With a legacy spanning 65 years, Finolex Cables has established itself as a beacon of innovation and excellence in manufacturing. The company is set to establish a new facility for E-Beam technology in the field of wire & cables. The company also plans to set up a new solar cable plant and is set to commence shipments to the market next month. Despite being in the initial stages of its journey, they have set a target to capture at least 15 percent market share over the coming 2 years, revealed Mr. Amit Mathur its President of Sales & Marketing while interacting with Wire & Cable India.
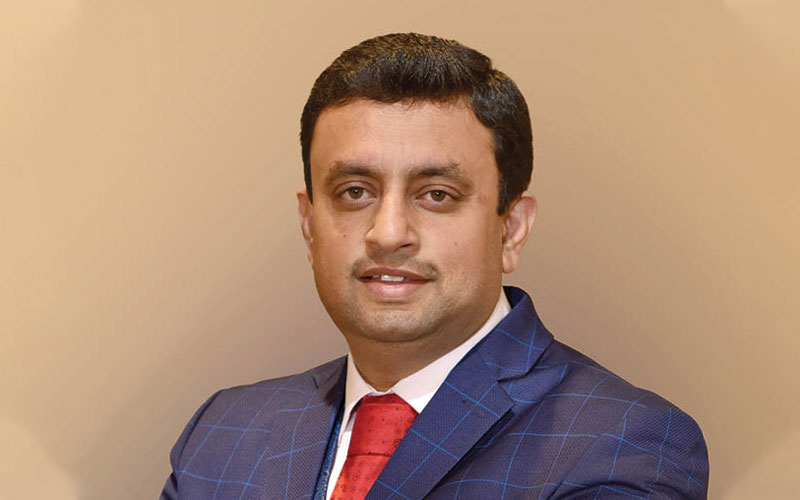
Wire & Cable India: How much has the Indian solar wire and cable segment evolved over the years, and how are you positioned as a manufacturer in it?
Amit Mathur: The shift towards sustainable products is promoting innovation and investment in sustainable solutions. The government’s as well as industry’s efforts have helped India achieve the fourth position globally in overall installed renewable energy capacity, which has increased by 286 percent in the last 7.5 years from 2.6 GW to more than 46 GW. Not just this, a few reports published also mentioned that the government has revised the National Solar Mission target of Grid Connected Solar Power projects from 20,000 MW by 2021-22 to 1,00,000 MW by 2022 along with a USD 100 billion investment target. Additionally, the government has pushed the growth of solar energy use, taking a central place in India’s National Action Plan on Climate Change with the National Solar Mission as one of the key programs.
The solar industry is rapidly growing worldwide, and so is the demand for solar cables. In India, the solar energy sector has grown exponentially with the government’s initiatives to promote clean energy sources. According to a report, the global solar cables market was valued at USD 628.2 million in 2020 and it is expected to reach USD 1109.6 million by the end of 2027.
We are investing in the E-Beam curing process to produce our solar cables. All the fundamental properties of a solar cable can be achieved with the E-Beam curing process with improved performance and efficiency. These are manufactured under a continuous operating temperature of 150°C to deliver better UV & ozone resistance, improved weather resistance in adverse conditions, improved oil & chemical resistance, improved crack resistance, long-term heat ageing, fire hazard reduction, higher insulation resistance, longer service life compared to conventional cables.
WCI: How significant is the solar segment for you? Please take us through your solar product portfolio.
AM: Finolex Cables is in the stage of setting up a new facility for E-Beam technology in the field of wire & cables. Electron beam processing will be employed in the area of cross-linking of wire and cable insulation material. The electron beam-cured cables show enhanced properties to withstand a higher range of temperatures, ozone, weathering/UV, and attack from acid & alkaline solutions. The proposed industrial accelerator radiation processing facility will be used for processing solar cables, high-temperature automotive cables, and high-temperature halogen-free electrical wires etc. Electron-beam accelerators utilize an on-off technology, with a common design being similar to that of a cathode ray television.
WCI: Based on end-users, such as residential, industrial and commercial, where do your solar cables experience more demand? Why?
