A new innovative multiwire drawing and annealing platform for electroplated copper wires has beenshown to meet market requirements such as enlarged outlet wire range diameter, number of wires,outlet diameter of each wire smaller and a faster and more flexible production.
Just like many conductive materials, bare copper forms an oxide layer when exposed to a normal atmosphere. This reaction accelerates with the increase of temperature, and at 180-190°C bright copper turns black in a few minutes. Oxide film is a poor conductor of electricity, reduces the reliability of connections and reduces the compound hook-up in insulation processes. For these reasons, oxide film must be removed or prevented from forming. This is usually accomplished by coating the copper wire with a pure metal coating which oxidizes slowly at processing temperature. In special cases, alloy coatings or composite coatings plated in multiple layers are applied. Bare copper presents satisfactory characteristics at temperatures up to approximately 100°C.The most common pure metals used for plating copper and copper alloys for conductors are tin, silver and nickel.In special cases, alloy coatings such as tin/lead or composite coatings (i.e. tin over nickel), plated in multiple layers, can be applied. The wire drawing and annealing process of copper and copper alloy conductors requires particular attention to avoid damage to the conductor surface.
Tin-plated copper wire: Tin is used as a pure metal coating to increase the operating temperature of copper and copper alloy conductors to 150°C and improve solderability characteristics. Tinned copper conductors are slightly more expensive than bare copper wire.
Due to the low melting temperature of tin, tin-plated copper conductors are used in applications where the base material is not exposed to high temperatures. Over a period of time, and at a rate determined by temperature, tin and copper interact to form an intermetallic alloy. This reaction reduces the solderability, occurs at room temperature and cannot be prevented by protective packaging. Surface oxidation also degrades solderability. Shelf life can be maximized by proper packaging and storage in a temperature-controlled environment.
Tin-coated copper conductors used in electrical applications are specified by ASTM-B33, which also defines general requirements such as elongation percentage, resistivity, dimensions and permissible variations, adherence and continuity of coating, test methods.
Silver-plated copper wire: Silver coating is used to increase the operating temperature of copper and copper alloy conductors to 200°C and also gives the conductor excellent solderability characteristics that do not diminish over time due to diffusion. Silver also has antibacterial effects, good pliability, is a relatively soft metal and its oxide is electrically conductive. Silver coated conductor oxide in a few hundred hours at 250°C.
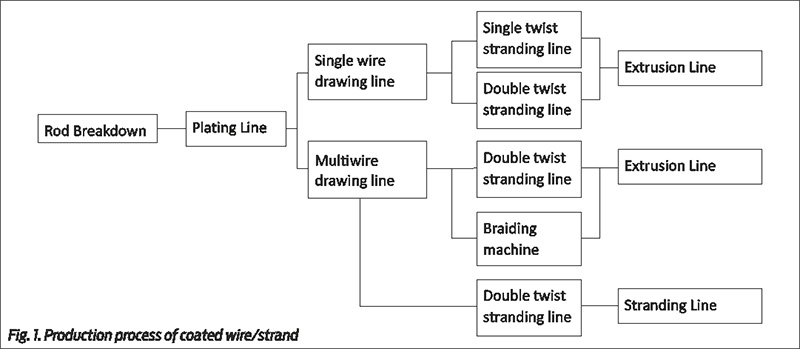
Silver has higher conductivity than copper and this is desirable for high-frequency applications where, because of the skin effect, signals travel along the surface of conductor. Plating a conductor with pure silver increases its performance in such applications. Silver-coated conductors are widely used despite having a higher cost than tin.
Standard silver-coated copper used in electrical equipment are divided by ASTM-B298 into five classes (A, B, C,D, E), representing the minimum percentage (by weight) of silver coating respect the coated wire (A=1.25%, B=2.5%, C=4%, D=6%, E=10%). Each Class gives information about the thickness of coating. Per ASTM-B298, the general requirements are also defined as elongation percentage, resistivity, dimensions and permissible variations, adherence and continuity of coating, test methods. Minimum thickness is 1 micron.
Nickel-plated copper wire: Nickel plating increases the operating temperature of copper and copper alloy conductors to 250-260°C. Nickel has a good resistance to corrosive atmosphere, low hardness and good ductility in annealed condition. As nickel is a poor conductor of electricity, it requires an activated flux for soldering and, due to its hardness, a nickel-plated conductor may exhibit more variability in crimp termination than other plating material (e.g., tin).
