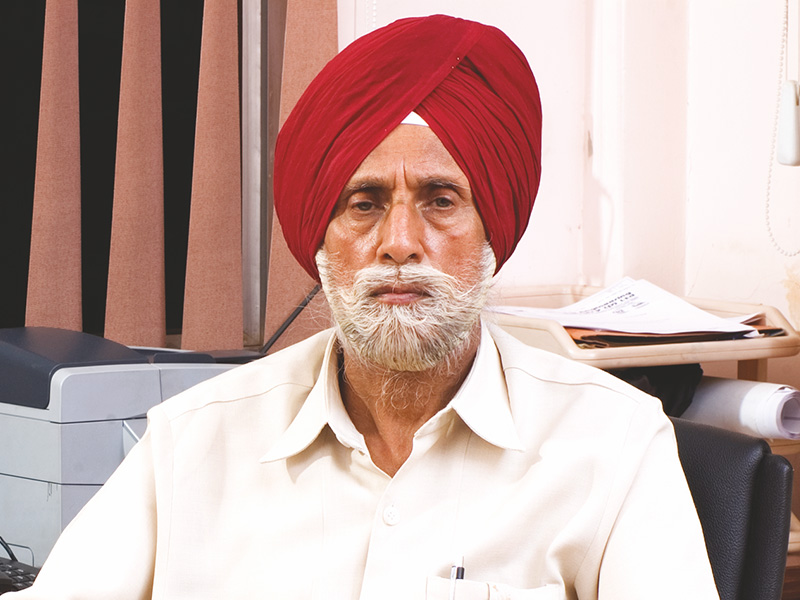
Most of us would agree that the term “local machinery”has negative connotations: It bespeaks impersonality. But when we start talking about Supermac Industries, we are compelled to change our preconceived notion. There is something about Supermac that brings a smile to our face. What is it that makes Supermac so different? To get an answer to this question, team WCI had a warm, rambling conversation with Mr. Harbhajan Singh, Chairman, Supermac Industries India Ltd, who intelligently summed up the history, infrastructure, technological capabilities and philosophy of Supermac. Here are a few excerpts from this unforgettable interaction with Mr. Singh.
Wire & Cable India: Tell us about the journey of Supermac Industries.
Harbhajan Singh: We founded Supermac Industries to provide high-end manufacturing systems and process technologies for cable industries the world over. Over the years, it has provided world-class technology and system for cable industries. It gives me great pleasure to tell you that Supermac is a renowned name in today’s cable industry; and let me also tell you that we owe our success to shear hard work, true dedication and utmost determination.
WCI: Give us an idea of Supermac’s infrastructure and the technology it has adopted.
HS: Our three technically advanced production units in Manesar and Delhi spread over an area of 95,000 sq. ft. They play a significant role in realising the company’s vision for research apart from manufacturing and delivering high-end extrusion lines for varied cable manufacturers. The manufacturing hub is powered by advance CNC equipment responsible for manufacturing high-end precision components for extrusion lines.
The New Delhi unit has a special division for manufacturing screws and barrels outfitted with special purpose machines for screw-cutting, polishing and special purpose barrel boring machines for accuracy and higher production along with a setup of special gauges for checking bore straightness and concentricity. To ensure high quality standards, the screw and barrel material is imported from Germany. The unit has a capacity of 100 sets of screw and barrel per annum.
Our Manesar unit is for assembly of extruders, and cross heads is one of the most advanced setup with a capacity of 5-6 extruders per month. Superlative quality standards are maintained through the use of imported components like cross head material from Austria, extruder gearbox from Italy, motors and drives form Germany and blowers from Spain. This policy ensures quality at par with European standards with the added benefits of indigenous manufacturing for the customers. The unit is equipped with special grinding machines meant for grinding cross head parts. The facility is capable of manufacturing annually more than 100 cross heads of varied sizes in single cross head, dual cross head, triple cross head, self centered and manually centering. The unit also has the capacity to manufacture 5-6 caterpillars and 5-6 take-ups and payoffs every month. Materials are sourced from the finest international counterparts to ensure consistency in class quality.
The division is equipped with advanced in-house matching and panel building facilities. Testing and trials of all complete lines are done before readying for dispatch. The division can efficiently deliver 3-4 complete extrusion lines every month.
A dedicated team of engineers works round the clock to ensure that the company’s commitment to unparalleled support stands true. The commitment is made possible by a huge inventory of spares and channel process flow from manufacturing to service and delivery. Every single component of Supermac cable machines is produced in-house. This efficient supply chain management helps to manage on time delivery.
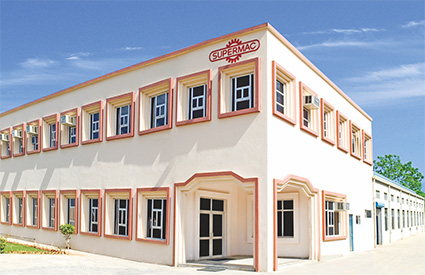
WCI: Share your mantras for good performance.
