The Group, with its comprehensive products portfolio in plasticizers and polymers, has a vast network of suppliers, distributors, and customers in the wire and cable industry, and beyond…
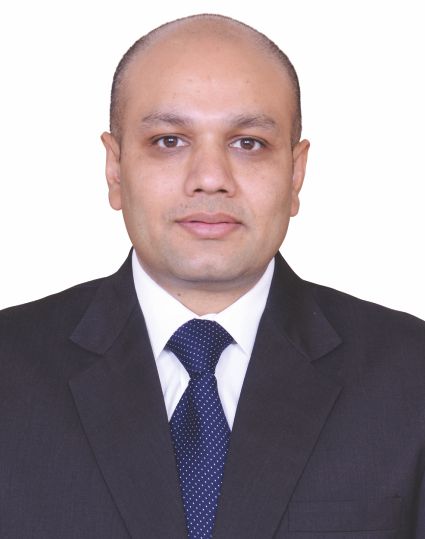
KLJ, incorporated in 1967, is the market leader in plasticizers and polymer compounds in South Asia. With its ultra modern manufacturing facilities at Silvassa and Bharuch in India, and at Rayong in Thailand, KLJ now is in an advanced stage of setting up an ultra-modern Chlor-Alkali plant in Qatar- expected to be upstream by 2016.
KLJ is also diversifying into chemistry of Benzyl Alcohol, Benzaldehyde and its derivatives. The project is coming up in Jhagadia, Gujarat and is expected to be commissioned by end of 2015.
Wire & Cable India recently talked to Mr. Kamal Jain, Director, KLJ Polymers to know more about new developments at product and process front. Excerpts:
Wire and Cable India: To start with, tell us briefly about your journey to becoming the largest plasticizer and polymer compound manufacturer in South Asia.
Kamal Jain: KLJ Group made a humble beginning in the year 1967 by setting up a polymer compound manufacturing unit in Delhi. Within a very short span of time, KLJ achieved good business volumes, even by today’s standards and was seen by customers as an optimum/quick solution provider. PVC compounding requires plasticizers as the key ingredient, and getting consistent quality plasticizers at competitive price was a bit difficult, so the Group ventured into manufacturing of plasticizers as backward integration in 1985. Mainly on account of quality and product innovation, today KLJ Group is the largest manufacturer of plasticizers in South Asia. It would be interesting to note that our compounding activity consumes only about 5 percent of total plasticizers produced by us. Balance 95 percent is sold to both domestic as well as overseas customers in over 80 countries across the globe, a great testimony of faith reposed in us by the industry across the world!!
WCI: You have manufacturing facilities at Silvassa and Bharuch in India, and at Rayong in Thailand. Would you brief us about the produce you get from these facilities respectively? Do the products from Rayong facility reach India?
KJ: In Silvassa, we have two manufacturing complexes; one for primary plasticizers & the other for polymer compound. In plasticizer complex, we produce both generic as well as specialty plasticizers to cater to the requirement of most of the plastic industries. Other industries like coatings, adhesives, perfumery, lubricants, catalysts, etc. also use our products. We manufacture the widest range of plasticizers in the world. For the cable industry, we offer the widest choice of plasticizers, starting from phthalates onwards to cover a very wide spectrum of end-customer requirements like REACh, FR, High/Low service temperature and so on. We are also the pioneer in offering customized plasticizer solutions.
In compounding complex, we do compounding of multiple polymers including PVC, PP, TPR, TPE, XLPE, EVA etc. Besides, we also manufacture color masterbatch for various end applications. We cover a wide range of applications using a number of polymers, at volumes/complexity which are un-matched by anyone in the Indian compounding industry. We serve industries ranging from Wire & Cable, Footwear, Medical, Automotive, Appliances, Engineering, Packaging, Sports, etc. For cable industry, we offer various compounds like PVC, XLPE (both Sioplas & Peroxide upto 33KV), Semicon, MDPE, ZHFR, EPR, etc. apart from color masterbatches (PVC, PE and Universal) meeting a wide range of specifications and statutory requirements.
At Bharuch, we manufacture a wide range of chlorinated paraffins which is used as a secondary plasticizer in PVC compounding, improving FR properties and the cost of the compound. CP also finds applications in industries like lubricants, metal working fluids etc. Very shortly, we are going to start manufacturing Benzyl Alcohol, Benzaldehyde & Benzyl Chloride in the same complex.
At Rayong, Thailand, we manufacture chlorinated paraffins. These are commercially viable to reach India under FTA, but as a strategy, we prefer to export the same to countries other than India. KLJ today holds the position of being the no. 1 manufacturer of the CP in the world in terms of all: volumes, product range and product quality – a rare distinction for an Indian company in the industry, where No.1 position is mostly dominated by companies from western world or China.
WCI: Being one of the Largest Plasticizer and Polymer Compound maker, which industry does take the biggest pie out of your produce and why?
KJ: In plasticizers, the largest share comes from Wire & Cable and Leather Cloth segments, whereas in compounds, the largest share comes from Wire & Cable and Footwear segment. Not only in terms of volumes, but also in terms of the product range, we have the options of servicing our customers with more products than our peers in the industry!!
WCI: Coming to your supplies to the wire and cable industry, we are keen to know the applications where your plasticizer and polymers are extensively used. Tell us separately for plasticizer and polymer.
