Excel Craft’s strength lies in building the complete machine by itself, from design and engineering to the development of software and other devices, says B. Ganguly
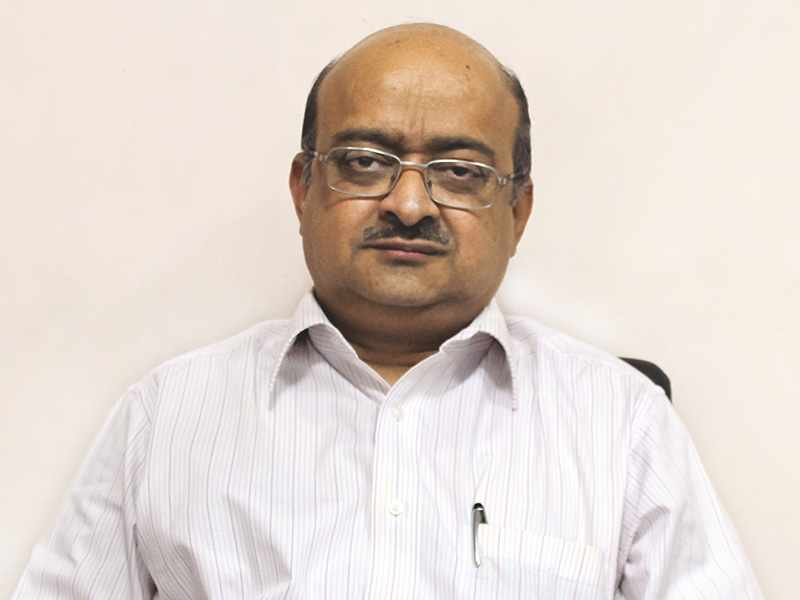
Excel Craft Machineries Pvt. Ltd., incorporated in the year 1994, is a pioneer and leader in the field of manufacturing wire and cable making machines. The company started initially as a joint venture with m/s Redaelli Techna Mechanica Group, Milano, Italy, who pioneered many developments in wire and cable machinery. Excel Craft is engaged in manufacturing of wire drawing for ferrous and non ferrous material, drum twister lines, rigid stranding machines, lrpc lines, tubular stranding, skip stranding, bunching and twinning machines etc.
Mr. B. Ganguly, Chief Operating Officer, Excel Craft Machineries Pvt. Ltd. Recently spoke to Wire & Cable India on a host of issues including the company’s present machine making involvements. Here is brief:
Wire & Cable India: Tell us briefly about Excel Craft and its evolution to current identity.
B. Ganguly: To start with, it was a 50:50 joint venture with the Italian group Redaelli Techna Mechanica and was formerly known as Redaelli (India) Pvt. Ltd. Later on, Redaelli itself got sold in Italy to another group, who was reluctant to let us use the name as they were not much interested in this line. In 2007, around the time when I joined the company, we changed the name to Excel Craft Machineries Pvt. Ltd.
Basically, earlier, since 1994, the set up in Hyderabad was an assembly set up where the original designs came from Italy along with all the essential components. This arrangement had its own drawback and there were a lot of issues as regards to customization, quality and timing. We wanted to have more independence and control over making of the machines. It became possible with Excel Craft. In the last eight years we have added quite a few different varieties of machineries and accessories which mostly are import substitutes. These were also developed in response to the varying requirements of our esteemed customers.
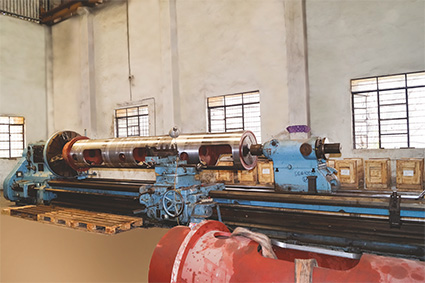
Today we make different kind of machines, all tailor-made as per customer’s requirements, especially the wire drawing and related machineries for the steel wire and rope industry. We design each and every machine as specified by our customers; may be basics we do not change, but certain customization always happens as regards to product and speed.
For the kind of control we wanted in the matters of machine design and manufacturing, we set up a machine shop and a fabrication shop – we increased the factory size to accommodate these two shops. Further, we kept on increasing the number of machines as when you change the design, you need special machines for machining according to the specific design.
WCI: Any project that you have been offered?
BG: We are currently involved in a big project. One of our customers is coming up with a completely new and most modern setup for producing steel wire ropes. The planned capacity is quite huge and I don’t remember any factory of this capacity has ever been built in this time frame for steel wire ropes in India. Apart from us, all other machinery suppliers are from abroad. We are manufacturing almost the entire range of wire drawing machines, high speed tubular stranders, and rope closing machines. The order cumulatively is worth around 450 million rupees. We have also added some machinery to deliver the equipments on time and to international standards as when one is the only domestic supplier, comparisons are bound to be drawn.
WCI: Tell us how you make your machines? What kind of R&D do you do to make your machines uniquely yours?
