“Having established ourselves as a prominent player for EBXL cables in the domestic market, we are now looking for more opportunities in the global market with renowned transport companies…”
Excerpts of the interview with Mr. N Srinivasa Rao, President, Thermo Cables Limited:
Product Portfolio and Technical Capabilities
Thermo Cables Limited is a specialty cable manufacturing company that is synonymous with quality and satisfying customers’ needs in the most critical areas. Our product range includes – LV power & control, instrumentation, thermocouple, fire resistant, high temperature (PTFE, FEP, PFA, ETFE, ECTFE and SiR), E-beam, elastomeric and other specialty cables.
With the addition of the E-beam facility, our supplies are extended to railways, navy – ships & submarines, offshore, marine, wind mills, solar plants and material handling sectors. The E-beam wire and cables offer superior performance in demanding applications, and in extreme environments.
Manufacturing and Technical Setup
Presently, we have a 3-MeV accelerator and another 2-MeV accelerator is under installation. Our 3-MeV accelerator is equipped with a reflection magnet which collects unused energy and reflects back onto the cable which increases the depth of beam penetration and enables to cross-link cables of large diameters.
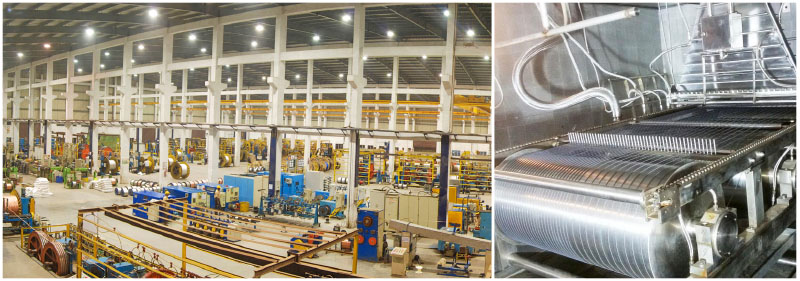
Market Footprint
We have made good progress in terms of approvals with Indian railways and Indian navy who are the major consumers of the E-beam cables. We have become an approved supplier after satisfying qualifying requirements with Indian railways in a short period of time as compared to our close competitors. There’s been a surge in our international marine sector business for EBXL cables after obtaining ABS approval and we’ve also got ourselves associated with global wind companies.
At present, we are serving to – railways, shipbuilding, marine, offshore, wind mills, solar plants and material handling industries. Having established ourselves as a prominent player for EBXL cables in the domestic market, we are now looking for more opportunities in the global market with renowned transport companies such as – Siemens, Alstom, Bombardier Inc., etc.
Raw Material and Quality
Using the right compound is essential for E-beam cables and we are proud to have our own compounding facility which ensures quality, shorter lead times and competitive prices. We are making various compounds such as – EPDM/EPR, EVA, CPE, PCP, CSP, SHF2, and LHLS for non-toxic and non-corrosive halogen-free E-beam cables that are used for critical applications in railways, navy, windmills, solar plants etc. While processing these compounds, we consider features such as – tensile strength, elongation, hot set and permanent set, fire properties, halogen content, toxic levels etc., which are very important for the performance of E-beam cables.
“Using the right compound is essential for E-beam cables and we are proud to have our own compounding facility which ensures quality, shorter lead times and competitive prices.”
Market Potential and Demand Shift
With an estimated potential of Rs. 2,000 cr per year in the domestic market for E-beam wires and cables, we would like to have as much share as possible from this consistently rising demand. We are educating our customers about the advantages of the E-beam cables over conventional cables and going forward, we are confident of the customers demanding E-beam cables for many of their applications.
Advantages Over Conventional Curing Process
The benefits and advantages of E-beam cross-linking are well-established and it is the most important commercial application of radiation technology. The major advantage of the E-beam cables is that they are lightweight with reduced diameters due to thin wall insulation/jacketing with improved service life than the conventional curing process. The E-beam cables are cured at room temperature whereas conventional curing is done at higher temperatures and may deteriorate the thermal properties of the insulation/jacket materials.
Some of the other advantages include – improved service/operating temperature, increase in current carrying capacity, and improved mechanical properties. Moreover, the service-life of the cable is also increased with this process, which is environment-friendly and ensures uniform curing of the cable. Also, the E-beam cables have improved abrasion-resistance; high throughput, improved flame propagation resistance, and reduction of short-circuit conditions.