The importance of cable compounds, made from mineral and synthetic raw materials, cannot be overlooked. They play a pivotal role in ensuring the safety, durability, and performance of cables used across various industries.
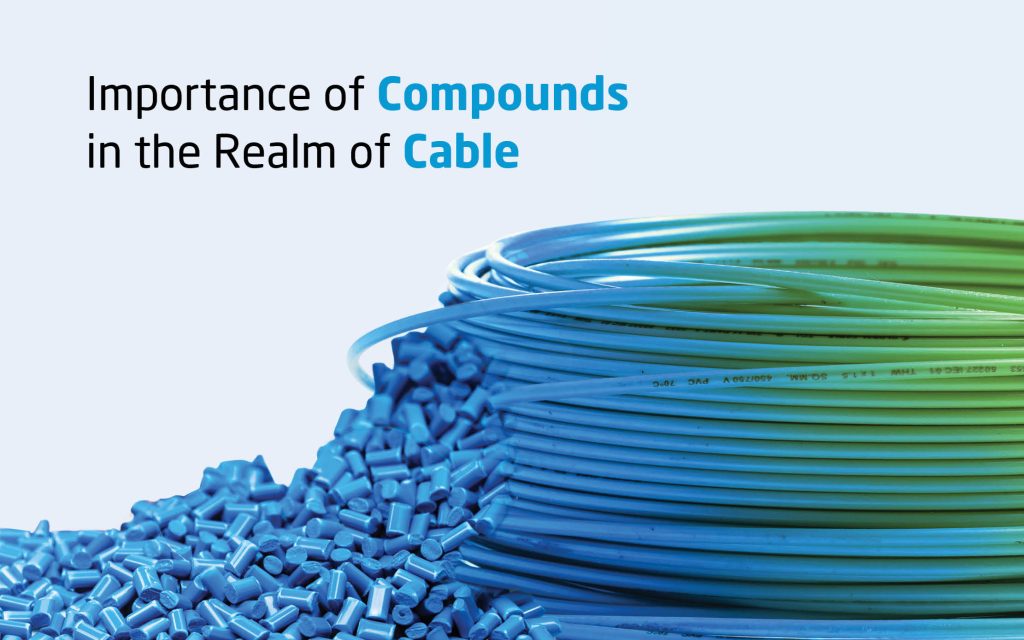
Driven by factors such as growing renewable energy production, increasing reserves in smart grid technology, industrialization, and government initiatives, the cable market is set to witness strong growth with more product diversification. Its global market, which was valued at $74.72 billion in 2020, is, according to Allied Market Res earch, projected to reach $156.49 billion by 2030, growing at a CAGR of 7.8%.
In the realm of cable, the importance of cable compounds, made from mineral and synthetic raw materials, cannot be overlooked. These compounds play a pivotal role in ensuring the safety, durability, and performance of cables used across various industries. On the basis of the polymeric materials commonly used as coatings for electrical cables, three types of classes can be highlighted: thermoplastic polyester (PBT), crosslinked polyethylene (XLPE), and halogenated resins, such as polyvinyl chloride (PVC). Cable compounds are fundamentally used for providing high degree of insulation to wires, and preventing the entry of moisture in power transmission or telecommunication cables. Besides, the compounds are also supposed to impart superior mechanical stability along with corrosive and chemical resistance to the wires and cables.
Portfolio
We manufacture 100 percent RoHS-compliant (including phthalate-free) products as well as RoHS 2.0 and 3.0 compliant products for MNCs, which find application in electrical appliances, consumer products, automotive OEM, medical consumables, and house wiring and cables sectors, says Mr. Deepak Takkar, Managing Director, Takkar Polychem Private Limited. The company is also exploring products in solar cables, telecom, advanced automobile compounds such as T3 compounds, masterbatches, and various other industries.
Similarly, Borouge’s offerings cover low to high-voltage XLPE solutions, and jacketing solutions for power and fibre optic cables. The product portfolio is complemented by its team’s expertise, providing technical services and industry know-how for a well-rounded customer experience, shares Mr. Jong William, its Vice President, Energy & Infrastructure Asia South.