AM: In India, the largest application of solar energy is in the utility-scale or large-scale commercial sector, rather than residential or industrial sectors because the government has been actively promoting solar energy through various policies and initiatives aimed at scaling up solar installations. This includes incentives, subsidies, and targets for utility-scale solar projects. Policies like the National Solar Mission (Jawaharlal Nehru National Solar Mission) have focused heavily on utility-scale solar installations to achieve significant capacity additions. Moreover, utility-scale solar projects benefit from economies of scale, where larger installations can often achieve lower per-unit costs compared to smaller residential or commercial installations making it more financially viable for developers and investors. In addition, India has vast areas of land available, especially in rural and semi-rural regions, which are suitable for large solar farms. These areas can accommodate the sizable land requirements of utility-scale solar projects, which typically require several hectares of land. The government is also encouraging grid integration whereby utility-scale solar projects are getting integrated into the existing power grid infrastructure. These projects contribute significantly to the overall electricity generation capacity and can be strategically located near existing transmission infrastructure, reducing transmission losses and improving grid stability.
Government agencies, utilities, and independent power producers (IPPs) typically enter into long-term Purchase Power Agreements for utility-scale solar projects. These agreements provide revenue certainty and financial stability, encouraging investment in large-scale solar projects. Advances in solar technology, such as improvements in efficiency and reduction in costs of solar panels and balance-of-system components, have further favored utility-scale solar installations. These improvements have made large-scale solar projects more competitive in terms of cost per unit of electricity generated. However, with increasing awareness, improving economics, and government incentives, the residential and commercial sectors are also expected to grow significantly in the coming years.
Watch: RR Kabel | Solar Cables | Solar Plant | Renewable Energy
WCI: Where in the country do your products enjoy strong demand? Please elaborate why.
AM: Currently, at Finolex, we are preparing for the launch of our new solar cable plant and are set to commence shipments to the market next month. Our research indicates significant latent demand for our products nationwide. We continuously elevate our standards by integrating cutting-edge technology, upgrading our facilities, and upholding the highest benchmarks in quality and service.
As one of India’s foremost electrical and telecommunication cable companies, we are evolving rapidly from a wires and cables manufacturer to a comprehensive electrical products company. Our expanded portfolio includes diverse offerings such as lighting, water heaters, fans, switches, switchgear, room heaters, irons, electrical conduits, and smart home solutions. Currently, Finolex products are available through an extensive network of 2,00,000 retail outlets, supported by over 800 distributors and 5,000 channel partners nationwide.
Traditionally, our stronghold has been in the southern states, contributing approximately 45 percent of our sales, followed by the Western region, with the North and Eastern markets key areas of focus.
WCI: What technologies have you incorporated into your manufacturing facilities to produce solar wire and cable? How unique are they?
AM: The ELV-type accelerators were designed with the use of the unified systems and units enabling us to adapt them to the specific requirements of the customer by the main parameters such as the energy range, beam power, length of extraction window, etc. Electron accelerators of the ELV-type covering the energy range from 0.3 to 2.5 MeV with a beam of accelerated electrons of up to 450 mA and a maximum power of up to 400 kW. The design and schematic solutions provide the long-term and round-the-clock operation of accelerators under the conditions of industrial production processes. The main application of ELV accelerators is the modification of polyethylene insulation of cable and wires.
We are preparing for the launch of our new solar cable plant and are set to commence shipments to the market next month. Additionally, Finolex Cables is in the stage of setting up a new facility for E-Beam technology in the field of wire & cables.
WCI: Compared to other wire and cable, how different is the manufacturing process of solar wire and cables?
AM: Common chemical crosslinking agents pose safety concerns and require elevated temperatures to cure. These types of chemical processes can also yield noxious fumes and/or sensitizing by-products and require regulated disposal. Chemical crosslinking processes are affected by a large number of variables and imperfect process control can result in significant product loss.
Conversely, the crosslinking facilitated by E-Beam processing does not require using additives nor does it generate hazardous chemical by-products. E-Beam crosslinking is energy efficient. Since the exposure time of the material to th is minimal (seconds), high throughputs are typical. E-Beam technology is precisely controlled and the degree of crosslinking is directly related to the level of E-Beam exposure. E-Beam crosslinking is suitable for polymers that are difficult to crosslink chemically.
