“Acute data measurement and analysis coupled with extensive process knowledge is the key to the success with industry 4.0 solutions”
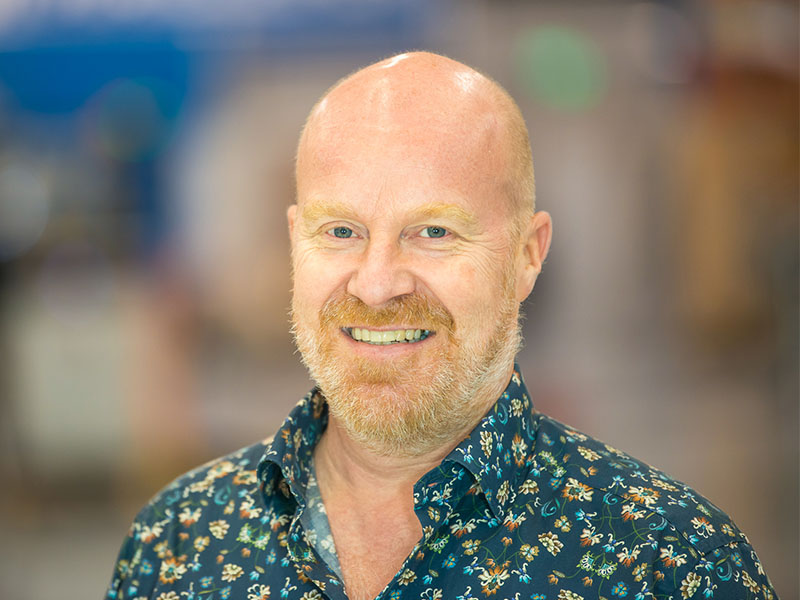
Maillefer Group has a long history of developing technology for the wire and cable industry. The company’s cable-making lines and solutions extensively use Industry 4.0 parameters to manufacture some of the most intelligent and efficient production systems. Wire & Cable India recently interviewed Dr. Mikko Lahti, Director, R&D, Maillefer Group wherein he talks about Smart Buffering and Topography Scanner – the company’s first real AI offerings, and envisages the future of Industry 4.0 – smart manufacturing, and automation in the Indian wire & cable industry.
Wire & Cable India: How according to you, has the implementation of Industry 4.0 grown over the years? Do you think that the wire and cable industry is ready to adapt to this evolving industrial revolution?
Mikko Lahti: Industry 4.0 is the automation of manufacturing technologies with built-in data collection and exchange mechanisms. Data today is a great power – to closely monitor and control operations. Therefore, in most cases, data collection has become important for people. However, mere data collection is of no use unless it is analysed to troubleshoot and upgrade the technology. Even though the wire & cable industry has had the data for decades, its convincing use has still not begun. We are measuring a huge pile of data in the products lines that we are offering. The wire & cable industry should adopt the attitude to utilise the production data more efficiently and productively. We see that the trend has begun but there are still many miles to overcome before the wire & cable industry is really deeply involved with Industry 4.0. By this, I mean that the data is used for more efficient and lean production optimisation.
WCI: What would be the impact on production efficiency and ROI with the implementation of Industry 4.0 technologies in the manufacturing process?
ML: We know what data should be measured and what devices should be used in our lines and machines. The devices help us to analyse the data and make decisions in terms of controlling our actions. This utilisation of data immensely helps us in designing a perfect machine. Designing and manufacturing machines are basically what we do, but once we have analysed previous data we can envision better machines – more efficient extruders and crossheads. A deeper knowledge of the process is also critical in order to better utilise the data to get a conclusive idea of how the machines have been working previously and how we can optimise it more. Hence, the acute data measurement and analysis coupled with extensive process knowledge is the key to the success even with industry 4.0 solutions. The productivity of manufacturing can be increased with higher line speeds. Higher speeds call for more precise process control. The manufacturing process contains several parameters that the line operator controls during production. The state of the process can be both estimated and controlled by process parameter adjustments – by offering a modern artificial intelligence-based control solution that brings value to customers by helping line operation and by optimising the process parameters. This improves the production efficiency, the product end-quality, and ROI.
