Demand Move in Lockstep
Innovation trends in wire and cable machinery are being driven by complex demands from rapidly evolving consumer industries. To address these challenges, manufacturers are incorporating advanced materials, automation, and precision engineering to boost efficiency, sustainability, and performance.
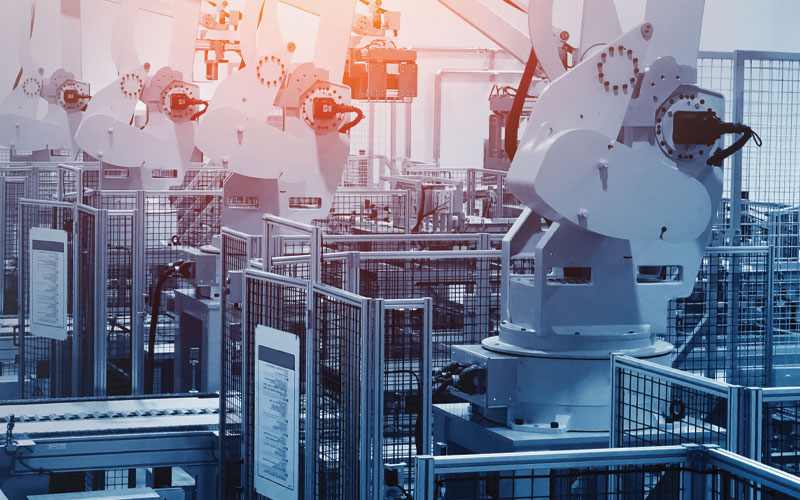
Cables, a Rather Complex Technological Product
Technology travels a long distance before reaching its application in wire and cable manufacturing. Countless innovations work together in sync, transforming raw materials into high-performance conductors and insulators, finally becoming the wires and cables that we see. One might wonder the rationale behind using this intricate technological system. The complexity of cable production, meeting modern demands, stems from the interplay of metallurgy, polymer science, and precision engineering. The efficiency and reliability of a cable are affected by many factors. These factors may range from the electrical and mechanical properties of the conductor to the thermal and environmental resilience of insulation and sheathing materials.
Conductors, typically made from copper, aluminum, or specialized alloys, undergo extensive processing to boost conductivity, flexibility, and mechanical strength. Continuous casting, multi-stage wire drawing, and annealing optimize grain structure, thus minimizing electrical resistance. To reduce losses from skin effects and boost performance in applications like high-frequency data transmission or high-voltage distribution, treatments like plating, compacting, and segmental shaping are necessary.
Likewise, insulation and sheathing leverage advanced extrusion techniques, polymer cross-linking, and foaming technologies to achieve precise dielectric properties. These materials must endure mechanical stress, moisture, and extreme temperatures, making them integral to offshore power transmission, industrial automation, and electric vehicle powertrains.
Though we’ve touched on conductors, insulators, sheathing, and their intricacies, that’s just one aspect of a far more complex picture. Cable production’s complexity arises not just from physics and chemistry, but also from diverse market demands for specialized wires and cables. Let’s figure out how.
Watch: Top Cable Companies in India
Dynamic Demand: An Explosion of Cable Types
Grid expansion and renewable energy integration are driving increased demand for HV and EHV cables. These cables need to be efficient in transmitting power over long distances while withstanding high loads and harsh conditions. To reach this goal, manufacturers are using advanced insulation materials such as XLPE and improving extrusion techniques for better dielectric strength and cable lifespan. Sustainability initiatives also aim to decrease waste and energy use, while promoting recyclable insulation.
In addition, the telecommunications industry is experiencing rapid growth thanks to AI-powered data centers and 5G networks. There is a high demand for high-frequency data cables featuring engineered insulation and foamed dielectric layers. Real-time monitoring now enables manufacturers to detect tiny insulation flaws precisely, guaranteeing product consistency. According to Aman Arora, Rosendahl Nextrom’s Head of Sales for India, the boom in AI data centers demands huge numbers of specialized cables.
The automotive industry is also evolving as EVs transition to 800V battery systems and beyond. High-voltage, heat-resistant, lightweight cables are now standard, using hairpin winding and PEEK insulation to boost conductivity and efficiency. Advances in material science and extrusion are improving power density and heat dissipation.
Industrial automation presents another complex challenge, demanding increasingly flexible, EMC-shielded, and ingress-protected cables. The shift toward Industry 4.0 and IoT-driven manufacturing has increased demand for high-speed industrial data cables with superior shielding and real-time monitoring.
