“We reach out to the customers and provide them the entire concept and work with their teams, hand in hand, to implement the IIoT solutions and ensure that the customers reap complete benefits using Industry 4.0 tools”
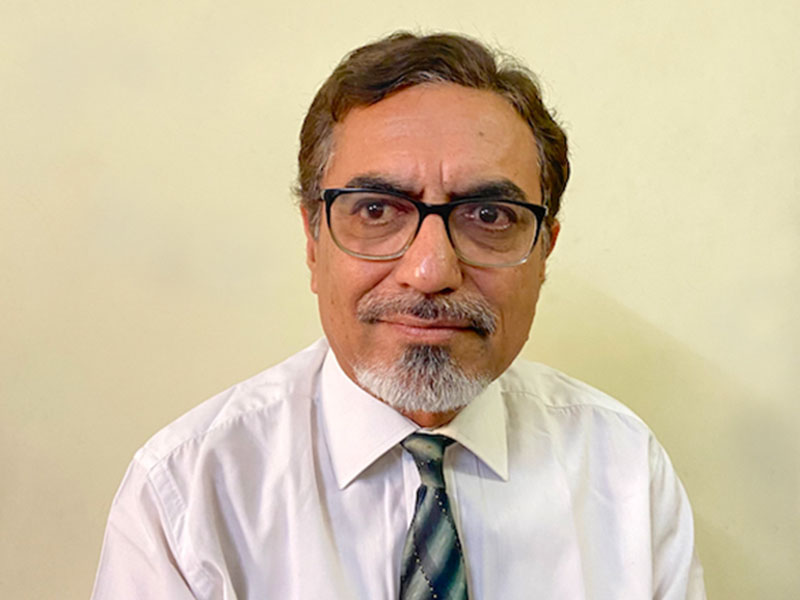
Supermac Industries (India) Ltd. is a leading global wire and cable extrusion line manufacturer with a focus on solution provider on extrusion and process technology. The company caters to numerous industries in wire & cable and related sector in the power, optical fibre, building wire, automative, elastomer, control, flouro carbon cables and specialised medical tubing products. Since its inception in 1974, innovation has been the driving force behind Supermac’s success. The company has time and again set the industry benchmark for devising innovative techniques to meet the burgeoning demands of a new-age economy. In an interview with Wire & Cable India magazine, Mr. Vivek Kohli, Director and Board Member of Supermac Industries (India) Ltd. talks about the implementation of Industry 4.0 by the wire and cable segment, common challenges faced by the customers, and some of the noteworthy projects accomplished by the company. He also reveals how the government’s ‘Make in India’ initiative is the right opportunity for the industry to implement Industry 4.0 concepts. Mr. Kohli has an overall experience of 43 years in the wire and cable and the insulators industry. He has held several senior positions including corporate management roles in the wire and cable industry in India and the Middle East. He is a pioneer to get the XLPE cable and HTLS conductor-technologies in India and author of the book called ‘Power Cable Technology’, published by CRC press USA in 2016.
Wire & Cable India: How according to you, has the implementation of Industry 4.0 grown over the years? Do you think that the wire and cable industry is ready to adapt to this evolving industrial revolution?
Vivek Kohli: Industry 4.0 or the fourth industrial revolution as it is commonly called is related to a new generation of connected technologies and data-driven modules. It is a combination of data analytics, Big Data handling, robotics & automation, Artificial Intelligence, Internet of Things (IoT) and process control digitisation, etc. across the business domain.
New and innovative technologies, such as robotics, automation, Artificial Intelligence (AI), industrial communications, data handling, and 3D printing, etc. are instrumental in bringing in transformation in the global manufacturing landscape. Those who have adopted Industry 4.0 or smart manufacturing processes at an early stage are enjoying the benefits of increased productivity, efficiencies, and lower costs. An intelligent factory is not only about the digitalisation of the processes but also related to the efficient use of energy, optimisation of the processes, and the reduction of the impacts on the environment.
