BUSS, a Switzerland-based global leader in compounding systems, also known as the original manufacturer of the Co-Kneader technology, is celebrating 80 years of the initial patent this year. BUSS’ unique compounding solutions set the standard for heat or shear critical applications in the plastics, aluminum, powder coating and food industries. Catering to the evolving needs of wire and cable manufacturers worldwide, BUSS has come up with the latest COMPEO™ co-kneader series, a compounding machinery based on the patented co-kneading technology, reveals Dr. Victor Callegari, Head of Business Development, Innovation and Marketing, in a conversation with Wire & Cable India. In India, BUSS is represented by Reifenhäuser India Marketing Private Limited.
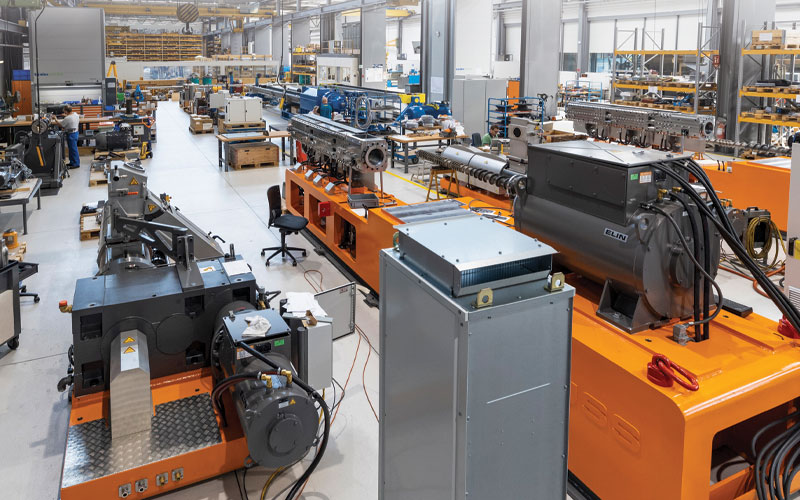
Wire & Cable India: What are the key innovations and emerging trends shaping the wire and cable industry?
Victor Callegari: There is a focus on the use of recyclable, recycled or biomaterials, and more generally low-carbon materials and processes, setting new standards for environmental responsibility.
We see more cables designed with integrated mechanical protection and increased resistance to water and UV exposure coming to the market, ensuring durability and reliability in various conditions. Additionally, ground-laid cables require mechanically robust solutions and have to meet the highest standards in terms of UV and moisture resistance.
In Europe, the legal regulations demand the use of HFFR compounds for public facilities and installations including buildings, tunnels and transportation. Similar regulations are either in force or expected to apply in India, China and the Middle East. In order to meet the demanding requirements for flame retardant properties, it is generally necessary to add 50-70 % of the appropriate fillers. For some applications, as much as 80% is needed. Formulations are therefore preferred with PE-copolymers, which enable higher filler absorption. Coupling and/or cross-linking systems are integrated in order to attain the required mechanical and application-relevant properties.
WCI: Please highlight the latest advancements and technology developments that you have introduced in your machines to cater to these evolving needs.
VC: At BUSS, we are helping our customers pioneer sustainable solutions in the cable industry by offering thermoplastic insulation and fully recyclable materials as alternatives to traditional cross-linked materials. This shift not only reduces environmental impact but also enhances the recyclability of our customers’ products.
BUSS’ state-of-the-art COMPEO™ co-kneader series are used in our new direct peroxide injection and gentle compounding of a newly developed additive cocktail. Our technologies offer access to, among others, various High Voltage (HV) and Extra High Voltage (EHV) insulation materials, exhibiting excellent product quality and superior process efficiency compared to the well-known soaking technology.
Silane-crosslinked cable compounds based on PE have proven to be the most cost-effective method worldwide for use in cable insulation applications up to voltages of 10 kV. BUSS co-kneading machines are also used for manufacturing the catalyst masterbatch and the XLPE Sioplas®, a two-stage process in which a peroxide-activated grafting of vinyl silane onto the polymer chains is realised. Buss kneaders are also extensively in use since many years for PVC applications.
