TKT Group, which has been supplying a range of products and services to the wire manufacturing industry since 1945, is planning to enhance its presence in the Indian market. This was revealed by Mr. Fabio Bellina, Vice President, Sales and Marketing, TKT Group, during an interaction with Wire & Cable India magazine.
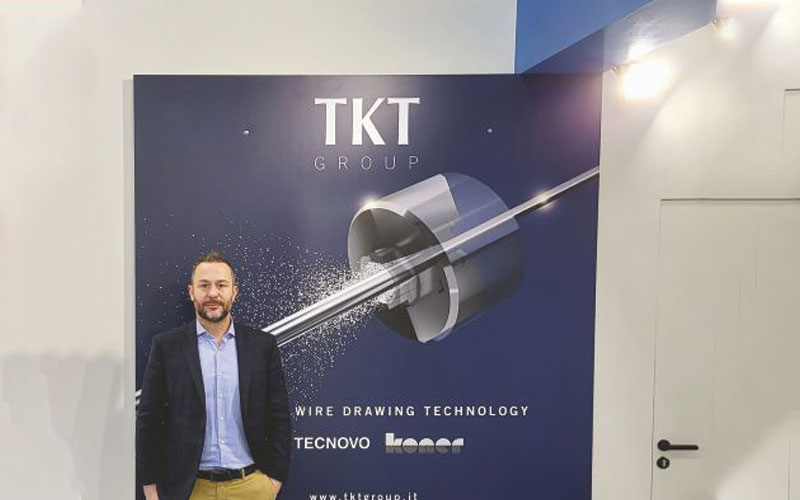
Wire & Cable India: Kindly walk us through your business journey, highlighting major milestones and crucial achievements.
Fabio Bellina: We are a top-ranking global group of companies, which has been operating in the wire manufacturing industry since 1945, producing drawing lubricants and drawing dies. We form a closely integrated operating unit. When we visit your plant, we examine each and every aspect that affects the wire drawing process. The TKT group works together with its customers, giving them the benefit of a highly specialised technical expertise from our companies, which include Tecnovo, Koner and Nuova Lasea.
Tecnovo has been producing lubricants and auxiliary chemicals for wire drawing and processing since 1945. It provides full and prompt technical assistance, starting with the selection of the most suitable products and thorough testing on the customer’s plant by its own specialist personnel.
Koner is a leading company in the field of wire drawing dies. It is committed to a policy of research and innovation both with regard to process & die technology and constantly seeks to co-operate with customers, providing them with complete solutions. Tecnovo technicians work in close cooperation with Koner ones. Joint trials with dies and lubricants mean high performances and synergies achieved according to different conditions.
In the 80s, Nuova Lasea came into contact with the TKT group and specifically with Tecnovo Srl, with whom it established a profitable business partnership. By the collaboration between Nuova Lasea and Tecnovo R&D activities, new formulations were marketed, highly appreciated by the markets. The company operates fundamentally in a niche sector, so that the sulfonates of oils and fatty acids, in which the operative technique requires, beyond an adequate plant engineering, a continuous evaluation of the production cycle and therefore, a high degree of experience and competence.
WCI: Innovation, coupled with research and development (R&D), plays a very important part in the progress of a company. Please elaborate on some of your recent developments.
FB: In the recent years, the TKT group has consolidated and expanded its position in the market and carried out important research & development programs by making investments in new machinery and technologies as well as expansion of TKT products portfolio, to offer its customers increasingly innovative, integrated and synergistic solutions.
Some of our new products include a high-performance ‘dust and borax free’ Tecnovo sodium soaps, which are the result of many years of research for the steel wire drawing market. We have a wide range of round and shaped dies, which can be supplied in solid hard metal or coated with special Koner treatments to enhance their durability characteristics.
We have added new additives in the formulation of Tecnovo green emulsifiable oils, which improve the wet drawing process in terms of lubrication and drawing performances. Besides, we are producing various types of drawing dies and custom-designed parts by sophisticated micro-grains with zero porosity and significantly higher density and hardness values, while maintaining the already high standards of toughness.
A new automatic press machine was installed at the end of 2023 at the Koner plant, with a pressing force of 120 tonnes to produce hard metal products up to an external diameter of 120mm.
We have introduced a new K.80 system for the regrinding and polishing operations of dies, making them sturdy.
The TKT Group has come out with a new Ecoclean/Ecowipe machine for wire and wire rod cleaning. We also have a new butt welder machine, which is efficient and very easy to use, and also significantly reduces the welding process time of the steel wire. This machine guarantees savings and a very high productivity thanks to welding and annealing in a single operation.
There are high quality polycrystalline diamond dies produced by Koner, which supply also a professional and specialized regrinding service of PCD dies. We have new dies with a very fine micro grain size that increases their work life.
We also have spiral brushes to clean the wire. We have a full range of wiping pads for the galvanising process. We have more than 30 different types of wiping pads, which increase the work life and improve the performances in the galvanising line.
Watch: RR Kabel | Solar Cables | Solar Plant | Renewable Energy
WCI: Please give insights about your D-lab.
FB: Concerning the auxiliary products, we have D-lab, an innovative instrument that can measure the diameter and ovality of dies in one second with an accuracy on diameter tolerance of 1-2 micron. It is a high performance, easy-to-use die-checking equipment designed to measure the diameter and ovality of drawing dies quickly and efficiently. The equipment is highly flexible and can measure different dies without system re-mastering. It is sturdy and robust, and suitable to be used in a workshop environment. All measured data can be saved and recorded, ready to be exported or printed. The software has been designed to be extremely user-friendly and flexible.
It’s a very competitively priced instrument having a measurement range between 0.3 mm to 8mm. The accuracy is ± 1 μm and the operation takes only one second to complete. TKT Group, by its Koner company, is the exclusive distributor of the D-lab measuring system for the worldwide steel wire market.
D-lab, after the great success on the world market in recent years, has been further improved with a larger ‘touch screen’ for greater ease of use by operators.
WCI: What is your USP, which gives you an edge over your peers in the market?
FB: We are very targeted to offer technical service. We not only provide commercial service and good products to our customers, but technical service and support, giving them the benefit of our extensive experience. Our mission right now is to continue on the path of innovation and high quality products because we are very targeted to innovate our product portfolio and give the customers a very good product integrated by a very competent technical service.
We customise the products according to customer needs. For example, in the case of lubricants and drawing dies, we suggest our customers the best product that is suitable for their process. Not only for the lubricants and drawing dies, but also in the case of wiping pads and galvanising processes, we suggest improvements of the processes at their plant. For example, we suggeste the drawing set to optimise the drawing performances. By the synergy between lubricants and dies, we can obtain it.
Also Read: Innovative Technologies at Dusseldorf Make Wire 2024 Historic
WCI: What kind of presence do you have in the Indian market?
FB: We have an extensive presence here. We supply our products to several big and medium-sized companies. We have a warehouse in New Delhi. We attend all the industry-related major exhibitions & fairs across the country and make lasting relationships with the customers.
The Indian market is very crucial for the development of our future. The Indian economy is growing and we are collaborating with a lot of drawing companies, customising products for them. We are very flexible with this market and plan to develop it hugely in the next three to five years.
Currently, 4 to 5 percent of our total business is in India. We want to increase our share in the Indian market in the future, which will also lead to an increase in the percentage of our business here.