The pace of implementation of industry 4.0 in India is lagging behind other nations like the US, the UK, Germany, Ireland, Sweden, China, and Japan, etc. These countries are widely incorporating the Industry 4.0 capabilities in their domestic market. The adoption of the Fourth Industrial Revolution or Industry 4.0 in India is at a nascent stage. It is expected that the Indian industry may witness widespread implementation. However, it still needs to develop in the near future and overcome current sluggish growth levels which are mainly due to initial investment, inadequate cybersecurity norms, and lack of infrastructure. The time has come to think about this slow growth and where India stands in competition with other countries. Time is running out, and India needs to move fast for a few years from now.
By the use of advanced analytics, production capacities can be improved and it might be possible to reduce the cost of poor quality. Using data analytics tools, there will be a shift towards a proactive model i.e. prediction and prevention of defects. Production cycles can be made shorter by the use of automation and robotics. This will give an improvement in the end-to-end business cycle. Cost-effective measures for business processes can be implemented using digitisation. IoT and connectivity of machine to people and machine to a machine or plant to plant would lead to a reduction in human errors and give improved supply chain and reduced lead times.
The wire and cable industry in India needs a big push for adopting the 4th industrial revolution. The government of India’s initiative of ‘Make in India’ is the right opportunity for the industry to implement Industry 4.0 concepts.
Supermac Industries in its endeavour to conform to Industry 4.0 norms has taken strong strides forward in implementing several digital initiatives, especially with regard to Industry Internet of Things or IIoT, which plays a key role in enhancing the areas like process optimisation, quality control, cross-vendor shop floor integration, energy efficiency predictive maintenance, data security. We have been able to implement such initiatives in the wire and cable industry successfully and looking forward to collaborating with our existing and future customer base and scale up on this initiative. With the services of our digital partner software, we have transformed the way to manufacture products, seamlessly co-ordinate amongst various factories & departments, connect with customers, and digitise workplaces. Our smart infrastructure delivers the following essential benefits:
Fully managed IIoT solution that allows the user to easily and securely connect, manage, and ingest data from production lines/assets;
Real-time monitoring of critical parameters, line uptime-downtime analysis along with OEE monitoring;
Real-time process traceability of critical process parameters to establish machine learning/analytics capabilities;
One-stop solution to provide visibility across all plants distributed globally;
Products like Mind Connect Nano from Siemens offer easy connectivity and capturing of data.
WCI: What would be the impact on production efficiency and ROI with the implementation of Industry 4.0 technologies in the manufacturing process?
VK: Industry 4.0 could be capable of decreasing the production costs by 10–30 percent, logistic costs by 10–30 percent, and quality management costs by 10–20 percent. Simulation and AI methods provided an improved solution for the robot arm’s movement path that can save more than 5 percent of the time, which means a significant improvement in productivity. According to one study, if Indian companies adopt Industry 4.0 across functions such as manufacturing, supply chain, logistics, and procurement, they can enhance their operating profits by 40 percent at less than 10 percent of the planned capital expenditure.
Nowadays, with the dynamic market conditions, it is needed that the production processes shall be flexible, adaptable, and agile on a real-time basis. Thus, the manufacturing automation or smart factory gives several tangible and intangible benefits in long run. Automation or digitalisation brings benefits, e.g., with virtualisation process, the physical world can be linked virtually. IIoT-based software solutions can provide online and real-time dashboard of key business performance indicators with enhanced transparency. These tools also help in triggering the improvement actions for the shop floor machines. Alerts are sent online to all the stakeholders. The software captures and then evaluates critical data, which can affect quality and productivity. It gives information on overall equipment effectiveness, production, quality, and other contributing parameters using IIoT connectivity. Improved performance management can help companies boost their labour efficiency by 20 to 40 percent.
When a company invests in ‘Industry 4.0,’ it will change technological aspects, product development processes, marketing, logistics, manufacturing, post-sales services, high quality, flexible production, advanced planning, and controlling with relevant, real-time data. This helps in rapid reaction to changes in demand, stock level, and errors by mentioning other advantages and improvements in the enterprise.
