September 30, 2013
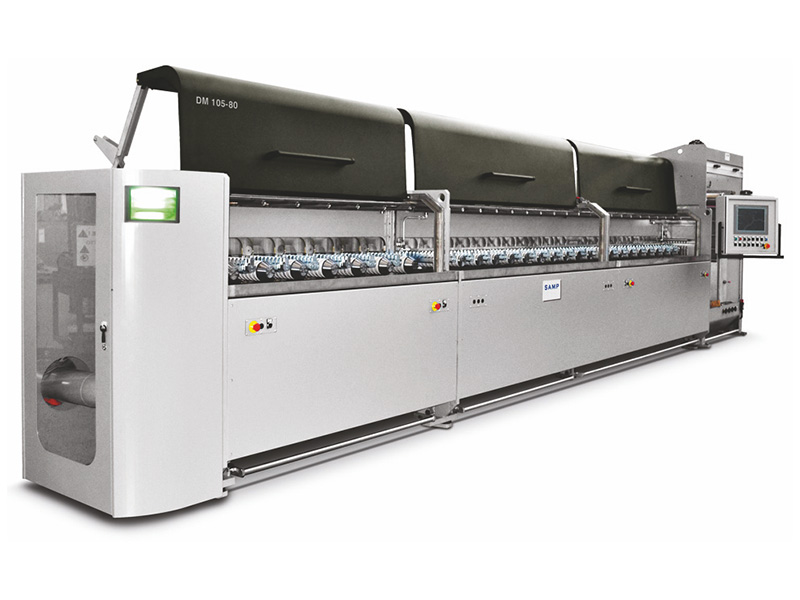
SAMP has introduced a complete multi-wire drawing line for 16 copper wires, which comprises a DM 80 drawing machine, an RC 200 annealer and a DS 800 dynamic spooler.
The DM 80 is part of a new generation of multi-wire drawing machines built according to a highly innovative concept. Indeed, the SAMP multi-wire drawing machine platform builds on many years of research and in-depth testing. The result is a series of modular machines that sets new standards in the wire manufacturing sector. In particular, the DM platform is capable of:
• Reducing production costs by increasing the energy efficiency and power factor (cosф) of the manufacturing line.
• Increasing the line productivity by diminishing setup times, reducing and simplifying maintenance operations, ensuring an easy accessibility of the machine spare parts.
• Maximising the process efficiency, thanks to a significant reduction of the acceleration and deceleration ramps.
The DM platform comprises four product segments, designed to meet every possible customer requirement depending on their final application (building wire, white/brown goods, automotive, etc.).
DM 80 EL (entry level): up to 8 wires per row and 22 drafts, max. inlet wire: 3.60 mm;
DM 80: up to 10 wires per row and 37 drafts, max. inlet wire: 2.05 mm;
DM 105-80: up to 16 wires per row and 29 drafts, max. inlet wire: 2.60 mm;
DM 105: up to 16 wires per row and 25 drafts, max. inlet wire: 3.20 mm.

The three main characteristics of the DM platform can be summarised as follows:
• Mechanical driving power distribution independent from the machine kinematics, thanks to highly efficient, high-torque brushless electric motors.
• Presence of fewer machine components for easier maintenance operations and reduced lead time of spare parts.
• Line automation and motion control architecture suitable to the most advanced platforms available on the market.
In order to achieve these goals, SAMP has developed a completely new mechanical project, carefully redesigning all sub-elements of a drawing machine (frame, transmission, spindles, seal systems, die holders, pulling rings and ancillary equipment). At the same time, the machines maintain the technological peculiarities that have always characterised SAMP machines, such as the wire interaxis, the alignment between die and wire, the pulling ring geometry and lubrorefrigeration. In doing this, maximum reliability and simplicity have always been the top-priority.
The DM platform features a new gear train, designed and engineered by the Sampingranaggi division, which ensures maximum, vibration-free performance and a significant reduction of the noise level, so that no soundproof cabin is needed. Therefore, as an additional advantage, DM machines have a smaller footprint. The mechanical driving power distribution and the machine kinematics allow an overall slip reduction. This, in turn, leads to a significant reduction of noise and a considerably lower energy consumption of the line.
Particular attention has been given to ergonomics and man-machine interface by a clear and rational distribution of services and accessories. The final result is a pleasant and simple design, which can be considered a reference model for the market.
All DM machines are equipped with advanced tele-service devices, thanks to the innovative tablet and Cloud technology. Moreover, the line can be easily linked to existing management software.
After in-depth testing both at SAMP Technology Centre and in numerous customers’ premises in real working conditions, DM machines have obtained outstanding results, showing a better wire quality, an average energy consumption reduced by over 30 per cent and a power factor (cosф) higher than 0.95.
At a glance:
• One drive and one motor used on the whole platform
• Designed for copper and aluminium wires
• Energy consumption reduced by over 30%
• Better wire quality due to one or more adjustable slips
• Outstanding acceleration/deceleration ramps (< 15 s from 0 up to 30 m/s) to improve productivity on small reels/coils
• Noise level: max 82 dBA
• Visual tele-service via tablet and Cloud technology
• Zero preventive maintenance