BG: Today, main technology lies with electronics, unlike earlier years when the machines, especially the wire drawing machines, used to be mostly with heavy mechanical items like heavy worm gearboxes, mostly manufactured in-house, with double blocks and OTO type blocks to take care of speed mismatch, electricals used to be very elementary with slipring motors etc.. Today, the whole concept has changed. For example, gear boxes have now become standard boughtout that you may get from a reputed manufacturer, use it, and build the machines. The entire lines are perfectly synchronized with the latest generation Inverter drives, PLCs, and other electronic devices.
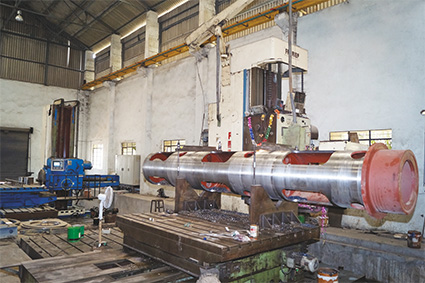
Excel Craft’s strength lies in building the complete machine by itself, from design and engineering, manufacturing (Both Mechanicals and Electricals) to the development of software and other devices. We of course purchase the main building blocks like the gearboxes, bearings, ac drives, PLC etc from the best of suppliers; however we are not much dependent on anyone for anything. Our machines are not only the latest, but are originally ours.
Three years back, we supplied three machines to Tata Steel for their Tarapur Plant and we have been selected beating the competition from all the best manufacturers. However they purchased one machine from the leading Wire Drawing Machine manufacturer from Italy; we can proudly mention that performance wise our machine is at par, if not superior, but there is a huge difference in price.
WCI: What are your strengths that give you an edge over other machine makers?
BG: First, when we shifted from our earlier company to the present one, we got a few people from Usha Martin having experience of 25-30 years in the steel line; this was extremely helpful in designing and building the right kind of machines to suit different applications. Moreover, it is easier to make changes in smaller companies unlike bigger ones. We made a lot of mechanical changes whenever and wherever it suited us to deliver quality technology within timeframe.
One of the major things which make a huge difference between two machines is the cooling system. In the wire drawing systems cooling of the blocks and dies are extremely important as this has direct impact on the finished wire quality and also on the achievable drawing speeds. We have done a lot of work on this front and our block cooling system now is one of the best.
Besides, we have been constantly working on our technology upgradation to make them at par with the international standards.
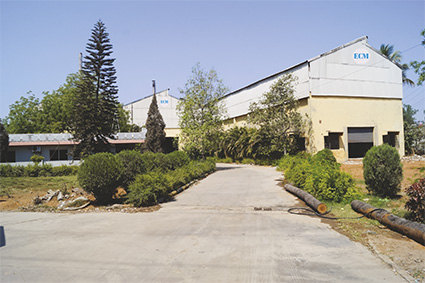
Since we have our own Electronics and Software Development Unit at Bangalore, a lot of work has gone into the Controls area. Our Electronics team has been able to develop special schemes which have enabled us to supply Rotating Machineries in our range like Tubular Stranders, Skip Stranders, Rigid Stranders, and Planetory Stranders etc with all separate drives with a Guarantee of Perfect Synchronized Stop even during any Mains Failure Condition. The moment we could establish this particular scheme all these machines mechanicals have become much simpler and easier to manufacture but adding tremendous flexibility to our machines as regards to lay, line speed and other relevant machine parameters. With this our Controls have become almost at par with any European and Korean Manufacturers.
Price is also a big concern in the Indian market. Here everything moves from cost to technology, not vice-versa, at least for a major part of the market. We have to consider this aspect also and today Excel Craft is able to adjudge a fine balance between quality and price, even when offering customized or tailor-made machines to our customers.
WCI: How do you take the Indian wire and cable industry in terms of technology adoption?
BG: I will talk about our wire customers mainly. All the top steel wire manufacturers are now with us like Tata Steels, Aarti Steels, Kangaro Industries, Rajratna Metals etc.
In this regards I would like to cite a very classical example of Aarti Steels, After we supplied one machine for their tyre bead section around five years back, they realized the benefit of technology and finally we have replaced all the old BB and OTO machines in their Tyre Bead Section and a few at the their Spring wire section. In the tyre bead section around nine old machines were replaced with only five machines.
Introduction of Latest Technology Machines have given multiple benefits :
- Substantial Improvement in the Quality of the Finished Product due to much improved cooling, zero slip drawing (Straight Line Machine), minimum bends, uniform back tension during drawing process etc.
- Huge Energy Saving and space saving.
- Reduction in the no. of Machine Operators with L-H and R-H Machine configurations.
Now, since the industry has seen the advantages of new machines and technology in terms of energy savings and cost optimization, they are now rapidly moving towards it. Now, one operator can operate two-three machines, can you imagine!
Last six years, among our various supplies, we have delivered more than 25 wire drawing machines of different sizes to different customers. Definitely, there is much higher growth happening in India in the steel wire sector as compared to the rest of the world. Customers are also now very quality conscious and with the changing business scenario, which demands most modern and optimized technology in every field, definitely we expect that people will surely go for a little expensive but latest technology, which is available in our range of machinery.