The automotive industry is driving revenue growth for companies operating in the wire and cable segment.
The wiring harness, which plays a critical role in the vehicle, serves as a vital link between the wire and cable industry and the automotive industry. This harness is a set of wires, connectors, and terminals that transmits information and electric power to deliver function to the vehicle. A car has many wires, and when these wires are stretched out, they can extend for miles.
In virtually all applications in a vehicle, such as engine, transmission, lights, braking, air conditioners, seat heaters and various dashboard applications like speedometer, fuel meter, etc., wires and cables serve a major function. With the advancement of new technologies and sharp rise in customer aspirations, applications of cables and wires in automotives have increased considerably with time.
The Automotive Wiring Harness Market
The growing demand for greater safety, convenience and comfort and the increasing volume of vehicle production are likely to push the demand for the automotive wiring harness market. The dashboard/cabin application is estimated to be the largest segment (by volume) of the automotive wiring harness market from 2018 to 2025. According to a study conducted by Grand View Research, Inc., the global automotive wiring harness market size is expected to reach USD 77.15 billion by 2025 at a 6.2% CAGR during the forecast period. However, the high cost of advanced technology may stymie the automotive wiring harness market.
It is estimated that by 2025, the Asia-Pacific region will be the largest market for automotive wiring harness. The main growth drivers for the market in this region are increasing disposable income in countries like India and China and the growing demand for premium cars and advanced features in the vehicles. The North American region is estimated to be the second largest market for automotive wiring harness market. North America – with one of the largest markets for premium segment vehicles – is expected to witness impressive growth in the automotive wiring harness market. The demand for additional safety and convenience features in mid-segment vehicles is also growing by leaps and bounds in the region.
The Electric Vehicle segment has turned out to be the fastest growing segment of automotive wiring harness market, thanks to growing environmental concerns, rising fossil fuel prices and strict government regulations for emission. Increasing adoption of electric vehicles is also expected to drive the automotive wiring harness market, as far more electronic components are used in EVs than in conventional automobiles. Wire manufacturing for EVs has to be done by wire and cable manufacturers, as in-house development of wire-manufacturing processes would prove rather costly for car manufacturers.
These developments in the automotive industry certainly augur well for the wire and cable industry.
Fossil-fuel Vehicles and EVs: Impact on the Wire & Cable Industry
In order to meet national climate targets under international agreements such as the Kyoto Accord and the Paris Agreement, to gain energy independence and to reduce health risk due to local emissions, many countries have proposed to ban the future sale of passenger vehicles powered by fossil fuels. These countries include India, China, Japan, South Korea, Taiwan, Denmark, Sweden, Norway, Germany, France, the Netherlands, Spain, Portugal and Costa Rica. Paradoxically, China is the largest auto market globally and Japan is the third largest auto market globally. It may be mentioned that Japan has comprehensive plans for a “hydrogen economy” by 2040. Be that as it may, fossil-fuel vehicles will not disappear completely from the market in the near future. Also, the sale of hybrid EV (HEV) is expected to increase with the passage of time. So, there are currently no roadblocks for the wire and cable industry.
The arrival of all sorts of EVs has also widened the scope of wire and cable markets. Governments of many countries consider EVs as the best alternative to fossil-fuel vehicles. Britain seeks to halve fossil- fuel vehicles by 2030. China is planning for 4 percent EV adoption by 2021, which means 1.12 million EVs would be sold in China in less than five years. India recently launched its Faster Adoption and Manufacturing of Hybrid and Electric Vehicles (FAME) scheme, which provides incentives for purchasing EVs. Recent reports suggest that the government may put a tax on fossil fuel vehicles to persuade buyers to opt for EVs. The government’s plan envisages 30 percent EVs on India’s roads by 2030. The government has also released tenders to increase charging infrastructure in the country. Concerted efforts are being made in many countries to push the sale of EVs.
Are EVs ready to overtake fossil-fuel vehicles? There are quite a few downsides to EVs. First of all, batteries for EVs need rare metals; for example, lithium. Battery technology is improving all the time but this is a fact at the moment. The demand for copper is also much higher in the EV sector. EVs need three times more copper than conventional combustion-engine vehicles. The amount of copper used in fossil-fuel vehicles is already quite high. A conventional car contains 18 to 49 lbs of copper; a hybrid EV (HEV) contains 85 lbs of copper; a plug-in hybrid electric vehicle (PHEV) uses 132 lbs of copper; a battery electric vehicle (BEV) contains 183 lbs of copper; a hybrid electric bus contains 196 lbs of copper; and a battery electric bus contains 814 lbs of copper (Source: www.copper.org, YES Sec – Research). Wire companies must look for ways and means of offering this metal at competitive prices. In order to reduce weight and cost, some companies have started installing high-strength aluminum alloy wire in the engine harness instead of copper wire which has been conventionally used. Besides, electric cars are more expensive to buy. Existing standard lithium-ion batteries use expensive materials such as cobalt, which raises price. So, the purchase price of an electric car tends to be much higher than that of a petrol or diesel-engine version of the same car. In addition, many electric cars have a range of just 100 miles or less between charges, which means they are not suited for long-distance travel. Also, there aren’t enough charging points.
Electric cars would gain enormous popularity once their manufacturers succeed in bringing price down through more efficient technology. Electrical design engineers are making efforts to reduce wiring mass while improving cost, safety and reliability. The gross weight of the wiring harness using a conventional electric wire is about 30 kg for a car, but weight reduction of about 30 percent is possible by using a weight-saving electric wire. Proper EV charging infrastructure also needs to be set up – and that is expected to happen soon. Interestingly, a manufacturer in the wire and cable industry is setting up a facility to grab the demand from the automotive industry and get ready for the futuristic demand for EV. Needless to say, the need for setting up EV charging infrastructure will stand wire manufactures in good stead, as setting up this infrastructure would entail an additional demand for wires.
