The company has successfully launched an online Factory Acceptance Test (FAT) where the customers are dialed-in live via video conference calls and they can observe the test run of their machine.
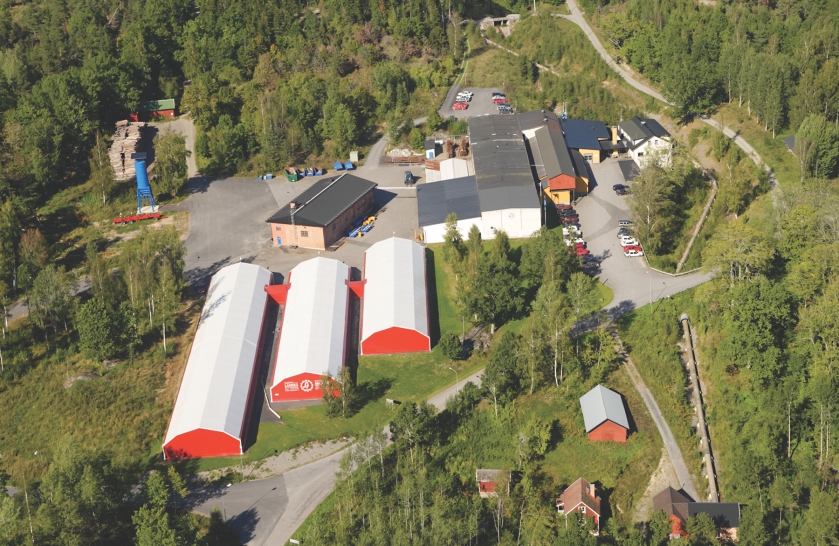
Wire & Cable India interviewed Mr. Jonas Hagstedt, Owner and Director, Lämneå Bruk AB, wherein he takes us through the business journey of the Company, the major innovations brought out in the recent times, how they have evolved their operations in face of the challenges due to the pandemic and the future plans of the company.
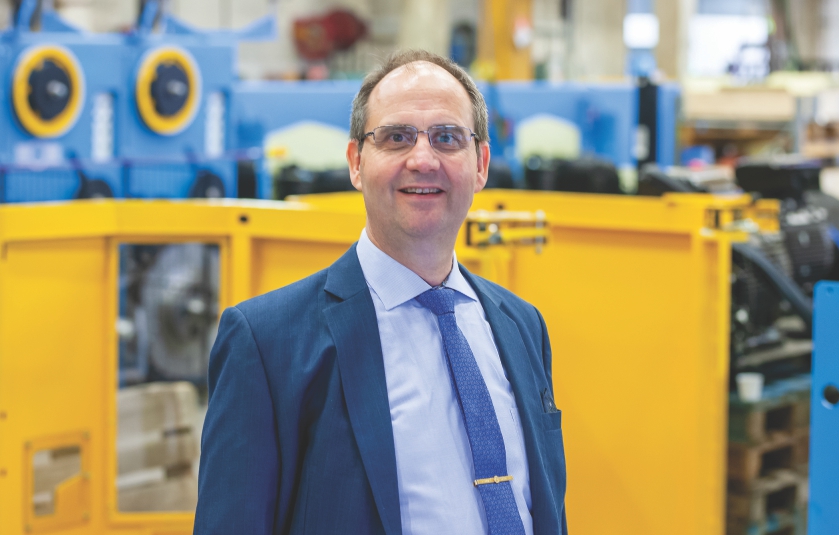
Wire & Cable India: Could you please give us a glimpse into the business journey of Lämneå Bruk which has been into the wire industry for more than 100 years while also charting out some of the most notable milestones?
Jonas Hagstedt: Lämneå Bruk has a long-standing history, it all started in 1727 when the company received the permission and stamp from no one else but the Swedish King to produce iron. Around 100 years later, we started manufacturing machines for the wire industry and stopped with the iron production completely in 1873 to focus solely on the wire business.
