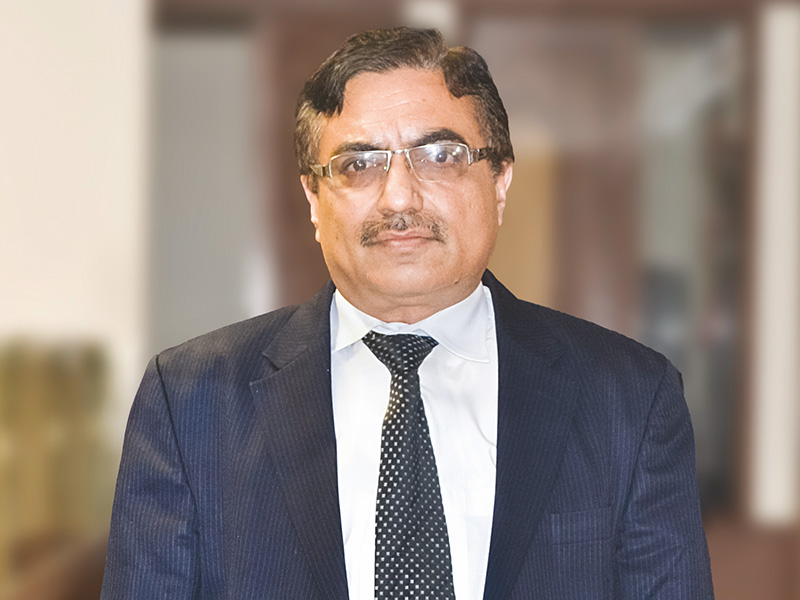
HVPL pledges to light the world with its intricate knowledge and technological supremacy as it extends its business activities into other fields.
Mr. Vivek Kohli is an Electrical engineering graduate with over 35 years of extensive experience as President, Business Head and Chief technology officer in various organizations. He has been heading, driving and ramping up Businesses and having very extensive experience in functions like Business and Market Development, Sales and marketing, Operations, Project management of Power Conductors/Cables and related fields.
Currently actively involved in several projects including expanding the Global presence of the Hindusthan group, Mr. Kohli has played a major role in getting Strategic Technology tie ups signed for HVPL with European companies in the GAP conductor technology and HTLS conductor technology. He has accomplished many first like rolling out of first XLPE cable in India in 1978 and first HTLS conductor in India Developed and rolled out under his leader ship. He has helped several companies to set up EHV cable plants and businesses.
Founded at Faridabad in 1959, HVPL – a leading manufacturer of overhead conductors and underground cables – produces high-quality products at its Faridabad, Gwalior and Guwahti Works with sophisticated manufacturing equipment imported from countries such as Denmark, Switzerland, Finland, Germany, France and China. Of late, the company has been focusing on producing specialised HTLS – high temperature low sag multi strand bigger size conductors required for transmission lines. Also, it has supplied ACSR conductors for 800 KV HVDC; and the various sizes of AAC/AAAC, ACAR, AACSR and ACSR conductors manufactured cover the entire range of high-voltage transmission and distribution lines up to 800 KV.
The Wire and Cable India (WCI) team recently had a face-to-face conversation with Mr. Vivek Kohli, President (Strategic New Business and Projects), HVPL. During this interaction, the WCI team gathered a lot of information about the rise of HVPL, its core strengths and its future targets. The conversation also revealed the role that the senior management core group has been playing in taking business to new heights. The company has recently succeeded in getting a strategic technology agreement signed for the GAP conductor technology and all other HTLS conductors like ACSS and super thermal alloy INVAR conductor technology with European companies.
Given below are excerpts from this interesting interaction.
Product Portfolio and Technologies
With a rich history of constant progress, HVPL has become one of the major suppliers of power products to leading Indian power generation and distribution companies, including refineries. It has exported quality conductors and cables to electricity boards and agencies located in 23 countries. HVPL offers a vast range of products consisting of AAC, ACSR, AAAC, AACSR, ACAR overhead conductors up to 800 KV lines and HT XLPE power cables up to 132 KV, PVC power cables up to 6.6 KV, FRLS cables (power and control), mining cables, shielded instrumentation cables, HR PVC cables to withstand up to 850C, railway signaling cables, aerial bunched cables (ABC) up to 33 KV, LT XLPE insulated power and control cables, and PVC control cables up to 61 cores. Special cables for sub zero -400C temperature applications have also been supplied, and they have been in operation for more than ten years now. In addition, the company recently included new-generation HTLS conductors in its product range.
