On November 9, 2024, Mikrotek Machines, along with Zeller+Gmelin, Niehoff and Mikrotek Services hosted a prestigious wire symposium in Vadodara, Gujarat, bringing together industry leaders to explore cutting-edge solutions and operational efficiencies in drawing machines. Their collaborative effort highlighted how established organizations can optimize wire drawing plants to ensure efficiency and produce value-added products.
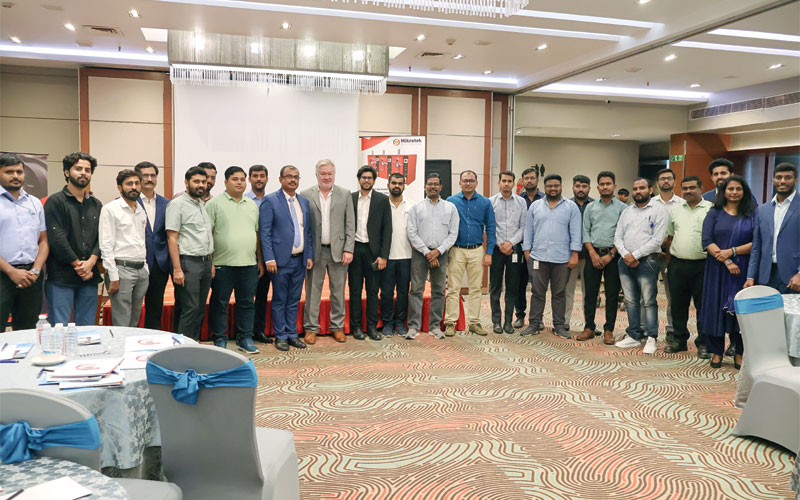
The event served as a dynamic platform for exchanging insights on innovative solutions, emphasizing advancements in technology, research and development, and testing methodologies aimed at upgrading wire and cable manufacturing technologies.
In the event, participants explored ways to maintain uninterrupted machine operations while achieving superior output quality. The symposium underscored Mikrotek’s commitment to fostering industry innovation and efficiency, paving the way for enhanced collaboration and progress across the wire and cable manufacturing sector.
Mr. Manjunath Ramakrishnappa, Sales Director at Mikrotek
Machines emphasizes Mikrotek’s commitment to quality and operational excellence, consistently delivering value-added products to its customers. He attributes the company’s success to its highly skilled workforce, capable of producing top-quality products within tight timeframes. He further shares Mikrotek’s vision to create user-friendly, and high-quality products, generate revenue for stakeholders, and enhance the standard of living for its employees.
During their presentation, he showcased a six-year growth record highlighting the company’s remarkable progress. Mr. Manjunath revealed that Mikrotek Machines began its journey in 1987 with a monthly production of 750 units. As of 2024, the company has scaled up to producing 30,000 units per month, reflecting significant growth and development. Currently, Mikrotek Machines has a presence in 40 countries, exporting 60% of its inventory. Looking ahead, the company plans to further expand its production capacity to 100,000 units per month by the end of 2025.
Further, Mr. Subbaiah M E, Manager, Mikrotek Machines highlights the key challenges in the wire and cable industry, focusing on operational inefficiencies and quality issues. He pressed on one major concern in the wire and cable sector, that is, wire breakage in drawing machines. He points out that the average rate of wire breakage is 0.3 breaks per turns which is significantly higher than international standards. Additionally, he mentions the machine inefficiency and lower capacity utilization in the industry which is typically around 60–70%, well below the global benchmark of 90%.
Other challenges include surface imperfections such as scratches and poor finishes, high operational costs, and material weight loss, all of which contribute to overall plant inefficiency and reduced productivity. Issues such as the generation of metallic particles, poor surface quality, and oversized bearings further compromise the performance and longevity of wires. Raw material quality and improper lubrication exacerbate these problems, while machine wear and misalignment lead to inconsistent output and increased maintenance costs.
To address these challenges, Subbaiah emphasizes the importance of using suitable lubricants compatible with the materials and processes involved. He also advocates for the implementation of effective filtration systems to eliminate contaminants, along with regular maintenance of equipment and dies. These measures are crucial for enhancing equipment performance, reducing downtime, and maximizing operational efficiency in the wire and cable sector.
Watch: Top Cable Companies in India
He further discusses the various types of dies available at Mikrotek Machines, highlighting the distinctions and comparative advantages of natural diamond dies, synthetic single-crystal diamond dies, and PCA dies. Each type offers unique benefits and limitations, tailored to specific applications within the industry. Additionally, he delves into the micro-extrusion process and the critical role of wire finishing in achieving optimal quality wires and cables, ensuring they meet the stringent requirements of modern applications.
