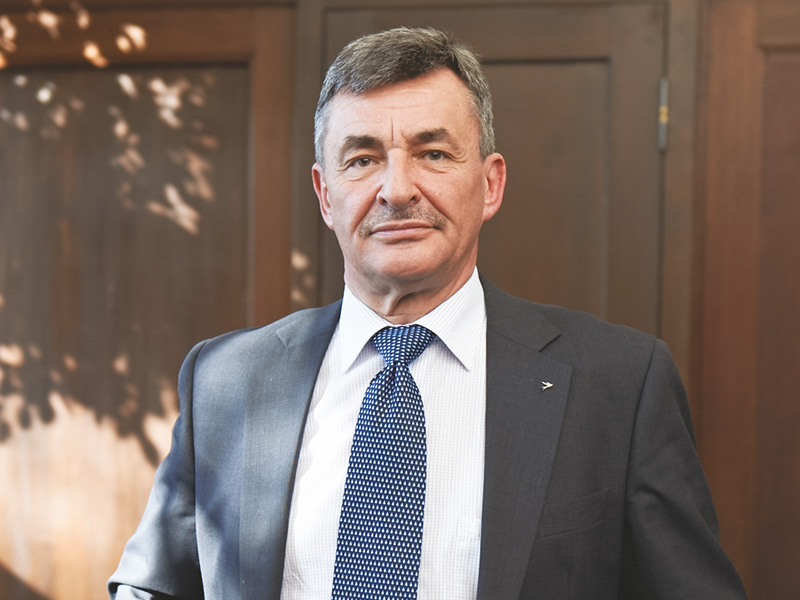
In a detailed Interaction with Mr Ulrich Eberhardt, Managing Director, Motan Group team WCI explored about the group and its activities, its Indian ingress & future plans, above all solutions offered to the wire & cable industry. Below are the excerpts of the interaction.
Wire & Cable India: Brief us about Motan Group, its operations and presence worldwide?
Ulrich Eberhardt: The Motan Group headquartered in Constance, Germany, on the lake of the same name, was founded in 1947. Motan was a pioneer in the plastics material handling and completes 40 years in this business in 2013. A leading materials handling expert, Motan delivers solutions for injection moulding, blow moulding, extrusion, compounding, in-line systems and chemicals. Its innovative, application-driven portfolio includes modular systems for the storage, drying, crystallisation, conveying, dosing and mixing of bulk goods for plastics processors and manufacturers.
Motan’s sales & service subsidiaries are located in Germany – North and East European markets; Switzerland – South European, South American, North African and Middle East markets; USA – North & Central America, Singapore – Far East, Australia and New Zealand, China and India – South Asian markets. This wide network is further deepened by agents. Motan operates production facilities in Germany, India and China, sells and services its products and end-to-end systems via its regional sales centres. With a headcount of more than 450, motan posts annual revenues of over 100 million Euros. Thanks to a vast network and extensive experience, Motan delivers precisely what its customers need: tailor-made solutions with excellent value added.
WCI: “Motan, one of the worldwide leading system suppliers for sustainable material handling, offers a comprehensive program that covers all areas of dosing and mixing” Kindly elaborate on your solutions?
UE: Power cable manufacturing process has two distinct and separate stages – (1) extruding the cable from special grade polymers and (2) compounding the polymer itself by combining different individual grades of polymers and additives to confer special properties. The group offers solutions for both applications.
Cable manufacture from granular polymers: Correct material handling – storage, drying, conveying and blending of the raw material plays a vital role in manufacturing quality power cables – medium voltage (MV), high voltage (HV) and extra-high voltage (EHV). Even the most expensive extruder will not deliver good products unless the handling of the raw materials meets the basic needs as far as product cleanliness, dust free material transport, material moisture level, material temperature etc. is concerned.
Cable polymer compounding: Cables are used in myriads of applications. Each application requires its own specific cable grades. This process manufactures the basic compound, which is subsequently extruded into cables. It is high technology and involves processing different types/grades of polymer with additives. Many of them are in powder form, some in liquid form and are in widely varying specifications – silane grafted, flame retardant, low smoke, halogen free, lead free etc.
WCI: What benefits does customer derives from Motan-Colortronic Solutions?
UE: The group has designed their products as per the customer needs, which are:
1. Available for the entire spectrum of cable material handling – polymer compounding, drying, conveying, storage and blending.
2. Offered as standard units in a very wide range. It ensures high flexibility for differing applications with standard products.
3. User friendly and net workable controls.
4. Reliable and energy efficient “green” technology.
5. And, comes with worldwide sales, application and service network.
WCI: When did Motan started its Indian operations, what was the idea behind it and going ahead what are the future plans?
UE: Motan entered the Indian market as early as 1993 through a technical collaboration agreement with Indian conglomerate Larsen & Toubro (L&T). In 1998, it set up a liaison office to support the fast growing Indian market better through L&T. In 2009, Motan-Colortronic Plastics Machinery (India) was set up as a wholly owned subsidiary of Motan Holding GmbH. The decision to start a new innings on its own was primarily due to the large future potential that the Indian market had. With Motan know-how combined with German quality, Chennai facility produces reliable, high-quality products such as the LUXOR dryer series, conveying equipment and mixing and dosing equipment. It has set up sales and service support centers at the following Indian locations: North (Delhi), South (Chennai) and West (Vadodara & Pune).
“Besides technology and innovation, Motan believes in transparent knowledge sharing. The company’s philosophy for training and skill building extends beyond its employees, to its customers and the entire industry. Motan-Colortronic India’s effort in this direction is fully supported by the Group. Its employees and customers are trained at facilities and technology laboratories in Germany and Switzerland. Motan India’s future plan is to widen the product range, customer base and to offer the same excellent quality, reliability and service here as it does elsewhere. Specifically, localization of parts will be done where volumes are reasonable to ensure quality and additional sales & service centers will be set up near customer clusters” elaborated Mr. Srikanth Padmanabhan, Managing Director, Motan-Colortronic Plastics Machinery (India) Pvt Ltd.
Many leading cable manufacturers in India already have installed Motan products/systems either directly purchased from the group or together with world renowned cable extruder manufacturers as OEM’s. The Indian base provides application, parts and service support to all products irrespective of the route through which it has come to the Indian customer.
WCI: Your views on the Indian wire & cable industry and areas of its improvisation?
UE: In relation to material handling, Indian wire & cable industry has the entire spectrum of equipment quality and standards – from highly automated and integrated dryers and conveying in use at some large optical fibre and EHV cable factories to very basic manual energy inefficient techniques in a vast majority. Basic polymer costs are the same for all cable manufacturers and are steeply increasing by the day. To stay competitive and profitable, Indian wire and cable manufacturers have to manufacture superior quality with lower operating costs. This means that in addition to the basic extruders, material handling equipment have to be:
1. Energy efficient in processes like drying
2. Reduce wastage and rejections with proper storage, blending/mixing and conveying
3. Suitable for value added high technology cables & wires
4. Consistent in quality and performance
5. Reliable suppliers with high uptime and quick trained local support
6. Benefit customer with low “total life cycle costs” rather than by low “initial investment”.
7. From a supplier with a proven technology background and who is willing to support transparently.
In specific terms, Indian wire & cable industry will follow international trends with:
1. Loss-in-weight gravimetric blending units with automatic conveying of the inputs in cable compounds manufacture.
2. Clean and safe storage solutions.
3. Energy efficient dehumidified air dryers for XLPE and hot air dryers for PVC.
4. Automatic conveying in cable extrusion.