MFL Group pushes innovation in the wire & cable industry by enhancing process automation, boosting line efficiency, and integrating smart monitoring systems. They continuously evolve their machinery with a focus on reducing energy consumption, minimizing waste, and lowering environmental impact while enhancing product quality and productivity. To enhance operational intelligence across all production lines, the group has developed MFL Acumen, fully compatible with all machinery types—drawing, stranding, and extrusion—delivering advanced data analysis and process optimization. In a conversation with Wire & Cable India magazine, Mr. Nicola Corti, Sales Director, Wire & Cable Division, MFL Group talks about their major breakthroughs, including the wireless data transfer system for double twist stranders, which is currently under patenting.
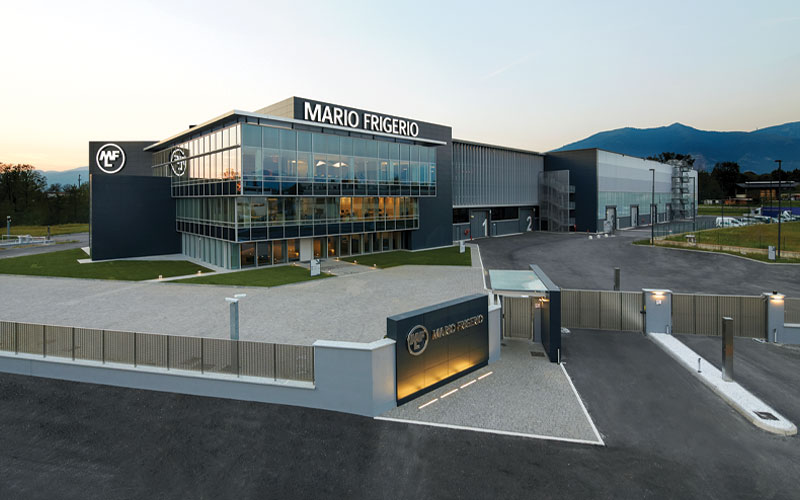
Wire & Cable India: Shed light on the key innovations and emerging trends shaping the wire and cable industry.
Nicola Corti: The wire and cable industry is undergoing a significant transformation, driven by automation, digitalization, sustainability, and safety. A major challenge is the shortage of skilled labor, pushing companies toward greater automation to ensure consistent quality and operational efficiency.
As manufacturers strive to increase efficiency and reduce costs, digitalization has become a game-changer, enabling the integration of data analytics to optimize manufacturing processes. Energy-efficient production lines, predictive maintenance, and real-time monitoring systems are enhancing productivity while minimizing downtime.
Sustainability is becoming a top priority, with manufacturers focusing on reducing waste, energy consumption, and material usage to minimize their environmental impact. Meanwhile, safety remains a critical concern, particularly in extrusion technology. The demand for safer, high-performance materials—such as flame-retardant compounds—is rising, driven by regulatory requirements to improve product safety.
WCI: Please highlight the latest advancements and technology developments that you have introduced in your machines to cater to these evolving needs.
NC: MFL Group continues to push innovation by enhancing process automation, boosting line efficiency, and integrating smart monitoring systems.
To meet growing demands for automation, the BAO Max (automatic rewinding and packaging line) automates the entire process for low and high carbon wire and strand, handling up to 200 kg coils. From continuous rewinding to palletizing, this high-tech solution requires just one operator to oversee the entire process. Following the same approach, our tubular machines now feature automated loading and unloading systems to further streamline operations.
Addressing sustainability and surface preparation efficiency, our rod preparation line combines mechanical descaling with phosphating, reducing environmental impact while ensuring an ideal wire surface for downstream drawing. We continue to refine this technology, particularly our electrolytic phosphating process, to improve wire drawability and corrosion protection.
Completing our Wire & Rope drawing portfolio, we have introduced the Pail Packer Machine (PPM), an advanced wire take-up solution designed for minimal or no permanent twist, ensuring smooth static wire payoff. With a high coil capacity of up to 2 tons, PPM reduces operator intervention, enhances production speed, and minimizes maintenance. Its adaptable design accommodates various wire diameters and can integrate a laser gauge in the preceding drawing machine for real-time quality control.
In the field of insulated magnet wire production, we have made significant advancements in PEEK and PPSU extrusion. Our expertise in managing the crystalline phase of these materials has resulted in exceptional insulation quality, minimal thickness, and improved adhesion to the conductor. Today, MFL Group offers end-to-end solutions for insulated magnet wire production in PEEK, from the initial rod breakdown to the final extrusion stage.