The renewable energy sector is another major driver of cable innovation, requiring UV-resistant, corrosion-proof, and highly flexible power cables. These cables must endure moisture, saltwater, and mechanical stress, pushing the industry towards flame-retardant, halogen-free, and recyclable insulation materials. With sustainability at the forefront, manufacturers are optimizing insulation processes and adopting biodegradable packaging to comply with global green policies.
In short, the wire and cable sector is emphasizing efficient energy transfer, robust cables, and environmentally responsible production methods. AI, precise measurement, and advanced insulation ensure cables meet the rising needs of modern infrastructure and mobility. But, how do these advanced cabling requirements affect machine manufacturers and technology integrators?
Machinery for Advanced Cabling: A Technological Synthesis
As previously mentioned, cutting-edge wire and cable production requires extensive technological advancements. Machinery experts combine separate technologies to build machines that efficiently produce high-quality wires and cables. With rising demand for specialized cables across power transmission, data connectivity, e-mobility, and automation, the manufacturing technologies are facing constant pressure to become cutting-edge.
Consequently, manufacturers are transforming production by combining advancements in extrusion, stranding, insulation, sheathing, and quality control. Not to say, these new machines are enhancing efficiency and product reliability while aligning with sustainability goals. Let’s quickly look at innovative developments in crucial cable manufacturing fields.
Advanced extrusion technologies play a key role in high-voltage power cables, fiber optics, and automotive wiring. Wire and cable manufacturing fundamentally relies on extrusion for the precise application of insulation and sheathing materials to conductors. Maintaining material integrity and performance requires strictly controlling temperature, pressure, and cooling rates during the process. Advanced extrusion lines incorporate multilayer co-extrusion, cross-linking techniques, and real-time monitoring systems to enhance efficiency and quality.
AI-powered automation within the extrusion process guarantees consistent insulation thickness and excellent electrical performance. In EVs, specialized PEEK extrusion is widely used for hairpin winding, reducing energy loss and improving system efficiency. Aman Arora of Rosendahl Nextrom explains, “Hairpins in electric vehicle stators allow for higher voltages, thus decreasing energy loss and improving motor efficiency and reliability. Mikko Lahti, Maillefer’s R&D Director, highlights key developments such as energy-efficient extrusion and cutting-edge insulation/sheathing technologies for minimizing excess material.
High-precision measuring and quality control systems are critical for maintaining strict performance standards. Advanced tools, including X-ray scanners, ultrasonic gauges, and optical diameter measurement systems, are essential for real-time monitoring of insulation thickness and detection of inconsistencies. Non-destructive testing of cable cores is achieved through X-ray solutions, whereas ultrasonic testing guarantees proper adhesion between insulation layers. Additionally, high-speed laser micrometers deliver precise outer diameter measurements, helping manufacturers maintain tight tolerances.
Moreover, laser-based monitoring, capacitance testing, and AI-driven defect detection improve consistency and reduce waste. Real-time monitoring identifies deviations early, ensuring that high-performance cables for power distribution and data transmission meet stringent specifications. SIKORA, a producer of high-tech measuring tools, emphasizes, “It’s the single value accuracy that matters, not an average of multiple measurements.”
Stranding, bunching, and coiling innovations have optimized power transmission cables and industrial wiring. Flexibility, conductivity, and mechanical strength are improved by twisting multiple wire strands together in these processes. Stranding can be done in concentric, compacted, or sectoral formations, each suited to specific applications. Bunching, mainly used with flexible cables, creates even strand distribution; coiling precisely winds cables to avoid tangles and damage.
Real-time tension control and automated splicing in modern coiling and rewinding machines lead to more consistent production. The adoption of no-twist coiling technology minimizes handling damage and enhances storage efficiency. According to Jonas Hagsted, President, Lämneå Bruk, “Our flagship innovation, the No Twist Coiler (NTC) portfolio, has been in development since 1992 and has transformed wire manufacturing worldwide. It significantly boosts productivity without requiring changes to existing setups.”
Continuous casting and rolling (CCR) innovations have modernized wire rod production through the integration of energy-efficient melting and refining, resulting in decreased power usage. The process begins with liquid metal being continuously cast into a strand, which is then hot-rolled through successive stands to achieve the desired diameter and mechanical properties. In advanced CCR systems, electromagnetic stirring improves metal purity and uniformity, and inline surface treatment minimizes defects and oxidation. In addition, maintaining exact temperatures during rolling creates the best grain structure, which improves the final product’s conductivity and its durability.