A big stepping stone was when my father, Lars Hagstedt acquired Lämneå Bruk in 1958 and an even bigger one for me personally was when my brother and I took over the entire operations in 1989. Just three years later, in 1992, we launched the first version of one of our bestselling machines, the No Twist Coiler (Pail Pack), the start of a real success story. Already in 1994, we began to focus on modern machinery and we have equipped all our machinery with modem connections for remote troubleshooting and access.
In 2007, I took over the Company as the sole owner and developed a new strategy to lead the company from a financially struggling entity towards being a successful, world-known, reliable supplier of wire machinery, with a strong focus on innovation, customized machine solutions, automated work processes, fact-based decision-making and of course teamwork. Since to get to the position where we are today, could only be possible with a dedicated and knowledgeable team behind me.
One of the main pillars of our success has been to come up with innovations and therefore, we strive for constant technological development.
In the following years, Lämneå Bruk introduced new machines and has continuously improved the existing machine portfolio. In 2008, we had introduced the Automatic Precision Layer Winder, which is now in its 2nd generation, and the Automatic Spooling Machine. Our Wire Drawing Machine portfolio has been completed with the Straight-Line Wire Drawing Machine in 2010 and also the AC inverter control. Since 2010, all of our machines have an internet connection as a standard feature. This allows us to do remote start-ups and troubleshooting which has been proven extremely beneficial during the current COVID-19 pandemic.
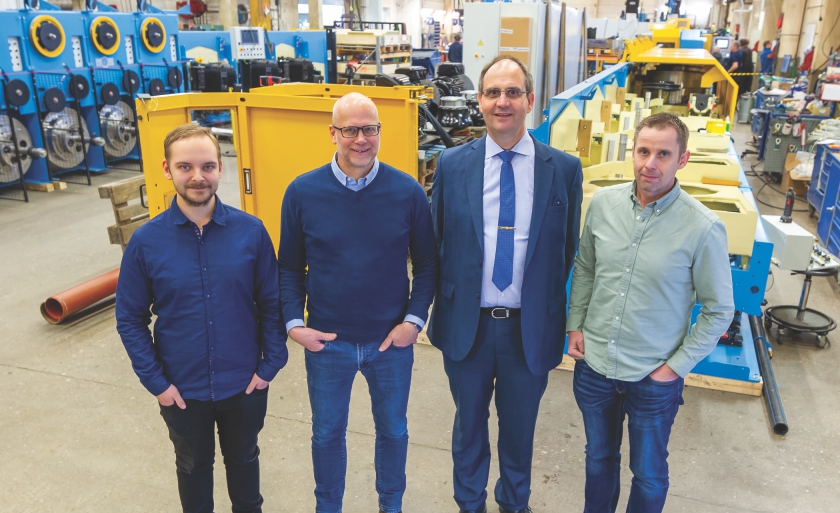
In 2013, we had advanced our Automatic Precision Layer Winder offer further, and we have launched this machine also for smaller 5 kg spools. Since 2017, Lämneå Bruk has been developing a highly innovative No Twist Coiler concept, which I believe can truly revolutionize the wire industry. This machine basically combines Take-Up and Pay-Off in one as it acts as the take-up for the wire machine while the inverted carrier is used as pay-off in the next production step and is placed directly on the floor.
And in 2020, we have introduced Factory Acceptance Test and Start-Ups completely remotely due to the worldwide travel restrictions. We have been doing this in combination with Augmented Reality devices to engage with our customers even better than usual.
WCI: What is the product portfolio of the company? Has there been any development or innovation with respect to the product offerings and any technological up-gradation in the recent past?
JH: We specialize in the design and manufacture of machines for the ferrous and stainless-steel wire industry. We are a reliable supplier of complete lines and plants for the wire industry including pay-offs, rod preparation equipment, spooling and re-spooling, coilers, drawing machines and take-up units. In addition, we also supply smaller equipment such as Pointing Machines and Rotating Die Holders. Our focus is on providing turnkey solutions, offer customized products and cater to a variety of customer requests.
