key industry challenge today causing unsafe products for consumers. The industry is unfortunately witness to many manufacturers who use inferior quality copper or less copper in cables in order to be cost-competitive. To control the various manufacturing and performance issues, UL has a stringent programme to test and certify the quality and performance of the cables. But the important question that is being raised in the industry is how they can ensure that cables made using TR XLPE technology complies with safety requirements.
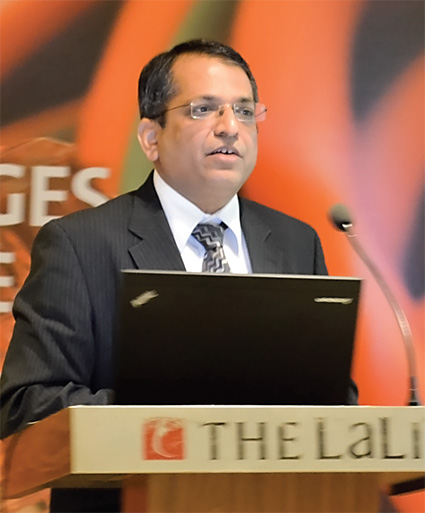
Speaking on the significance of TR XLPE compound used in MV cables, Mr. Rajendra Mishra, Chief Operating Officer, Power Cables Business, Sterlite Technologies Limited, addressed the technology aspect of the TR XLPE compound and stressed that as a growing nation, India needs more power. Statistical indices show a sustained increase in GDP, industrialisation and increase in per capita income in India, giving rise to a demand for power. However in the 11th Five Year Plan, transmission and distribution has trailed due to an inefficient distribution network, causing a bottleneck in the power value chain.
In India, ironically, most utilities will deny that cables fail, but we still have power outages. With low analysis and accountability, we are somewhere in the middle of the reliability index. Data provided by the World Bank show that inefficient power systems have a deep and negative impact on businesses.
We have the installed capacity, but it is not reaching customers due to inefficient distribution and transmission. Various solutions for water treeing have been implemented but how far they have worked is debatable. In developed countries like North America, since 2000 onwards, no non TR XLPE cables have been specified. Europe has seen a huge reduction in failures since the use of TR XLPE cables. Asian countries are following suit based on the success stories of other developing nations.
Distinguishing between TR and normal XLPE is an issue that is often neglected in India. Another problem is that utilities are not willing to admit that water treeing is a big issue; they often cite mechanical problems instead.
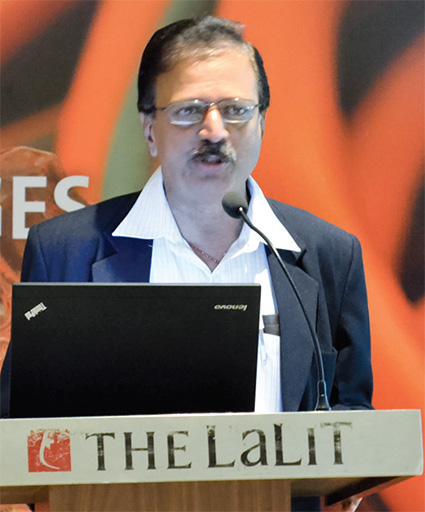
Addressing the challenges of using substandard TR XLPE materials, Mr. L. Ravi, General Manager (Elec) Distribution Automation & Smart Grid of Bangalore Electricity Supply Company Limited (BESCOM), pointed out that quality is a big issue all over India, unlike in other developing nations. It must be understood that ensuring quality enhances the efficiency and safety of the cables. Karnataka is the pioneer state in piloting the distribution automation project in India which is aimed at significantly enhancing the power value chain. The operating environment of BESCOM spans 47,972 km across a population of 20.7 million and a customer base of 15.548 million, and an average BESCOM cable lifespan is 15-20 years.
There are several reasons for the failure of cables – some known factors caused by different utilities and other unknown factors that are not analysed. Reasons for the cables to fail to perform and last the duration of 10-15 years can range from faulty and haphazard handling of the cables during transportation to lack of training in laying the cables properly. Supervision during handling and laying of cables is crucial to their overall performance.
In India, a lifespan of 20 years is only on paper. It is, practically, not likely to last that long. To improve the lifespan, the onus lies on manufacturers to be honest in the procurement of genuine material compounds and in the production of efficient cable networks. In India, utility engineers are not competent to test the cables for reliability and the inspection engineers are not sufficiently trained. During testing, it should be made mandatory for a junior engineer to provide a supporting role to a senior engineer and learn the training methods in the process in order to independently carry out the testing protocols.
