Quality control is a process by which entities review the quality of all factors involved in production to ensure that products meet all the quality specifications and requirements. In the wire and cable industry, a quality issue, among other things, is also a safety issue. Cables need to comply with a growing list of requirements to protect consumers and their property against a range of issues, from electric shock and burns to electric arcing and fire propagation. There are a range of machines and tools to check whether a product is standard as per specifications and free from all the defects.
Wire & Cable India recently had detailed intercourse with some of the quality control machines and tools provider to wire and cable industry where they elaborated on the significance and process of quality control.
SIKORA AG: Importance of Quality Control
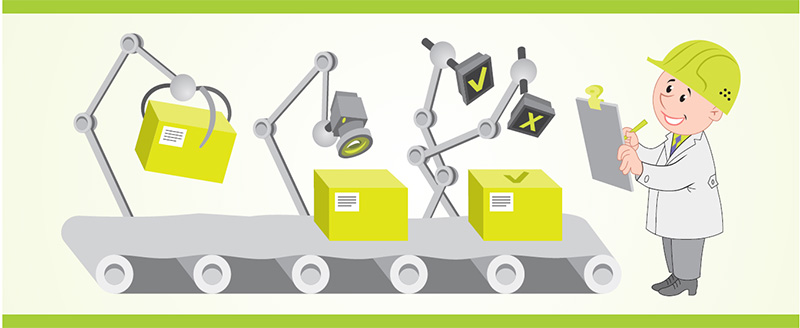
SIKORA AG was founded in 1973 and celebrated its 40th anniversary in 2013. Today, SIKORA is a leading global manufacturer and supplier of measuring and control technology for the wire and cable, hose and tube as well as optical fiber and plastic industry. Here are the excerpts of exchange with Harry Prunk, CEO, SIKORA AG:
Wire & Cable India: What are your offerings for the wire and cable industry in terms of quality control equipment/services?
Harry Prunk: SIKORA’s offering for quality control in the wire and cable industry touches all sorts of applications, whether it is data communication, including the equipment for the measurement of optical fibers and all of the devices needed for data transmission wire copper cable, or equipment for the automotive sector and for the medium, high and extra voltage cable.
Concerning the automotive segment, SIKORA’s offerings for quality control go even beyond wire and cable and include measuring and control equipment as well as equipment that is used for hoses like brake fluid, gasoline hoses and turbochargers.
Quality control very often starts with diameter measurement, includes capacitance measurement and SRL prediction specifically for the data cable, continues with eccentricity measurement in all cable segments and finishes with cable surface inspection and the checking for defects in the insulation by spark testing. SIKORA’s latest development for quality control focuses on the detection of contaminated pellets in XLPE material which is used for medium, high and extra voltage cables.
WCI: Quality control (QC) intends to ensure that a manufactured product or performed service adheres to a defined set of quality criteria or meets the requirements of the client or customer. How far have you been successful in that and how do you ensure it?
HP: 30 years ago, when the line speed at the drawing of fiber had been relatively slow, it was possible to check the diameter of a cable by a tape, or to perform offline measurement by a caliper. Today’s requirements go far beyond, thus, online measurement is necessary for quality control and measuring values are not only used for monitoring, but they are directly fed back into the control loop.
The main reason why SIKORA has been successful over the past four decades in the development and supply of devices that are used for quality control today is based on a very close customer relation. One needs to listen very carefully to customer demands and needs to establish more than just a customer – supplier relation, but a partnership. It is essential that all equipment, which is used in the online process for quality control, offer reliability over the years, and SIKORA’s internationally established network of service plays an important role concerning maintenance and calibration, as it is required particularly by the ISO standards.
WCI: How do you go about educating your customers about importance of quality control? Do they really understand it? Elaborate on some challenges therein (in convincing your customers).
HP: Customers understand quite well the importance of quality control, as without an online quality control, they have less chance to survive in this competitive business. A permanent online quality control does not only reduce the amount of scrap that is produced, but it increases as well the productivity and, therefore, reduces costs at the end. Many end users of the cable specify quite much in detail their expectations towards their supplier, whereby an online control is typically one of the aspects.
Online eccentricity measurement is a typical example where customers are always surprised by the performance of the SIKORA equipment. Typically, devices take a number of readings in order to receive a good average. One may, however, cut the cable and find an eccentricity, because the eccentricity in the average might be correct. But at certain points where the cable is cut, the values may be out of tolerance. What it really needs is measuring equipment that provides single value accuracy. By using this equipment, it is possible to present all of the values in a form of a scatter plot (cloud diagram), which clearly visualizes the single measuring values taken on short intervals on the cable. Therefore, measurements can be taken immediately, scrap is avoided accordingly and satisfaction of the customer is assured.
