Founded in 1727 as an ironwork with a royal warrant, Sweden based Lämneå Bruk evolved into a wire machinery specialist in 1823. Accumulating over 200 years of expertise in the industry, the company manufactures wire drawing lines, advanced coiling and automation solutions. Their flagship innovation, the No Twist Coiler portfolio, has significantly transformed wire manufacturing worldwide. The Hagstedt family, owners of Lämneå Bruk, has been ‘wired up’ for ten generations; the passion for wire simply runs in their blood. In a recent interaction with Wire & Cable India, Lämneå Bruk’s President, Mr. Jonas Hagstedt revealed that they design and manufacture all components for their machines in-house while integrating sustainability in its manufacturing processes.

Wire & Cable India: What are the key innovations and emerging trends shaping the wire and cable industry?
Jonas Hagstedt: We have noticed that the wire industry is experiencing a strong push towards automation, increased production efficiency, and enhanced support systems. Manufacturers are seeking ways to minimize downtime and optimize operations with uninterrupted production cycles. Additionally, instead of investing in entirely new machinery, there is a growing demand for upgrading existing systems to improve performance while maintaining cost efficiency.
WCI: Please highlight the latest advancements and technology developments that you have introduced in your machines to cater to these evolving needs.
JH: At Lämneå Bruk, we are widely known for our complete wire drawing lines, but in recent years, we have concentrated on advancing coiling and automation solutions. Our flagship innovation, the No Twist Coiler (NTC) portfolio, has been in development since 1992 and has significantly transformed wire manufacturing worldwide.
With hundreds of successful installations, the NTC enhances productivity by increasing output in both wire drawing and uncoiling without requiring modifications to existing production setups. This system replaces conventional gooseneck and spooling methods, creating precisely laid, twist-free wire coils of up to 4.5 metric tons in inverted carriers. This not only reduces scrap and enhances economic efficiency but also minimizes operational stoppages and improves logistics as the big wire package offers convenient shipment options to end-users. The NTC is designed for various applications and industries, including but not limited to welding wire, bedding & seating springs, reinforcement wire, intermediate wire, galvanizing lines, heat-treatment multiwire lines, and nail manufacturing.
Beyond the NTC, we are also focused on fully automated production lines, including rewinding lines, coilers, and spoolers, all designed to optimize modern wire manufacturing processes by reducing men-hours and streamlining production.
Electronic equipment development is constantly and rapidly progressing, and often, the technology utilized today is not compatible with older solutions, making replacement parts difficult to find on the market. To help customers avoid costly downtime, we recommend planning system upgrades before machine failures occur.
Lämneå Bruk offers tailored solutions for modernizing frequency inverters, PLC systems, HMIs, and more, ensuring seamless operation and extended equipment lifespan for both Lämneå Bruk and other manufacturers’ machines.
Watch: Top Cable Companies in India
WCI: How do you help your customers achieve better efficiencies in their production processes? Maybe, by reducing the energy consumption; enhancing quality or reducing the waste in the production process.
JH: Efficiency and sustainability go hand in hand in our approach. The No Twist Coiler, for example, is engineered to reduce energy consumption through its innovative payoff system, while removing the pre-twist ensures that every meter of wire is utilized with minimal waste.
We take pride in our in-house manufacturing, where every component is designed and produced in Sweden. This allows us to maintain strict quality control and provide customized solutions that align with our customers’ specific production needs. By reducing scrap, enhancing automation, and designing machines with energy efficiency in mind, we help wire manufacturers achieve more cost-effective and sustainable operations
WCI: What is your current product portfolio catering to the wire & cable sector? Are there any expansion plans in the pipeline?
JH: Lämneå Bruk has been a trusted partner in the wire industry for nearly 300 years, delivering tailored machinery solutions for the complete wire drawing process, from payoff to rewinding operations. Our equipment is suitable for a wide range of wire types, including welding wire, low to high-carbon wire, and stainless steel. We can adapt to industry demands and develop cutting-edge solutions which have positioned us as a leading supplier in the global market.
To support our continuous growth, we recently expanded our workshop by 40 meters, constructed new office facilities, and invested in additional automated machinery and robotics. These investments allow us to further optimize our production and continue delivering high-quality, innovative solutions to our customers.
Also Read: Reimagining Energy for Sustainable Future
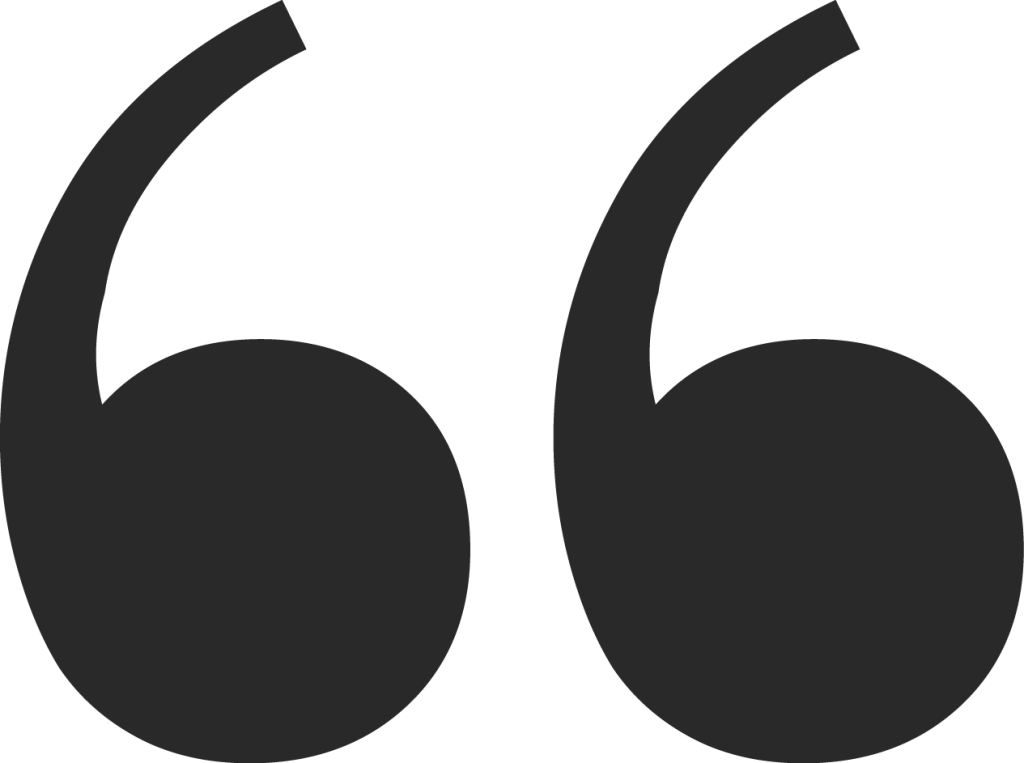
Sustainability is a core principle at Lämneå Bruk. Today, approximately 50% of our electricity comes from renewable sources.
WCI: How do you integrate sustainability into your manufacturing and application processes?
JH: Sustainability is a core principle at Lämneå Bruk. Our facility operates its own hydropower station, utilizing renewable energy from the adjacent lake—a tradition that has powered our operations for centuries. Today, approximately 50% of our electricity comes from renewable sources.
Additionally, our workshop is heated with an environmentally friendly floor heating system that uses sustainable woodchips. We have also implemented electric charging stations for employees and transitioned from paper-based documentation to a fully digital setup in our production area, reducing paper waste and improving efficiency.
By integrating these sustainable practices, we are not only reducing our environmental footprint but also ensuring that our customers receive solutions that support their own sustainability goals.