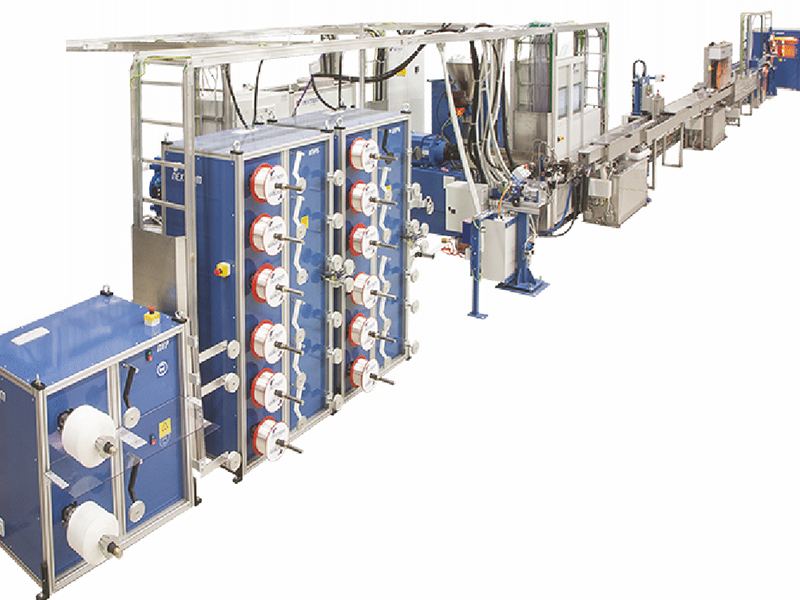
Yes, we did it. We took the existing line, added tons of knowledge from experienced Nextrom and Rosendahl people, redesigned, rebuilt, tested and fine-tuned the results. And there it is: the pimped-up Loose Tube Line. A moment we would rather call a ground-breaking new era in fiber optic cable production.
It has been challenging – we admit that the existing model has already met expectations. But what would life be without challenges? Challenges are there to be met.
And the outcome? Let’s elaborate.
The current trends in fiber optic cable manufacturing are all connected to the general optimization of each step of the production process. In order to improve cable performance and to reduce the costs of the final product, many technologies and devices have been invented to minimize optical loss, increase production speed and allow more flexibility in the manufacturing process.
New technology developments made specially for the loose tube process:
• Improved high speed fiber pay-off design with reduced footprint for space saving
• Special processing unit of the ROEX extruder to optimize the process ability of typical material used for loose tube production
• Optimized and space saving cooling trough design – safe up to 9.5m in line length!
• Better process feedback during production
• Typical line speed 600 m/min for standard loose tube types
• New development of the crosshead series RX for optimized material flow in the melt distributor, in conjunction with a linear jelly needle guiding system for easier handling
• New generation of pulley clenching capstan SCC100 for accurate post shrinkage and EFL control, especially for dry tqubes
• Improved online EFL measurement system.