We have recently launched the Fully Automatic Respooling Lines for various spool sizes
Yes, one of the main pillars of our success has been to come up with innovations and therefore, we strive for constant technological development. We have discussions with our various in-house departments on how we can use our engineering resources in the best possible ways. We have recently launched the Fully Automatic Respooling Lines for various spool sizes. Apart from that, we have developed a new Sandpaper Descaling Machine designed for a state-of-the-art rod preparation. Furthermore, we have diligently worked on the development of the No Twist Coiler 1200 for more streamlined production lines and also a No Twist Coiler for smaller wire types down to 0.3 mm.
WCI: Could you please touch upon the evolution you have perceived in the Global Wire Industry with respect to wire drawing technology?
JH: I have perceived that the speed in the wire drawing processes has increased tremendously in the past few years to be much higher with up to 50 meters per second. Generally, there have been no major changes with respect to the technology of Wire Drawing. Nevertheless, there is no doubt about the fact that the electrical components are much better and advanced these days. Also, the customer service and convenience have remarkably improved over the years with the availability of more remote service and support offers.
WCI: What are the factors and technological capabilities which give a significant competitive advantage to Lämneå Bruk in the Wire industry?
JH: In my opinion, Lämneå Bruk has a major competitive advantage since we purely focus on the wire industry and this is where our passion and expertise lies in as you can tell from our longstanding history. Another major factor is that our team truly has the knowledge and they know the intricate details of each machine and its process. For instance, even our sales team are well-informed about the wire drawing processes, so, this equips them with hands-on experience that is highly beneficial for our international customer base.
I am also proud to say that every part of the Lämneå Bruk machines is manufactured on-site in our workshop in Sweden – right from the first idea to the finished machine. We have full control over the production process; hence, the quality that we bring is very high.
WCI: How would you describe the general outlook of the global Wire Industry and the substantial technologies or innovations which have been providing an impetus to the further growth of the sector? Also, please delineate on the key emerging trends and the anticipated trends you envision for the segment?
JH: The PLC (Programmable Logic Controller) systems and Drives have helped the industry to grow competently in the past few years. Basically, the mechanical aspects are almost the same as before and have not changed much over the years, but the electrical part has made tremendous improvements. Also, the HMI (Human-Machine Interface) screens, they are evolving to get better and better with time. Thus, the machines are becoming more intuitive, effective and operator friendly.
A key emerging trend that I have witnessed in the industry is the inclination towards and demand for bigger units such as 2 – 4 tons spools. Apart from that, the trend I envision for the coming future is the shift towards more automated machinery.
WCI: In view of the crisis brought by the COVID-19 pandemic, how would you describe the impact on the Global Wire sector and the disruptions brought in the supply chain and the demand? How did you adapt in the crisis and the different strategies which enabled the Company in doing so?
JH: With the outbreak of the pandemic and the resultant lockdown, the whole world came to a standstill; orders were either withdrawn or postponed. The entire spectrum of industries could not work for months, and this had certainly created major impacts on the wire industry as well, since we are so connected with the economic development of other sectors such as the automobile industry or construction industry.
Lämneå Bruk was doing fine in the first two months of the lockdown, but, then we were hit hard and we lost almost half of our projected sales. We could not welcome customers to our facilities or follow up with potential new customers. I have to be completely honest here; these are extremely challenging times for probably almost everyone in the world unless one is in online sales.
Luckily, I have built my company on autonomic, independent work processes and trained staff to be flexible and adapt to new situations. This has helped tremendously during recent months. Everyone who could work from home did so and we had conducted regular meetings online. In fact, the productivity and efficiency were much better with virtual meetings for us, as it saved time, and everyone could attend the meeting and had no other commitments. We are known for our excellent customer service and we still wanted to fulfill this expectation and adapt to the “new normal”. As all of our machines are equipped with an internet connection, we could execute entire machine commissioning remotely over video conferencing devices and with the help of Augmented Reality for the customers living in different countries.
