Reducing material costs in automotive wire production with SK-400-C.
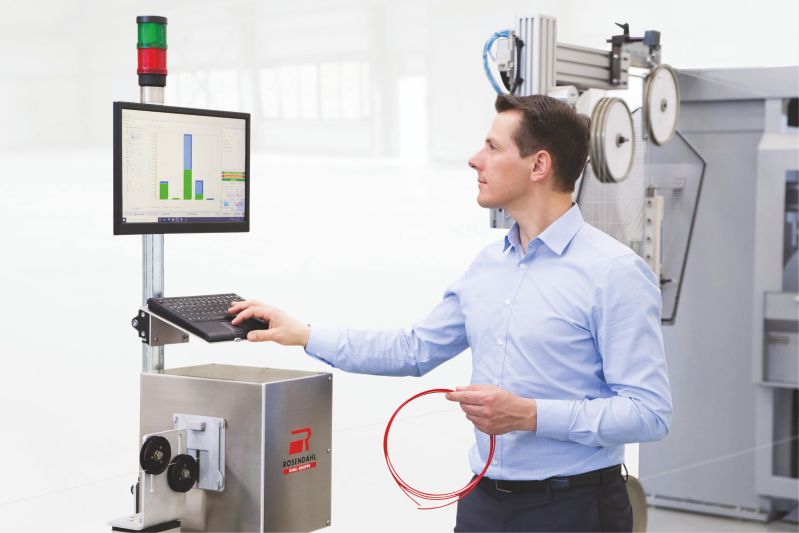
When producing on your automotive wire production line, just one or two granules of a different color can cause a contamination of approximately 200 m of insulation cable. 200 m seems long, but detecting this color variation at a speed of 1800 m/min by the operator is impossible. But what if it weren’t?
Rosendahl has optimized an innovative sensor system for color detection for exactly this reason – to detect color variations which the human eye can no longer perceive: the SK-400-C.
Let’s take a closer look at this color recognition system: The SK-400-C measures the main and stripe colors, as well as the stripe width, exactly in accordance with the previously set references.
The main component is a PC-based evaluation unit with 360° camera surveillance. The unit consists of four cameras which are covered by a protective housing. This enables monitoring of the color quality over the entire scope. This allows the tested color quality to be documented, e.g. in the spool protocol. Thanks to the immediately assured color reliability, color complaints and faulty productions are now a thing of the past.
This also means that waste and scrap rates are significantly reduced at start-up, during production as well as during color changes.
Of course, it has undergone intensive testing on Rosendahl’s laboratory line in Pischelsdorf, Austria, as well as on automotive wire production lines directly at customers’ sites. The results have revealed that recipes with 2.5% master-batch can easily be decreased down to 1.5%, while still maintaining the same color shade. All these improvements lead to immediate savings regarding the master-batch, and thus reduce material costs.