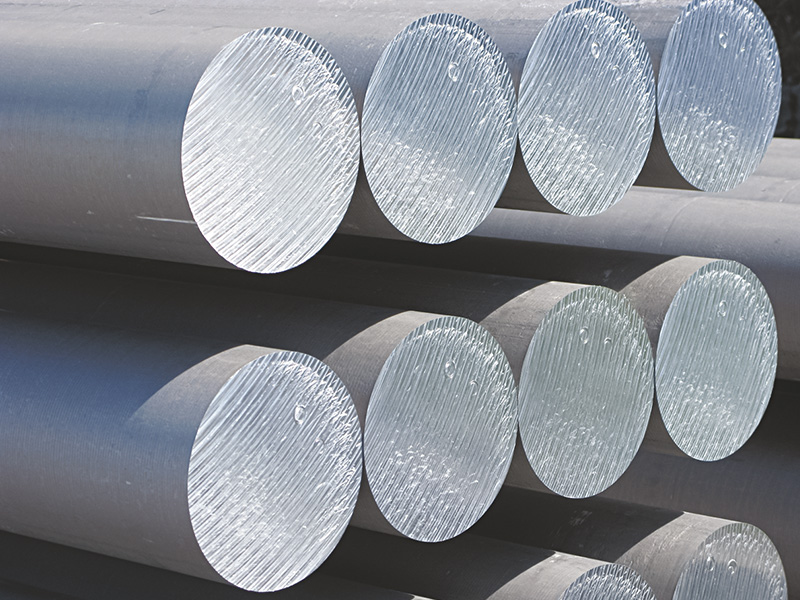
The growth of demand for aluminium in the global automotive industry is one of the most striking trends in materials today.
One forecast by a US consultancy, Ducker Worldwide, is that the global use of aluminium in passenger vehicles is likely to surge by 65 per cent over this decade.
It’s not hard to see why.
European legislation on CO2 emissions and demand from consumers and regulators alike to improve fuel efficiency means that vehicles have to lose weight. After years of getting heavier, cars are going on a diet.
That means using more aluminium. It is already being used extensively by Jaguar Land Rover, which started switching its car bodies to all-aluminium in 2009, but it will soon be used for mass market vehicles. According to management consultants Alix Partners, the proportion of conventional steel in a typical car will fall from two-thirds today to about one-fifth.
So the message for all component makers in the automotive supply chain is: think aluminium. And all companies in the supply chain must also be able to guarantee the quality of this growing output of aluminium components.
That’s because the major car makers are electing to use higher grades of aluminium and are setting higher technical standards of performance. There is no room for false economy.
Aluminium fluid transmission pipes – such as brake pipes – and multi-port tube for heat exchangers are two specific applications in the auto industry for which Meltech’s Continuous Rotary Extrusion (CRE) technology has established a strong global presence.
“CRE is the technology of choice where efficiency, output quality and reliability are the key factors,” says Peter Drever, Managing Director of Meltech CRE. “And for any manufacturer in the automotive supply chain, those certainly are.”
This is because the CRE process provides better metallurgical integrity and enables extremely high levels of consistency, he explains.
A key future development will be the use of foamed aluminium extrusion, Peter Drever believes. “This is definitely an emerging technology,” he says. Foamed aluminium embodies the same strength but is even lighter and uses less material. “It’s an exciting advance in the use of aluminium for transportation,” he adds.
Meltech’s technology is being used to research the capabilities of foamed aluminium at the Light Metals Division of Poland’s Institute of Non-Ferrous Metals.
Of course, it’s not just in the automotive industry where demand is growing – and where Meltech’s expertise at aluminium extrusion is required.
“There’s continuing demand for solid aluminium conductor for high and medium voltage power cables,” says Peter Drever, “and that is another area where Meltech has massive expertise.”
Everything clearly points to aluminium being the material of the future.