January 19, 2021
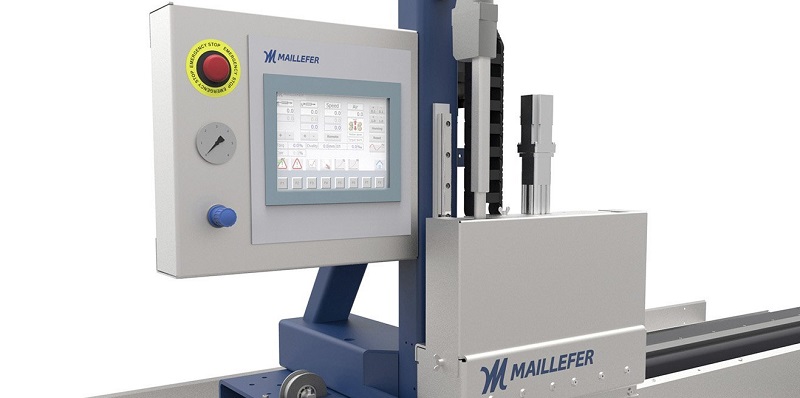
The productivity of optical cable manufacturing can increase with higher line speeds. However, the higher speeds call for more precise process control. The manufacturing process contains several parameters that the line operator controls during the production. The state of the process is both controlled and estimated by process parameter adjustments and observations.
Sensor data is difficult for humans to analyze in detail, especially in real-time during production. Interpreting the sensor data is difficult due to complex interactions throughout the manufacturing process. Also, the wear and tear of equipment causes drift in absolute sensor values. The ideal process state window, originally defined by process sensor values; shifts over time.
Maillefer has developed an artificial intelligence based automated process assistant (patent pending) that analyses the buffering process in real-time and is able to optimize the process automatically during production.
Maillefer’s Smart Buffering process assistant uses stream processing to process the raw sensor data into information. It then utilizes that information together with process state models and quality prediction models to control the clinching and the buffering process.
The company has successfully applied the Smart Buffering process assistant to a secondary coating line’s buffering process running at 800m/min with dry PP product. Abnormal process conditions, such as coupling and slipping, easily led to inferior end-quality products. Smart Buffering detects such abnormal situations and optimize the process back to a quality production state.
The automated process assistant removes the “gut-feeling” of knowing good process parameter values. Instead, the automated process assistant system automatically adjusts the process parameters until the sensor values correspond to those expected by the internal process models.
Automated feedback based process adjustment leads to a more predictable operation of the line, which eventually leads to a more stable process and better end-quality for the product. Finally, the result is improved production efficiency and considerable material savings.
Expertise from humans remains essential. Their knowledge is invaluable when operating the AI system and handling all the abnormal situations, such as wear and tear of machinery, material abnormalities, etc. Human knowledge is also required to initialize the system after line maintenance.
The Smart Buffering system signals the need to perform line maintenance when detecting a process that cannot be fully optimized. In these cases, the system generates a list of items to check before further line operation.
The end-quality feedback mechanism optimizes the process to a desired EFL target value. In order for the system to operate at full potential, the end-quality feedback mechanism must rely on external information about measured end-quality of produced reels. This can be only done by skilled professionals.
Also Read: Maillefer Expanding in India, Introduces Local Manufacturing.
The automated process monitoring and process assistant guidance leads to more stable process and better product end-quality. It monitors the process constantly and allows the line to produce at full potential. Smart Buffering is an invaluable tool that leverages the buffering line’s operation and efficiency to new levels.
Benefits:
- Good and stable end product quality
- Reduced scrap and improved productivity
- Constant monitoring and automatic control
- Operator feedback and guidance
- Downtime is reduced