As India aims to achieve last mile connectivity, especially in rural areas, Polycab India Limited, a true-blue Make-in-India company with a wealth of experience and expertise, braces up to evolve and grow with various government projects. Mr. Ashish D. Jain, Executive President & COO, Telecom Business, Polycab India Limited, disclosed during an exclusive interaction with Wire & Cable India that the company is continuing expansions in OFC manufacturing capacity, while also setting its eyes on foreign shores.
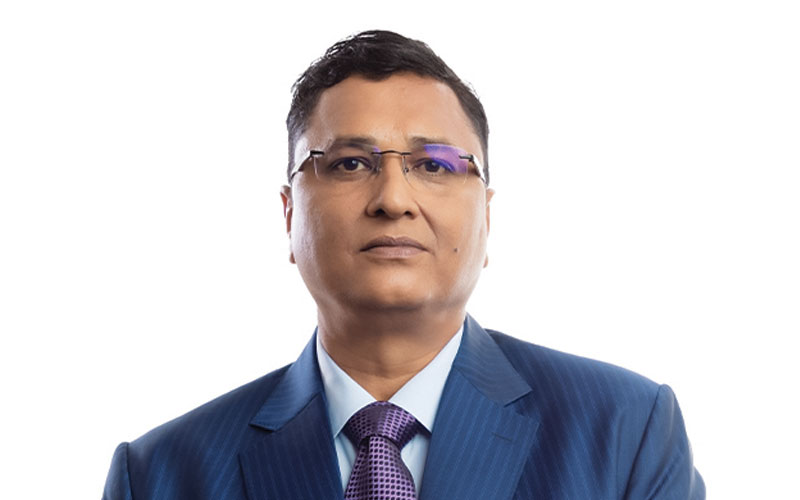
Wire & Cable India: What motivated you to enter the fibre-optic segment and how are you positioned in this segment?
Ashish D. Jain: Digital advances have made a transformative impact on every sphere of daily life, be it business, education, healthcare or government services. The incessantly rising demand for high-speed internet services and dependable communication infrastructure has made fibre-optic deployment a necessity in the rapidly evolving digital era. In the wake of fast infusion of data in people’s lives and increasing reliance of consumers and businesses on bandwidth-intensive applications, manufacturing of optical fibre cables (OFCs) for robust and high-capacity fibre-optic networks was a natural progression for our company, having decades of expertise in making wire and cables.
Today, we’re a leading OFC manufacturer, with a high degree of in-house backward integration and automation capabilities. In a few years’ time, we have diversified to create an OFC-based network and successfully positioned ourselves amongst the top telecom EPC players in India, with one after another successful implementation of large telecom-infra projects. We’ve deployed our OFCs to build OFC-based networks for BharatNet Phase-II projects in Gujarat, Bihar and Tamil Nadu. Furthermore, we’ve continuously been supplying our OFCs to our project and consortium partners.
WCI: What types of fibre-optic cables do you cater to and how unique are they in terms of performance and application?
ADJ: We’ve a dedicated and state-of-the-art facility in Halol, Gujarat, which specializes in manufacturing OFCs ranging between 6 cores to 576 cores. We produce single-mode and multi-mode cables with various designs as per customer requirements, like duct cables, micro-duct cables, armoured cables, FTTH, Fig-8, aerial cables, indoor/outdoor cables, ribbon cables, special cables and hybrid cables. Our specialized fibre-optic cabling solutions and accessories, for both indoor and outdoor purposes, are factory-made to the highest standards. We create fibre-optic assemblies using top quality raw materials.
Our cables can carry the desired capacity of data in a specific network. Not only cables, each of our products is tested and certified to meet the desired capacity of a specified network in terms of data volume and data speed. With the recent commissioning of OPGW (Optical Ground Wire) operations, we’ve extended our business to the power transmission industry as well. Diversification to OPGWs reflects our appetite for evolution in offering data and power together.
Watch: RR Kabel | Solar Cables | Solar Plant | Renewable Energy
WCI: What state-of-the-art technologies do you use to manufacture them?
ADJ: With globally recognized state-of-the-art machines, we’ve an integrated facility for OFC manufacturing, wherein we execute a harmonized sequence of processes like colouring, ribbon technology, buffering, stranding and sheathing. UV curable inks are applied on high-grade transparent fibres with the help of our high-tech colouring machines. With the industry-leading competence, we use ribbon technology to arrange cables in various strips. The process, which is very efficient in managing a large number of fibres in the installations, gets executed by a specially designed machine, the only-of-its-kind in Asia and second in the world.
We have a well-equipped facility to execute buffering or secondary coating process. We perform the stranding process, wherein loose tubes are stranded around a central strength element. A special unit called SZ Oscillator creates an SZ pattern in stranding. Sheathing is done as per the cable specifications. The premium standard compounds like high-density polyethylene, low-smoke zero halogen and nylon PA-12 are used in sheaths for Polycab’s OFCs, giving them exceptional strength and a superior level of protection. We’ve an in-house manufacturing facility for backward integration with FRP, ARP and IGFR Yarns, which empower the cables with armouring and other strength members. In OPGW manufacturing, we’ve adopted technological solutions of the highest order to have compact design and intelligent monitoring technology, bringing in enhanced wiring flexibility, high standards of quality control and excellent maintenance efficiency. We’ve invested substantial resources and created infrastructure for R&D.
WCI: In what sectors do they find their major applications? What other sectors are you eyeing?
