Constantly re-inventing the future of wire drawing, stranding-screening-armoring and extrusion machinery, MFL Group today offers completely integrated turn-key solutions equipped with the latest digital applications required to unlock the entire value of an industrial machinery for wire, cable and rope manufacturers. MFL Group has grown organically and through several acquisitions that have played a role in the steady expansion. This was revealed by Mr. Martino Castelli, Area Manager (Wire and Rope Division) and Mr. Davide Costabile, Area Manager (Wire and Cable Division) in an interaction with the Wire & Cable India magazine.
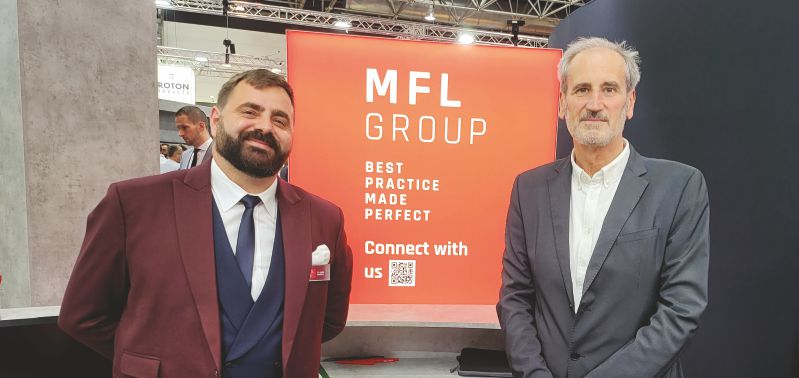
Wire & Cable India: Please walk us through your business journey, highlighting your major milestones and crucial achievements.
Martino Castelli: I joined the MFL Group in 1992 and have been with them for the past 32 years. At the beginning, there were about 40 people and now the figure has increased more than tenfold. Today, our entire group comprises over 450 dedicated employees, spread across six manufacturing plants in Italy, Germany, Spain and China, along with nine sales/service offices in Italy, Switzerland, Germany, China and the USA. We are proud to share that in the past 127 years, we have served more than 2000 happy customers in over 100 countries.
With over a century of experience, we leverage extensive engineering and manufacturing expertise to develop drawing, stranding, and extrusion machinery tailored for wire, rope, and cable production. Whether our customers specialize in wire, rope, or cable manufacturing, MFL Group serves as the only fully integrated partner.
Moreover, at MFL X, we empower our customers to maximize the capabilities of their production lines by embracing cutting-edge technologies such as Industrial IoT, big data, and artificial intelligence. This reflects our steadfast commitment to pioneering Industry 4.0 advancements, ensuring that our customers stay ahead of the curve and elevate both their production efficiency and product quality.
Davide Costabile: Four years ago, I became a part of the MFL Group, but even before that, I had wide experience working with the Indian market. The Indian market is thriving, and we’re highly engaged there. Our expertise in extrusion technology sets us apart in the Indian market, particularly with regard to producing HFFR, XLHFFR, LS0H and PEEK solutions.
Watch: RR Kabel | Solar Cables | Solar Plant | Renewable Energy
WCI: Please tell us about your market footprint in India and your future plans for the Indian market.
MC: In India, it all began in 1993 when we secured a partnership with one of the world’s top rope manufacturers. This collaboration marked our starting point and steady expansion into the Asian market. Today, MFL Group is a trusted supplier to industry leaders in India, providing a comprehensive range of machinery, including steel wire drawing machines, LRPC, and roping lines for automotive, welding wire, and more.
Our commitment to excellence ensures that our machinery delivers high performance while minimizing waste and ensuring cost-effectiveness, quality, and safety. We also collaborate with leading furnace suppliers on galvanizing lines with pay-off and take-ups.
Among our standout products are IT induction tempering lines for automotive suspension springs, which have been successfully deployed not only in India but also in China, Italy, and the US.
