Shakun Polymers is a leading manufacturer of compounds for the wire and cable market in the Indian subcontinent, the Middle East, South East Asia, and Africa. Its products in both domestic and international markets are established with a diversified customer portfolio. It says that its long-standing experience in manufacturing specialty compounds has resulted in the ability to customize products. The company works towards applications across a wide spectrum of the wire and cable industry such as power cables, building wires, telecommunication and fibre optic cables, instrumentation cables, and photovoltaic cables. “We expect the demand for solar cable compounds to grow as many new cable manufacturers are entering this space and building their own niche,” Mr. Abhinav Bansal, Vice President – Growth Initiatives shares with Wire & Cable India in an interaction.
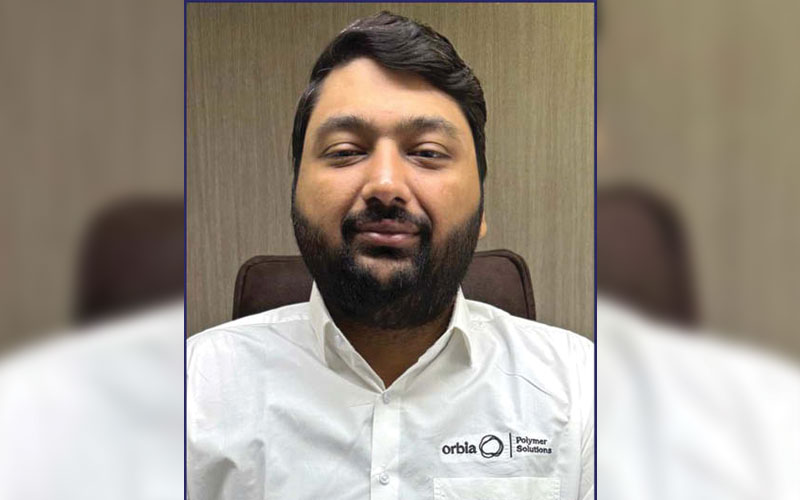
Wire & Cable India: India has embarked on a journey to achieve an ambitious 500 GW renewable energy installation. How has this impacted the demand for your solar cable compounds?
Abhinav Bansal: India’s installed non-fossil fuel capacity has increased 4x in the last decade and stands at more than 201.75 GW (including large hydro and nuclear), or about 40-45% of the country’s total capacity in the current year. In 2022, India saw the highest year-on-year growth in renewable energy additions, at 10%. The installed solar energy capacity has increased by 30 times in the last nine years and stands at 84 GW as of May 2024.
The announcement of a national policy in 2018 aimed to promote an extensive grid-connected wind-solar PV hybrid system for efficient use of transmission infrastructure and land. A way to address the intermittency challenge of one renewable power source is to combine solar and wind, achieving better grid stability. It allows for flexibility in the share of wind and solar components in the hybrid project, however, one resource’s capacity must be at least 25% of the rated power capacity of other resources.
We expect the demand for solar cable compounds to grow as many new cable manufacturers are entering this space and building their own niche. Specifically related to our solar cable compound sales, we have seen growth of 2x in terms of volumes and customer base. Currently, the majority of cable manufacturers are moving towards the capacity expansion phase, increasing their product portfolio and offerings.
WCI: What kind of solar cable compounds do you supply? What properties make them unique?
AB: At Shakun, we currently offer solutions for two distinct solar cable compound technologies: the first is a halogen-free, cross-linkable material that facilitates crosslinking through moisture, while the other is also a halogen-free flame retardant, designed specifically for electron beam applications, which customers with electron beam accelerators can produce.
The BS EN 50618, IEC 62930, and TUV standards are followed by our HFFR-based solar compounds. These standards are used in both of the technologies listed above. Solar cables are designed to operate in harsh environmental conditions such as higher temperatures, and continuous UV and ozone radiation exposure. They also need to meet the flexibility, low flammability, and low halogen acid gas requirements. According to the BS EN specification, we conduct thermal endurance tests to ensure the material meets the higher operating temperature for 20,000 hours. Also, we evaluate the material for the cable’s lifecycle and determine its ability to provide service for over 20 years. At Shakun, we have a pilot cable line to test our products, understand the challenges our customers face, and have troubleshooting solutions readily available. We are one of the few cable compounders who have a BS EN and TUV certificate for our solar compounds.
Watch: RR Kabel | Solar Cables | Solar Plant | Renewable Energy
WCI: Apart from solar cable compounds, what other compounds do you cater to?