ADJ: As the Government of India plans to provide last-mile optical fibre-based connectivity to homes in all villages and BharatNet aims to connect 6.4 lakh villages in the country with broadband internet, our OFCs have a promising opportunity for major applications, including manufacturing and deployment. Simultaneously, we’re also eyeing modernization initiatives of Indian Railways like Mission Raftaar and Kavach, emerging FTTH networks and NHAI’s goal to build digital highways across the country. Further, India needs at least 70 percent of the towers to have fibre connectivity to fully capitalize on the comprehensiveness of 5G-based services and we’re upbeat to make the most of the rising demand for 5G-centric fibre-rich infrastructural requirements for backhaul fibreization. For our OPGWs of 24 to 144 cores, we’re getting demands from the domestic and international power sector. Serving to the large spans between towers, our OPGWs are fit for installation for longer lengths, including over rivers.
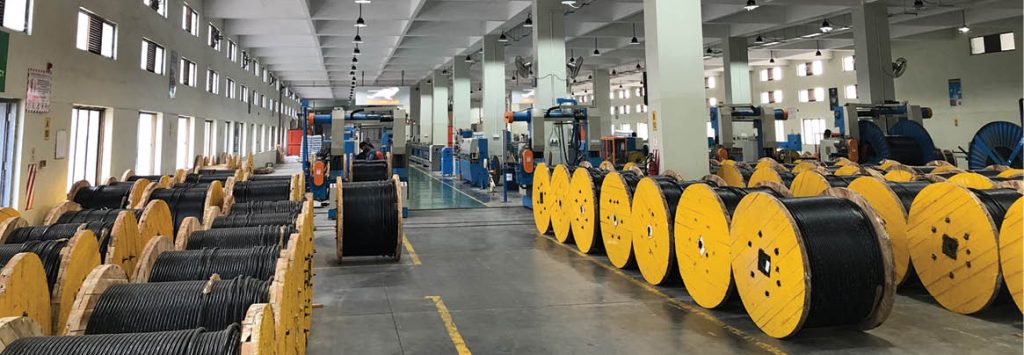
WCI: What are the latest advancements in fibre-optic technology and how might they benefit the users?
ADJ: With technological advancements like Wavelength Division Multiplexing (WDM) and Coherent Detection Techniques, fibre optic transmission has catapulted to unimaginable speeds. Manufacturing of smaller & lighter cables with higher fibre counts and enabling higher data transmission capabilities is a major trend in the industry. Micro-duct cables are being used globally, as they are easy to install and can be blown into ducts. With the new air-blown micro-cable technology, fibre optic installers are capitalizing on lower installation costs and improved construction efficiency.
Innovations in materials and manufacturing processes have made OFC-based systems increasingly healthy, resilient and reliable, offering greater resistance to environmental factors, substantially diminishing signal degradation and improving the level of fault tolerance by several notches. High-density fibre optic cables and connectors have come to the fore in response to the rising demands of users for higher bandwidth and scalability. All the innovations lead us to higher speed of communication with reliability.
Also Read: Finolex Cables: Connecting India with Comprehensive, High-Quality Network Solutions
WCI: How important is sustainability to your operations? Elaborate some of the initiatives.
ADJ: Sustainability has always been integral to our operations. Use of sustainable materials, redesigning of cables, energy-efficiency and responsible water management has been the core of our OFC manufacturing. We always look for optimized transportation logistics to keep a check on carbon emissions as much as we can.
WCI: Please discuss some of the major challenges you have been experiencing.
ADJ: Challenges are part and parcel of our field. But knowing that OFCs now are almost the mainstay of our country’s digital economy, we strive hard to win over challenges. Devious trade practices remain one of the major challenges in the OFC industry. Several foreign players are frequently dumping low-quality fibre at predatory prices in the Indian market. Further, high equipment costs continue to play a key deterrent for manufacturers to go for huge expansion. Lack of quality resources, shortage of vendors & contractors and the scarcity of skilled manpower are other challenges we face in the manufacturing and deployment of OFCs.
WCI: How are you positioned, in terms of market share and production capacity?
ADJ: We’ve continued expansion in our OFC manufacturing capacity to meet the growing demands under BSNL’s BharatNet Phase III, SPV-run BharatNet Phase III and other upcoming projects. We’ve continued export of OFCs and FRP rods, ARP rods and IGFR yarns in diverse customizations to meet the specific needs of our global clients.
WCI: How do you view the Indian OFC market in terms of growth and product diversification? Where do you see yourself in 2024-25?
ADJ: Aligned with the grand vision of our Prime Minister Narendra Modiji, we’re making rapid strides to take broadband connectivity to the remotest villages of the country. In the growing Digital India story, ‘Achhe Din’ for OFC manufacturers are on the anvil for sure. India has an approximate annual production of 100 million fibre kms. With a special emphasis on growing investments in OFC network infrastructure from the Indian government, our country continues to be one of the leading manufacturers and exporters of OFCs in the world.
As consumption of data is rising by the day, there is a growing urge to have its super-fast and dependable availability. Fibre-deployment in our country is the most crucial part to the new and evolving hybrid & remote working culture, and the 5G story. Last mile connectivity has become a more significant currency for evolving networks, which is why OFCs and accessories have a growing market in India.
BharatNet, world’s largest rural broadband project, is continuously engaged in fibreization, creating connectivity based on high-quality OFCs throughout the country. The project aims to spend a whopping INR 1.39 lakh crore in its Phase III to expand and enhance India’s rural internet connectivity, which would give a boost to the entire ecosystem of the Indian wire and cable industry with massive job opportunities. As a true-blue Make-in-India company with a wealth of experience and expertise, we’re keyed up to capitalize on our large network of partners and consortiums to work on various Digital India projects and find a strong growth for ourselves in the evolving scheme of things.