Founded in 1897, MFL Group is an engineering and manufacturing group of companies headquartered in Molteno, Italy that distinguishes itself through its extensive machinery portfolio and complete production plants to ferrous and non-ferrous wire, cable, and rope manufacturers. Over the last 30 years, the group is fully committed to increasing its investments in machinery performance enhancements, catering to the evolving requirements of its customers. Their global reach spans more than 100 countries, supported by a network of sales/service hubs in Europe, North America, and Asia. In the upcoming two years, its supply chain is expected to face significant challenges, necessitating innovative approaches to address current process constraints. Ms. Lucia Frigerio, Executive Vice-President, MFL Group, shared with Wire & Cable India, the company’s journey, product portfolio, and business roadmap for the coming year. She also talked about the group’s approach to continuously improving wire and cable manufacturing technologies.
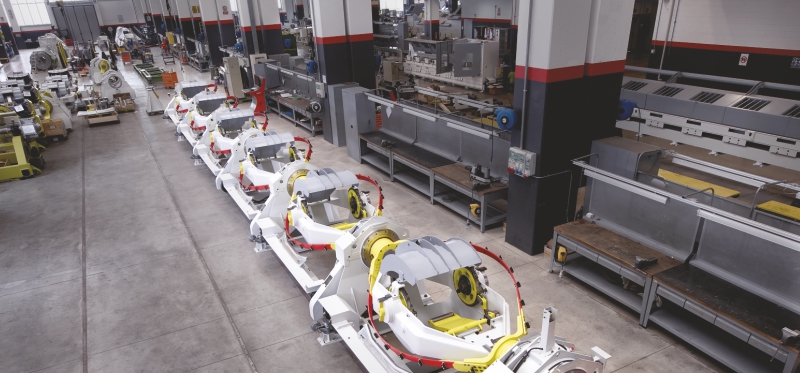
Wire & Cable India: Please tell us about your journey, major milestones, and crucial achievements.
Lucia Frigerio: MFL Group is a globally recognized family-owned company specializing in industrial machinery for wire, cable, and rope manufacturers. Established in 1897 as a small workshop, our journey reached a significant milestone in 1919 with the creation of our first wire drawing machine under the Mario Frigerio brand. In 1998, we entered the wire and cable market for non-ferrous materials with a new brand, Frigeco. During the 1990s and 2000s, we expanded our presence, establishing new companies in China and the USA, solidifying our position as the world leader in the wire and rope industry. In the past decade, we experienced substantial growth through strategic acquisitions.
In the wire and cable sector, we enriched our brand portfolio with the expertise and experience of Caballé, OM Lesmo, and Eurodraw Energy. This transformation positioned MFL Group as a unique machinery manufacturer, offering turn-key solutions for cable production, spanning from rod breakdown machines to stranding lines, and extending to extrusion and sheathing processes.
In the wire and rope division, the acquisition of the esteemed brand Koch allowed us to further diversify our portfolio, incorporating reinforcement steel wire lines. A significant milestone in eco-friendly wire treatment was achieved through the acquisition of Coseco, a company specializing in chemical and electrolytic equipment.
As early as 2019, we recognized the immense potential of digital technologies within the manufacturing industry. This strong conviction led to the inception of MFL X, a new program dedicated to empowering wire, rope, and cable manufacturers to unlock the full capabilities of their production lines through the utilization of exponential technologies. Today, our entire group comprises over 450 dedicated employees, spread across six manufacturing plants in Italy, Germany, Spain, and China and nine sales/service offices in Italy, Switzerland, Germany, USA, and China.
WCI: Kindly elaborate on your product portfolio and its applications.