HS: Supermac believes in change. It firmly believes in setting new benchmarks and consistently widening the envelope for the cable industry. Its strength in engineering coupled with an extraordinary technical team gives it an edge over other companies in the same area. The team works on design and development of logics and software to recommend necessary improvements in existing products while coming up with new value-added products for the future. The company follows strict engineering standards for its engineered products. All of its products are validated in-house ensuring the finest quality it is known for.
Our infrastructural strength comes from our vision for groundbreaking developments in the field of extrusion. This approach has turned us into a technological leader. We are the only Indian company to have in-house automation, panel making and testing facilities. Our exemplary product line is the result of a robust manufacturing setup at par with the best in the world.
WCI: Elaborate on your product offerings.
HS: We have already successfully deployed more than 400 lines in India and abroad. The range of our products includes:
• Insulation and sheathing lines for power cables
• Sheathing and jacketing lines for PIJF telephone cables
• Insulating line for control cables, building wires, automotive wires
• Sheathing lines for optical fibre cables
• CCV lines for medium voltage cables up to 66kV
• Sioplas line for MV cables up to 33kV
We also manufacture ancillary machinery and components including Extruders up to 175mm screw diameter, pay-off and take up stands up to 4.5 meter height and to load 40 tons weight caterpillars, capstans and cross heads.
WCI: Summarise your quality policy.
HS: Quality is the lifeline of our company. Our commitment to quality has earned the company the prestigious Gold Awards at Quality Summit in New York. The company has also been awarded the CE Mark for its high quality products. Not the one to rest on past accolades, Supermac is consistently working to make improvements on existing procedures and to derive new improved quality control and enhancements. All its processes are governed by stringent ISO guidelines and its in-house quality control technique. Supermac is marked by its determined pursuit of excellence. Innovation, both in process or technology and thought, has made it a world leader in extrusion lines manufacturing.
WCI: Tell us about the new developments that have taken place in your company.
JS: Our new generation extruders are perfectly adapted to the demands of processing newly developed materials like PVC, FRLS, XLPE and ZHFR. The incorporation of energy efficient torque motors are coupled with high torque gear boxes to meet the challenging demand of processing new materials.
The screw barrel geometry is a result of 39 years of rich experience in extrusion field and handling of various polymers. The extruder incorporates the 3-stage high torque helical gearbox meant to deliver high torque. System is delivered with a splash cooling and force cooling lubricants system depending upon the requirement. The combination of latest generation of asynchronous motors and drives and perfect design of screw, barrel and feeding zone results in absolute no pulsation even at low RPM. The demanding nature of new polymers like ZHFR, which are very sensitive to friction heat, are also extruded easily.
The barrels are offered in nitrided and bimetallic version depending upon the process requirement. Barrels are honed and designed to bear the max pressure of 1000 bars. Barrels are grooved linear or helical depending upon the polymer and process requirement. Screws are made of nitro alloy polished and bored for heating/cooling with a thermo-regulation system. Extruder is provided with melt pressure gauge and transducer for keeping a check on pressure building in extruder.
The space-saving mobile extruders usually operate in conjunction with the fixed horizontal extruder. Thus, in combination, they provide extra flexibility to insulate automotive wires, building wire and control cables, etc., and are also employed as auxiliary extruder for skin insulation, striping and colouring. It is grounded by foundation bolts and provides mobility in all four directions, i.e., backward, forward and both sideways. It ensures that its mobility leaves no impact on the quality of the products and provides the ease of cleaning and changing the screw and cross head as well and manages the thermal expansion of the main extruders. Extruder control is through a modular automation system, which is assembled in line as per customer requirement and optimises the extruder as a single unit and as a part of complete line. The implementation and designing of all control concepts take place in Supermac’s own electrical engineering department. In brief, we have quite a few feathers in our cap, and we take healthy pride in telling the world about our achievements.
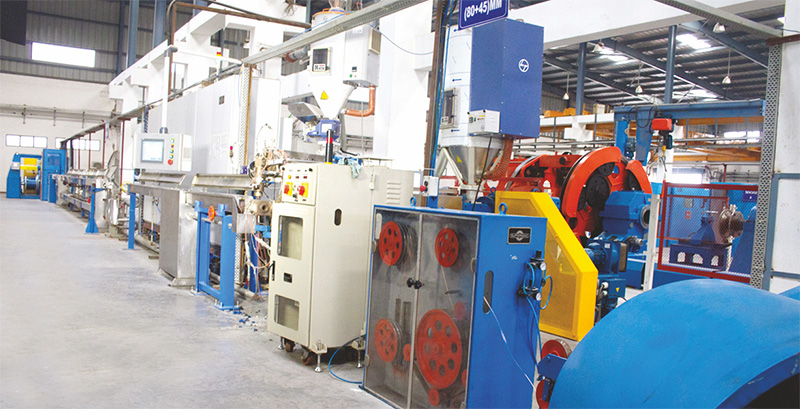