Also interesting is a newly developed PREHEATER for wires, which is used in the data cable and automotive industry. While it was before quite usual to just control the power of a PREHEATER in order to heat the wire, a newly developed system now also allows to measure the temperature and to control the power exactly in that way that the demanded temperature at the surface of the wire is assured in order to guarantee a good adhesion of the insulation to the conductor.
WCI: Define some of the benefits that your customer can reap by using your quality control equipment/services?
HP: A number of benefits, such as a better process control and costs savings are the very typical first aspects when using online quality control. In this regards, it is very important to never stop investigating new challenges. With the PURITY SCANNER, which inspects online the raw material that is fed into the extruder for the manufacturing of high voltage cable and the ULTRATEMP 6000 to measure the melt temperature, SIKORA has just recently presented two products that are unique today and offer new possibilities far beyond of what was possible in the past.
SIKORA offers a special service to customers that want to modernize their entire plant in respect to quality control. Their plant is inspected by SIKORA experts and a quality control concept is created that includes a layout for all equipment required from wire drawing, insulation to sheathing, including a recommendation of the priorities. Together with the customer a plan will be worked out for the steps of the implementation of the measures and the financing.
Medek & Schörner: An Array of High Quality Marking Tools
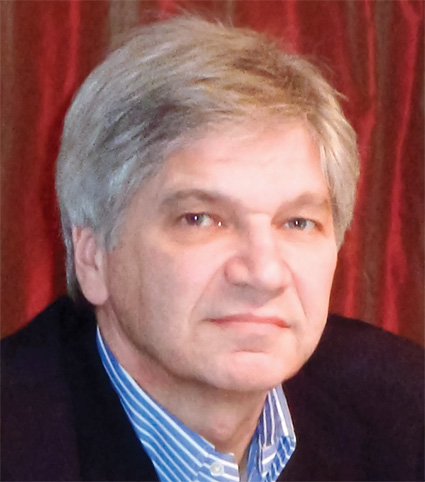
Medek & Schörner, established in 1929 by Josef Medek and Gustav Schörner as a mechanical engineering firm, has been specializing for more than fifty years in designing and building marking machines for continuously produced goods such as wires, cables, tubing and sections. The Medek & Schörner product range includes a wide variety of marking equipment from simple marking heads to fully automated high performance systems for use in advanced production lines. Here are the excerpts of exchange with Mr. Werner Lichtscheidl, Managing Director, Medek & Schoerner GmbH:
Wire & cable India: What are your offerings for the wire and cable industry in terms of quality control equipments/services?
Werner Lichtscheidl: For decades now, Medek & Schörner has been a world market leader in cable marking machines and optical fiber processing lines. As the leading manufacturer of cable marking machines, Medek & Schörner has developed the VST high-speed video monitoring system to continuously monitor the print quality of fast-running cable printing machines. The integrated software allows various evaluations of the print area displayed, e.g. alarm in the event of poor quality and/or missing text.
The big difference compared to similar print monitoring systems from competitors is that the VST system is suitable for really high speeds of up to 2,500 m/min and above. The system is therefore also predestined for use in high-speed optical fiber coating lines, e.g., for inspecting and adjusting the centricity of the fiber coating or for inspecting the imprint on fiber ribbons.
WCI: Quality control (QC) intends to ensure that a manufactured product or performed service adheres to a defined set of quality criteria or meets the requirements of the client or customer. How far have you been successful in that and how do you ensure it?
WL: The only company operating in this market segment of cable marking machines and optical fiber processing lines, Medek & Schörner covers virtually the entire spectrum of machines for marking cables and coating optical fibers.
Even when high-performance cable marking machines guarantee extremely high reliability, the printing process may be affected by factors such as natural wear of parts, broken components, wrongly adjusted printing ink viscosity, etc. This can result into bad print quality and/or missing text. Very often such errors are not detected by the operator immediately they occur, resulting in rejects. To overcome this snag only, as has already been mentioned, Medek & Schörner has developed the VST high-speed video monitoring system.
WCI: How do you go about educating your customers about importance of quality control? Do they really understand it? Elaborate on some challenges therein (in convincing your customers).
WL: When customers introduce such a system, they realize that it helps them improve the quality of their cable products with respect to printing, and to make considerable savings due to the elimination of rejects. However, for all that it is difficult to convince customers to invest in such a system even when you can prove that the cost of a print monitoring system will be amortized within a short period of time.
WCI: Define some of the benefits that your customer can reap by using your quality control equipments/services?