Standard nickel-coated copper conductors used in electrical applications are divided by ASTM-B355 in five classes (Class 2, 4, 7, 10, 27) representing the minimum percentage (by weight) of nickel coating with respect to that of the wire (i.e., Class 4 means that the nickel-coating weight is at least 4% of the total weight of the coated wire). Each class gives information about the thickness of coating. ASTM-B355 also defines the general requirements as elongation %, resistivity, dimensions and permissible variations, adherence and continuity of coating, test methods. Minimum thickness is 1.25 micron.
The Class 27 in ASTM-B355 refers to specialized conductors used in extremely high temperature conditions.
PLATING CONSIDERATIONS
Multiple plating: Sequential plating technology is used when is needed a reduction of intermetallic interaction between the surface and the base metal while maintaining the favourable properties of the surface plating.
One example is multiple plating of nickel/tin, where the nickel under the layer plating is used for mitigate “whiskers,” an unwanted growth of conductive filament caused in a tin-plated copper conductor by the diffusion of copper from the base material into the tin layer. These whiskers can cause problems or failures in electronic applications.
Application of plated copper and copper alloy wires: Plated copper and copper alloy conductors are used for: wire for shielding, braiding and screening applications; strand for electrical and electronic applications; automotive signal cables; aircraft signal cables, communication and RF cables; mining cables; railways cables, rubber insulated vulcanized cables; special cables.
PLATING PROCESSES
Two different processes can be used for plating copper and copper alloy conductors: hot-dipped and electroplating.
Hot-dipped process: This process is used for tin plating copper. The conductor passes several cleaning baths and a specific bath with flux, then is dipped in a bath of molten tin. After cooling, the wire is cleaned and spooled.
The characteristics of the hot-dipped process for a pure tin coating include the following pluses: the formation of an instant inner inter-metallic bond that ensures totally firm adhesion; no whisker formation, and a homogenous coating that is free from contamination or chemical residues; a uniform coating composition regardless of process parameters;and the highest abrasion resistance. The minuses arethat setup of the concentricity of tin layer is difficult; andthere is more consumption of tin due to higher tolerances (6 μm) and bath oxidation.
Electroplating process: Coating material (tin, nickel orsilver) and base material (conductor) is treated by way ofimmersion into an electrolytic bath, coating material (e.g., silver pellets) is connected to an anode and the conductorto a cathode. After drying, the wire is spooled.
The characteristics of the electroplating process puretin plating includes the following pluses: a close-grainedcoating, with firm adhesion; a bright or matte surface; aconsistent coating thickness to tight tolerances over theentire length of the wire, thus ensuring optimum characteristicsfor further processing which might involvehighly diverse criteria; a process without thermal stress forthe conductor; multiple platingcan be applied; and lessconsumption of tin due to abetter thickness/concentricitycontrol and low tolerances(2 μm). One minus is thatthere is lower abrasion resistance.
A wiredrawing setup withan accurate electroplatingprocess that ensures constantthickness of coating, adhesionand concentricity, would be asuccessful process.
TECHNICAL MULTI-WIREDRAWING LINE SOLUTIONS
The ability to offer highquality lines for coated wireand strand market constitutesa competitive advantageover rival companies.Product development is therefore oriented in two paralleldirections: the development of new products; and the continuousimprovement of existing products within a contextof continuous market evolution; and the ability to respondto market demand in the best possible way at all times.
In a high competitive market, wire manufacturers ask toincrease the product quality and the production reliability,whereas production costs and scrap rate should be reduced.
Over the last few years, there has been more demand formetal coatings for multi-wire drawing machines. In particular,the number of requested wires has increased, theoutlet diameter of each wire has become smaller and therequested production speed is increased.
The development of the new multiwire drawing line platform took several years, it’s the result of comparative analysis of the process of wire drawing and annealing of bare copper and metalplated copper wire. In particular, adding plating to a bare copper multiwire drawing system presents technical challenges in the coating surface as the wire is hard and abrasive and the dust and powder generation is higher. Annealer contact band life is critical due to sparking. One concern for using tin for plating is its low melting point.
The cross-section reduction of the outlet wire requires anincrease in the number of drafts of the multiwire drawingline. The multiwire drawing machine is a slipping gearboxmachine; therefore, a high number of drafts causes a highcumulative slip in the wire inlet side. For example, in a29-draft machine setup, the cumulative slip at the wire inlet is approximately 45-50% (considering a slip of 1.5% for each die, and 3% at the final die).
