“The biggest trend in India is the electrification of the railway system. We are hopeful that something will move forward in this area. We had productive conversations with some people in recent times. We hope to have similar conversations this year as well. Also, we hope to supply our equipment to an Indian manufacturer who would make trolley wire,” says Jens Kieselstein, Managing Director, Kieselstein International GmbH, in an interview given to Wire & Cable India.
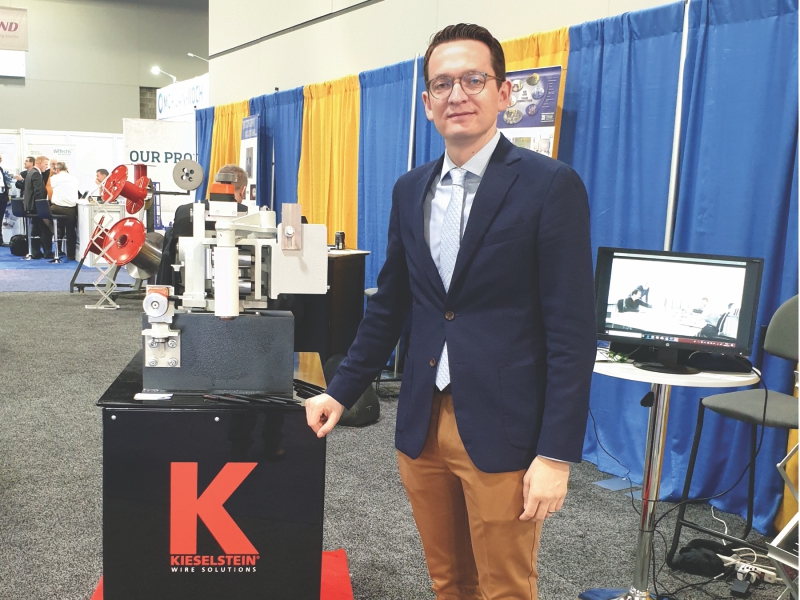
Wire & Cable India: What new developments are taking place in your company?
Jens Kieselstein: Our Company is well known for wire shaving, peeling and drawing of trolley wire for contact wire for train tracks. We have increased our range for the shaving application. The minimum we can do now is 0.8 mm, and the maximum is 35 mm, with different kinds of equipment. So, with that we cover the entire market for non-ferrous wire and steel wire. In trolley wire, we have improved the entire line concept. We are now running high-speed on production line, which means that our equipment is three times faster than the equipment available on the market. This enormous increase in productivity is an important factor when it comes to analyzing the efficiency of a plant investment. We have reached it by the cooling concept of the machine to avoid high temperature, which is a critical factor in the manufacturing of trolley wire, because if the material gets too hot, you lose tension in the material.
WCI: Could you elaborate on the cooling concept?
JK: We considered the existing lines that we had supplied in Europe and China and discussed them with the R&D departments of our customers’ mostly in Japan and Europe. Through these discussions we identified the critical points: It’s the area where the tool is; it’s the temperature of the lubricant; and the capstan. On the capstan, in the past, cooling was not applied directly to the wire. So, we improved it by an additional outside cooling system to make cooling highly efficient. That is a key point in getting the temperature low.
WCI: Are you planning to go for further developments in your company?
JK: We are looking at the product lines in other applications. We have built our first machine to draw tubes. It’s a coil-to-coil drawing line for tubes. We also do machines to produce mesh, especially mesh for aqua culture for fish farming – that is a complete new development. We have also improved our system to slit mesh for filters. So, we are diversifying the market for us.
WCI: What are your views on the market in India? What market trends have you noticed there?
JK: The biggest trend in India is the electrification of the railway system. We are hopeful that something will move forward in this area. We had productive conversations with some people in recent times. We hope to have similar conversations this year as well. Also, we hope to supply our equipment to an Indian manufacturer who would make trolley wire.
WCI: I understand that you have supplied some major equipment to one of your customers in India in the recent past. What have you to say for it?
JK: Not long ago, we got orders from an existing customer in India for a shaving line. The line is currently giving the best possible results, and the customer is quite pleased with it. It is new technology for him. We also introduced him to efficient tools and lubricants suppliers so that he could procure the right tools and lubricants for the line.
WCI: Is this customer Raajratna? Would you like to elaborate on it?
JK: Yes, you are right about the customer. This line was a coil-to-coil shaving line for removing surface defects and any imperfections from the surface of the stainless steel wire that is produced. That is a requirement if, for example, you want cold-heading, aerospace or automotive to have a high-quality wire. Basically, the use of shaving gives you the opportunity to use, let’s say, a different quality of material. ‘Different quality’ means that lower quality, which can be purchased at more attractive prices, has a higher number of imperfections on the surface and you remove these imperfections through the shaving technology. We have a laboratory in Germany where we run two shaving lines and other kinds of equipment. We invite our customers to send us their materials or to take a look at the technology we use. And that is what we did for Raajratna. They came to us with some material, and we did the rest. Before they made a decision, they were convinced that we knew what we were doing.
WCI: How important is R&D to you?
JK: R&D is enormously important to us. Machine manufacturers usually have an engineering department where they have electrical and mechanical engineers. We have an engineering department but we work differently. In addition to having an engineering department, we have an R&D department, which started with just one person. It currently has five people working in it. We look into technology and material development; for example, in cooperation with a producer of cold-heading parts. It may interest you to know that we have developed a complete technology for developing magnesium wire for screws with a university. Our location in Germany is quite advantageous because we have quite a few institutes and universities here. We have good relations with them; and if we want to conduct material testing or special investigation, it is easy for us to do it in a short period of time. We constantly look for improvement in any kind of market. We do a little bit of digitalization and software things to improve our machines and products. So, that is what we do in these departments.