A major breakthrough, currently under patenting, is our wireless data transfer system for double twist stranders, eliminating wiring, reducing maintenance, and solving connection issues associated with traditional brush-based systems.
Further expanding our rod breakdown portfolio, we have introduced the TS2 machine, featuring a compact design, real slip of 1%, and energy-saving capabilities that boost overall efficiency.
To enhance operational intelligence across all production lines, we have developed MFL Acumen, now fully compatible with all machinery types—drawing, stranding, and extrusion—delivering advanced data analysis and process optimization.
Watch: Top Cable Companies in India
WCI: How do you help your customers achieve better efficiencies in their production processes? Maybe, by reducing the energy consumption; enhancing quality or reducing the waste in the production process.
NC: We design and continuously evolve our machinery with a focus on reducing energy consumption, minimizing waste, and lowering environmental impact while enhancing product quality and productivity. Our commitment extends beyond technological advancements—by conducting life cycle assessments, we gain deeper insights into sustainability improvements, further supporting both our innovation efforts and our customers’ goals.
To optimize production efficiency, we provide MFL Acumen, a smart solution that evolves alongside our machinery. Acumen enables users to make data-driven decisions, optimizing performance and maximizing productivity across the entire production line.
Complementing this, we are introducing Emma, a next-generation app that offers 24/7 real-time support. Emma provides instant access to manuals, service cases, IIoT machine data, and engineering expertise, ensuring that operators can troubleshoot issues efficiently, reduce downtime, and maintain peak performance.
WCI: Do you have any R&D team catering to evolving needs? Elaborate more about your R&D efforts.
NC: MFL Group has made substantial investments in pioneering products and services, offering comprehensive, vertically integrated turnkey solutions for ferrous and non-ferrous wire, cable, and rope manufacturers.
Our commitment to innovation is reflected in our dedicated R&D efforts, which focus on advancing automation, reducing maintenance and wear, and developing sustainable solutions while pushing the digital frontiers of the industry. By staying ahead of technological shifts, we continuously refine our machinery to enhance performance and minimize environmental impact.
A key pillar of our innovation strategy is our long-standing partnership with Politecnico di Milano, one of the most recognized technical universities. This collaboration enables us to develop cutting-edge technologies while integrating sustainability-driven research into our solutions.
To further accelerate innovation, we established JRC Matt in 2019—a joint research center in collaboration with Politecnico di Milano and key stakeholders across the metal products supply chain. Operating on principles of open innovation, JRC Matt fosters knowledge-sharing and collective problem-solving, focusing on the production, transformation, and applications of semi-finished metal products.
Additionally, through the MFL X Program, we explore exponential technologies to enhance our customers’ productivity. By partnering with 40Factory, a leader in industrial digitalization, we leverage insights from multiple sectors to refine our applications and expand the possibilities of smart manufacturing.
WCI: What is your current product portfolio catering to the wire & cable sector?
NC: MFL Group provides a complete range of machinery for wire drawing, stranding, extrusion, and surface treatment, serving all industries, with applications in automotive, energy, agriculture, mining, and construction, among others.
WCI: Could you provide insights into your market presence and key clientele globally & in India?
NC: MFL Group serves a diverse range of wire, cable, and rope manufacturers across industries and applications worldwide. With a presence in over 100 countries, we support our customers through nine sales and service hubs across Europe, North America, and Asia, ensuring tailored solutions and dedicated support on a global scale.
Our clientele includes both established industry leaders and emerging players, all relying on MFL Group for high-quality machinery and services to enhance their production capabilities.
In India, our presence continues to expand, driven by Area Managers Martino Castelli (Wire & Rope) and Davide Costabile (Wire & Cable), working alongside local agents to strengthen relationships and provide localized support.
Also Read: Rosendahl Nextrom: All Set to Support AI Revolution
WCI: How do you integrate sustainability into your manufacturing and application processes?
NC: MFL Group integrates sustainability and quality at every stage of machinery design and manufacturing. By prioritizing energy-efficient solutions, we reduce energy consumption in production processes while maintaining the highest product standards. Our investment in eco-friendly technologies, such as sustainable rod preparation solutions, further minimizes environmental impact without compromising performance.
Beyond energy efficiency, we actively promote recycling initiatives, reusing materials where possible and ensuring responsible waste management. Our commitment is reinforced by UNI EN ISO 14001:2015 certifications held by our primary operating companies, reflecting our adherence to environmentally responsible practices.
