Mr. Amit Agarwal, Senior Manager, Wire Technology,
Tata Steel Ltd, Global Wires India
In this article of wire speaks, Pre-Stressed concrete wires, will share its experiences, about being used in manufacturing of concrete poles for electricity transmission.
Hello readers! I am PC wire (pre-stressed concrete wire), produced at Global Wires, Tata Steel Limited. I am a very crucial and integral part of electricity transmission concrete poles, which help in letting electricity reach your homes. I am relatively stronger wire, with a carbon content of ranging from 0.81% to 0.85%.
I can proudly state that,
• I provide strength to the pole, by acting as reinforcement.
• I help in restricting the deflection of pole, when it is under load and does not allow concrete to fall.
• I do all this silently, and since, I am inside the pole, you don’t see me; however, I am always there.
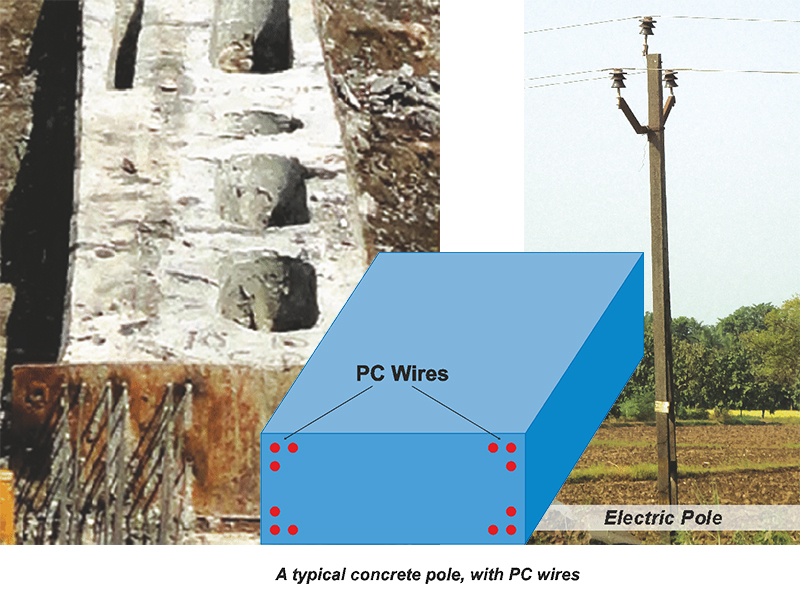
Let me take you through the journey that I undergo, right from my dispatch to the pole manufacturers:
1. Handling and Storage:
I come in big bundles (coils) of I am unloaded manually or with the help of cranes, from the truck, and stacked. In order toprotect me from getting rusted, tarpaulin sheets are put over me.
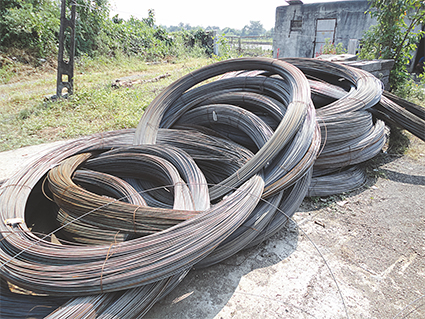
2. Bed / Mould preparation:
Concrete poles are made by casting process. One line has got 2 beds. One bed has 10-16 moulds. In one mould, 2 poles are cast. In the mould, burnt engine oil is applied, for easy removal of pole from mould, after curing.
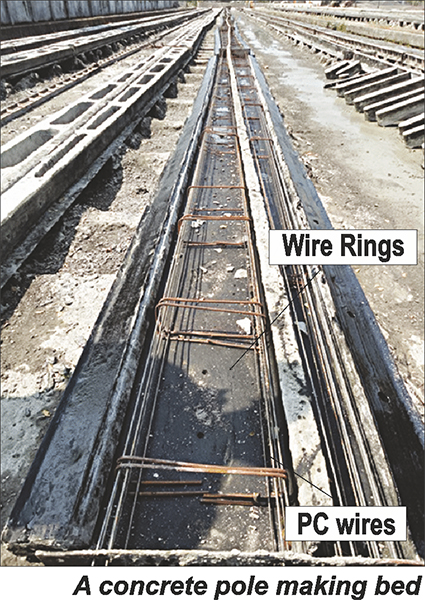
3. My usage in poles:
First of all, rings are made out of me and attached to the poles. Thereafter, I am pulled from inside the poles & rings. Two wires are pulled manually at a time by one person; total 12 wires for one pole, i.e. 24 wires per mould. After pulling the wires that is me, I am locked at one end, using cone & pin locking system.
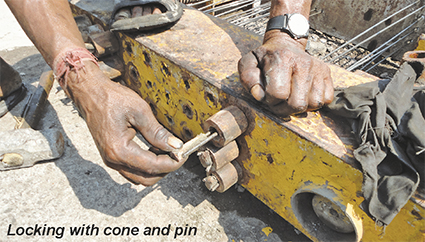
4. Stressing of wires:
Here comes the process, which is quite painful for me, but I patiently withstand the pain, with courage. Wires are stressed using a jack with cone and pin locking system; 2 inch wire is pulled for 8 meters pole. After stressing, wires are again locked using cone & pin.
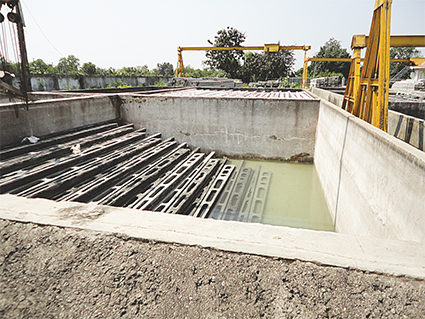
5. Pouring of concrete mixes:
Time comes for my invisibility to you all. Concrete mixes are poured, after fixing of side plates and other steel cores. Poles are kept for curing for 3 days. After 3 days of curing on bed, poles are dipped into the pond, full of water, for 30 days. Thereafter I am ready for dispatch.
6. Testing of poles:
In order to ascertain the quality of poles, tests are carried out by applying load. The tail end of the pole is fixed into a frame of 2 feet, and head is pulled with a certain load using a wire rope. The load is given in equal intervals and released; same time, the plastic & elastic deflections are measured.
During testing, when load is applied at higher levels, cracks appear on the concrete, which subside as soon as the load is released, and guess what… this is due to my presence in the pole.
Now, you must have understood my importance in a concrete pole. I am required around 11.5 to 20.5 kg per pole (for 8 to 10 meters pole). I must possess certain inherent characteristics like required proof stress and required depth of indentation, in order to ensure better quality of poles.
Republished with permission from Taarsansar, House Magazine of Tata Steel Global Wires India