Prospects and Demand Growth
Prospects in the wire and cable industry are excellent. The wire and cable space is looking up: It is expected to double over FY18 to FY23 to Rs 1.03 lakh crores (estimate) amid a likely strong power distribution capital expenditure and the growth in the wire segment led by a number of affordable housing projects. The adoption of EV in India would also leverage demand growth, mainly because EV consumes three times more wires than a conventional vehicle. Also, an additional demand would come from the development of EV infrastructure.
The revenue growth of the industry as a whole would be higher than its volume growth, as the industry is focusing on high voltage cables and housing wire manufacturers are moving up the value chain with niche, high-quality products. According to recent estimates, the size of the wire and cable industry in India is Rs 53,000 crores. The size is expected to increase in times to come.
“With different specifications of wire and process, the wire and cable industry will continue to grow in the hybrid EV and EV segments”, says Ravi Baraskar, Managing Director, LEONI Wiring Systems (Pune) Private Limited, in an exclusive interview given to Wire & Cable India.
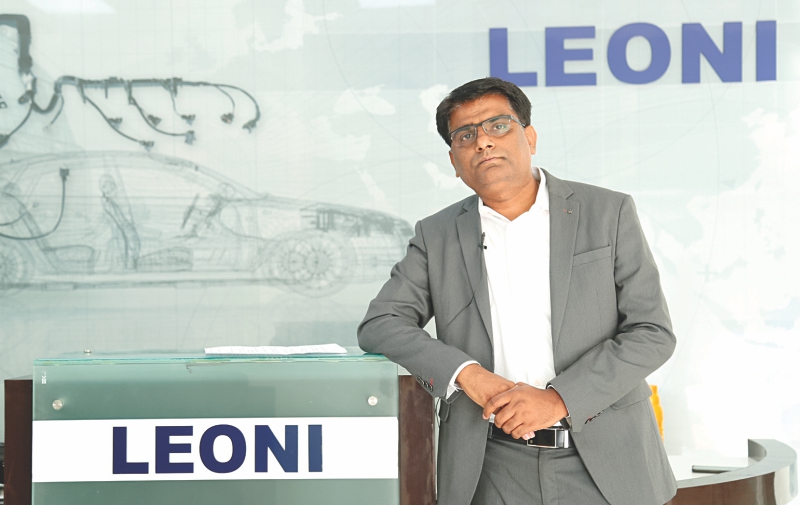
Wire & Cable India: Do you think that with the advancement of new technologies and customer aspirations, applications of cables and wires in automotives have increased considerably with time? Please elaborate.
Ravi Baraskar: Speaking for the Indian market, the answer is “yes”. It starts from transition of BS3 to BS4 electronics engine, and now from April 2020, compulsory to BS6 engine, there are many electronics devices, communication devices, sensors, ABS and added safety features. Due to all these overall changes, customer aspiration and connectivity applications, the amount of wiring systems in automotives have increased.
WCI: Can we say that the automotive industry is driving revenue growth for companies operating in the wire and cable segment?
RB: Yes. We see some global trends that are driving the wiring content in vehicles. The first is that with a rising number of electric and electronic components, for example, entertainment and safety, there is an additional need for transporting energy and data via cables. Secondly, mid-size-car and even smaller cars are increasingly well equipped with such devices, resulting in bigger harnesses in theses vehicle groups. Thirdly, the introduction of electric and hybrid vehicles provokes a higher volume of cabling due to the additional high-voltage harness.
WCI: In order to reduce weight and cost of the wiring harness, some wire and cable companies have started installing high-strength aluminum alloy wire in the engine harness instead of copper wire, which has been conventionally used. Will the use of aluminum alloy wire make EVs even more efficient?
RB: For aluminum alloy you still need to do more things as currently it’s proven for big cross section and longer length. Currently, it can be efficient on the cost and weight front.
WCI: Do you think that the electric-vehicle segment has turned out to be the fastest growing segment of the automotive wiring harness market? Please elaborate.
RB: Yes, as we need to count the next 5 to 6 years, and then real development starts in India. Currently we see EV development for city bus which is on the road. Speaking for the Indian market, pure electric should cross 10K units in 2022 and full hybrid should be 31K. Mild hybrid should be more than 700K units in 2022; and 2030 onward, India should really be on EV.
WCI: The gross weight of the wiring harness using a conventional electric wire is about 30 kg for a car, but weight reduction of about 30 percent is possible by using a weight-saving electric wire. Is your company looking for ways and means of reducing the gross weight of the wiring harness?
RB: There are different means of reducing weight, starting from reducing some of the wire’s cross-sections to optimizing the overall architecture of the wiring system and introducing intelligent techniques. Harness makers should involve themselves in the OEM’s development process without further delay, as that would enable them to add value to the optimization of the vehicle’s overall design. This is all the more important since the wiring harness will become a crucial component for energy and data supply when it comes to higher levels of autonomous driving.
WCI: Do you think the wire and cable industry will continue to grow in the hybrid EV and EV segments?
RB: Yes with different specifications of wire and process. The wiring content will definitely grow because a hybrid car needs an additional HV harness. Pure EVs too – whereas here the combustion engine harness is not needed anymore. Today’s HV harness architectures will change and probably become simpler with the next e-car generations. From the point of view of price, we estimate the average harness price to grow moderately until 2030, due to the shift to EV and hybrid cars.