Leading polymer solution provider SACO AEI Polymers recently entered joint venture with Bihani Group to form SACO AEI Bihani Polymers Pvt. Ltd. The JV aims to create one of the largest HFFR / ZHFR manufacturing facilities in the world and expects to come up with two greenfield projects in the coming years. The Wire and Cable India team recently interviewed Mr. Sushil Bihani, Chairman, and Jaideep Bihani, Managing Director, Bihani Group, Mr. Luca Saggese, CEO, and Mr. Claudio Massimo Galli, Head of International Sales, SACO AEI Polymers to know more about their plans.
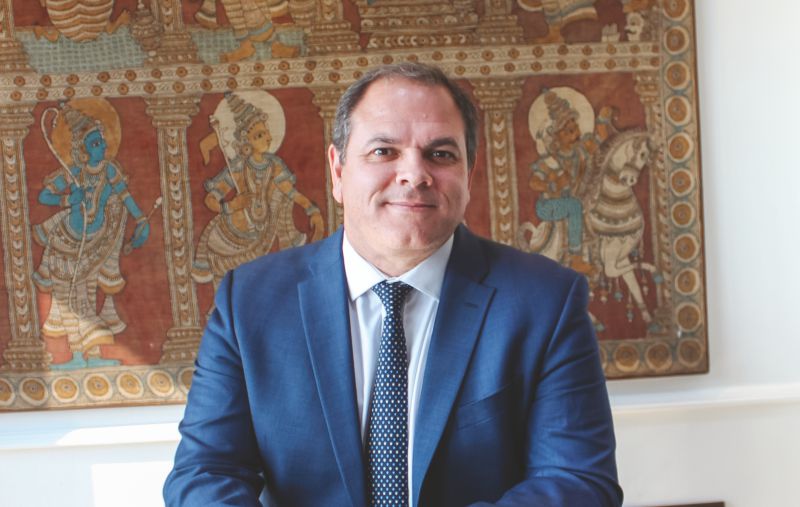
Wire & Cable India: Could you give us a glimpse of SACO AEI Polymers along with its product line and applications?
Luca Saggese: SACO AEI Polymers (Company) has developed expertise in reactive extrusion and flame retardant technologies and is today a premier manufacturer of grafted resins, masterbatches, compounds and additives for sale across all six continents. Headquartered in Sheboygan, Wisconsin, the Company has three manufacturing sites located in Sheboygan, Wisconsin, Aurora, Ohio, and Sandwich, England. Focus on the markets it serves is brought forward via its six business units, Wire & Cable USMCA, Pipe & Emerging, Custom Solutions, Substrates, Additives, and International. Over time this has allowed the Company to reach leadership status in Moisture Cross-Linkable XLPE compounds used for UL/CSA rated Low Voltage wire & cable insulations, and for NSF rated Pressure Pipes.
The Company’s role in this value chain continues to be vital as its customers increasingly require reliable suppliers with quality products, in-depth application and regulatory knowledge, and the ability to quickly bring solutions to the market. The Company has developed solid long-term relationships with a well-recognized and diverse customer base who rely on the high quality product that is supported technically and delivered under short lead time (often same day shipping) conditions.
The manufactured product lines which are of interest by the Wire & Cable market include a variety of silane grafted cross-linkable polyethylenes (“XLPE”) resins based on EPR, LLDPE and HDPE paired with application specific Catalyst Masterbatches (Non-FR, Halogenated FR and Halogen-Free FR) and, a complete range of thermoplastic jacketing compounds ranging from HFFR, CPEs and TPUs. It’s reactive extrusion capabilities have allowed expansion into Maleic-Anhydride grafted additives for impact modification of Nylons and Polyesters as well as Coupling Agents for WPC, PE and PP compounds. These additives are relevant for companies that have a focus on in-house compounding.
“The joint venture would be a key strategic asset to both SACO AEI and the Bihani Group. SACO AEI Polymers has been a pioneer in cross-linking and grafting methods.”
WCI: Can you please elaborate on your manufacturing facilities and the capabilities you have globally?
LS: Headquartered in Sheboygan, Wisconsin, the Company has three manufacturing sites located in Sheboygan, Wisconsin; Aurora, Ohio; and Sandwich, England. Each site is equipped with state of the art compounding and laboratory equipment. We pride ourselves on the ability to produce our products at multiple locations, essentially de-risking a customer’s supply chain. In addition, we continue to expand our warehousing capabilities, which enable SACO to deliver 90% of our portfolio from stock. SACO supports its customers with a global technical team, which is equipped to support customers through product launches, process optimization, regulatory questions and application development. We are accessible via phone, video call, email, social media and website, every day of the year, globally.
WCI: As SACO AEI Polymers enters in JV with Bihani; could you please brief us on this strategic partnership? What kind of synergies do you foresee after the incorporation of SACO AEI Bihani Polymers Pvt. Ltd.?
Sushil Bihani: The joint venture is not based on a relationship that is working on experimentation; rather both parties have been in the Indian market for over a decade. With the help of SACO AEI, the Bihani Group has been able to bring halogen-free compounds to India and its neighboring countries. Today, Bihani’s commercial coverage extends to over 20 countries. This reach, combined with SACO’s global footprint, and detailed knowledge of customer requirements, gives SACO AEI Bihani (SAB) a real jump in servicing the customers here in India. We expect serious work on the enhancement of formulations to meet the changing customer requirements, therefore we have equipped the JV accordingly.