Speaking about HTLS conductors, the special conductors on which the company has been focusing, Mr. Kohli said, “HTLS conductors (High temperature Low sag) are being considered by the electric power industry as a replacement for conventional overhead transmission line conductors. These conductors are also referred to as either highly-efficient conductors or high-performance conductors. The HTLS conductors are designed and manufactured to tolerate lower sags and temperatures. HTLS conductors can handle a higher current-carrying capacity, sometimes twice for the same diameter of the conductor. HTLS conductors exhibit lower sag as compared to conventional conductors at higher operating temperatures. Various technologies available in the area of HTLS technology have led to a number of HTLS conductors being commercially available”.
“ACSS, the Aluminum Conductor Steel Supported (ACSS) bare overhead conductor, was first developed in the 1970s. ACSS conductors are used in up-rating the existing transmission lines and in new lines to transfer more electrical power and give support to system reliability. It is predominantly used in countries such as the United States, France and Canada. Till date, thousands of kilometres of ACSS conductors have been installed throughout North America and Europe and ACSS is gaining ground in the overhead conductor market“. Mr. Kohli also said that “ACSS is one of the most cost-effective technologies available, but it may not fit in all the applications.”
“ZTACIR conductors use a combination of Aluminum Clad Invar (a special Fe-Ni alloy with very low thermal expansion coefficient) for the core and super thermal resistant Al-Zr alloy for the conductive layer. This allows low conductor thermal expansion coefficient that limits the sag increase with the increase of the temperature and maintenance of the mechanical strength of the conductor with continuous operating temperature up to 210°C. ZTACIR-type conductors have been used in many areas in Japan and Asia and in some parts of Europe. However, this technology has a disadvantage: It’s not cost-effective and the sources for getting INVAR are limited”.
“GAP-type ZT-aluminum conductor steel reinforced (GZTACSR) uses heat-resistant aluminum over a steel core and has been developed in Japan in the 1970s. It has been used in Japan, Saudi Arabia, Malaysia and Kuwait and is being extensively implemented by National Grid in the UK. In India, PGCIL has completed a few projects using the same. These conductors have a special construction feature with a small gap filled with grease between the high strength steel core and the thermal resistant Al-Zr alloy conductive layers”.
“Due to its unique installation methodology, the conductor’s knee point is located at installation temperature without pre-tensioning. This is a very important fact because in other types of conductors, knee point is located in the range of 100ºC, and then the conductor does not work like low sag conductor below this temperature. In the case of GAP type conductors, because knee point is located at installation temperature, it works like a low sag conductor from this temperature, providing a superior performance in the ‘intelligent’ working temperature range (60ºC to 120ºC), where the losses are not too significant. In the earlier days, the installation process of this conductor was quite tough, but our technology partners from Europe in hardware and installations have not just automated this installation but also made it very simple and safe. This technology claims to have the best ratio in terms of price/performance,” said Mr. Kohli.
HVPL has been focusing on other types of new technologies in a big way. “We are in the process of manufacturing a new ‘hybrid conductor’. This type of conductor has a central carbon core, which is made up of carbon fibre and glass. This technology is quite new and is based on composite technology, and we have put in a lot of hard work in the same. There are very few suppliers of carbon core in the world and so this technology has the limitation of central core supply on the market and operates in very protective markets, thereby limiting the competition. HVPL is in the process of entering into export markets with this product soon”.
“Another technology that has recently been started is known as Aluminium Conductor Composite Reinforced (ACCR) which has been developed by 3M. The core is an aluminum-matrix composite containing alumina fibres, with the outer layers made from a heat-resistant aluminum alloy. The low-expansion coefficient of the core contributes to a fairly low knee point, allowing the conductor to make full use of the heat resistant alloy within existing sag constraints. This technology has the highest cost, and its use is therefore in very limited markets as of now”.
“The cost of these HTLS conductors is surely more than that of conventional conductors. If X is the cost of the ACSR conductor, then cost of ACSS, is about 1.8 times; GAP conductor is 2 to 2.5 times; carbon core conductors is 3 to 3.5 times; Invar type is 4 times; and ACCR is more than 5 times. So we feel that that both ACSS and GAP conductors can be the most viable techno-commercial solutions. Though the cost of the conductor is higher, the overall transmission cost in re-conductoring the line is much lower than putting up a new line,” said Mr. Kohli.
