Online diameter control during wire and cable production
In the past years wire and cable manufacturers have invested heavily into measuring and control technique as well as line control systems aiming for online quality control, higher productivity and cost reduction. Today, online measuring devices with controlling function had therefore become a standard in extrusion lines. The used measuring devices include, amongst others, gauge heads, which measure the outer diameter of the cable during the extrusion process. SIKORA is a pioneer in the production of diameter measuring systems and developed two product series based on laser technology for continuous online quality control. Operators can choose between classic and high-end orientated technologies.
Methods for diameter measurement
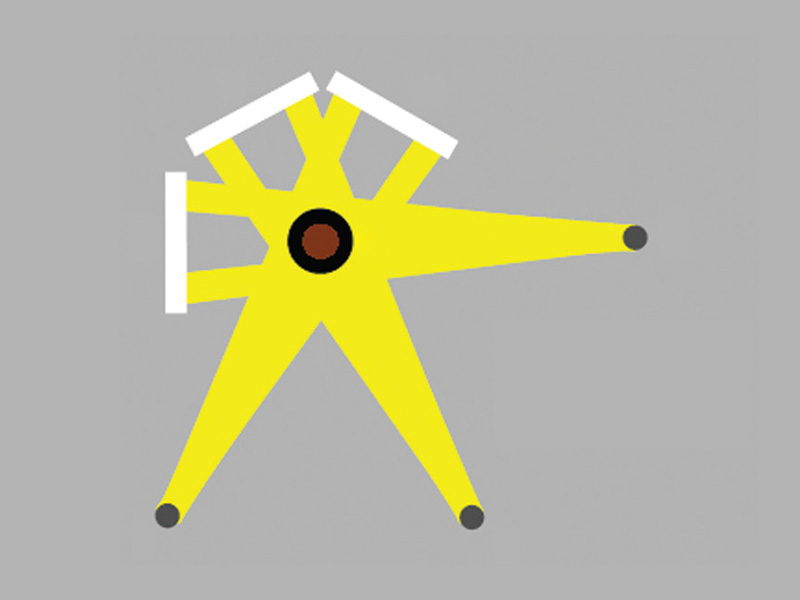
For the measurement of a product diameter there are two established techniques known. The first method was invented 40 years ago and is commonly known as “Scanning System”. By using a rotating mirror, a laser beam is scanned across the measuring field onto a light sensor. In between the rotating mirror and the light sensor there are two lenses. The first lens directs the laser beam in parallel across the measuring field to the second lens. The second lens directs the laser beam onto the light sensor. The product is guided in between the two lenses and interrupts the laser beam while the laser beam is scanned across the measuring field. Thus, the diameter of the product is calculated from the time the laser beam needs to pass across the total measuring field, compared to the time the laser beam needs to run across the product. Time is in this case equivalent to diameter. The measuring rate depends on the rotating speed of the mirror.
The technology that was presented 20 year later uses a laser beam, which is directed onto a high resolution CCD line sensor, with no rotating mirror and lenses in between (Picture 1). The product causes a shadow on the CCD line sensor. In this case the number of dark pixels on the line sensor is equivalent to the diameter. In reality the shadow evaluation is done by signal processing of the diffraction signal, resulting in most accurate readings. The measuring rate is in this case extremely high and only limited by the selected CCD line sensor.
The main differences between the two techniques are therefore that the secondly described technology is completely digital, requires no moving components and no lenses. As a consequence, accuracy, repeatability and measuring rate are higher, calibration is not necessary.
The technological base of SIKORA diameter gauges described in the following is the second principle, using CCD-line sensor technology combined with laser diodes as light sources and powerful analysis software. There are two types of measuring heads available that meet classic respectively high-end requirements demanded for quality control at cable production lines.
Classic diameter control
There are diameter gauges with classic functions available such as the gauge heads of the LASER Series 2000 that meet the standard requirements, which are imposed on a diameter measuring system. The gauges measure the diameter in 2 or 3 planes with a measuring rate of 500 measurements per second. Interesting is the 3-axis gauge head for defining the ovality of a product. It is known that an oval is defined by 5 tangents. Accordingly, by using 3 measuring axis (6 tangents on the oval) not only the min/max value of the oval, but also the orientation of the oval can be defined. All devices are equipped with standard interfaces such as RS 485, optional Profibus-DP and other industrial field buses for the data transfer to a line PC or a display and control device. With an additional control module, which is integrated into SIKORA’s display and control devices, the diameter is continuously controlled to the nominal value. Customers can select from 18 types of devices covering a diameter range from 0.05 mm to 500 mm. These devices are standard in extrusion lines today (Picture 2).