High slip has a negative effect on the quality of plated wires. This factor increases the frequency of wire breaks, reduces the lifetime of the drawing capstans and increases energy consumption and the noise level of the multiwire line.
A SAMP multiwire drawing platform (DM Platform) (see Photo 1) has been designed and offered to the industry that is based on the splitting of gear transmission into two or more independent sections, with separate AC servomotors.This allows slip recovery between each section and at the inlet side. A 29-draft machine with three motors has a maximum slip at the wire inlet of 15-18% and reduces the slip at the separation to ca. 5%.
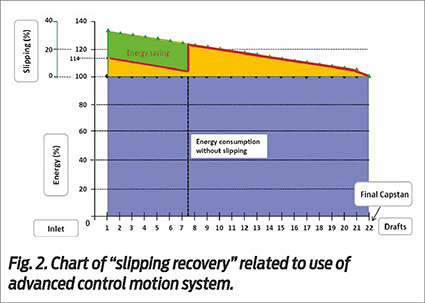
advanced control motion system.
Power splitting also enables the use of compact AC servomotors with compact drives that allow a more precise regulation in the operation and high efficiency of transformation current in mechanical torque at drive end.
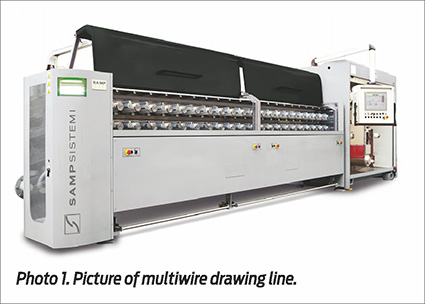
A control motion system (see Fig. 2) is used for synchronization of all motors. The reduction of slipping and the improvement in the quality of gear transmission, bearings, seals, etc., have allowed energy consumption reduction of up to 10-15%, reducing production costs. In order to reach the best wire quality surface, zirconium oxide pulling rings have been adopted.
The drawing of metal coated wires requires an increased amount of lubricant compared to bare copper, a better control of temperature and cleaning.
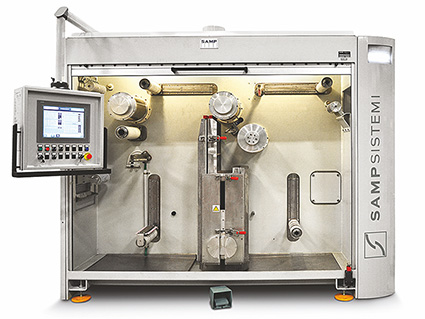
Die holders have spray jets on both the inlet and outlet cones to improve wire lubrication within the die to reduce friction and to facilitate cleaning of the inlet/outlet cones themselves, thereby enhancing product quality and prolonging die life. There is also a spray for pulling rings to reduce the friction with wire.
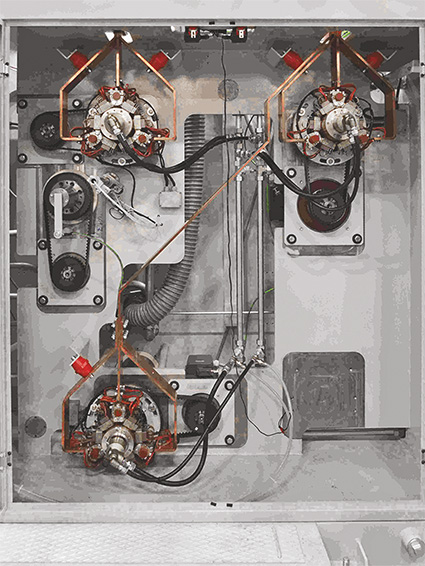
The lubrication of the final die is critical as it is here the wire attains its minimum diameter. At the maximum speed, the metal coating is at minimum thickness and the lubrication is usually only on the entrance die cone.For these reasons, the designed multiwire drawing machines have a pressurized separate lubricant supply circuit for their final dies.
The annealing process is critical because the annealing path must ensure the integrity of the wire coated surface, the requested physical properties (mechanical strength, elongation, conductivity and resistance) and maintain the diameter and roundness of the wire. Wire quality and production efficiency are also influenced by contact ring surfaces.