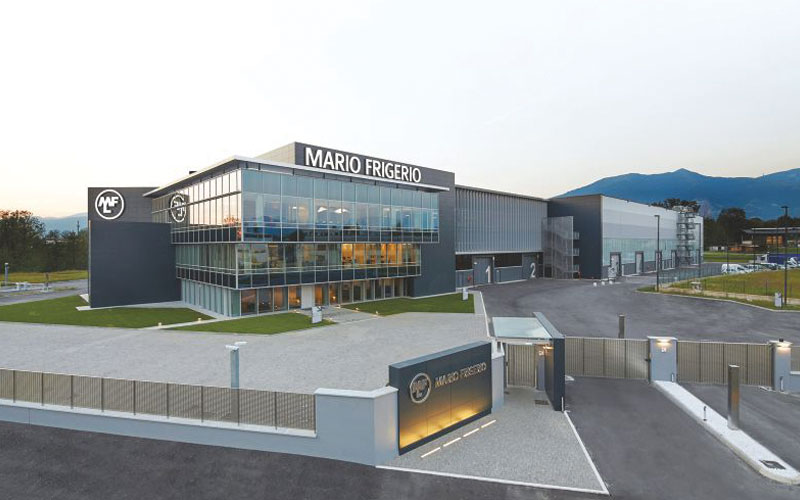
India is one of the greatest newcomers in the LRPC market and is projected to soon become an important player in this sector.
Thanks to visionary Indian companies, the Indian market is witnessing advancements in rod quality, dies, and lubricants, leading to improved final products and enabling better performance during manufacturing. Today, investing in an MFL Group line makes more sense than ever before, due to the long lifespan and the capacity to run higher speed while keeping the same or even better final quality. MFL never cuts corners on quality, and it always pays off.
We continuously enhance our technologies, not only boosting production capacity over time but also capitalizing on technological advancements and material developments. This innovation is further fueled by our close collaboration with the Politecnico di Milano University and the joint research center for metal and transformation technologies, of which we are a co-founder.
Our ongoing efforts include the development of integrated systems that merge mechanical, electronic, and Industry 4.0 elements. Our MFL X applications complement our offerings, combining top-quality and reliable machines with enhanced service assistance and advanced control systems.
India’s current internal increasing demand for infrastructure and logistics presents new opportunities for our group to thrive.
Also Read: Troester Aims to Become Part of India’s Growth Story
DC: Our presence in the Indian market is getting more and more strong. We supplied lines for the production of HFFR/LSZH and PEEK to leading cable producers.
The significant advantage of our machines lies in their exceptional performance and energy efficiency. From my perspective, India stands out as the only country experiencing consistent growth year after year. This is also evident in the significant number of multi-wire machines and extrusion lines we sold to our Indian customers. Additionally, we’re on track to supply rod breakdown machines (RBD) shortly. What we’re bringing to India is the latest in technological advancements.
WCI: Kindly share the recent developments of MFL.
MC: We are expecting an increased demand in our ferrous division. In 2022, we acquired 100% intellectual property (IP) rights of Coseco, a manufacturer specializing in wire coating and plating plants, from CO2 to tyre cord and bead and inline rod preparation. Coseco now operates under the MFL Group umbrella as our dedicated coating and treatment lines company. We have new applications, mostly related to ecological approaches to systems. As a result, we reached significant advancements in mechanical descaling and in-line phosphating.
Moreover, for bead wire production, we’ve implemented an induction application for diffusion, eliminating the need for lead or lead baths and thereby contributing to a more environmentally friendly process.
Our vision is to enhance our products and expand our product range in a highly efficient and ecologically conscious manner.
DC: In the non-ferrous division, we are expecting a significant demand for extrusion lines and rod breakdown machinery. With Coseco’s support, we’re not only addressing the needs of our ferrous division but also expanding into the non-ferrous sector with offerings such as tinning and electroplating lines. As a result, we foresee substantial growth opportunities in India.
We are looking forward to Indian trade exhibitions as India is the place to be.
WCI: We have seen MFL giving priority to Industry 4.0. Please elaborate.
MC: At MFL X, our digital division, we’ve developed applications through a partnership with 40Factory, a company specializing in digital solutions for industrial enhancement and new business models. Our primary application, Acumen, is a cloud-based, multi-platform, and highly modular Industrial IoT Application. Acumen aids customers in making informed, real-time data-driven operational decisions, optimizing Overall Equipment Effectiveness (OEE), and receiving enhanced customer support by bridging the information gap between us and our customers. It provides crucial insights into machine down-time, empowering users to refine production processes and address challenges effectively. Unlike traditional SCADA systems, Acumen transcends local limitations, offering comprehensive data analysis and actionable feedback.
Acumen represents our commitment to Industry 4.0 and is readily available for immediate implementation.