Technological Collaboration
Speaking about the company’s technological collaboration with two strong European technology players, Mr. Kohli said, “We are backed by strong European partners having in-depth experience in areas such as raw material, design, manufacturing, hardware and international projects and the ability to provide end-to-end solutions. We have added quite a few products in our portfolio like GAP type, ACSS, Super thermal Alloy Invar and other types of HTLS conductors. When we collaborate with companies that have the ability to guide us with their expertise, experience and background, we add greater value to our products. We offer products as per the application and work closely with our partners to identify the best fit for the requirement, keeping the best techno-commercial solutions for our customers. Our technological collaboration with our partners and emphasis on innovation have surely played a vital role in enabling us to gain an edge in HTLS products.”
Innovation and Quality Assurance
HVPL’s new generation HTLS conductors and aggressive plans to enter some of the diversified products underscore its commitment to product innovation. Innovation is also seen in its approach to conservation of energy. HVPL has grid-connected wind power plants in Rajasthan and Madhya Pradesh and a state-of-the-art solar power plant with parabolic structures at Faridabad Works. Interestingly, this is the first solar power plant put up by a cable company in India.
HVPL always ensures that its products exceed the expectations of its customers. This is the reason why each of its products goes through rigorous quality tests. Stringent quality assurance practices are followed in each of its manufacturing facilities to ensure that HVPL’s products are compliant with ISO 9001:2008 and ISO 14001:2004 standards.
“To ensure that our customers enjoy our technology without any hassles, HVPL strives for quality and excellence in its products. Our passion for superior performance, quality, unmatched commitment, seamlessness and speedy response time signifies our dedication to our customers,” said Mr. Kohli.
Business as Usual
The sluggishness that the power conductor market in India saw last year and is currently witnessing has not been able to thwart the company’s competitive spirit. “The Indian power conductor market has not been lively of late, mainly because the Power Grid of India has not been inviting tenders. So there is a lack of orders in our field of activity, and the dearth of orders has pushed many companies in the industry to the brink of closure or reduction of operations. Our past performance and delivery have enabled us to win a big order from the Power Grid a few months ago. It will keep us busy for some time at least. To be able to cater more competitively in the east, north east and south-borne markets, we are setting up a new unit for conductor manufacturing in Odisha. We plan to add state-of-the-art machinery at this location and dedicate this unit towards the manufacture of HTLS conductors. This plant will be integrated backwards to derive a cost advantage and that will help us to offer a competitive price to our customers. Currently, we have three manufacturing units for power conductors and one unit for HV power cables. All our units are strategically located in close geographic proximity to end-customers. A good mix between the best of equipment and an experienced technical and commercial team has enabled us to continuously produce quality products. This has played a vital role in creating brand image as a quality player on both domestic and international markets. With a strong focus on quality, delivery and costs, we aim to win several tenders in domestic as well as international markets. We are focussing on a well-defined strategic shift from a product-based to a solution-based company”.
“Our R&D efforts have led to our manufacturing various types of HTLS conductors. To meet our group’s mission and vision, “to be a global leader in sustainable energy solution with the best of the quality, technology and competitiveness”, we are all set to target these products on international markets and we are confident of garnering a reasonable market share as these new generation HTLS conductors are widely used on several global markets and there is acceptability of HTLS technology depending upon application,” said Mr. Kohli.
Future Targets
Speaking about the company’s future targets, Mr. Kohli said, “While we will continue to drive power business for niche markets, we have decided to diversify into other businesses and are currently exploring the speciality chemicals and infrastructure business for addition to our portfolio. We are the first power product company to add new diversified and specialised products to our portfolio. This is a strategic shift, and we are using our strong business strength for venturing into these new areas”.
“Though we exported our first overhead conductor in 1961 and have over 50 years of experience in the power conductor business, we are looking towards niche international markets for specialised products. We have aggressive plans to penetrate the export market. We recently concluded an order for Europe, which passed all the tests and met all stringent quality standards. Our focus on high-quality products, packaging and on-time delivery commitments has inspired a lot of confidence – we know for sure that we can deliver on the global market.”