Among the numerous products supplied for different applications in the cables market, the Italian company Mixer’s portfolio includes a wide range of rubber-based solutions. Its medium voltage insulation portfolio includes grades for applications up to 95kV, based on full EPR, EPDM, and EPDM-PE blends, comprising solutions with and without lead. The lead-free grades, it says, have been specifically developed to minimize the environmental impact, keeping excellent insulating performances in compliance with the lead-free directive necessary to access the European market, the RoHS regulation. All these compounds, it claims, are fully compliant with the international standards for 90°C and 105°C operating temperatures and they can be employed both for static and dynamic applications, even in extremely cold environments down to -40°C.
Watch: RR Kabel | Solar Cables | Solar Plant | Renewable Energy
Technology
All these offerings mean being equipped with technological prowess. Finproject S.p.A maintains that it invests heavily in the best manufacturing equipment, machines and testing facility, and this ensures that they have no issues related to ‘the inconsistency of a product performance’. “Our company follows the Industry 4.0 approach. We have a very strong quality management process and certifications such as ISO 9001, ISO 14001, ISO 45001 to ensure the highest technical advancement and good quality of our products,” Mr. Davide Vavassori, its Business Manager elucidates.
Together with Borealis, Borouge has been introducing proprietary technological advances to provide a wide range of energy solutions including XLPE for high productivity and HVDC XLPE cable applications. These aspects differentiate its products ‘from the rest in the market’. “The full polymerization process from feedstock to end-product is fully controlled by Borouge and Borealis, ensuring the highest quality and stability of the products. The company has a unique technology platform that allows it to tailor the molecular structure and the cross-linking degree of its XLPE products to meet the specific requirements of different cable applications,” elaborates Mr. Jong.
On technical capabilities in manufacturing setup that have made it possible to stand out, Shakun states innovation is the key to unlocking growth to the next level and providing a competitive edge over its peers. Another is automation which, it underscores, helps achieve better product quality and process checks. According to Mr. Deepak, heavy investment in research and development leads to the creation of unique compounds with superior properties, giving a competitive edge. “We use various technologies such as Banbury mixers, single screw extruders, and heating cooling mixers in our production processes to manufacture world-class products. The challenges we face include high capital investment, ongoing costs, system integration, and the need for a skilled workforce.”
Universal Polychem sees advanced polymer extrusion technology as ‘indeed a cornerstone for ensuring high-quality production processes’. “This technology allows for precise control over temperature, tool and die design, and the overall extrusion process, which is crucial for achieving consistent dispersion and minimizing degradation. By maintaining batch-to-batch consistency and implementing rigorous quality control and testing, you can ensure that each product meets stringent standards,” elaborates Lalit Bansal, the company’s Managing Director.
Latest
Recently, Mixer has enriched its offer with increased flexibility grades that avoid the scorch issues especially at high extrusion speed. EKOPREN® 3IS73F and 3IS75F for applications up to 35 kV, and EKOPREN® 3IS74F for applications up to 69 kV represent such solutions. Due to the increasing interest for rubber cables suitable for applications up to 95 kV, a new grade named EKOPREN® 3IS721 is a result of a deep investigation and study of the raw materials capable of providing the highest quality in terms of insulation behaviour and electrical properties, it states.
Global chemical and specialty materials company Celanese’s ‘best-in-class portfolio’ of elastomer solutions for wire and cable applications has been expanded with the launch of Hytrel® TPC HTR8908 ECO-B. This new product provides cable manufacturers with a sustainable flame-retardant solution for flexible wire and cable production. Flame retardance, according to the company, in this new solution is achieved with non-halogenated flame retardant.
Also Read: Shakun Polymers: A Long-standing Experience in Specialty Compounds
Sustainability
In every business, irrespective of industry, sustainability has been a cornerstone, and this is considered crucial by all industry players. For instance, 3R Polymers says that all its developments are sustainable and eco-friendly, and the company is into providing non-toxic products with all standards and required grades. “Our products are as per various national & international standards like BIS, IEC, BS, UL, ROHS and REACH for almost all kinds of wire and cable segments. In the next few years, we plan to enter new segments like Halogen-free, high flame retardant, non-toxic, electric vehicle, sustainability and E-Beam,” its Director – Sales & Marketing, Mr. Nitin Aggarwal elaborates.