“We see that the trend has begun but there are still many miles to overcome before the wire & cable industry is deeply involved with Industry 4.0.”
WCI: What are the most common challenges/pitfalls when customers try to move to Industry 4.0 systems? How do you help the industry address these challenges?
ML: In some simple cases, the first challenge is to gather the data from the process. But in most processes that have been solved several years ago, the most common challenge is to couple the process data with quality data. There is often a lack of quality data or it is measured afterward. Without knowing the relations between the process data and quality data, it is extremely difficult to improve the effectiveness of the production process.
We are measuring a huge pile of data in the product lines that we are offering. Today, we have also started to utilise the data. Nowadays, we have our first real AI offerings launched to the market: smart buffering and topography scanner. In smart buffering, the line can autonomously control itself leading to extremely efficient production with minimal raw material consumption. In the topography scanner, we have developed a neural network-based inspection method for identifying defects from cable surfaces which will help our customers to save remarkable amounts of money not making scrap in the post processes.
WCI: Cybersecurity is an increasingly important requirement for Industry 4.0. In what ways do you address it?
ML: Cybersecurity in the Age of Industry 4.0 requires state-of-the-art risk management. Our systems are built with continuous operation in mind and they have been hardened against old and emerging new threats. Access control, system monitoring, and automatic recovery are integral parts of critical systems. While data sharing and connectivity are building blocks of Industry 4.0, it is necessary to identify and restrict data access solely between benefitting parties. Last but not least, continuous education of our personnel ensures that our customers receive the best available training to face future challenges.
“While data sharing and connectivity are building blocks of Industry 4.0, it is necessary to identify and restrict data access solely between benefitting parties.”
WCI: Could you tell us about recent & noteworthy projects accomplished by your company in India — specific to wire & cable companies?
ML: We have strengthened our support and presence in India by introducing local manufacturing and supply of brand-name technology destined to low voltage wire & cable manufacturers within the region. The Indian subcontinent is seen as one of the fastest-growing wire & cable markets in the world in long term. We have a long history of presence, supporting the growth of this market, and of serving our customers in the region through our office and team in Mumbai. We have introduced local manufacturing and local supply of Maillefer India technology for the low voltage market. We now combine Maillefer’s expertise with local Indian manufacturing and resources. This local supply, testing capability, and service/support will bring the Maillefer brand and leading technology close to all building wire, low voltage cable, and automotive wire producers in India and the region
WCI: Due to COVID resultant lockdowns, the wire & cable industry recently shifted its focus on automation & remote commissioning — how does your solution simplify their operations?
ML: Maillefer has had the remote connection to the production lines for years. We have finalised several remote commissions during this COVID time. Remote commissioning has some advantages. Since we do not have to travel as much as before, we can save time by staying at our own location though remote commissioning requires special skills from the customer as well. Even though there can be video connection or even augmented reality available, customers should have personnel available who are familiar with our technology. We see remote commissioning as a good tool for troubleshooting and an additional instrument for real on-site commissioning.
WCI: What are your short-term and long-term plans — specific to the wire & cable industry? What is the future of Industry 4.0 – smart manufacturing, and automation in the Indian wire & cable industry?
ML: The term big data, Industry 4.0, deep learning, artificial intelligence, and smart technology are just some buzz words we hear which describe the trends taking hold of the industry. We too are excited by the changes arriving in the wire & cable industry. Maillefer welcomes smart technology as a means of taking the manufacturing process to the next level. Today’s production processes are nearly all digitally integrated and automated. The amount of data collected and constantly generated is simply gigantic, making it practically impossible for humans to comprehend without assistance. Fortunately, modern tools and methods can process and understand it. Deep learning and computer algorithms sift through huge volumes of data to product quality measurements. The powerful smart manufacturing is being implemented to previously unseen levels of automation control.
“Maillefer welcomes smart technology as a means of taking the manufacturing process to the next level.”
As the future unfolds, we see operators becoming either facilitators who keep smart lines running or dedicated process specialists, who handle the exceptions and work to improve the AI models. The idea is to have an autonomous production line that will control itself according to the end-product quality.