Investment return is a key element in the business world. For this reason, when migrating or digitising a company, it must be done in a customised way and according to the model of each business. During this process, technological aspects should not be the only thing to focus on between the transformations to a new production model. It is very important to deepen in the benefits and efforts involved in migrating to a digitalised industry. In order to do it, the key process is to meticulously calculate the investment return in each aspect that is migrated, for example, it can be technological, training management, process improvement, automation, a reduction in rejections, etc.
These calculations for ROI must be performed in each area to know exactly the benefits that could be obtained when performing the migration. With that information, the company management will be able to decide how to perform with the migration to Industry 4.0 or how it should be adjusted to obtain a better investment return. It must be estimated over time, by drawing short, medium, and long-term plans.
WCI: What are the most common challenges/pitfalls when customers try to move to Industry 4.0 systems? How do you help the industry address these challenges?
VK: The Indian industry faces several challenges in its journey to adapt to Industry 4.0. Resistance to change, initial high cost, lack of data analytics skills within the system, lack of resources/knowledge, lack of desire or courage of top management to accept the innovations, data security risk, fear of job losses owing to robotics & automation, lack of leadership and vision are few concerns which need to be addressed. Political situation/dynamics, lack of coordination from management are some of the factors that need greater attention.
“We, at Supermac, provide innovative solutions not only for the equipment but also thrust a lot on the automation and exceeding the needs of the customer in terms of higher productivity and lesser operational cost.”
We, at Supermac, provide innovative solutions not only for the equipment but also thrust a lot on the automation and exceeding the needs of the customer in terms of higher productivity and lesser operational cost. We give quality products and offer new technologies and cost-effective solutions. Some of our products on IIoT are modelled on the affordable cost which customers are ready to invest in. Each of our products related to IIoT or automation is a result of constant and continuous efforts on R&D and innovation. We reach out to the customers and provide them the entire concept and work with their teams, hand in hand, to implement the IIoT solutions and ensure that the customers reap complete benefits using Industry 4.0 tools.
WCI: Cybersecurity is an increasingly important requirement for Industry 4.0. In what ways do you address it?
VK: Cybersecurity is very important to provide security/protection to the captured and stored information, either on a device or on the system. The system is capable of protecting the information from threats of computer attacks. Other than cybersecurity, it is important that the right methods are adapted that help the user to preserve the information either in a data centre or in the third party cloud system. Cybersecurity has three components to focus on: maintaining the confidentiality of data, data integrity, and availability of data at the right time.
Computer hardware threats can be a virus, Trojan, and malware, hacking, etc. and they can come from external devices or by potentially risky emails. In the same way, there are encrypted, boot, filed, or overwrite viruses, etc.
The most important thing in Industry 4.0 is to provide good and safety practices to factories, which can be reviewed as per relevant ISO standards. The industries must give importance to this because with the interconnection of devices due to the IoT incorporation, industrial plants have become more vulnerable. The increase in connected devices means more possibilities for cyber attacks.
Therefore, the IoT must be built on the basis of secure communications at each point of the manufacturing processes and it has to guarantee the inter-operability of security between facilities as basic elements of the supply value chain. Multiple levels of security are another option that must be implemented to protect from cyber attacks.
WCI: Could you tell us about recent & noteworthy projects accomplished by your company in India — specific to wire & cable companies?
VK: We have been able to cater to the needs of the US and other markets by providing high-speed THHN, building wire lines. Some of the prestigious orders we recently executed are for a US Defence and Aerospace company, and also from a multinational cable company in the US for which we are an approved supplier of customised products. Our products are acknowledged all over the globe as we offer high-speed fully automatic, best in quality, and cost-effective products with 24×7 online service support.