Interesting is the market development of the measuring and control devices concerning advanced technologies, which offer enhanced functionality, easy operation, higher measuring rates, highest accuracy and flexible data transfer. Today, users are aiming for a permanent quality control of their production as well as maximum productivity and cost reduction, for instant, by using advanced innovative measuring devices.
High-end diameter control
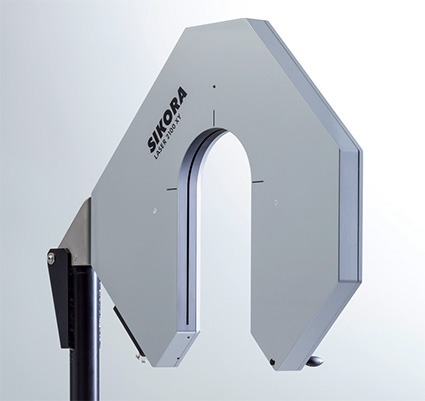
Due to this demand, SIKORA developed three diameter gauge head models of the LASER Series 6000, which meet the current high-end requirements in the wire and cable sector (Picture 3). Besides the classic features, which are also covered by the LASER Series 2000, the gauge heads of the 6000 Series combine a variety of technological innovations to improve the productivity of extrusion lines sustainably. Up to 5,000 measurements per second, each of them with highest single value precision, allow for an optimum line control and provide reliable statistical data. The high measuring rate also allows the detection of lumps and neckdowns. Therefore, the user is receiving a two-in-one system with which investment costs are being reduced and more space is achieved in the line, as the installation of only one gauge head is required. Intransparent and colored products can be measured with the LASER Series 6000 as well as transparent products. Additionally, the gauge heads have an integrated LCD display. This gives the operator the diameter value at one glance, directly at the measuring device.

For applications where statistic data shall be processed and stored and/or where reports shall be printed, external processing systems of the ECOCONTROL Series are available. Directly integrated in the gauge heads is an universal interface module for all connections such as RS 485, RS 232, Profibus-DP, Profinet or alternative industrial field busses. Additionally, the LASER Series 6000 has an optional Wi-Fi interface, which allows for a direct connection to a smartphone or laptop. The Wi-Fi interface is used for diagnosis and quality control and transfers measuring values, trend and statistic data, as well as video signals. The Wi-Fi interface, the interface module as well as all plug connections are completely integrated into the gauge head and, in this position, protected against water, dirt or mechanical influences during production. Furthermore, the LASER series 6000 can be used for mobile quality control: An App does not only allow the operator to display all production data at smartphones (Picture 4); the App also offers a gauge head calibration in accordance with ISO 9001. The values of the test probes are fed via QR Code and the measuring values are saved in a log file. For the quality management system, a test certificate is created, sent and archived.
An important feature for the integration in the production line is the swiveling gauge head design. The gauge heads can, for example for a product change, easily moved up and out of the extrusion line. All measuring heads are open at the bottom side to prevent dirt and water from falling into the measuring area. The feeding of the cable connection to the interface module is also safely protected in the gauge head stand. SIKORA offers the three diameter measuring devices for a product diameter from 0.2 up to 78 mm.
Conclusion
The decision which measuring and control device for quality control is being used in the production line depends on the requirements that an operator imposes on a testing device. Diameter measuring devices have to control the quality continuously during production. They provide actual information about the product and therewith the basis for automatic control. Ultimately, only the combination of the gauge head and the control device contribute to cost reduction during production. The diameter is automatically controlled to the minimum value based on the measuring results and the comparison with the nominal value. Hence, there is only as much material used as currently required. In this way, costs can be reduced, scrap avoided, and the productivity is increased significantly.
The LASER Series 2000, in combination with a line PC or control device, offers classic technology features which enable the operator to react quickly to tolerance deviations and to produce optimum quality. The LASER Series 6000 is additionally equipped with various advanced features, with which the users can run their production lines more efficiently. Especially the extremely high measuring rate, measuring accuracy and repeatability are setting new standards in the precise controlling of the production line and, therewith, for the production of cables of high quality. It is necessary to comply with product dimensions in order to further process the produced cables in the production chain. Last but not least, costs are reduced by using the provided material efficiently.