SIKORA has launched X-RAY 8000 ADVANCED for faster measurement and efficient control of CV lines. This High Speed technology (HST) system is tailored to the requirements of Industry 4.0 and is an advanced alternative to the successful and established X-RAY 8000 NXT.
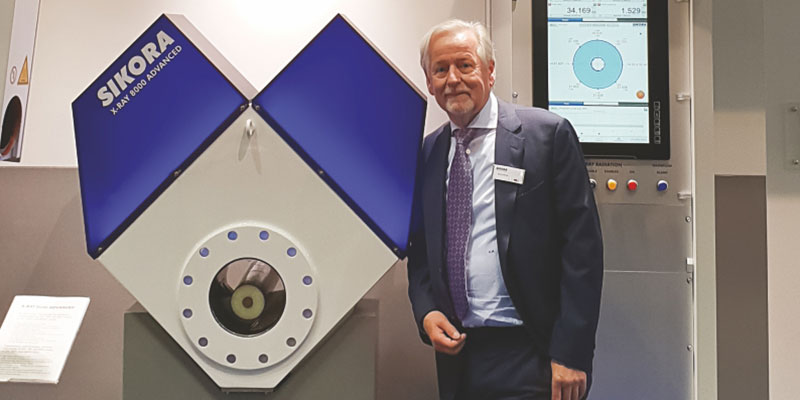
WCI recently conducted an interview with Mr. Harry Prunk, Executive Board, SIKORA AG. Mr. Prunk shared the latest developments of the company and also highlighted his perception of trends, challenges, opportunities, and area of improvisation in the Indian wire and cable India market. Excerpts:
Wire & Cable India: First, tell us something about your newly launched RAY 8000 ADVANCED. How is it different from your current innovative X-RAY 8000 NXT? Highlight some of its novel features.
Harry Prunk: With the X-RAY 8000 ADVANCED, SIKORA has launched a system with state-of-the-art High Speed Technology (HST) that is tailored to the requirements of Industry 4.0 in regards to fast provision of comprehensive data for information transparency. It represents an advanced alternative to the worldwide successful and established X-RAY 8000 NXT. The system – equipped with 16 measuring sensors – measures the diameter, wall thickness and eccentricity of MV, HV, and EHV cables in CV lines by a factor of up to 10 times faster than the X-RAY 8000 NXT, and thus, is predestined for an efficient control.
Interesting are the advantages resulting from the centering as each change of the centering screws is immediately registered and visualized. The four times greater number of measuring points, compared to the NXT system, simultaneously leads to a measurement almost without delay and an immediate control. Both factors optimize the process and ensure the highest quality of the cable, at maximum material and cost savings.
The High Speed Technology (HST) is the latest innovation from SIKORA. The focus is on efficiency enhancement due to a fast centering and an automatic control of the product parameters. The basis for this is quick and reliable measuring values with the HST. For a fast update of the scan data, the system optimizes the scanning time by automatically adapting the scan path to the cable diameter. Thus, the X-RAY 8000 ADVANCED significantly contributes to quality assurance and process optimization in CV lines.
WCI: Are there further additions to your already comprehensive line of technology? Also, tell us about the other development on the product side if any?
HP: We have added a new feature to our diameter measuring devices of the LASER Series 2000. Besides diameter measurement, the LASER 2010 T, LASER 2010 XY and LASER 2025 T are now equipped with high-speed lump detection. We thereby particularly meet the quality requirements of manufacturers of smaller product diameters as they are common for communication, automotive, and installation wires and cables. The measuring devices are usually installed at the end of the production line for final quality control. Thus, SIKORA offers a two-in-one-system, which leads to a reduction in investment costs and leaves more space in the production line as only one gauge head has to be installed.