As far as the jointing of cables is concerned, there is no record of any analysis on how the jointing was done or who it was done by. It is important to analyse how the jointing kits are supplied and how they are utilised. The question of safety is directly related to the quality, materials, laying, jointing and maintenance of the cables.
BESCOM has initiated a programme on the strengthening of cable networks to improve reliability. Besides, distribution automation is a new concept that is also gaining traction. The objective is to provide assured quality and reliable power supply in the 11 KV cable distribution network to minimise loss of time and reduce loss in cost. The benefits of automation include real-time control, better reliability optimum power factor and online energy audit. Facing the threat of privatisation, utilities must adopt innovations to cater to the demand for reliable power in the country.
Following a rare instance of a death caused by a distribution transformer explosion, the importance of analysis of transformer and cable failure was highlighted, especially in rural areas. Under existing conditions, transformers are just replaced without ascertaining the cause of failure.
The integrity of manufacturers and inspectors is very important. Every batch of cables has to go through complete testing and certification for quality control. Or else, under the current conditions, 5 years is the lifespan of a cable.
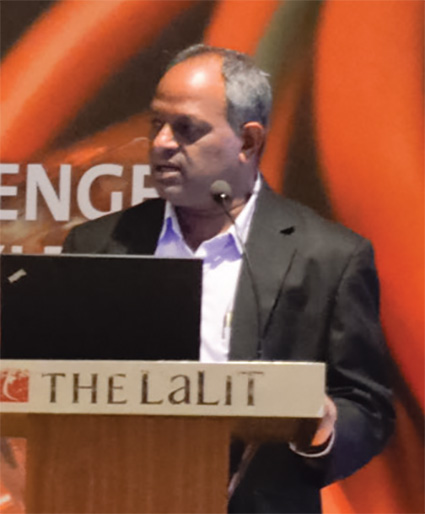
Highlighting the challenges of dealing with substandard TR XLPE materials, Mr. Dhruv Palekar, Additional Vice President, Central Engineering Services, Reliance Infrastructure Ltd., said that Reliance Infra has been involved in the continual improvement in quality movements with 1,500 employees working on quality control.
A lesser known fact about PLC cables is that if they are not disturbed, they can last up to 50 years. Failures occur when they are disturbed, and so many utilities are responsible for this. In a city like Mumbai, which witnesses heavy rainfall and high levels of humidity through most part of the year and in areas of reclaimed land, the lifespan of a cable cannot exceed 15 years. Therefore, to circumvent the problem, Reliance Infrastructure shifted to TR XLPE cables.
Speaking about the challenges, Mr Palekar emphasised that there is no third-party laboratory in India to test whether a compound used is genuine TR XLPE. There are approved vendors but there is no assurance of quality products from them. Therefore, the expectations from the industry include:
- Elevating Indian standards to differentiate between insulation materials
- Focusing on performance criteria of cables in line with global and ICA standards
Dr. Peter Pang, Asia Pacific End Use Marketing Manager for Dow Electrical & Telecommunications, highlighted the key challenges faced by TR XLPE compound manufacturers and advanced solutions for reliable medium-voltage cable.
The potential defects of cables include water trees and contaminated insulation. The main cause, however, is electrical stress. TR XLPE cables have proven to lower life-cycle costs significantly. The third generation of innovation in TR XLPE cables helps maintain quality and reliability and the new generation materials used give a much longer life to the cables. Among the benefits include lower life-cycle costs, reliability and options to reduce current cable costs.
To ensure quality and eliminate counterfeiting, chemical fingerprints are used to analyse whether materials are genuine. FTIR testing can help identify the chemical fingerprint of each compound. In addition, every batch of cables comes with a unique batch number with the production date. So, from a quality standpoint, suppliers should provide the batch number to customers.
Speaking on the advanced solutions for reliable medium-voltage cables, Mr. Hakan Lennartsson, Value Chain Marketing Manager, Borouge Pte Ltd., spoke of a higher demand and need to develop power in India where the reliability factor is high and costs are controlled. XLPE has become the preferred material for power cables. But with a large variety found on the market, every XLPE cable is different. In some cables, additives are added to ensure that they are water tree retardant. Manufacturing of cables earlier involved single extrusion but now the standard is triple extrusions, which have significantly improved the quality of cables.