KJ: Products of KLJ Group whether plasticizers or polymer compounds, cover very wide range of applications in the wire and cable industry. We remain the preferred supplier for the entire range of applications, starting from normal sheathing or insulation application to more specialized applications like high/low temperature applications, FR, FRLS, AVSS, ZHFR, HRFR applications and so on.
Our development works in very close coordination with the customers to enable both of us to offer new innovations in the market. Our compounds have been developed to suit high speed and thin coating application for PVC as well as Sioplas compounds. Kanatol-HT9 is one such product innovated by KLJ as a cost effective, REACh compliant HR plasticizer, Kanatol-8080 is again an economical phthalate free plasticizer & many more of such innovations.
WCI: Compounding remains one of the most dynamic segments wherein it does not take much time for a compound to become obsolete. What do you do to stay relevant in this fast changing demand scenario regarding polymers and compounds?
KJ: Continuous research and development of newer products for different end applications is a routine at KLJ and this is how we keep growing our volumes despite the market conditions. Our experienced and focused R&D team with their skills and regular knowledge up-gradation through participation in various seminars, interactions to upkeep with developments in raw material side and regulatory environment, provides the required knowledge base to address the fast changing demand scenario regarding Compounds.
Wire & Cable, Medical & Automotive industries are governed by a number of international and national standards, hence it is imperative that R&D does the required development keeping in mind all the perspectives required for the approval including the specifications/cost requirements and at a pace demanded in such competitive world. KLJ puts great attention of its R&D infrastructure in terms of people and hardware to achieve and retain its leadership position. Today, the cable industry is gearing up to match the international standards of quality and productivity by making huge investments in creating world class manufacturing plants. The customer today is more educated to invest in best value in the electrical products in buildings rather than simply going for the lowest cost option. It is a constant endeavor at KLJ to satisfy new challenges posed by the customers, regulations and the consumer market at large.
WCI: Most of the compounding industry keeps facing the heat of environmental regulations. How does KLJ perform or strive to perform on these environmental fronts?
KJ: KLJ manufactures generic compounds as well as the compounds meeting specific environmental regulations. Our product range includes RoHS, REACh compliant & Phthalate free compounds apart from country/customer specific compliant products. In India the environmental regulations are more practical and less in number, unlike some developed countries where simply they are perceived, by other countries, more as a trade barrier rather than anything else, given their complicated nature and prohibitively expensive and time consuming nature of approvals.
WCI: What about safety regulations?
KJ: Product safety is another aspect where we seem to have adequate regulations in the Industry. They can certainly be upgraded to be closer to the international standards. The bigger challenge we face is in retaining the product safety at the point of the use of our wires-cables, to ensure that even the smallest manufacturer of wires-cables respects the compliance of the safety of product and process. Public awareness about the safety should be improved through media, camps, road shows, better vigilance by authorities.
We at KLJ have devoted sufficient and un-paralleled resources, both in terms of hardware and highly skilled manpower at our plants, to ensure that our product comply with all the required specification for quality, environment and product safety. It is our firm belief that the path to holistic and sustainable growth has no room for short-cuts and compromises.
WCI: Your chlor-alkali plant in Qatar was supposed to be upstream by 2016. What is the status and where one does find the usage of chlor-alkali?
KJ: The construction activity at Chlor-Alkali plant in Qatar is on and if all goes as per plan, the project is likely to be upstream by last quarter of 2016. The main products would be caustic soda, calcium Chloride and chlorinated paraffins. Caustic-chlorine are one of most basic and widely used chemicals in the world, finding application in plastics, textile, metal refining, water purification, paper, soaps, etc. Their link to the wire-cable industry is through PVC, CP where chlorine is used and Aluminium refining where caustic soda is used.
WCI: Tell us something about the project related to Benzyl Alcohol, Benzaldehyde and its derivatives, which is expected to be commissioned by end of 2015. Also, brief us about the targeted industries and applications for your new chemistries.
KJ: The project related to benzyl products is under advanced stage of commissioning and is likely to commence production w.e.f. Jan 2016 initially with two products benzal-dehyde and benzyl alcohol. Other derivatives like benzyl chloride and sodium benzoate are likely to be added thereafter. The targeted industries are pesticides, pharmaceuticals, perfumery, soaps, flavours & fragrances, dyes, paints & inks, etc.
WCI: Do you wish to add something, not covered by above questions?
KJ: I would just like to add that as WCI is doing its bit to bring together the wire and cable industry, same way KLJ Group is doing its bit to add value to the plastic industry. We also take this opportunity to thank our customers for the faith and trust reposed in us and in making us the pioneers in the fields that we work in. Our guiding principles such as Trust, Innovation and Accessibility will always lead us to the path of achieving customer satisfaction.
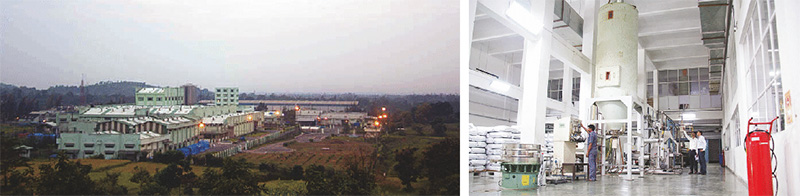