Leading manufacturer of optical fibre cables in India, Finolex Cables, is committed to providing innovative communication products and latest technologies in optical fibre field like FTTH, armoured, unarmoured, aerial, ADSS, ribbon, spiral armoured, and simplex/duplex cables. Mr. Sunil Upmanyu, President – Operations, Finolex Cables Limited, revealed during an exclusive interview with Wire & Cable India that the company looked forward to expanding its presence in data centres, microduct cables, higher fibre count ribbon cables with intermittently bonded ribbon technology, rural telephony, sensing, and perimeter detection systems.
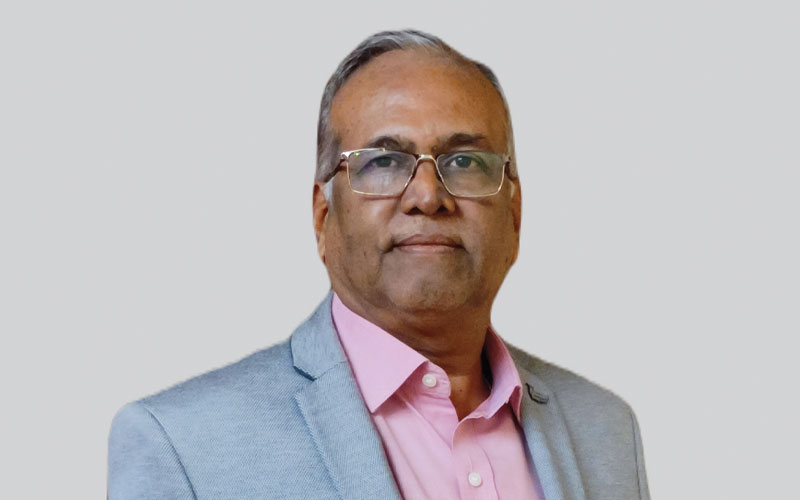
Wire & Cable India: What types of fibre optic cables do you offer, and how do they differ in terms of performance and application?
Sunil Upmanyu: As a comprehensive cable solutions provider, we manufacture a wide range of optical fibre cables (OFCs) at our two plants located in Goa and Maharashtra, products of which are certified by Mandatory Testing and Certification of Telecommunication Equipment (MTCTE). Our product portfolio includes designs such as direct burial cables with corrugated steel tape armoring, suitable for telecom, highways, and utility sectors. We also produce wire armoured cables, featuring either steel or plastic tubes, designed for rugged applications, including use in challenging terrains like river crossings. Additionally, we specialise in developing and supplying IGFR (impregnated glass fibre) armoured cables, which are non-metallic and widely used by leading telecom operators.
For urban areas, our unarmoured duct cables are preferred by telecom companies and contractors where cables are laid inside ducts. We also produce high-capacity ribbon optical fibre cables in both armoured and unarmoured designs, with capacities of up to 1728 fibres, catering to data centres and the telecom sector. In regions with difficult terrain, such as hilly areas or river crossings, we manufacture aerial cables with various properties, including anti-tracking for power lines and ADSS cables with anti-bird bite features.
We also produce simplex & duplex cables for patch cords used in data centres, adhering to global standards. Our spiral armoured cables meet the needs of tower fibreisation, and our optical fibre cables are approved by all major telecom operators for the Fibre-to-the-Antenna (FTTA) applications. Furthermore, we manufacture and export microduct cables to various international markets.
All our designs can be customised to meet specific requirements such as high tensile strength, anti-termite and anti-rodent properties. We also have expertise in manufacturing riser cables and various dry & wet designs for industries such as nuclear plants, oil refineries and pipeline projects. Our diversified portfolio serves telecom operators, utility providers, infrastructure companies, tower firms, data centres and system integrators.
WCI: What makes your fibre optic cables unique and efficient in their applications?
SU: The Finolex brand is synonymous with quality. Our plants benefit from the backward integration of key raw materials like glass roving and FRP (fibreglass reinforced plastic), which helps us in maintaining high-quality standards while also offering competitive pricing and timely delivery. We produce our own optical fibre, which is MTCTE/CACT-approved and well-accepted by all telecom operators. Our product range includes low-loss G652D fibres for long-haul and NLD networks, as well as bend-insensitive G657A1 and G657A2 fibres, along with 200-micron low-loss fibres for micro duct cables, meeting the needs of FTTH (fibre to the home) and last-mile applications.
Watch: RR Kabel | Solar Cables | Solar Plant | Renewable Energy
WCI: What state-of-the-art technologies do you use in manufacturing your fibre optic cables?