In many countries, water barriers like metallic sheets are used, but a huge cost is attached to it. Different countries learn and innovate based on their experience when it comes to increasing the lifespan of cables. In Europe, the lifespan of a cable is around 30-plus years. Training in handling and laying is very important to ensure longevity. In France, a barrier system is used with metallic sheets to ensure the cables are water-tree retardant.
Looking at the performance of PVC and HTP cables over 10 years, HTP cables have roughly double the electrical withstanding strength. Building a failure analysis is a very important step. Instead of developing its own methods of analysis, India should look at what is available and make the best use of it.
Fingerprint or FTIR testing can be tampered with and is therefore not a reliable means of testing. Problems can occur at any stage. Knowledge about different parts of the cable will minimise any errors in laying the cables. Quality control is a total package that includes cable design, performance, etc. It is vital to remember that ‘know why’ is as important as ‘know how’.
Mr. Rajnikanth Umakanthan, Business Head, Energy, Industrial Systems, Chemical, Wire & Cable, UL, India, highlighted the role of third-party testing and certification bodies like UL to support the industry needs. Not just specific to TR XLPE but to wire and cable industry as a whole, safety and compliance to standards are important issues. The industry, as we see it today, has good and bad manufacturers. Bad manufacturers use cheap, substandard materials and do not go through the testing, evaluation and certification process. By avoiding the stringent quality control measures they are building unsafe products sold at a lower price on the market. The good quality-controlled products obviously are more expensive, thereby giving bad manufacturers an unfair advantage. To sustain themselves, quality-conscious manufacturers are forced to look for ways to cut costs by using cheap components and making false claims on the product performance. What they do not realise is the huge impact it has on their business, market reputation and the financial implications that result. At greater risk is the loss of life or injuries caused by unsafe products. Recent incidents in Mumbai and Bangalore prove this point. This is where third-party certification companies like UL can make a difference and ensure safety and compliance.
UL works through the value chain right from the design stage to market performance and evaluation of the product. UL is involved in standards development and has written over 1,400 standards for various products starting from the design stage. One of the unique positions that UL enjoys is that it offers a complete circle of trust – right from writing standards to testing and certification. UL also invests in corporate research in wire and cable industry to develop new standards and inputs to change testing methods as the product and market evolve.
To cater to the value chain, UL has over 19 inspection centres with 120 field representatives in Asia alone. 70,000 inspections are conducted every year among 9,000 manufacturers, with 1,100 manufacturers in the wire and cable industry in Asia. UL also works with international organisations like the Interpol and Homeland Security to fight and control counterfeiting. In continuation to inspection, market surveillance is also carried out to ensure compliance.
All UL certified products have a UL label. To prevent copying, gold holographic labels are used. UL is also open to offering training programmes in installation when required.
Ensuring Consumer Safety from Electrical Hazards – Developing a Roadmap
The brainstorming session moderated by Mr. R. A Venkitachalam, Vice President, Public Safety Mission, Underwriters Laboratories Inc., was a knowledge-gathering and empowerment session aimed at driving forward thoughts and ideas and allowing an exchange of views between the participants to arrive at sustainable solutions to ensuring consumer safety in the face of electrical hazards.
As the Indian economy grows, the generation, distribution and usage of power is expected to rise. Faced with umpteen challenges, power generation is set to become more diverse. Statistics recorded by the National Crime Records Bureau for 2012 show that 3,72,000 people died due to accidents by unnatural causes. Out of this, 30,000 deaths were caused by fire and electrical accidents. The magnitude of the problem is huge and it can affect anyone anytime. As responsible conscious, educated citizens of society, it is up to each and every member of the community to sensitise ourselves and find solutions to the various problems that we face today. A report indicates that in rural areas, the incidence of electrical accidents is higher than in urban centres. As electricity becomes more accessible in rural areas, the need for education and awareness of the hazards is that much higher.
The views that were brought forth in the session revolved around five pertinent questions:
1. How big is the problem today?
2. What are the possible causes?
3. What is being done?
4. What needs improvement?
5. How can we join hands to resolve the problem?
As a result of brainstorming the various challenges and finding solutions to overcome them, the following actions points were recommended:
- Model distribution points with specified minimum heights to make the electrical points child proof and electric shock proof
- Sensitising citizens through training and education to create awareness
- Law to permit only trained and licensed electrical engineers to test and install electrical points and poles
- A dedicated corridor for utilities; planning localities with proper electrical infrastructure.