KK Kompounding Tech Giant observes that the practice is at the core of all operations, and it wants to build a greener future through sustainable products and practices. According to its Mr. Karan Chandan, its Executive Director, “We are committed to minimizing the environmental impact by embracing renewable energy sources, implementing responsible packaging practices, reducing waste generation, and producing non-hazardous, green products. Our team is dedicated to fostering a culture of sustainability and continuously seeking innovative ways to promote a greener future.”
Designing compounds with recyclability in mind and conducting Life Cycle Assessments (LCAs) to evaluate environmental impact are excellent practices, Mr. Lalit adds. “Adhering to national and international regulations and collaborating with customers to develop sustainable solutions further highlights your proactive approach. Our efforts align perfectly with global sustainability goals, contributing to a greener future.”
Prospects and Future
The goal is to continuously grow as a company, with a focus on sustainable and durable products, Mr. Jong asserts. He goes on to say that manufacturing of durable product parts for Energy and Infrastructure will be a key part of the company’s future growth. Asia continues to be one of its priority markets, with huge potential for growth as the countries experience rapid urbanization with increasing demand for infrastructure upgrades. To meet this demand, Borouge, he says, looks to enhance its production capacity to increase its global sales of polyolefin solutions including for the wire and cable sector. “Borouge 4, our fourth expansion of our production facilities, will boost our annual polyolefin production capacity when it is completed by the end of 2025, making it the world’s largest single-site polyolefin complex. We will be investing in 100,000 tonnes per year of incremental XLPE production capacity from our plant in Abu Dhabi. Borouge is committed to the wire and cable industry for the long term. This investment in a second XLPE production plant will strengthen Borouge’s position in specialized materials for the wire & cable,” he elaborates.
Shakun Polymers says that it is currently expanding its semicon production capacities, with a newly installed fully automated world-class semicon compounding facility, from 10,000 metric tons to 30,000 metric tons. “We will have the capacity available in Q2 2024; we expect to grow at 12-15% CAGR. Our mission is to have a single compounding complex manufacturing 100,000 tons of compounds with state-of-the-art manufacturing equipment,” says Mr. Abhinav Bansal, its Vice President -Growth Initiatives.
We are very bullish towards the demands from the wire and cable industry, says Mr. Nitin. “Almost all wire and cable manufacturers are increasing their capacities. We are planning to double our capacity for PVC compounds and start two new production lines for PE-based compounds by the end of FY 24-25.”
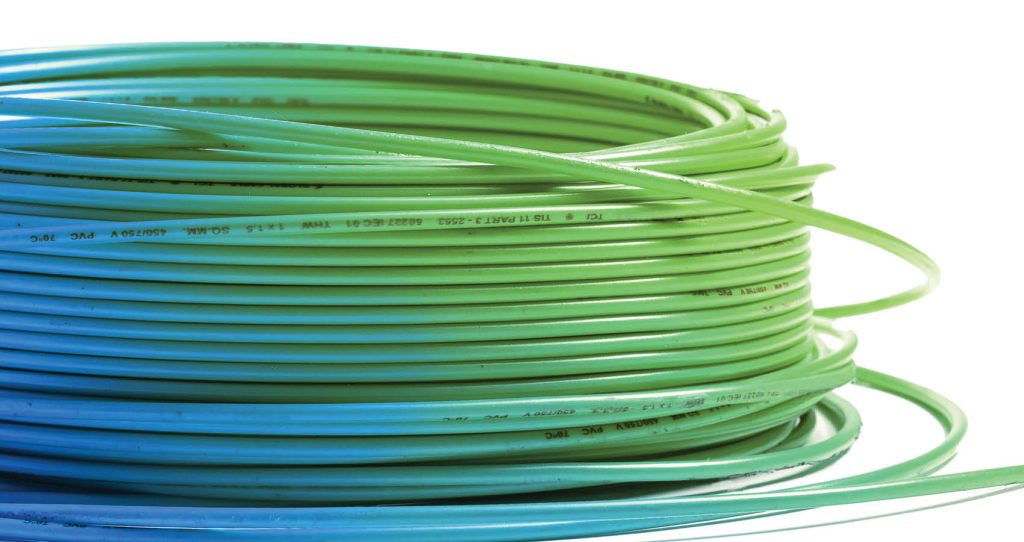