LF: MFL Group distinguishes itself through its extensive machinery portfolio and its capability to engineer and manufacture complete production plants. We cater to wire and rope manufacturers across a wide spectrum of industries and applications. Our offerings include wire rod preparation lines, drawing lines, cold rolling lines, reinforcement steel wire lines, welding lines, induction tempering and hardening lines, automatic rewinding and packaging lines, wire treatment lines, cold heading and ball bearing lines, low relaxation PC lines, and sheathing lines, as well as stranding and closing lines. In the wire and cable industry, just like in the wire and rope sector, we provide a comprehensive array of machinery, encompassing drawing lines, stranding lines, extrusion, and sheathing lines. All production lines are renowned for their outstanding performance, reliability, continuous innovation, and minimal maintenance demands.
Watch: RR Kabel | Solar Cables | Solar Plant | Renewable Energy
WCI: Please shed some light on your clientele and market footprint.
LF: We serve a wide range of wire, cable, and rope manufacturers across various industries and applications worldwide. Our global reach spans more than 100 countries, supported by a network of sales/service hubs in Europe, North America, and Asia. This extensive presence enables us to provide tailored solutions and exceptional support to our clients on a global scale. Our clientele includes both established industry leaders and emerging players, all seeking the high-quality machinery and services that MFL Group offers.
WCI: How does MFL Group ensure customer satisfaction?
LF: At MFL Group, customer satisfaction is a top priority, and we employ several key strategies to ensure our clients’ contentment. We maintain stringent quality control processes throughout our manufacturing operations, ensuring that our machinery meets the highest standards. This commitment to quality results in reliable and durable equipment that consistently delivers optimal performance. We continually invest in research and development to stay at the forefront of technological advancements. This includes a strong focus on developing machinery that is not only technologically advanced but also increasingly efficient in terms of energy consumption. This allows us to offer cutting-edge solutions that meet our customers’ evolving needs, enhance efficiency, reduce operating costs, and drive their success.
We take the time to understand our client’s specific requirements and challenges. Our dedicated sales and service teams work closely with customers to provide tailored solutions and after-sales support, including training, maintenance, and technical assistance. With a worldwide presence, we can offer timely and responsive assistance to clients across the globe. MFL Group provides a complete range of machinery, offering customers a one-stop solution for their wire, cable, and rope manufacturing needs. This streamlines procurement and ensures compatibility between different production processes. Our dedication to quality, innovation, customer-centricity, and continuous improvement is reflected in our high rate of loyal customers and ensures that MFL Group consistently meets and exceeds customer expectations.
WCI: Please shed some light on R&D initiatives taken by the company to stay ahead of its competition.
LF: Over the course of three decades, MFL has made substantial investments in pioneering products and services designed to offer comprehensive, vertically integrated turn-key solutions to both ferrous and non-ferrous wire, cable, and rope manufacturers. Our commitment to staying at the forefront of innovation is evident in our unwavering dedication to research and development. We’ve made strides in various areas, from pioneering advanced coiler machines, such as the no-twist coiler, to introducing ecologically sustainable solutions for rod preparation. We’ve also elevated our rod breakdown equipment and developed machinery for the fiber optics sector. At MFL Group, our R&D team maintains a vigilant watch over the ever-evolving landscape of our industry.
Our strategic partnership with researchers from the University of Politecnico di Milano, one of the most recognized technical universities, has been instrumental in driving our innovations. This collaboration empowers us to continually refine our technologies and minimize their environmental footprint. In 2019, we took a significant step forward by establishing JRC Matt, a joint research center in collaboration with Politecnico di Milano and key stakeholders along the supply chain for metal products. This center is dedicated to fostering innovation and knowledge-sharing among its members, with a primary focus on the production, transformation, and derivatives of semi-finished metal products. JRC Matt operates on principles of open innovation, aiming to collectively address common challenges within the industry.
Additionally, the MFL X Program is charged with innovative projects geared towards enhancing the productivity of our customers’ production lines by harnessing exponential technologies. Through these concerted efforts, MFL continues to stay ahead of the competition, offering cutting-edge solutions and advancing the wire and cable, wire, and rope industries into the future.
“Our entire group comprises over 450 dedicated employees, spread across six manufacturing plants in Italy, Germany, Spain, and China and nine sales/service offices in Italy, Switzerland, Germany, USA, and China.”