In the Indian markets, besides standard products, we have successfully executed high-end HV cable CCV lines. As of now, Supermac and Scholz (German partner) CCV lines are operating with a large number of customers in India. We have a few more orders in hand which are under execution. Customers have gradually understood that low-cost Chinese equipment does not last long and they have ordered us to replace CCV lines from China with Supermac and Scholz Germany equipment which were executed successfully.
We have recently supplied one high-speed automotive line to a multinational automotive company. With the advancement of the 5G network and in view of the future demands of fibre cables for implementation of 5G technologies, we have received big equipment orders from Europe and the US. These orders are under execution.
WCI: Due to COVID resultant lockdowns, the wire & cable industry recently shifted its focus on automation & remote commissioning — how does your solution simplify their operations?
VK: Supermac Industries was one of the first companies in reaching out to the industry amid the COVID pandemic by focusing on adopting new innovative ways of working and moving on with advanced automation and new technologies with an edge over the competition. It has broken the myth that the equipment can only be commissioned by the supplier’s engineer visit to customer site and charging the equipment at the site. Supermac remotely commissioned equipment online. The company’s first equipment – an optical fibre rewinding line was commissioned in Texas, USA during the lockdown phase. This was followed by a successful charging of a sheathing line to a prestigious customer in India and a high-speed insulation line in Bangladesh in the lockdown phase. The Supermac team could upload all drives software etc. working from remote. All this equipment was commissioned with online support by their engineers and technical support cell to conclude the successful start-up of the equipment. This has now become a routine for our teams and more and more online commissioning is being asked by customers.
WCI: What are your short-term and long-term plans — specific to the wire & cable industry? What is the future of Industry 4.0 – smart manufacturing, and automation in the Indian wire & cable industry?
VK: Our short-term plans are to expand our customer base in untapped markets by offering fully automated, high-speed lines with affordable IoT solutions as an integral part of the supply. We are passionate and bullish to offer IIoT as a standard product feature of our equipment in near future. We are fully geared up to offering differentiated products and solutions in new upcoming areas like high-speed FTTH optical fibre line which is a masterpiece of Supermac product portfolio. The line is equipped with very high precision tension control devices, which run in a completely closed-loop system. The special design extruder offers the perfect extrusion and provides the online diameter control, capacitance monitoring system. There are various combinations e.g. tandem, co-extrusion, or single extrusion, with the incorporation of many types of fillers, yarns, and online corrugation facilities.
“The future of Industry 4.0 implementation in the wire and cable industry is an excellent opportunity to sink in with ‘Make in India’ initiative and realise the full potential of Indian manufacturing capabilities and thereby adapting to this change.”
Supermac offers state-of-the-art high-speed tandem lines for data cable manufacturing. The tandem extrusion machine for LAN Cables intakes the solid copper and draws and anneals it online before putting it through the extrusion process. The special design extruder and crosshead give the high concentricity. The line has an online diameter control, capacitance monitoring system on the wire. The line is equipped with high-speed dual take-up for continuous production.
To meet FEP/PTFE cable requirements for military applications, aerospace and aircraft equipment, OEM and nuclear power products, Supermac offers specially designed high-speed extrusion lines for FEP/PTFE.
In the long term, we are actively working for our next project on a model to offer customers – plug and switch service on the equipment at their sites without sending any commissioning engineers. This will be possible by doing all online trials at our premises before sending them to customers.
Post-COVID customers are demanding more and more such features like online negotiations for equipment procurement and commissioning support for the equipment they order. Supermac is fully capable of meeting newer requirements and needs of the customers giving us our strong commitment to meet customer needs.
The future of Industry 4.0 implementation in the wire and cable industry is an excellent opportunity to sink in with ‘Make in India’ initiative and realise the full potential of Indian manufacturing capabilities and thereby adapting to this change.
Overall, the widespread adoption of Industry 4.0 would require the collaborative efforts of wire and cable industry leaders and related associations. The Indian industry and associations can work closely with the government and make short and long-term plans in the adoption of Industry 4.0 in the wire and cable segment and expand its growth.