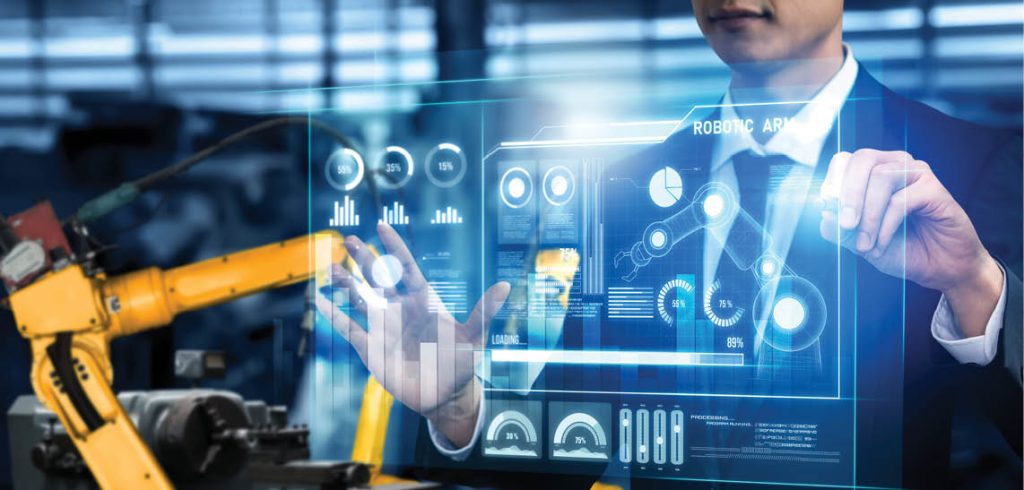
Advanced rolling mills boost conductivity, curb oxidation, and self-annealing technologies slash energy use by as much as 50%. Continuus-Properzi, a major machine maker in this segment, highlights, “We have dedicated particular attention to the reduction of electrical consumption during the casting, rolling, and coiling. Our SAM system enables up to 50% energy savings with no copper dust creation.”
Smart manufacturing, AI, and automation (Industry 4.0) are transforming production. Digital twin technology produces virtual copies of extrusion lines, allowing for real-time simulation and troubleshooting. IoT sensors track key factors like temperature, tension, insulation thickness to maintain consistent product quality. Predictive maintenance algorithms assess machine performance, thus minimizing downtime and averting defects proactively. Automated material handling systems boost production efficiency by reducing waste and improving resource allocation. Production is faster, more efficient, and less wasteful thanks to these advancements. Maillefer emphasizes this transition, stating, “Our new data storage solution will change how manufacturers collect and analyze production data.”
Sustainability and environmentally responsible manufacturing are gaining traction. There’s a growing trend toward using biodegradable insulation, halogen-free flame retardants, and energy-efficient materials. Cable manufacturers are now embracing circular economy principles and reducing plastic waste through recycling. “Sustainability is a top priority for manufacturers,” says Nicola Corti, Sales Director at MFL Group, “with a focus on reducing waste, energy, and materials to minimize environmental impact.” “We have engineered our machines to support biodegradable packaging materials, allowing cables to be securely packaged while reducing environmental impact,” says Dieter Gerger, Sales Manager at Windak, expanding on the subject. “In fact, our latest developments enable cable packaging without any plastic at all—a major step toward a greener future.”
Continued industry progress hinges on precision, automation, and sustainability. Companies specializing in extrusion, measuring systems, coiling automation, continuous casting, and smart manufacturing, such as Maillefer, Rosendahl Nextrom, FUHR, MFL Group, Lämneå Bruk, Windak, SIKORA, Continuus-Properzi, and many others continue to shape the next generation of wire and cable technologies.
Also Read: MFL Group Integrates Sustainability with Technological Advancements
Future Getting More Complex and Miniaturized
The future of wire and cable manufacturing will be shaped by miniaturization, energy efficiency, and intelligent automation. Ultra-thin, high-performance conductors made from advanced composites will enhance conductivity and heat dissipation while reducing material consumption. Energy-efficient cables with minimal transmission losses will be vital for renewable energy grids and smart infrastructure.
AI-driven predictive maintenance and smart monitoring will revolutionize production, enabling manufacturers to detect failures early, reduce downtime, and optimize efficiency. Digital twins and software-based process control will ensure continuous improvements in quality and sustainability. Growing global infrastructure and technology needs will drive the industry towards creating smarter, more durable, and energy-efficient cables for a more interconnected and electrified future.