Durability is another cornerstone of our approach. Our machinery is built to last, reducing the need for frequent replacements, minimizing waste, and ensuring long-term value for our customers. Additionally, we prioritize local sourcing within our supply chains, reducing transportation distances, lowering carbon emissions, and supporting local economies.
Our first sustainability report and the life cycle assessment of a rod breakdown machine further demonstrate our ongoing commitment to sustainability, reinforcing our mission to align environmental responsibility with exceptional product quality.
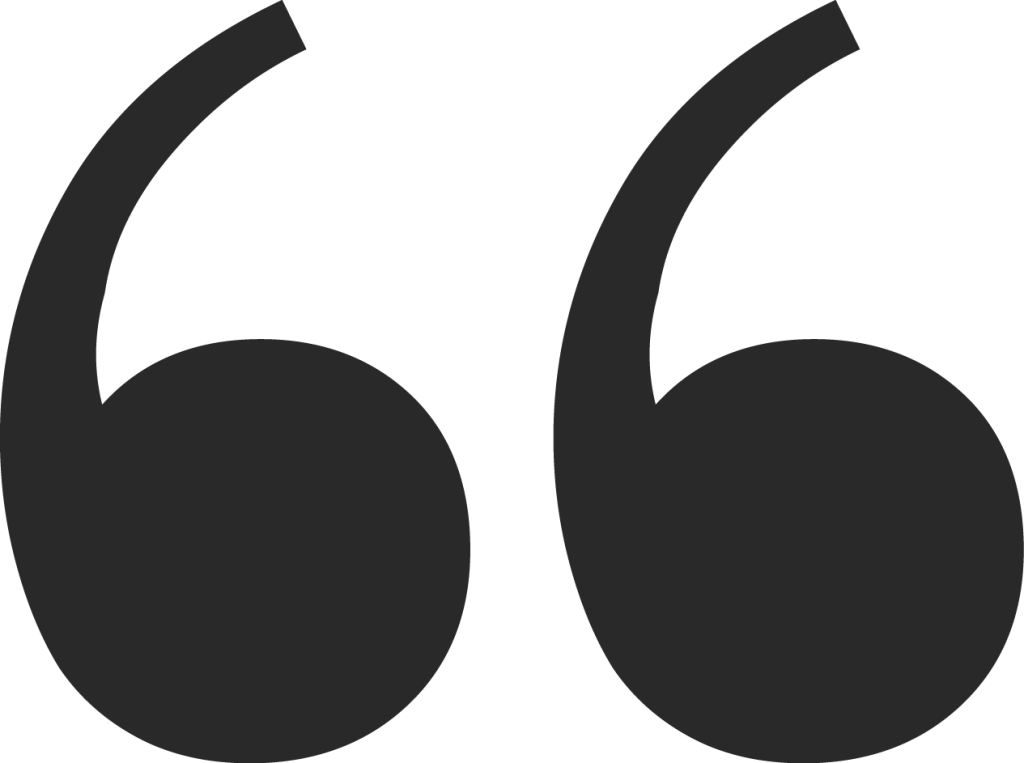
We have introduced the PPM Pail Packer Machine (PPM), an advanced wire take-up solution designed for minimal or no permanent twist, ensuring smooth static wire payoff.
WCI: What are your company’s long-term growth strategies and future plans?
NC: MFL Group is committed to enhancing machinery performance and expanding our turnkey solutions to meet the evolving needs of both the ferrous and non-ferrous industries. As the value of industrial production lines shifts toward software and service quality, our MFL X program continues to drive innovations that address the challenges faced by wire, cable, and rope manufacturers.
Sustainability remains a key focus, as we develop eco-friendly machinery solutions to reduce carbon footprints and waste for our customers, while also supporting local communities.
We recognize the importance of cultivating long-term partnerships with both customers, suppliers and partners. By working closely, we can identify emerging needs and develop new solutions through open innovation.
A key pillar of our strategy is expanding our local network of aftersales assistance globally, ensuring faster response times, localized expertise, and greater operational continuity for our customers. By strengthening our service presence worldwide, we aim to make our support even more concrete and accessible.
We’re driven to empower wire, cable, and rope manufacturers with comprehensive turnkey solutions, blending our rich heritage with a forward-thinking approach. We’re forging a path to our clients’ continuous and sustainable growth, embracing their entrepreneurial challenges as catalysts for innovation.