WCI: How sustainable are your products? Please ensure the process you have adopted to achieve it?
AM: E-Beams are a cleaner and more environmentally friendly option. The process does not involve the use of hazardous chemicals, reducing the generation of harmful by-products and minimizing the overall environmental impact of cable manufacturing.
WCI: Given India’s ambitious 500GW renew able energy target and solar wire and cable being the lifelines of the solar power system, what kind of growth prospects are you staring at?
AM: Overall, the Indian solar industry is set to experience robust growth driven by favorable government policies, technological advancements, declining costs, and increasing investor confidence. This growth trajectory positions solar power as a critical component of India’s energy future, contributing to sustainable development and energy security. Though we are currently in the initial stages of our journey, we expect our solar wire business to grow in double digits year on year. The target is to capture at least 15 percent market share over the coming 2 years.
Also Read: Prysmian: Leading Energy Transition with Cabling Solution
WCI: Discuss some of the major challenges you have been experiencing as a manufacturer in the industry? What could help overcome them?
AM: As a manufacturer, multiple challenges must be navigated to maintain competitiveness and growth. This includes managing fluctuations in the prices of raw materials, such as copper and PVC that significantly impact production costs. Managing these costs while maintaining product quality and pricing competitiveness is a constant challenge. We also need to continuously invest in technology and machinery to enhance manufacturing efficiency, product quality, and meet evolving customer expectations. Balancing these investments with financial constraints can be demanding.
Moreover, the Indian cable industry is highly competitive with numerous players in the organized and unorganized sectors. Differentiating products through innovation, quality, and service is vital for market differentiation and customer retention. The market is constantly evolving, we all need to understand and adapt to market trends, customer preferences, and demand fluctuations by introducing innovative new products. Rapid changes in technology and customer expectations require agile responses to stay ahead in the competitive landscape.
Last but equally important is managing infrastructure gaps, especially in remote or rural areas that hinder distribution and market reach. Improving connectivity and infrastructure development are crucial for expanding market penetration.
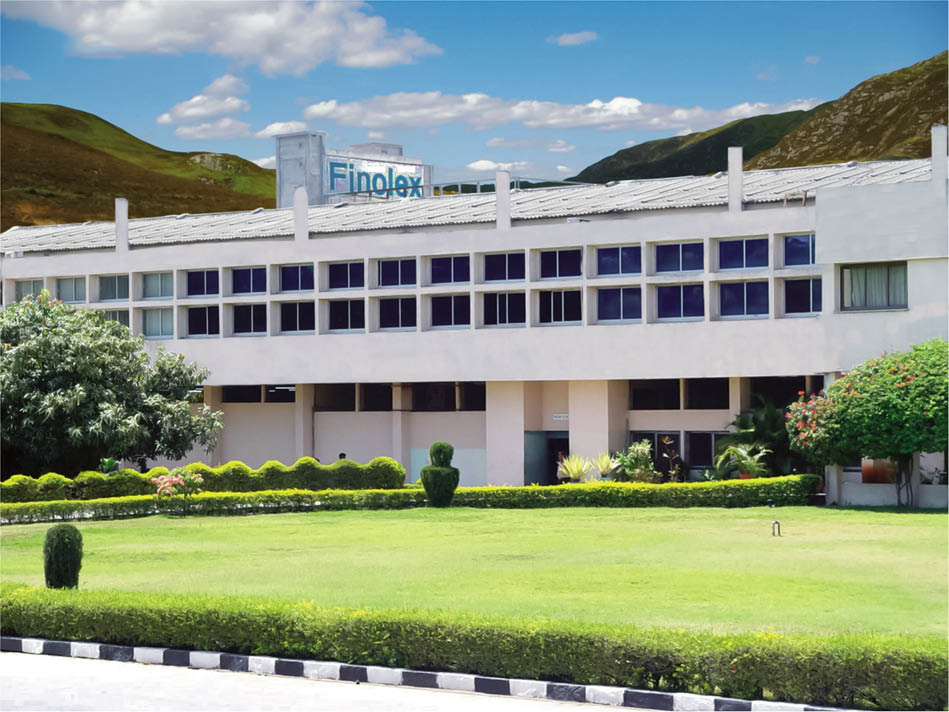