We are already selling globally and have no specific market we focus on. However, India is of high importance for us as I see a big growth potential in the coming years.
Furthermore, we have successfully launched an online Factory Acceptance Test (FAT) where the customers are dialed-in live via video conference calls and they can observe the test run of their machine. The team has set up 4 cameras at different crucial points, so the customer could see the critical parts from all angles. For example, for the Fully Automatic Precision Layer Winder, the cameras have been placed at the spooler to observe the spooling-off process and see the behind and front of the basket spool when the wire is spooled on. To allow the customer to focus on one point at a time, he/she can easily choose which camera to look at first or switch between the different views.
WCI: Kindly outline on the different markets you serve and your plans of further expansion to different geographies. How pertinent do you consider the Indian market is for the Company in the present time and what are your views on the potential of the market?
JH: We are already selling globally and have no specific market we focus on. However, India is of high importance for us as I see a big growth potential in the coming years.
We had planned to be present at trade shows in India this year and I had planned several visits myself. Even so, considering the current situation, this probably has to wait until next year, but we are looking forward to expanding more into the Indian market.
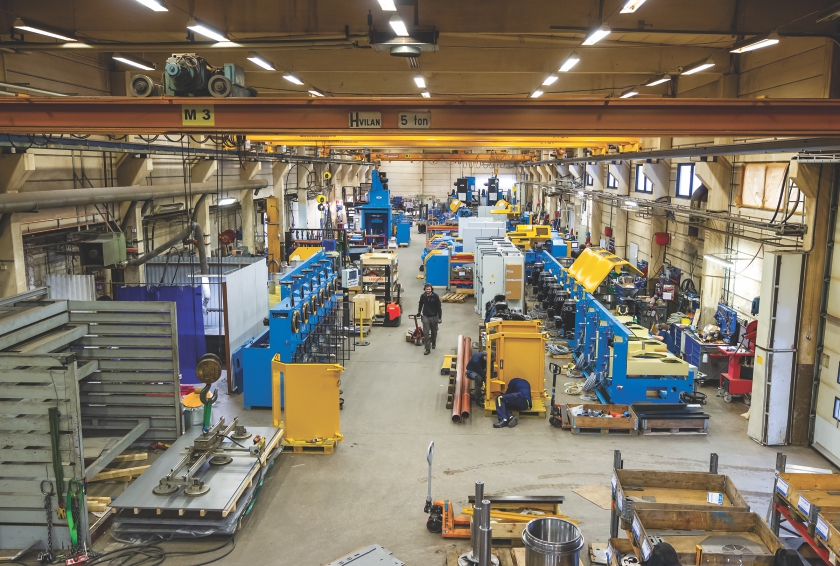
WCI: Has there been any recent development at Lämneå Bruk which you would like to talk about and what are the future plans of the company going forward?
JH: Our major focus is certainly the NTC (No Twist Coiler) Concept. This concept allows not only for a streamlined production line, but also decreases power consumption to produce the wire pack significantly and enables trouble-free pay-off without any power. It allows the user to save space as well as money. Apart from this, with the NTC concept, it is possible to produce very big wire packages, even with extremely thin wire. This aspect is unique to the concept and it has not been possible before.
Another focus for Lämneå Bruk is to launch effective and energy-efficient rod-preparation equipment and to make rod cleaning and preparation more environmentally- friendly.
As I have outlined, I believe that the trend goes towards the demand for more automatic machines. That is why; we are constantly developing innovative and top-notch fully automatic lines, such as our Fully Automatic Precision Layer Winder that can now be purchased together with an automatic palletizing robot – an invention that will make our customers’ lives much easier. The robot checks the total weight of the finished spools that the machine has spooled thoroughly. Should there be any discrepancies, the robot will put the spool aside to get double-checked by the staff and continues with the next spool for an uninterrupted process. If everything is in accordance with the set standards, the finished spools can be moved onto pallets and is packed for shipping.