SU: Our plants are certified with multiple ISO standards, including TL 9000 and ISO 9001, ensuring that our cables are manufactured according to the highest global standards and practices. We use advanced machinery sourced from top global suppliers to produce optical fibre and optical fibre cables that fully comply with customer specifications. For preform manufacturing, we have adopted the Vapour Axial Deposition (VAD) process, a technology commonly used by leading Japanese fibre optic companies. Currently, we are the only company in India using this state-of-the-art technology for mass production of single-mode low-loss bend-insensitive optical fibres.
WCI: In what sectors do your fibre optic cables find major applications, and what additional sectors are you targeting?
SU: Our fibre optic cables serve a wide range of sectors, including telecommunications, internet service providers, infrastructure, highways, railways, oil & gas, power, defence, control and automation, and any other sector requiring reliable communication solutions. Looking ahead, we aim to expand our presence in data centres, microduct cables, higher fibre count ribbon cables with intermittently bonded ribbon technology, rural telephony, sensing, and perimeter detection systems.
WCI: How do you coordinate with clients during installation, and what challenges do you encounter?
SU: We have launched a new vertical offering optical fibre cable installation services to provide our customers with end-to-end solutions. We have begun operations in a few states and are focusing on gaining strength and experience in this new venture. Our commitment to quality has earned us the status of a key deployment partner with one of India’s leading telecom operators. We are also exploring the use of the latest technologies in fibre optic laying and deployment, similar to those used in developed countries.
“Recent advancements in fibre optic technology include the development of 200-micron fibres, which are smaller than the standard 250-micron fibres, offering enhanced performance and space savings.”
WCI: Do you offer any warranties or guarantees on your fibre optic products and services?
SU: We take pride in maintaining a track record of zero complaints related to optical fibres over the past 20 years. Most complaints we receive are typically due to transportation damage or improper handling. We use only the best and virgin raw materials, which result in negligible complaints. Nevertheless, we offer warranties covering manufacturing defects and also provide defect liability for our service offerings, particularly in the EPC segment.
WCI: What are the latest advancements in fibre optic technology, and how do they benefit users?
SU: Recent advancements in fibre optic technology include the development of 200-micron fibres, which are smaller than the standard 250-micron fibres, offering enhanced performance and space savings. Additionally, bend-insensitive and low-loss fibres are gaining traction. Other innovations include combining G652D and G657A1 fibres, along with large MFD G657A2 fibres and intermittent bonded flexible ribbons. Multi-core fibres are also being developed globally, which will enable higher fibre counts, space efficiency and increased data-carrying capacity.
WCI: How important is sustainability to your operations, and what initiatives have you undertaken?
SU: At Finolex, quality is integral to our operations. We have a 5 MW solar power plant dedicated to captive consumption, allowing us to produce optical fibres and optical fibre cables at our Urse plant in Maharashtra using green energy. This initiative also benefits our customers by contributing to their sustainability goals. All our plants are ISO 14001:2015 certified for environmental management systems. To reduce wood consumption, we supply OF cables in coils wherever possible. Our packing materials are made of polyethene bags used with a minimum thickness of more than 50 microns and are recyclable. We also reuse spools and packing materials for optical fibre spools to minimise plastic and paper usage.
Also Read: West Coast Optilinks: Connecting the Future through Digital Infrastructure
WCI: What are the major challenges you frequently encounter?
SU: Everyone is aware that the global supply chain disruptions caused by geopolitical factors, including currency fluctuations and shifts in raw material prices, present significant challenges. Additionally, frequent changes in demand across various segments further complicate our operations.
WCI: How are you positioned in the market in terms of market share and production capacity?
SU: Finolex is one of the few companies in India with its own preform manufacturing facility, marking a significant step in backward integration. We are among the top four optical fibre cable suppliers in India in terms of market share and production capacity. Our products are recognised for their high quality and reliability, making us a trusted supplier for all major telecom operators in India.
WCI: How do you view the Indian optical fibre cable market in terms of growth and product diversification, and what is your outlook for 2024-25?
SU: The optical fibre cable market in India holds great growth potential, particularly with the increasing demand for data-driven by the implementation of 5G and the need for tower fibreisation, which is currently among the lowest in the world. A significant growth driver is the government’s initiative to provide digital connectivity in rural areas. For instance, BSNL has issued a tender under the BharatNet project for middle-mile network connectivity, requiring over 10 lakh kilometres of cables in the next three years. Additionally, the rising number of data centres across the country is expected to further drive demand. Despite the ongoing consolidation and challenges in the Indian OFC market, we are on a growth trajectory due to our strengths and capabilities.