WL: Once again, the benefits of a print QC system are self-evident:
- Real-time print quality control
- Relieves the operator of monitoring print quality
- Allows more convenient adjustment of printer parameters
- Provides an alarm in the event of poor print quality and/or missing text
- Helps avoid costly rejects
LMI India: At Par With International Standards
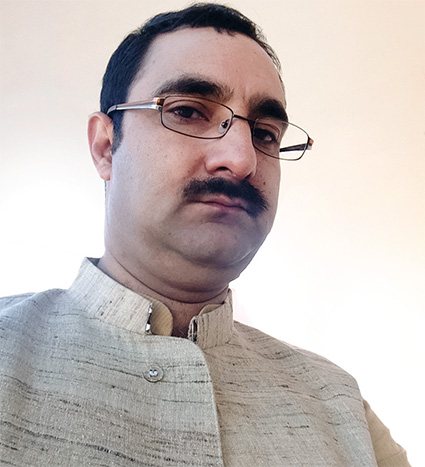
LMI India is a leading provider of sustainable solution and automation in the area of quality control/ improvement. With an experience of over decade, LMI India caters to a spectrum of industries viz. Extrusion, FMCG, Pharma, Automobile, Electrical & Electronics, Metal, Cable, Tube & Pipe, Food & Beverage, Printing, Logistics, Tyre, etc. Here are the excerpts of exchange with Mr. Mohan Pandit, CEO, LMI India:
Wire & cable India: What are your offerings for the wire and cable industry in terms of quality control equipments/services?
Mohan Pundit: LMI India has been in the forefront in the cable industry by offering various products for quality improvement supported by software/ hardware tools to quantify them.
Our non-contact LaserScan, online/ offline measurement and control system monitor and maintain critical parameters such as diameter, ovality, width, and wall thickness of cables. Our Scanlength is a compact standalone device to give the option of measuring length of the cable accurately down to the unit of millimeter, thus, saving on material costs in long run and avoid the embarrassment of short length delivery to an end user.
Every type of cable mandates printing of company name, length, specs, ratings, standards, etc. on the outer sheath or cable insulation. LMI India offers an end-to-end solution to this requirement with a renowned German technology that has qualified for “Gold” award at the international level.
Cable insulation slice profiler is a latest offer from the house of LMI India to their valuable customers. Traditional method using profile projector has difficulty and relies on expertise to cut and analyze a cable insulation cross-section. Our VPro overcomes this limitation and offers a easy and zoomable profile of single or multilayered cross-section of cable which is a boon for QC Lab technicians.
A good cable finish on a wooden drum, steel spool or disposable reel essentially is one in which unwinding is made easy without entanglement. To achieve this, LMI India offers a universally acclaimed traverse mechanism that is robust, has long life and requires very less maintenance. The uniform winding pattern from one end to another end of spool width and from layer above another layer is a visual delight at an affordable one time investment.
WCI: Quality control (QC) intends to ensure that a manufactured product or performed service adheres to a defined set of quality criteria or meets the requirements of the client or customer. How far have you been successful in that and how do you ensure it?
MP: Cables are used extensively in telecom, power transmission, defense, commercial, automotive, and home appliances and establish communication between various modern devices. We know that cable is not one of the discrete components or device whose failure does not matter to the overall function of complex systems. In contrast, cable by itself is used in a length ranging from few feet to several kilometers. Necessarily the cable so used must meet quality parameters throughout its length. LMI India knowing this importance offers a comprehensive tool to measure and quantify Statistical Process Control (SPC) of cable right from a wire draw till the final rewind and shipment.
Since the cable manufacturing processes are to some extent labor intensive, an element of doubt exists in factory manager’s mind whether his final product would be the one which meets all quality norms and regulations. LMI India through its innovative approach and practical offers has helped their clients overcome this doubt factor.
WCI: How do you go about educating your customers about importance of quality control? Do they really understand it? Elaborate on some challenges therein (in convincing your customers).
MP: Interestingly, in the cable industry, our business model requires interaction at various levels. Such as, say, an extruder operator, machinery maintenance personnel, quality supervisor, and at far extreme to the top level management of the company. Thus, on day-to-day basis, our sales and field support staff in LMI India play a constructive role of educating/ discussing process parameters and its adherence methods. In such interactions, we end up providing meaningful solutions that meet the production challenges and establish customer competitiveness in the market, thus we act as a consultant on such instances.
Eventually our products also get widely accepted in the industry to become a benchmarking tool.
WCI: Define some of the benefits that your customer can reap by using your quality control equipments/services?
MP: As we discussed in length, just a while ago, a cable manufacturer would vouch for all his shipped products to be in service for many years even in rugged field conditions. He would not wish to hear any rejections due to quality factor which may dent his company’s image in the market. They know the products and services from LMI India are at par with any international companies. They have kept us in business and we take pride in serving them to the best of our abilities.