SACO AEI is known for its quality, reliability, innovation and longevity in the Wire & Cable industry. SAB has adopted these best practices and applied the best technology in the state-of-art machines that are being deployed. SAB plans to ‘Make in India, Make for India and Make for the World’.
SACO AEI Polymers has been churning out its product for over two decades now. Some of these products are now made in India and sold to select customers. With the incorporation of SACO AEI Bihani, the AEI Compounds business would shift to SAB making it a revenue positive Company from the first year. It is a matter of great pride that we are in a position to invest in state-of-the-art technologies in India. We are expecting that in the next two-three quarters, we would be running the additional capacities in our current site at Bhiwadi. We are expecting two greenfield projects in the next 18 to 24 months.
Jaideep Bihani: The joint venture would be a key strategic asset to both SACO AEI and the Bihani Group. SACO AEI Polymers has been a pioneer in cross-linking and grafting methods. In India, we are trying to create this competitive edge in thermosets as well as thermoplastics. We would be integrating these technologies, which have been there for over half a century, and products that have been in service for over three to four decades with standardization, good customer response, and reliability over the period of time. We have taken the core competencies of SACO AEI and developed many grades that were specifically suitable for the Indian market and could run on the localized machinery and equipment. Many of our thermoplastic grades have been flagship products.
Luca Saggese: We have had a relationship with the Bihani group for almost a decade. They became our partners when we wanted to foray into India and the neighboring countries. That relationship blossomed over the years and created an opportunity for this joint venture, where we plan to integrate our technology and R&D efforts to develop and deliver the next-generation Wire & Cable products. We are starting with halogen-free thermoplastics in the market, and then we’re going to move into the thermoset segment. Our manufacturing teams plan to work together to develop improved and enhanced products specifically for the Indian and neighboring markets. I am very optimistic about this collaboration.
“We are expecting two greenfield projects in the next 18 to 24 months.”
Claudio Massimo Galli: The strategy behind this joint venture is not just to sell our product in India, but also to understand our customers in a better way. We are pretty known in the Indian market, but establishing our brand here can give us an opportunity to know what our customers would like to have in the future and develop a product accordingly with our knowledge and experience.
WCI: What are your views on the Indian wire and cable market?
LS: I find a tremendous opportunity for our business in India. The customers here are technically sound. They have invested in state-of-the-art equipment and laboratories for testing their own products as well as the compounds. They have a very global view of how they can grow their businesses. And I think it’s their global view that makes us an ideal partner for wire and cable customers in India. The Indian government has launched various schemes to boost infrastructure, internet connectivity, electricity supply, and clean energy transition and we provide solutions in all these segments.
JB: Wire & cable acts as a nervous system of any structure. Talking about the kind of growth the world is looking at, in a recessionary phase, ours is the only country that is extremely promising. When it comes to specific products such as halogen-free, these products have been there in service for over 20 to 30 years. As new building construction technologies are coming in, there is more emphasis on fire safety. Halogen-free is the product, which is the need of the hour; however, halogen-free has its own set of issues. And these issues can be addressed only through the very specified and specific manufacturing process. We have understood this over time. We are going to offer products consistently over a period of long time. The fire safety regulations have become very tight. HFFR has a tendency not to emit smoke. The application of such products is only going to help contribute to public safety. Over the period of time, we hope to see the shift of building wire from PVC to HFFR.
Also Read: Wire & Cable India Emagazine Nov-Dec Issue 2022
WCI: Where do you see SAB five years down the line?
LS: It is important to us that our customers trust us not only with their current orders but also with their future needs. Within the next five years, SAB will be a world class manufacturing site, producing state of the art products, with a customer centric and quick go to market product development team. We plan to launch a center of excellence in India to develop the next-gen halogen-free compounds. We expect to be a customer’s preferred supplier and we will continue to invest to make sure it is so.
“SAB will be a world class manufacturing site, producing state of the art products, with a customer centric and quick go to market product development team.”
WCI: What are the key strengths of the company that helps you stay ahead of your competitors?
LS: We have the ability to develop high-quality products that meet the new standards using a combination of unique materials and compounding know-how. When customers see an opportunity, they want to get the solution quickly; we give our customers the advantage to be the first entrant in new markets. In addition to that, our service model relies on having the right product in inventory at all times. In the last few years, the pandemic has really tested this model with supply shortages and demand spikes. Stocking products locally, for quick delivery has been and will remain a key advantage.
WCI: What future do you foresee for cross-linking polymers?
LS: It is important to understand why cross-linked products are needed in the wire & cable sector. The desire to drive more energy through the metal conductors generates heats. This heat typically melts standard thermoplastic insulation, and that’s the primary reason why cross-linked polymers are important. They don’t melt off the wire and keep everyone safe. Further, cross-linked polymers are much tougher than standard thermoplastics. This enhanced toughness and chemical resistance make cross-linked products the right solution for environments where safety is a priority. The market for these products has been growing steadily, as the electricity is being demanded in every corner of the world. Therefore, I expect continued growth for decades to come.