We need to use cables that can prevent not only fire propagation but also the first spark that gives rise to a big fire.
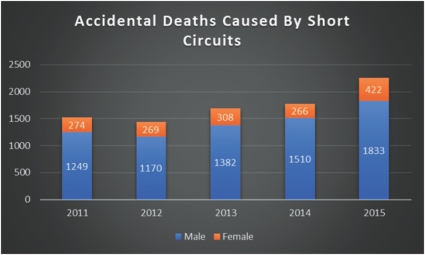
Fire accidents, if not handled carefully, can result in loss of life and assets. In India, fire outbreak is the third biggest risk to business continuity and operations (India Risk Survey 2018). Fire accidents have been increasing in number over the years and authorities have repetitively failed to implement policies to reduce or stop fire-related accidents. It is therefore necessary to take special measures to avoid fire accidents.
Deaths due to fire caused by electrical short circuits accounted for 12% of total accidental fire-related deaths in 2015. In 2011, such deaths accounted for 6% of the total fire-related deaths. In all of these fatal short-circuit accidents, most of the victims, or a median 81%, were male. (Graph 1)
Statistics by National Crime Record Bureau on fire accidents in buildings attribute 42% of such accidents to electrical issues. In 2015, 2,255 people died due to accidental fires caused by electrical short circuits. This was a 25% rise from the previous year and a 48% jump from 2011.
According to another data provided by Indian Copper Association India (ICA-India), the year 2016-17 witnessed 11,444 electrical accidents. Of this, 4,799 caused deaths while 2,309 resulted in injuries and yet others involved deaths of 4,296 animals.
The increasing number of accidents related to electrical issues needs urgent attention now. New appliances, gizmos and gadgets are increasing the load on India’s outdated electrical infrastructure, which needs major overhauling. Lack of upgradation has led to fire accidents due to short circuit. Therefore, we need to use cables that can prevent not only fire propagation but also the first spark that gives rise to a big fire.
Accidents related to electrical issues can be prevented by using materials with superior thermal properties, such as fluoropolymer consisting of PTFE/FEP/PFA, as insulation. Such a material may also include a sheathing material on top of it.
It should be noted that fluoropolymers have excellent thermal properties and an outstanding current rating. Depending upon the type of fluoropolymer, the wire is able to withstand very high temperatures, even up to 260OC. Even after the melting temperature, fluoropolymer insulation tends to cling on to the wire and remains there till disturbed, protecting the conductor from the environment, nearby wires and short circuiting. Low dielectric constant of fluoropolymers also causes lower energy losses and high dielectric strength. The synergy between fluoropolymers and the high abrasion-resistant sheathing material also enhances the life of the product.
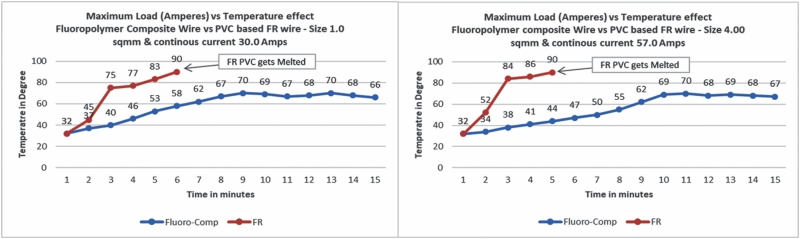
The following graph 2 shows a comparison between a normal FR wire and a fluoropolymer composite (Fluoro-Comp) wire for sizes 1.5 mm2 and 4mm2. As the comparison clearly shows, regular PVC FR melts completely at 90OC in around 8 minutes, while Fluoro-Compwire sustains all the way up to 120 minutes; also, the superior heat dissipation property of the Fluoro-Compwire keeps the temperature below 70OC with continuous current transmission. Increasing temperature also warrants an increase in the resistance of the wire.
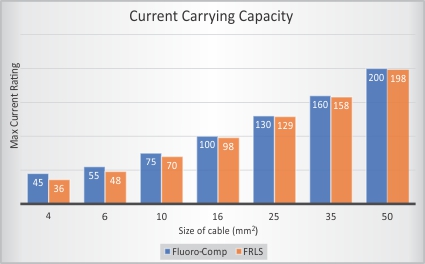
Good thermal properties of the wire also confer excellent current rating on the cable. The graph given below shows a thorough comparison of the maximum current ratings of fluoropolymer composite and PVC-based Flame Retardant Low Smoke (FRLS) cables. (Graph 3)
In view of increasing cases of deaths caused by electricity-related fire breakouts, we need to go for a new course of action. Fluoropolymer composite wires can surely be a panacea for fire breakouts caused by sparks, low efficiency and high temperature in cables.
– Written by Anurag Gulati and Pranjal Pathak