Screened, separable connectors in EPDM have been widely used with enormous success for over 50 years. Many utilities and industrial companies have already introduced these products into their network, next to the silicone connectors, which have been on the market for 30 years. At the request of the market to provide more compact solutions for higher currents, new connectors were developed recently. Euromold-Nexans used this demand to redesign their most popular interface C (630 – 1250 A) connector line. The products were conceived in such a way that the production process could be automated as much as possible. A robotised production process is a very stable production process resulting in a product with only very small variations in physical properties.

Introduction
Euromold was created in the early seventies by Amerace Company to produce and distribute connectors to connect underground cables to electrical equipment on the European market. At that time shielded EPDM connectors were already very popular in the United States. The first initiative of the Euromold team was to create the interface B bushing to standardise it and to develop, produce and commercialise a separable shielded connector to apply on this bushing. The company became a Nexans subsidiary and further developed its own products portfolio by standardising the interface C bushing and by developing a complete new connector line dedicated to it. Thanks to its long experience and because the company decided to keep the full mastering of connector process (research and development, industrialisation, production), Euromold connectors continue to be valued for their high performances and reliability levels.
Since the beginning of the century, the need for a more compact connector was strongly expressed by switchgear manufacturers to fit in more modern gas-insulated switches. As a consequence of this evolution and coupled with the building of wind energy and solar parks, the market demanded a compact double connection for larger cables.
Requirements for a New Product Line
The EPDM connector is, due to its thick conductive layer, famous for its safety and reliability (minimum 40-year lifetime). All products are 100 per cent routine tested in the factory. All products carry a traceability number to enable a total quality control.
While redesigning the interface C (630 & 1250 A) connector line the following objectives were given to our engineers to design a new product, which had to be as safe and reliable as the existing one while being much more compact (double assembly to fit in the new switchgear generation). It should generate less references and stocks for the customer for the largest range of cables and be deliverable quickly when requested. The process should necessitate as less manual intervention as possible in order to reach a very high stability level. Lastly, the 100 per cent routine test and marking had to be kept as an additional guaranty for the customer of the quality of our products. Once we turned these customers-oriented features into product ones, we issued the following technical specifications for the so-called new 430TB connector:
• Keep EPDM as raw material. Our long experience in the connector business convinced us that EPDM is the most appropriate rubber for this application
• Develop a connector range covering from 95 up to 1200 mm2 cables, integrating bolted contact technology developed by our subsidiary GPH-Nexans
• Slim, easy-to-install product with a design allowing robot handling
Compared to other material types, EPDM connectors offer a much higher degree of reliability to the operators. Additionally, the stability of the conductivity of the external thick EPDM layer has been proved to be much superior to other common materials, especially in an ozone-rich environment.
Material Studies
While silicone compounds are standard catalogue raw materials, EPDM compounds are in-house developments. In order to use these compounds in an automated process, we have to be sure that the quality deviations are under control. Therefore, an experimental study was set-up for the mixing process of the insulating materials, related to the injection process.
Our decision to keep EPDM materials for our connectors was additionally supported by comparative studies performed in our laboratories on the necessary force to disconnect different types of connectors from an epoxy bushing (EPDM and silicone ones from different suppliers).
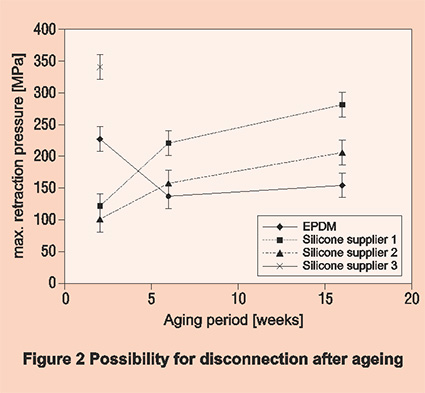
Although Silicone connectors performed initially better than our EPDM connector, after a longer period of ageing (here six weeks at 75°C), the latter one outperformed the others. The retraction force for connectors from EPDM connectors decreases below the values for the connectors of the Silicone ones. We also observed that only in the EPDM connector, the grease layer preserves its lubricating properties. The Silicone connectors absorb the grease in the interface between the bushing and the connector, which results in a longer application period for the incapacity to separate the connector from the bushing when necessary.
Another advantage of the EDPM connector is the 3mm thick conductive outer layer, whose properties remain stable in time:
• Conductivity, ensuring a screened connection
• Mechanical stability
• Failure recognition (the screen fault initiation test (CENELEC) passed at 6kV level, meaning the system will detect a possible connector fault even at operating voltages as low as 6kV.)
• Excellent ageing properties
Validation of the New Product
Once prototypes were ready, an official test programme was performed to validate the design. The products were tested according to the Cenelec HD629 standard (which exceeds the requirements of IEC 60504).
During in-house tests some specific properties of the product were investigated:
• The force to disconnect the product after some time of installation
• Long duration tests (over 9 months) to prove the stability of the insulation properties
• Conductivity of the outer semi-conductive layer, especially in humid or ozone rich environments
Extension of the Product Range
In addition to the standard 430TB product, the following associated products were developed:
• A coupling connector 300PB
• A 10 kA surge arrestor 300SA
• Extension to 36 kV voltage class
• Extension to larger cross sections up to 1200 mm² 484TB and 489TB
These products were validated according to the existing standards: the connectors according to HD629.1 S1 and the surge arrestor according to IEC 60099-4.
Additional accessories were developed around the new product line, such as test rod and voltage indicator.
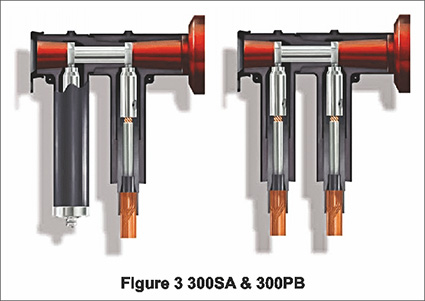
Summary
The new connector meets the new demand of switchgear manufacturers. Its major properties are:
• Due to the high degree of automatisation, a constant quality is delivered, without the interference of manual operations
• The design with the thick conductive EPDM layer is kept, which offers an advantage against pollution, touchability, mechanical stability, adsorption of grease, failure recognition, ageing properties
• The 100 per cent routine test is still guaranteed and integrated with the process
• The material compounding is modernised and under absolute control
All our products are tested in accredited labs to validate the designs. The five-year-long testing has proved beyond any doubt the stability of conducting and insulating properties and the quality of the whole product. n
Written by H. Keymeulen,
Nexans Network Solutions N.V. – Div. Euromold Zuid III,
Industrielaan 12, 9320 Erembodegem, Belgium
References
[1] S. Chatterjee, “Sicherheit und Zuverlässigkeit von Kabelsteckern”, Elektrizitätswirtschaft, Jg. 84 (1985), H.26, S1111-1117)