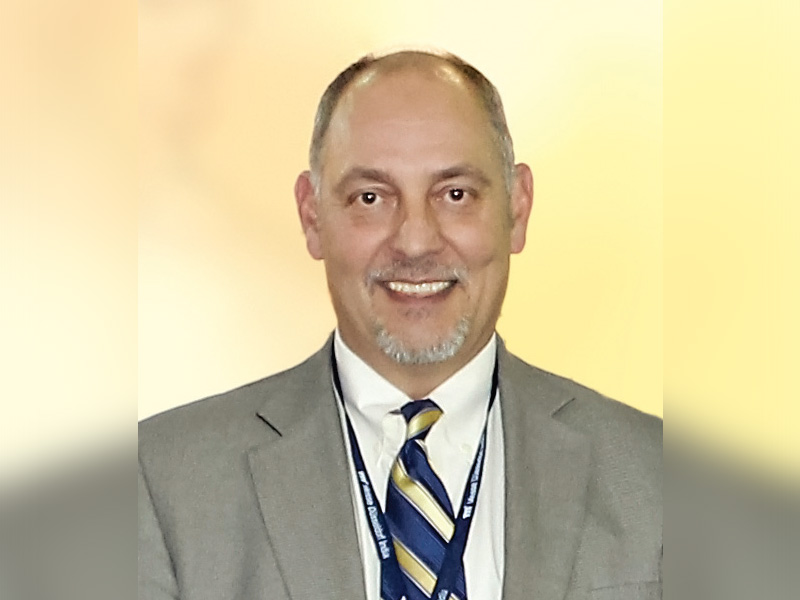
Founded in 1968, Paramount Die is one of the largest wire die manufacturers in the world servicing both the ferrous and non-ferrous wire industry. The company is well known for providing innovative products to the wire industry. According to the company, more than 70 percent of ferrous wire companies either utilize drawing inserts exclusively or incorporate them in a part of their production. In a brief exchange with Wire & Cable India, Mr. Al Kozlowski, Vice President at Paramount Die Company explains the fundamentals of the company and its plans for growth in India.
WCI: Kindly brief us about Paramount Die and its technology.
Al Kozlowski: Paramount Die is the world’s largest supplier of finished tungsten carbide wire drawing inserts, exporting more than 60 percent of our products to the world. Our mission is to provide the wire industry with the world’s most efficient and technologically advanced tooling for drawing wire. Paramount Die’s primary product line is the wire die insert which is available in a wide range of sizes for all wire drawing applications. By utilizing a wire drawing insert opposed to conventionally cased dies, wire drawers eliminate the permanent steel casing and reduce material and shipping costs. Paramount Die’s wire drawing inserts may be used in a basic die holder or in our ParaLoc™ pressure system in both direct and indirect water cooled options. The key to Paramount Die’s success can be found in our production process. Paramount Die manufactures several million wire drawing inserts annually and has the volume to justify the utilization of extremely proficient and highly consistent automated production equipment. We consistently produce high quality wire dies at a competitive price point.
WCI: Please explain the benefits customers can derive using Paramount’s dies.
AK: Paramount Die’s exchangeable carbide drawing inserts coupled with our ParaLoc™ pressure system have contributed greatly to increasing drawing speeds and improving productivity for customers throughout the globe. Our ParaLoc™ pressure system is designed to increase lubrication by enabling the lubricant to pressurize during the drawing process improving lubrication, increasing productivity, extending die life and enabling faster drawing speeds. Some customers have seen upwards of a 45 percent increase in drawing speeds by optimizing their wire drawing process with inserts and holders from Paramount Die.
WCI: Your experience with the Indian market?
AK: Historically, companies in India have had a tendency to recut dies locally, sometimes resulting in less than ideal internal die geometries and decreased productivity. Now that India is emerging as one of the fastest growing markets in the world we see many companies making investments in wire drawing machinery, tooling, technology, and various other process improvements. These investments are signs that Indian companies recognize and appreciate the need for newer technologies and more efficient methods of production. Paramount Die’s wire drawing systems support the country’s push for more sophisticated technologies.
WCI: What are the targets of Paramount Die for the next five years?
AK: For Paramount Die, India is an untapped market with huge potential. Over the past several years the leadership in India has made significant investments in infrastructure, education, and automotive all positioning the country for rapid growth and foreign investment. Paramount Die is committed to working with the indigenous companies to support the country’s expansion efforts over the next several years.
WCI: Can you highlight some of the challenges you are facing in the Indian market?
AK: From Paramount Die’s perspective, our biggest challenge will be educating the wire drawing companies in India about the importance of eliminating internal re-cutting or local refurbishment of dies. The present die manufacturing process being used by many wire drawers in India is outdated and results in lower productivity and increased die consumption. By working with Paramount Die, wire drawers in India can expect a consistent wire drawing insert made from the highest quality carbide.
WCI: Tell us about your take on R & D that you undertake keeping different markets in viewpoint?
AK: In today’s competitive landscape, it is imperative that companies remain informed and actively seek improved manufacturing methods. Paramount Die has a team of in-house R & D engineers dedicated to product development improvements. The engineering team at Paramount Die works closely with the sales and marketing team to incorporate our customers’ needs and requirements in to the development of wire drawing solutions that will solve our customers’ needs long term.
WCI: Any message to the Indian market from Paramount Die?
AK: The biggest take-away from this interview for the wire drawing market in India is that when combined with modern drawing machinery and optimal drawing lubricant chemistries, Paramount Die’s pressure die systems have enabled wire drawers to reach drawing speeds topping 50 meters per second. This type of performance can only be achieved with the consistency and reliability of Paramount Die’s wire drawing inserts.
WCI: And how is it going- the partnership with Ronak?
AK: The partnership with Ronak Industry is new and exciting. Mr. Shah’s connections within the wire drawing industry are very strong and so are his relationships with companies that draw wire in India. We look forward to working with Ronak Industry to provide Paramount Die’s exchangeable wire drawing inserts and tooling systems to the Indian marketplace.