“We are quite well-versed with the diverse needs of the cable industry due to which we can develop specialized products for different applications and specific needs of the customers.”
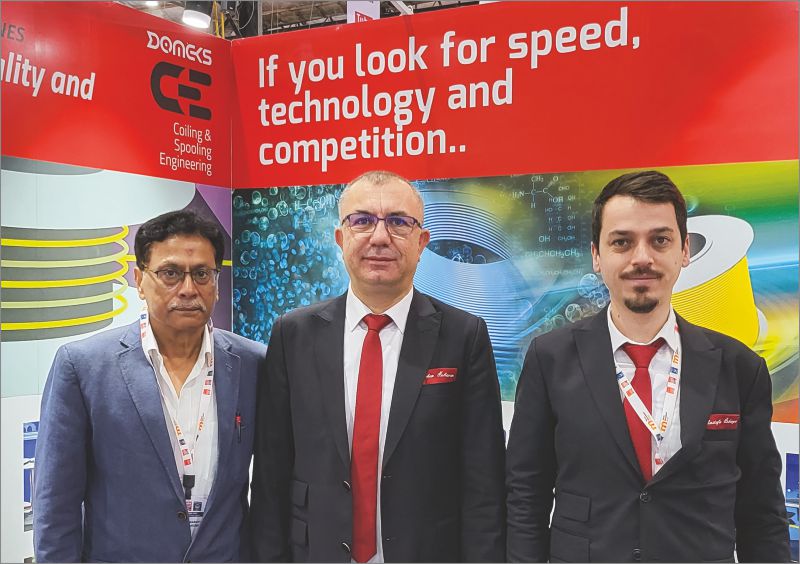
Turkey-based Domeks Makine Ltd. Sti., started in 2002, produces high-speed coiling and reel packaging lines for all plant cables. With a diverse product range, the Company has distinct expertise in compounding lines. Wire & Cable India recently interacted with Mr. Orhan Özbaran, General Manager, Domeks Makine A.S., and Mr. Rajneesh Nagrath, Indian Partner of Domeks Makine, wherein they presented an overview of Domeks Makine, the key strengths, their presence in the Indian market, and the way ahead.
Wire & Cable India: At the outset, please present an overview of Domeks Makine.
Orhan Özbaran: We, at Domeks Makine, are majorly focused on two major applications – automatic coiling line (including packaging line for coil applications) and compounding line, to serve the different needs of our customers. In addition, we are always prepared to redraw our model in line with our vision to cater to the diverse needs of our customers.
With regard to the compounding line, which is mostly concentrated in the cable industry, we are concerned with the production of PVC compounds as well as cable components like fillers, sheaths, insulation, and raving, gasket compounds. With time, we’ve established an extensive presence both on the formulation side and the machinery. During the last ten years, we’ve been focusing on halogen-free flame retardant (HFFR) cable compounds. In fact, we have established a distinct venture for the production of the HFFR compounding line.
WCI: Tell us about the strengths of your company. How do your technology and machines have an edge over the competitors?
OÖ: Domeks Makine launched a machine called Quadromatik Series for the ‘Coil and Spool’ segment. Around 12 years ago, there was no such machine which could take care of both the coiling and spooling applications simultaneously. We combined these two diverse applications in one single line.
Presently, we are focusing on the Speedmatik coiling line, especially for building wires and cables all over the world. So far, the maximum speed for the coil line was about six-seven coils per minute for a 100-meter cable length. With our new project, we can improve this volume up to eight-nine coils per minute. Moreover, this line can be worked with the extruder directly. We have amassed extensive experience working on coiling lines. Further, another key strength of Domeks is that our team is cognizant of the manufacturing environments and cable production behavior. Thus, we are quite well-versed in the diverse needs of the cable industry due to which we can develop specialized products for different applications and the specific needs of the customers.
WCI: To Mr. Rajneesh Nagrath]: Being Domeks’ partner for the Indian market, tell us about your partnership with the firm.
Rajneesh Nagrath: We’ve been associated with Domeks Makine since 2006 and it has been a great experience working with the firm. We have established a cordial association with Domeks. Their after-sales-services are excellent. Also, the majority of the customers are highly satisfied with the machines as well as the quality of services by Domeks. In addition, I would like to add that we are assured of getting more business opportunities in India.
WCI: Tell us about the Company’s presence in the Indian market.
OÖ: We are quite excited about the growth opportunities in the Indian market. It was in 2006 that we forayed into the Indian market. At present, we have established considerable production lines and we have more than 35 machines operating in the region. Thus, India has always been quite a significant market for Domeks. We are mindful of considerations like energy consumption and machine efficiency for increasing competitiveness to serve our customers in a better way.
RN: Our valued customers include Polycab India, RR Kabel, KEI Industries, Universal Cables, Shakun Polymers, Kkalpana Industries, Payal Petrochem, Panasonic, HFCL, HTL, and so on. I would further say that we are optimistic that our number of customers will keep growing. We would now like to focus on expanding our footprint in the country.
WCI: Tell us about your manufacturing facilities and the capabilities of the Company.
OÖ: In 2015, we shifted our facility to the Tekirdağ region which is around 100 kilometers away from Istanbul, Turkey. The facility spans 20,000 sqm for the manufacturing assembly, and testing units and, the joining HDOplast. We are also a compound producer for the HDOplast site. Thus, year by year, we are looking forward to increasing the production capacities.
Also Read: Wire & Cable India Emagazine Nov-Dec Issue 2022
WCI: What is the future outlook of Domeks Makine in India? What kind of strategies are you going to espouse for the Indian market?
OÖ: In our understanding, the Indian cable industry is growing significantly on a yearly basis. In view of this, we could look for opportunities to establish an even stronger presence of Domeks by setting up a manufacturing base in the country. For instance, three years ago, we achieved the production of a fully-automated line with a capacity of about seven coils per minute. Thus, we assess the requirements in the Indian market after which we work on bringing distinct solutions keeping in mind the needs and applications of our customers.
RN: In our understanding, India is going to be the next manufacturing hub for the wire and cable industry. In the next few years, it is projected that the Indian players would be the prominent suppliers for the wire and cable industry globally. As a matter of fact, a few of our customers have penetrated the European and the US markets where the quality has been well accepted. Thus, there is a great scope for expansion in the wire and cable industry. In particular, in the solar cables segment, there would be a great growth potential driven by the Government of India’s initiatives. Thus, there is a great future ahead in the segment about which we are quite enthused.
WCI: Please talk about the future plans of the company.
OÖ: As I mentioned, we have a new project for the coiling line. Our main goal for this project is to present excellent machinery with respect to building wire applications. For instance, for the building wires and cables, most of the extrusion lines’ speed is up to a thousand meters per minute. This means that for one line, you would need approximately two pointing lines for equalizing the speed. However, if you increase the speed up to a thousand meters per meter or near this volume, we can match the speed of the coiling line with the exclusion line. This means that even if are working with offline operation or inline operation that gives our customers good results.
Furthermore, I would like to emphasize our expertise in compounding lines. In the next year, we will start for the X HFFR compound which will be especially used for the solar cables. Later on, we would start executive production as a machinery manufacturer. These are the major future plans and strategies for Domeks which we aspire to bring to fruition!