WCI: What role does innovation play in MFL Group’s approach to continuously improving wire and cable manufacturing technologies?
LF: Innovation plays a pivotal role in MFL Group’s approach to continuously improving wire, cable, and rope manufacturing technologies and staying at the forefront of the industry. We prioritize research and development to harness the latest technological advancements. This allows us to design and manufacture machinery that incorporates cutting-edge features and capabilities. For example, our focus on automation, data analytics, and Industry 4.0 technologies has transformed production processes, enabling greater efficiency and precision.
Innovation extends to developing machinery that is increasingly efficient in terms of energy consumption. We continually explore eco-friendly solutions and sustainable practices to align with both industry trends and environmental concerns. We understand that every wire and cable manufacturer has unique requirements. Through innovation, we can offer highly customizable solutions that cater to specific needs. This flexibility ensures that our customers can optimize their production lines according to their product specifications and operational goals.
Innovation drives the development of machinery that enhances productivity. By leveraging advanced technologies, we can design equipment that reduces downtime, minimizes waste, and maximizes throughput. This results in increased production capacity and improved overall efficiency. Innovation enables us to adapt swiftly to changing market demands. By closely monitoring industry trends and customer feedback, we can develop and refine our machinery to address emerging needs and challenges effectively.
Also Read: Assomac: A Name Synonym with Wire Machinery in India
WCI: In what ways does the company prioritize sustainability in its operations without compromising quality?
LF: MFL Group underscores its commitment to sustainability while maintaining the highest quality standards. We design and manufacture machinery that prioritizes energy efficiency, thus reducing energy consumption during production processes. We continually explore and invest in eco-friendly technologies, such as our sustainable solutions for rod preparation, which decrease our environmental footprint while upholding the utmost product quality. Additionally, we actively promote recycling initiatives, reusing materials whenever feasible, and ensuring proper waste disposal practices. Furthermore, our primary operating companies hold UNI EN ISO 14001:2015 certifications, highlighting our dedication to environmentally responsible practices. Moreover, our machinery is purposefully engineered for durability, reducing the need for frequent replacements. This approach not only minimizes waste but also underscores our commitment to providing customers with long-lasting, high-quality equipment. We are committed to giving top priority to local sourcing within our supply chains. This approach not only helps us decrease transportation distances and minimize carbon emissions but also fosters the growth of local economies. Through these concerted efforts, we seamlessly prioritize sustainability without compromising the exceptional quality of our products and services.
WCI: What is the business roadmap for the coming years?
LF: In the coming years, we are fully committed to increasing our investments in machinery performance enhancements, catering to the evolving requirements of both the ferrous and non-ferrous industries.
There has been a notable shift in the perceived value of industrial production lines, with a substantial portion of this value now attributed to advancements in software and service quality. In this context, MFL X program remains dedicated to delivering applications capable of addressing the emerging challenges faced by wire, cable, and rope manufacturers.
In the upcoming two years, our supply chain is expected to face significant challenges, necessitating innovative approaches to address current process constraints. We may find it imperative to incubate activities that were previously outsourced, enhance vertical integration, and invest in resource planning. Sustainability continues to be a paramount focus for us, marked by a dual approach. On one front, we are actively engaged in researching eco-friendly machinery solutions for our customers, with the goal of reducing carbon footprints and minimizing waste. Concurrently, we are resolute in our commitment to implementing eco-friendly practices across all companies within our group. MFL Group’s primary goal remains ‘people’. Recognizing the rapid evolution of job roles, we are making substantial investments in upskilling and reskilling, fostering lifelong learning experiences, and embracing interdisciplinary profiles. We recognize that our ability to cultivate enduring relationships with both suppliers and customers is just as crucial as acquiring new ones and this belief will guide our efforts in the coming years. We firmly believe in the power of active listening and understanding the real needs of our partners. It’s not solely about the products we offer; it’s more about aligning with our customers’ needs and providing tailored solutions to meet those needs effectively.