MFL Group is preparing to launch a PEEK testing extrusion line at its Italian site in Spinetoli. Polyether Ether Ketone (PEEK) stands out for its superior insulation performance, remarkable chemical resistance, and ability to operate at temperatures up to 240°C.
Sep 14, 2024
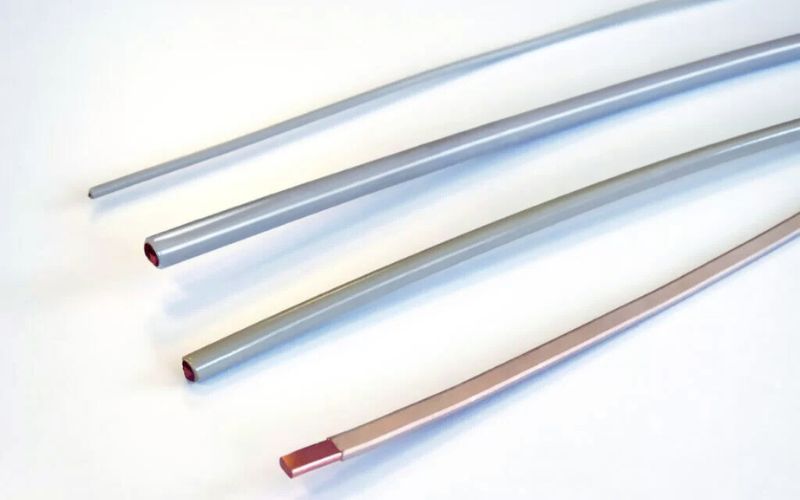
With the increasing demand for advanced electric vehicles, the shift in magnet wire production towards plastic-based electrical insulation is accelerating. This evolution is primarily driven by the latest electric motor technologies, which require greater power and energy density, operating at voltages as high as 1,000 volts.
Watch: RR Kabel | Solar Cables | Solar Plant | Renewable Energy
To meet these demands, motor windings are now insulated using cutting-edge materials like Polyether Ether Ketone (PEEK). PEEK stands out for its superior insulation performance, remarkable chemical resistance, and ability to operate at temperatures up to 240°C. Unlike traditional enameling techniques, PEEK provides increased flexibility, enabling tighter bending radii and significantly boosting energy density due to its thinner insulation layers.
For over ten years, Frigeco has pioneered the development of specialized extrusion lines for producing PEEK-coated cables, particularly for oil pump applications. This experience has allowed them to fine-tune their expertise in processing this material. Recently, the company has made significant advances in manufacturing insulated magnet wire using both PEEK and PPSU.
Also Read: BUSS Strengthens its Presence in Southeast Asia
The company’s technical prowess has yielded impressive results, including precise control over the crystalline structure of the material, achieving minimal insulation thickness while enhancing its adhesion to the conductor. MFL Group now offers complete machinery solutions for insulated magnet wire production with PEEK, covering every stage, from rod breakdown to final extrusion. Additionally, the company is preparing to launch a PEEK testing extrusion line at our Italian site in Spinetoli.