We have also launched an intelligent device for the plastics industry at the wire that inspects and analyses plastic material that is, for example, used for the cable insulation. The PURITY CONCEPT V combines the advantages of an optical light table with an automatic offline material control. The system moves material samples on a tray through the inspection area. Within seconds the material is automatically inspected by a color camera and contaminated material is highlighted by a projector. By evaluating the image recordings, contamination on the surface of transparent, diffuse and colored material is automatically detected, visualized, and evaluated. A clear allocation of contamination and follow-up inspection is possible at any time. That means customers receive a system that is more precise, more reproducible and more reliable than human, eye, and manual light table and therefore significantly contributes to quality control and process optimization.
WCI: How was the experience at the exhibition ‘wire 2018’?
HP: The wire and cable market is one of our core markets. Therefore, the wire exhibition is the most important trade fair for us as well as for the wire and cable industry worldwide. This year the show was again a great success. We met many customers and friends and discussed our technologies and trends in the industry. Compared to 2016 we welcomed 7 percent more visitors to our booth, which underlines the strong interest in SIKORA’s future oriented technological solutions.
What we see from the show is that India is further on the advance in the area of optical fiber. The focus is on mobile communications of the 5th generation, which leads to data rates of 10 gigabits per second, that corresponds to a real time network. To achieve these high data rates, India is investing in new towers and also going for modernization in the existing drawing towers. SIKORA has been active in the area of optical fibers for 18 years and has established a discrete business unit for this application. Hence, we offer a comprehensive device portfolio for online quality control of optical fibers in the drawing tower that we also presented at the show. A drawing tower with devices for measuring the different optical fiber parameters was a visitor attraction at our booth.
This year, wire Düsseldorf was far special for us. This is because for the very first time SIKORA was also present with a booth at the simultaneously running Tube exhibition. Here we presented the operator’s advantages that result from using SIKORA measuring systems, with proven techno-logies to the metal tube and pipe market.
WCI: SIKORA’s customer communication, besides being leader in communication, is one of the benchmark in the technology industry. What practices, methods, and principles have made your kind of smooth company-client interface?
HP: The key to establishing customer relation is communication. All sources of communication have their merit, but essential is the face to face conversation. It is for that reason that, already 27 years ago, SIKORA had its first subsidiaries. The SIKORA team in the subsidiaries has an understanding of the processes of the customers, their requirements, and the solutions SIKORA can provide. Further, these people speak the native language of the customer and their aim is customer satisfaction. 10 out of 14 offices also provide service. The way we communicate with customers is decisive to build up a trustful long-term partnership. We communicate frequently and openly about different topics via various channels with our customers such as our customer magazine ‘EXTRA’, e-mailings to trade fairs, advertisements in trade magazines, social media like Twitter, conferences and shows, etc. We introduce and explain our products and keep our customers informed about market trends, how they can improve their processes and save costs by using our technology.
WCI: Give us your perception of trends, challenges, opportunities, and area of improvisation in the Indian wire and cable India market.
HP: In 2004, we founded SIKORA’s office in India. At that time, we could not have imagined the business would develop in that way. Years ago, SIKORA’s measuring and control technology were predominantly used for the energy cable and building wires industries. Today, also the automotive and optical fiber markets are strong and there is an increase in the quality demands. In addition to wire and cable, we offer measuring, control, inspection, analysis and sorting devices for the business units hose and tube, sheet, metal and plastics. These systems have as well gained a high level of acceptance in India. Just ten years ago, the challenge was to find acceptance in the Indian market for high-technology that is a little bit more expensive than the standard. Today, it is understood that high-tech is not available for a low-cost price.
SIKORA’s strengths, in particular, include professional sales support and full local service. This is characterized by innovative technology, high quality, and customer focus. With our international offices, we are available for our customers at any time all over the world independent from time or lingual or cultural diversity.
The development in India is also reflected by our office that has grown from a one-man office to two offices in New Delhi and Mumbai with presently 7 employees. Due to SIKORA’s diversification strategy in the different markets and the increasing product portfolio that we offer, our office in India will also continue to grow in the future.