To satisfy these requirements, the described multiwire annealer platform includes a number of technical features, – such as multimotor technology, adjustable pre-heating length, a wire walker before contact rings and a cleaning device on contact rings. See Photo 2.
A traditional Joule effect annealer is a machine with one motor and a belt transmission that connects all contact rings with a fixed ratio between each axes. This ratio is a compromise for the whole wire range diameter of the annealer and there it is not possible to set an optimized adjustment for each wire diameter. This characteristic causes surface damage, reduces contact ring life and increases production costs.
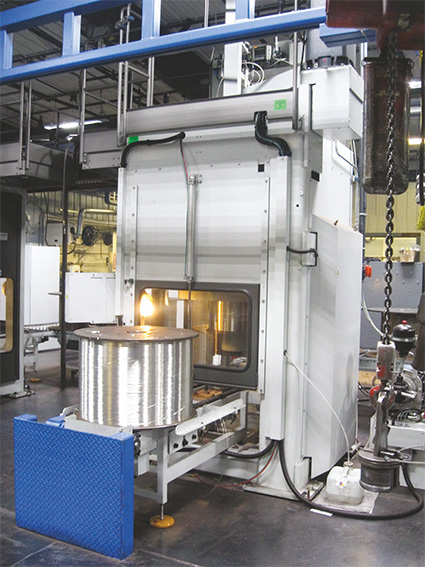
In the described Multimotor Annealer Platform, which has been designed for the coated wire market, the system is able to set up production parameters, in particular the kinematic ratio between each axis, to form a production recipe stored in the HMI panel. See Photo 3.
The described Annealer Platform is completed with the latest development in annealing electrical equipment, in particular the development of the electronic equipment that reduces current distortion (THD-I) and energy waste (PF > 0.90). This development was quite demanding, in particular for the choice of reliable components and their tuning. Different units has been tried in-house with a “dry test” and with wire, and then installed in rod breakdown and multiwire lines at different customers’ plant with positive results in terms of quality of the wire produced and energy efficiency
A gentle wire path and pulleys with ceramic coatings are others keys for obtaining good results.
SUMMARY AND FUTURE AREAS OF DEVELOPMENT
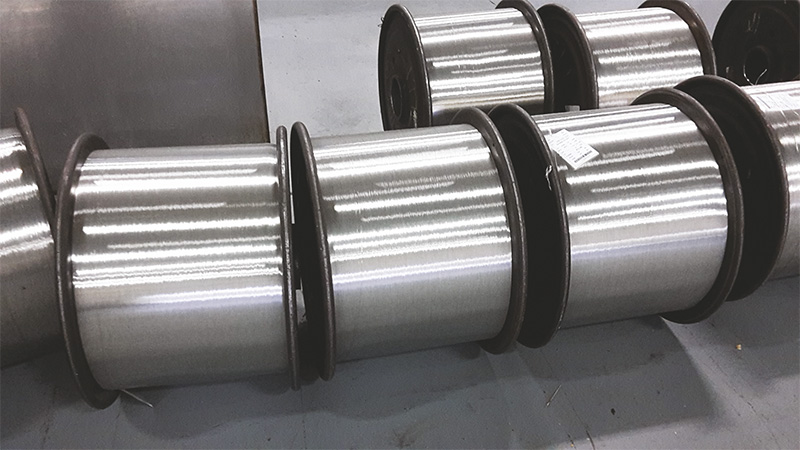
A new multiwire drawing and annealing platform for electroplated copper wires has been shown to meet market requirements such as enlarged outlet wire range diameter, number of wires, outlet diameter of each wire smaller and a faster and more flexible production.
New electronic technologies, as well as innovative and improved design in multiwire and annealer, generate savings through increased production efficiency (i.e. less wire breakage), long annealer contact band life (six months for tin-plated copper) and less energy consumption and allowing to obtain a better wire quality surface. See Photos 4 and 5.
The aim of the company is and will always be to supply technologically advanced systems that guarantee users the lowest possible operating costs. Innovation and know-how will therefore form the basis for all development activities over the next few years.
References:
1. SampSistemi Technical Presentation, IntercableMeeting December 2005
2. SampSistemi Technical Presentation, 6th CabWire World Technical Conference 2013, Milan
3. www.calmont.com, www.fiskalloy.com,
4. ASTM-B33, ASTM-B298, ASTM-B355.
(Courtesy: SAMP SpA)