Watch: Top Cable Companies in India
WCI: How do you help your customers achieve better efficiencies in their production processes? Maybe, by reducing the energy consumption; enhancing quality or reducing the waste in the production process.
VC: We have developed and patented together with a partner, a direct peroxide injection and gentle compounding of a newly developed additive cocktail by using BUSS state-of-the-art COMPEO™ co-kneader series, allowing at the same time for significantly reduced capital expenses and equipment requirements. Further advantages are the compact plant design without high-rise soaking tower and improved cleanliness and physical-electrical properties of the produced materials.
Another example where BUSS technology plays its strength is the processing of semiconducting cable compounds. This is a very demanding process. The conductivity values must be guaranteed both at room temperature and at elevated operating temperatures. The structure of the highly structured carbon blacks must be maintained, and they must be distributed extremely homogeneously to form the conductive network. The polymers used must degrade as little as possible. The surfaces of the layers coextruded during processing must be very smooth and even.
To meet this complex set of requirements for semi-conducting cable compounds, the BUSS kneader can play to its specific strengths: the high proportions of conductive additives can be distributed to several feeding points. The immediately initiated mixing processes at moderate shear rates lead to excellent distributive mixing results without damaging the internal structure of the conductive materials and polymers.
The system’s design freedom also makes it possible to specifically address the increasing viscosity in the processing zones with carefully selected configurations. This allows for customised control and monitoring of the process conditions.
WCI: Do you have any R&D team catering to evolving needs? Elaborate more about your R&D efforts.
VC: BUSS operates its own global academies with over 100 collaborative customer trials per year, encompassing equipment, formulation, and analysis.
Our extensive global network includes leading private and public research institutions and specialists in wire and cable formulations, all utilizing BUSS equipment to drive innovation and excellence.
BUSS holds patents and licenses the technology to customers in the wires & cables industry operating our equipment world-wide.
WCI: What is your current product portfolio catering to the wire & cable sector? Are there any expansion plans in the pipeline?
VC: BUSS has a strong global presence in wire and cable applications with reference plants for low voltage materials, HFFR compounds, filling compounds, conductive layers and insulation materials ranging from medium to extra-high voltage applications for AC and DC.
This October, we will unveil our latest additions to our kneader family of products, including digitally enabled technology for machine performance and health monitoring. Additionally, we will introduce new enhancements to our state-of-the-art COMPEO line, ensuring even greater operational efficiency for our customers. BUSS is committed to further investing in our core markets, driving technological advancements in machinery and processes for the wires & cable industry.
WCI: Could you provide insights into your market presence and key clientele globally & in India?
VC: BUSS is an international market leader in compounding systems for demanding applications. As the original manufacturer of the Co-Kneader technology, celebrating 80 years of the initial patent this year, the company offers unique compounding solutions that set the benchmark for heat- or shear-sensitive applications in the plastics, aluminium, powder coating and food industries. The core competence is customer and application specific solutions for advanced compounding tasks in line with the high demands on process technology and product quality as well as the continuously increasing technological market needs. We count all major wires and cables companies worldwide as our valued customers.
In India, BUSS is proudly represented by Reifenhäuser India Marketing Private Limited.
Also Read: Windak Focussing on Innovation, Sustainability and Global Expansion
WCI: How do you integrate sustainability into your manufacturing and application processes?
VC: At BUSS, we are dedicated to design and manufacture products with a lower environmental impact. Our kneaders boast an impressive lifespan, with some of our plants operating for over 60 years. Through continuous modernization and upgrades, we extend the replacement cycle, thereby reducing waste.
Our innovative processes and optimized additive usage minimize material waste, while the simplified cleaning of our equipment further reduces material consumption. Additionally, our plants are designed for optimized energy consumption, ensuring efficient operation.
One of the standout features of our technology is the superior distributive mixing efficacy of our kneaders, which results in smaller footprints.
At BUSS, we are committed to reducing waste, utilizing energy-friendly technologies, and incorporating components that align closely with the concepts of energy savings and circular economy. Our measures ensure that we not only meet but exceed environmental standards, paving the way for a sustainable future.