AB: At Shakun, we offer various brand categories, which include the following: ECOTEK: halogen-free flame retardant compounds (thermoplastic and thermoset). We have solutions for power cables, optical fibre cables, off-shore cables, building wire, and FS cables. ESCONTEK-semi conductive compounds (thermoplastic and thermoset) Medium Voltage (MV), High Voltage (HV), and Extra High Voltage (EHV) power cables use our ESCONTEK solutions. We offer FRTEK-Flame Retardant/PPVC Compounds, VINYLTEK-TPR/PPVC Compounds, and PE SHEATHING-black polyethylene compounds. For low-temperature applications, we offer some specialty PVC compounds. We also offer Compounds for Overhead Medium Voltage Covered Conductors (MVCC), Semicon and Anti-tracking materials.
We also personalize and customize compounding solutions for our customers, depending on the severity of their application. We have also participated in joint development programs with customers and developed compounds for a market they anticipate will grow.
WCI: What technical capabilities in your manufacturing setup have made it possible for you to stand out in the competition?
AB: Shakun has been in the compounding business for more than three decades and is a relevant player in this market. Our value systems based on ethics and safety compliance have led us to this path. Additional strategies we employ to differentiate ourselves from the competition include innovation and automation.
Innovation is the key to unlocking growth to the next level and providing a competitive edge over our peers. We have many functions in the manufacturing industry; innovation can be product, process, or any specific area of expertise.
Automation helps in achieving better product quality and process checks. With innovative technologies in the manufacturing setup, companies can improve the quality of their products as there is no human intervention, which helps in saving labour costs. We can apply the latest manufacturing technologies, such as AI, IOT, and some machine learning tools, to the process of designing, producing, and testing goods.
WCI: What mechanisms do you have in place to ensure the quality of the compounds you cater to?
AB: We implement control measures at various stages, from raw material selection to finished goods. We rigorously test our raw materials and fully automate our compounding machines to eliminate any variations between production lots.
Our in-process and finished goods testing procedures further ensure the quality of our compounds. As an ISO-certified company, we follow standard operating procedures in operations and documentation for quality control. Additionally, our fully equipped lab and R&D facility ensure that only the highest-standard products reach our customers.
We are expanding our semicon production capacities, with our newly installed fully automated world-class Semicon compounding facility, from 10,000 metric tons to 30,000 metric tons. Our mission is to have a single compounding complex manufacturing 100,000 tons of compounds with state-of-the-art manufacturing equipment.
WCI: What growth figure are you staring at, and what changes do you foresee in the market?
AB: Currently we are expanding our semicon production capacities, with our newly installed fully automated world-class semicon compounding facility, from 10,000 metric tons to 30,000 metric tons. We will have the capacity available in Q2 2024; we expect to grow at 12-15% CAGR. Our mission is to have a single compounding complex manufacturing 100,000 tons of compounds with state-of-the-art manufacturing equipment.
For our solar cable compounds, we see strong demand coming from the Middle East/North Africa (MENA), South East Asia (SEA), India, Turkey and EU compared to last year, as we have solutions for moisture and beam curing. MENA, Turkey and EU majorly want solutions for moisture cure and in India and some parts of SEA we see demand for Electron beam type of solutions. Now the market is moving towards PV solar water-resistant adhering to AD 8 in particular for floating solar panels and for continuous wet condition requirement.
In order to enhance the performance of their offerings and the design of their products in a changing market, solar cable manufacturers are increasingly investing in their research and development initiatives. Cable companies increasingly recognize the significance of utilizing high-quality equipment and production facilities to ensure the unparalleled quality of their products, thereby optimizing their investments.
As a result, a growing number of organizations are investing in the acquisition of advanced equipment and raw materials, as well as the training of skilled labour to operate state-of-the-art machinery. Furthermore, solar cable manufacturers are enthusiastic about establishing the most advanced laboratories and testing facilities to guarantee that all of their products adhere to internationally recognized safety and performance standards.
Also Read: Borouge Eyes Asia Growth with XLPE Expansion
WCI: What are some of the major challenges you often face, and how do you plan to overcome them?
AB: We are part of an industry where we face challenges every day, and those challenges help us in giving direction and an opportunity to grow. As compound manufacturers we face challenges in terms of protecting the intellectual property of our products from substandard products available in the market which are cost-effective but not application-effective, and customers investing in compounds manufacturing and backward integration to save costs. Some of the challenges mentioned above are similar concerns of our peers as well. In order to address these challenges, we have adopted a few strategies.
To protect IP of our products, we have a masking system through robust ERP in place where traceability and tracking is accessed by the R&D and product development team. This system provides access limited to product owners for a specific development at a given time.
Cost-effective compounds in some cable applications, like bedding and inner sheath, can work but the majority of cable designs developed by cable manufacturers need performance-based compounding solutions. Our approach with customers is first to understand their specifications and the balance of properties needed. We offer customer fit-for-purpose solutions which does not add cost and help in adding value to their final product. Our approach has always been to look in the customer’s interest and provide solutions.