Mixer S.p.A., an expert in manufacturing wire and cable compounds, in its recent innovations, has introduced high-flexibility medium voltage insulation compounds that prevent scorch issues, particularly at high extrusion speeds.
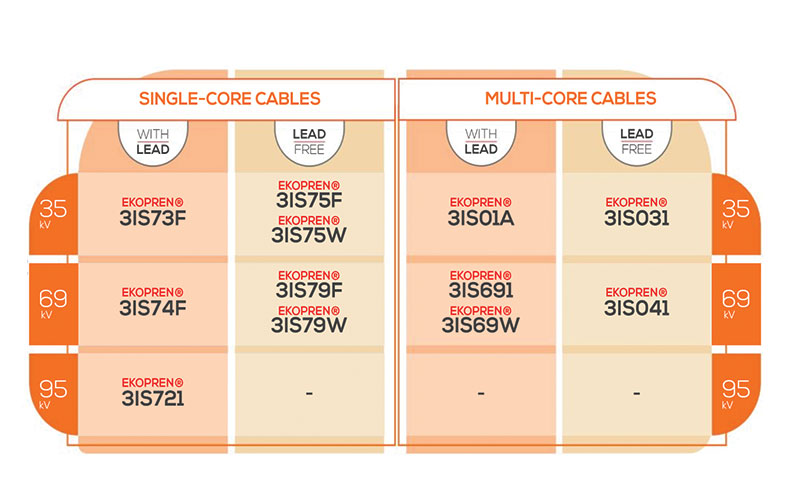
Mixer S.p.A., the Italian company with over 25 years of experience in cable industry, is committed to meeting customer needs through personalized support and collaborative strategy. Since its founding in 1996, the company has focused on innovation and reliability, steadily advancing its expertise in wire and cable compounds. By offering its compounds in pellet form rather than strips, Mixer ensures key advantages for its clients, such as more efficient transportation and storage, as well as enhanced product consistency and uniformity.
The company’s portfolio is built on stringent quality control, from raw material selection to the final product, and features a wide range of solutions customized for different applications in the cables market. Among its offerings, Mixer is globally recognized for its rubber-based medium voltage insulation, offering solutions that will guarantee advantages compared to other types of insulation materials such as PVC or XLPE. Flexibility, oil resistance, and resilience in applications that face extreme environmental conditions are some of the main properties that our rubber-based compounds can provide.
Watch: West Coast Optilinks: Digitizing the World With High-Speed Data Connection
Mixer’s insulation solutions cover a variety of grades based on EPR, EPDM, and EPDM-PE blends, available with or without lead. They completely comply with the international specifications for operating temperatures of 90°C and 105°C, withstanding also extremely cold settings as low as -50°C/-60°C. The lead-free options are specifically designed to reduce the environmental impact while maintaining outstanding insulating performance adhering to RoHS regulations for market access in Europe.
In its recent innovations, Mixer has introduced high-flexibility grades that prevent scorch issues, particularly at high extrusion speeds. EKOPREN® 3IS73F and 3IS75F for applications up to 35 kV, and EKOPREN® 3IS74F for applications up to 69 kV represent such solutions, all of them suitable for single core cables. On the other hand, focusing the attention on the multicore applications, it is worth noting the new grades such as EKOPREN® 3IS01A and EKOPREN® 3IS691 which, together their lead-free counterparts EKOPREN® 3IS031 and EKOPREN® 3IS041, ensure low deformation in processes that involve a second step of peroxide-induced crosslinking for the sheathing extrusion. These grades can maintain constant the diameter of each insulation core against the high pressure generated by the outer sheath, ensuring a high level of flexibility and avoiding partial discharges or breakdown issues. EKOPREN® 3IS041, in particular, is designed for wind turbine applications where high flexibility is strictly required. Besides, focusing on a deep investigation on the raw materials capable to provide the highest quality in terms of electrical properties, the company offers, on one hand, a new grade for applications in single-core cables up to 95 kV named EKOPREN® 3IS721 and, on the other, new grades with enhanced water resistance named EKOPREN® 3IS69W for multicore solutions up to 69 kV and EKOPREN® 3IS75W and 3IS79W for single-core ones, 35 kV and 69 kV respectively.
Also Read: Colombo Witnessed Symposium on Efficient Drawing Plants
Mixer S.p.A. continues to stand out by being “Wired Differently,” maintaining a focus on understanding and adapting to its customers’ unique needs. Through innovative materials and custom-tailored solutions, the company ensures reliability and competitiveness, from product design to delivery, for clients worldwide.