Taking the discussion forward, Mr. Ravi Kumar, Technical Head, Neihoff of India along with Mr. Daniel Thomas, Managing Director, Niehoff of India underscores the importance of proper machine maintenance to ensure production efficiency. Mr. Ravi Kumar stresses that cleaning the machine is crucial, as excessive copper in dies and lubricant lines can negatively affect operations. He also highlights the need for correctly mounting annealing contact bands and mentions issues like brazing in tubes and pipes, which can cause splits and impact the quality of production.
Further caution is given regarding potential breakages in the annealer, which can diminish efficiency in wire and cable manufacturing. He emphasizes the importance of cleaning the filter paper in the ESC and the blower regularly, recommending a weekly schedule. Cleaning the heat exchanger is also vital to maintain optimal performance.
Regarding lubricants, Mr. Ravi advises using the correct grade of gear oil for machines. His company produces up to 20 grades of gear oil, along with 100 grades each of multiwire and intermediate oils. He recommends changing gear oil every 500 operating hours and replacing filters at the same interval, with an additional filter change at 1200 hours. Regular cleaning of filters every 300 hours is also essential. He warns against over-greasing, as it can damage the primer belt.
Mr. Ravi further discusses the sealing systems in machines, emphasizing the need to prevent lubricants from leaking into the gearbox. Regular checks of seal conditions are necessary to avoid such issues. He also advises opening machine doors periodically to release trapped air and improve ventilation.
Additionally, he highlights useful machine system upgrades, particularly focusing on magnetic locking mechanisms for enhanced efficiency.
Later in the symposium, Mr. Guido Schiller, Regional Sales Manager- Lubes at Zeller+Gmelin discussed their broad range of products, emphasizing both water-miscible and non-miscible options. They highlighted their expanding presence in India, not only in the wire and cable industry but also in sectors like punching, corrosion protection, and textiles. During the event, they introduced their lubrication series aimed at optimizing wire drawing production, with a focus on solutions for diverse environments.
Among the key products discussed was Multidraw CU MFE, a water-miscible drawing agent for copper wires, specifically designed for use on inline enameling machines in the intermediate and fine drawing range. Another standout product, Multidraw CU MF, is a water-miscible copper wire drawing agent that has become popular due to its exceptional lubricity and ability to maintain machine cleanliness. The company has developed products for countries having high-humidity and high-temperature regions, in contrast to the CU-GWZ which is predominantly used in European countries, where humidity levels are lower.
Mr. Guido also shared details about their water-miscible solutions for aluminum wire and greasing products, noting the unique challenges that come with water-miscible products.He emphasized that the bacterial and fungal growth can pose significant issues, and the quality of water, especially chloride content, is critical for ensuring effective anti-corrosion properties. For annealing processes, de-mineralized water is essential to achieve the desired results.
Another challenge lies in managing the emulsion level. If it is too low, foam problems can arise, leading to operational inefficiencies. To mitigate this, Mr. Guido recommends regularly testing concentrations with a refractometer to avoid wire breakage and corrosion. The pH level is also a critical factor; low concentration levels can lead to a drop in pH, creating an environment conducive to bacterial growth. Conversely, even with an optimal pH, bacterial contamination remains a potential risk.
Also Read: Wire & Cable India Emagazine Nov-Dec Issue 2024
To address these issues, Mr. Guido suggests incorporating biocides to combat microbial growth and using anti-foam agents to minimize foaming. These measures help ensure the reliability and longevity of their products, maintaining their reputation as a trusted solution provider for wire drawing and related applications.
Further, Ms. Mangala N, Techo Commercial Manager, Mikrotek Services explains that crossheads can be categorized into two segments: manual centering and fixed center. Fixed center crossheads are designed to ensure proper alignment once all parts are assembled. These crossheads provide uniform insulation, making them ideal for primary insulation applications. On the other hand, manual centering crossheads are used for larger sizes, ranging from 25-30 mm to 160-175 mm, and are primarily employed in secondary insulation processes, such as manufacturing large, long, and flat cables.
She also highlights the significance of distributors in their production process. These distributors facilitate uniform distribution of material to the faucet, creating a perfectly centered cable. The internal diagonal-polished surfaces of the distributors enable smooth plastic flow through the channels, ensuring even distribution within the faucet.
In addition to crossheads and distributors, Ms. Mangala discusses the company’s manufacturing of tips and dies, which come in various configurations such as round holes, flat holes, and flat-profile holes. These components are produced in two stages and hardened to a range of 45 to 50 HRC for durability. She also elaborates on velocity sections, which connect the extruder to the process. These sections efficiently convert straight flow into the 90-degree turn required to enter the crossheads. The company provides both main velocity sections and scale velocity sections, ensuring seamless and efficient material flow throughout the process.
All in all, the symposium showcased the power of collaboration and innovation in the wire drawing industry. By bringing together expertise from Mikrotek Machines, Zeller+Gmelin, Niehoff, and Mikrotek Services, the event emphasized the importance of leveraging advanced technologies and operational strategies to drive efficiency and deliver high-quality in the wire and cable sector.